Les raisons pour lesquelles le nombre d’entreprises de construction métallique misant sur l’impression 3D, nommée WAAM (Wire Arc Additive Manufacturing) dans le jargon du secteur, est en augmentation, sont évidentes : les nombreuses possibilités d’individualisation offertes par les installations de production modernes sont accompagnées d’une demande de solutions individuelles sur mesure. Nous avons régulièrement besoin de pièces de rechange non standard dans des délais très courts, et dans le domaine de la construction de prototypes nous voulons non seulement réduire les frais d’outillage, mais également les temps de développement. C’est face à toutes ces exigences que la fabrication additive fait valoir ses atouts majeurs. Des géométries de pièces qui semblaient hier encore irréalisables le deviennent aujourd’hui, couche après couche, grâce à l’impression 3D métallique, et ce au moment précis où nous en avons besoin.
WAAM – moins de matériau, plus de légèreté, des frais moindre
En comparant l’impression 3D métallique avec les processus d’usinage comme le fraisage, on constate que le Wire Arc Additive Manufacturing consomme moins de matériau. Plus le prix des matières premières est élevé, plus ce mode de fabrication additive est rentable rapidement.
Les moules fabriqués à grands frais, comme ceux dont nous avons besoin pour le moulage, ne sont pas non plus nécessaires. Au lieu de cela, nous pouvons utiliser une technologie de soudage moderne pour fabriquer des pièces métalliques complexes, à la topologie optimisée, couche par couche, selon des instructions que l’on appelle dans le jargon « Additive Manufacturing Procedure Specification » (AMPS). Une AMPS contient tout le nécessaire pour un « processus d’impression » parfait : les différents descriptifs de mode opératoire de soudage (Deposition Procedure Specifications, en abrégé DPS), les certificats d’opérateur et de matériau ainsi que la stratégie cinématique, dont nous avons besoin pour la planification de la trajectoire et la commande de mouvement du robot de soudage.
Les certificats de matériau assurent une qualité des fils de soudage adaptée à la production. Les certificats d’opérateur garantissent que les cellules de soudage robotisées DED-Arc utilisées dans la fabrication additive ne sont utilisées que par des spécialistes compétents. DED-Arc signifie Directed Energy Deposition Arc. Il s’agit d’un arc électrique pour déposer le fil d’apport fondu couche par couche.
« Lors de l’optimisation de la topologie, nous voulons garantir une répartition idéale des matériaux des composants. En fait, il s’agit de réduire le poids tout en conservant la rigidité », explique l’expert en impression 3D métallique Philipp Roithinger, qui poursuit : « Les applications typiques sont les structures bioniques, empruntées à la nature, comme nous les trouvons par exemple dans le domaine de l’aérospatiale. Un autre avantage de l’impression 3D métallique est la possibilité de fabrication décentralisée. Il n’y a pas besoin de lignes de production comme dans la fabrication en série, peu importe le lieu. La fabrication additive avec fil d’apport se caractérise par des cellules de soudage robotisé avec un équipement spécial, qui peuvent être utilisées de manière flexible dans le monde entier. Dans tous les domaines de la construction métallique où le poids, les matériaux, les coûts et l’impact environnemental doivent être réduits, nous misons aujourd’hui de plus en plus sur l’impression 3D métallique. »
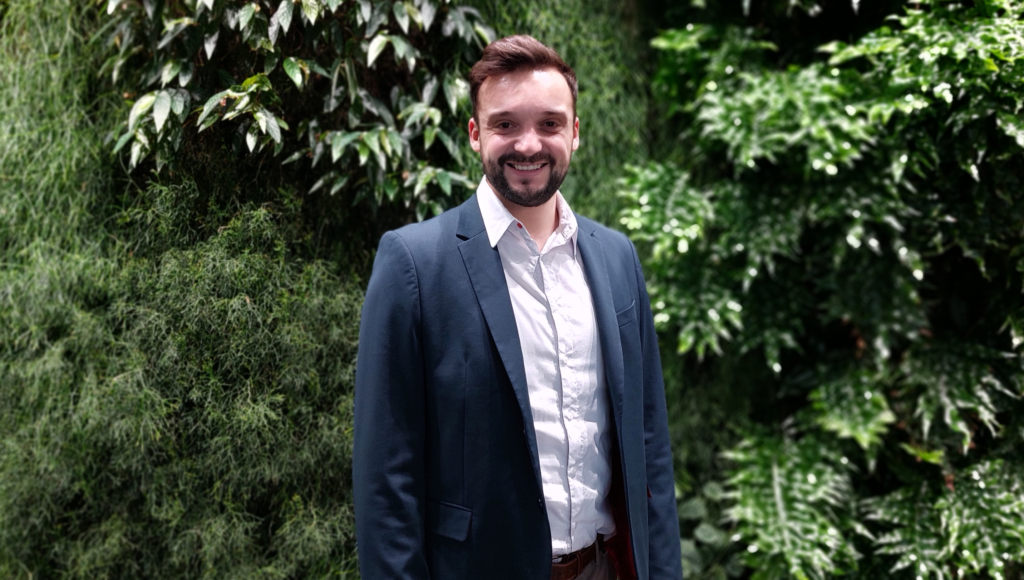
Un indispensable de l’impression 3D métallique : un arc électrique plus stable comme pour le process CMT
Pour obtenir la qualité souhaitée en soudage additif, nous avons besoin d’un process de soudage extrêmement stable comme le process CMT (Cold Metal Transfer). Ce dernier est un process de soudage à court-circuit « froid », qui malgré son taux de dépôt élevé, maintient un faible apport d’énergie. Cela fonctionne parce que le détachement des gouttes est déclenché par un mouvement de rétractation du fil-électrode.
Dans le processus à court-circuit conventionnel, peu adapté au WAAM, qui génère un apport d’énergie plus important, le fil se déplace en continu vers la pièce à usiner, contrairement au process CMT. Dès que l’extrémité molle du fil entre en contact avec le bain de fusion, il se produit un court-circuit. Une grande partie du fil d’apport liquide s’écoule dans le bain de fusion, la goutte se détache. Dans la phase de court-circuit, la tension de soudage tend vers zéro, tandis que le courant augmente jusqu’à une valeur élevée, le court-circuit est rompu et l’arc électrique est réamorcé.
Le détachement de la goutte et le réamorçage de l’arc électrique s’effectuent de façon contrôlée avec le process CMT, et avec un apport d’énergie moindre par rapport à l’arc court, notamment grâce au mouvement de rétractation du fil-électrode dans la phase de court-circuit. En fonction de la caractéristique pour le matériau d’apport, le gaz de protection et le diamètre d’électrode, le mouvement de rétractation du fil a lieu dans une plage de fréquence de 50 à 170 Hz.
L’apport d’énergie lors du soudage CMT est jusqu’à 33 % plus faible qu’avec les arcs courts classiques. C’est pourquoi ce processus convient parfaitement au soudage additif, où le dépôt cyclique de passes entraîne un apport d’énergie important. Si la température du composant est trop élevée, cela diminue les propriétés du matériau et entraîne des temps d’attente. Dans un tel cas, le process de soudage devrait être interrompu jusqu’au refroidissement des couches de soudage. Les variations de la distance tube-contact/pièce sont peu critiques avec le CMT, l’arc électrique reste stable et, le système à fil unique octroie un degré de liberté supplémentaire lors de la programmation du robot.
CMT Additive Pro : un apport d’énergie ciblé pour une superposition régulière
Le process CMT prend en charge des fonctions spécialement adaptées à l’impression 3D métallique, comme la « correction de puissance ». Elle permet d’adapter avec précision la puissance électrique utilisée à chaque phase du processus à la structure des couches et à l’apport d’énergie. Le taux de dépôt reste constant.
« Grâce à nos fonctions CMT Additive Pro spécialement développées pour la fabrication additive telles que la correction de puissance ou la stabilisation du dépôt, nous pouvons contrôler de manière ciblée la puissance et donc la hauteur ainsi que la largeur de la soudure », ajoute M. Roithinger.
Un nouveau redémarrage de la soudure pendant la superposition des couches, en raison du remplacement des fûts de fil vides, peut représenter une source d’erreur à ne pas sous-estimer. Les erreurs d’assemblage ou les surhaussements qui en résulteraient dans la zone de démarrage du soudage affecteraient massivement la qualité des pièces fabriquées par fabrication additive. La fonction Pulsed HotStart permet de remédier à ce problème. Si elle est active lors du redémarrage du soudage à l’arc pulsé, on obtient autant de pénétration que nécessaire et la hauteur de la couche est maintenue constante.
Service intégral dans le centre de prototypage Fronius
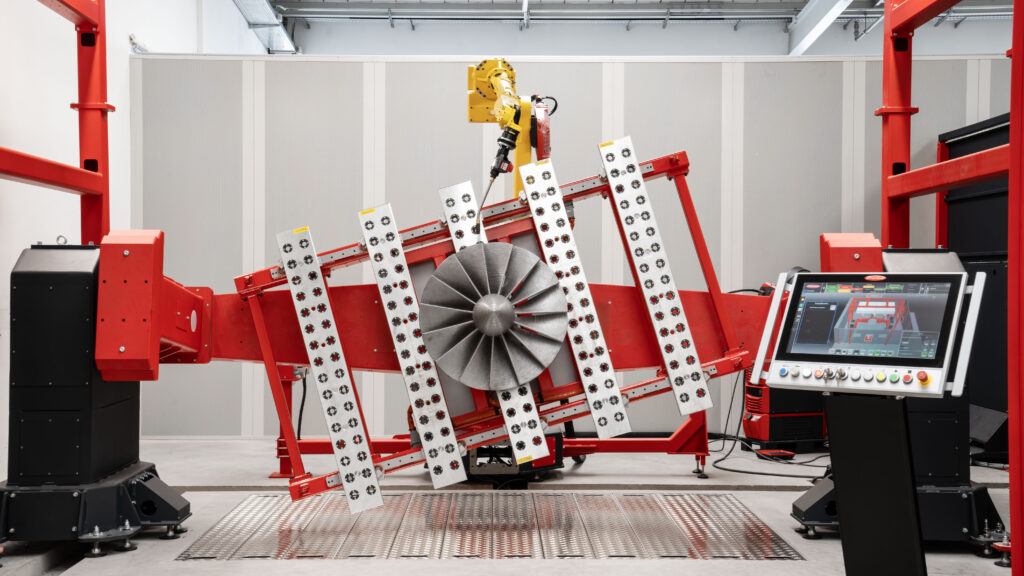
Dans le centre de prototypage du site de Wels, en Autriche, nous mettons à disposition un large éventail de services. Cela comprend des études de faisabilité, des solutions sur mesure pour les demandes individuelles des clients, l’optimisation de process et la fabrication de prototypes en accord avec nos clients et de manière strictement confidentielle. Dans la construction de prototypes, nous voulons réduire au maximum le délai entre le développement et la maturité du produit. Pour cela, nous exploitons tout notre potentiel en matière de technologie de soudage.
Si nécessaire, nos experts apportent leur soutien lors de la fabrication des prototypes, mais également lors de la fabrication des pré-séries. Ils aident à se lancer en douceur dans l’impression 3D métallique robotisée et donnent des recommandations sur le process de soudage, la rentabilité, la qualité et la production. Le centre de prototypage d’environ 900 m² dispose de systèmes robotisés équipés d’une technologie avancée de soudage, de détection et de mesure. Un laboratoire de soudage est également disponible, où des contrôles non destructifs et destructifs de composants peuvent être effectués. Notre gamme de services complète comprend la programmation hors ligne, les simulations, les analyses métallurgiques, la mesure de pièce en 3D, la documentation de données de soudage et plus encore.
De nouvelles normes pour l’impression 3D métallique
Entre-temps, les premières normes pour la fabrication additive basée sur l’arc électrique voient le jour dans différents secteurs. En collaboration avec Linde Engineering, qui nous a mis le cas d’application à disposition, le fabricant de fil Migal.co et TÜV Süd Deutschland, nous avons participé chez Fronius à la qualification de l’échantillon d’un réservoir sous pression fabriqué par fabrication additive sous la forme d’un embranchement de tubes. L’applicabilité du projet de norme preEN 13445-14 pour l’utilisation de réservoirs sous pression fabriqués par fabrication additive a été examinée.
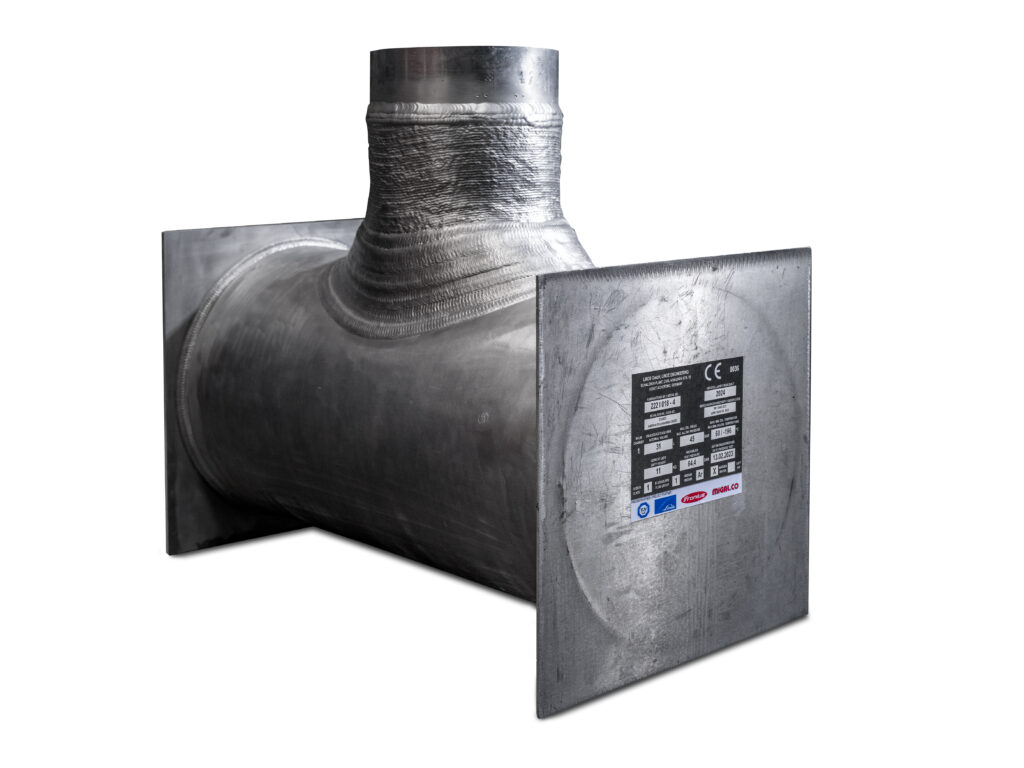
La qualité du matériau utilisé est décisive en matière d’impression 3D métallique. Dans notre cas concret, nous avons opté pour un alliage d’aluminium de corroyage à dureté naturelle. En raison de son excellente résistance aux basses températures (jusqu’à -273°C), ce matériau, qui est également utilisé dans la construction légère, convient particulièrement bien à la construction d’installations de tuyauterie.
Dans le projet de norme européenne susmentionné, l’ensemble de la chaîne de création de valeur pour la fabrication additive est pris en compte, y compris tous les détails de surveillance nécessaires. De cette manière, on veut s’assurer que les exigences de sécurité de base définies dans la directive sur les équipements sous pression sont bien remplies.
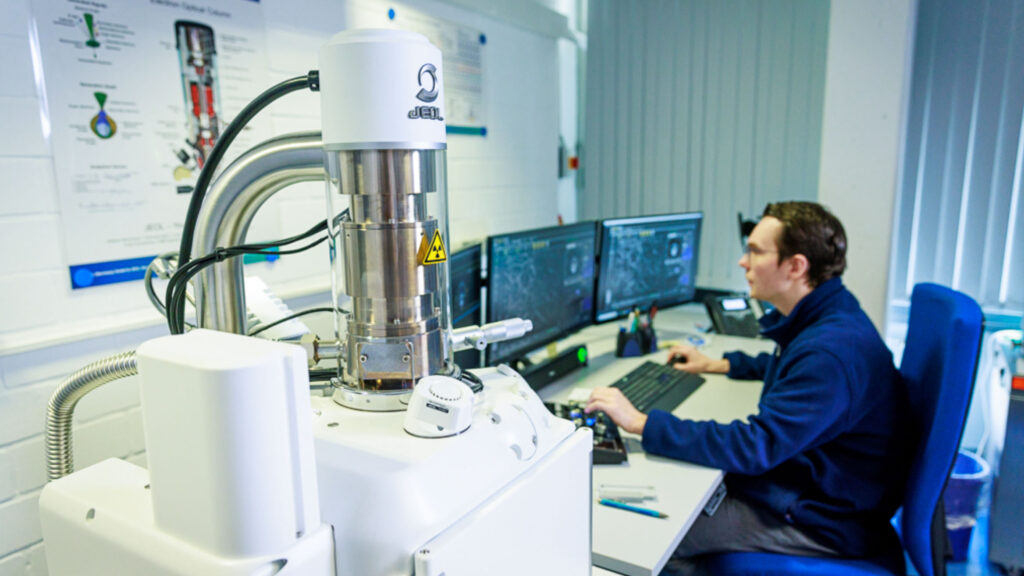
Pendant la qualification de l’échantillon, nous avons vérifié et documenté toute la chaîne de processus, de la conception à l’essai de pression final, en passant par la construction, la fabrication et la planification des trajectoires, ainsi que la surveillance du processus.
Les informations détaillées concernant la qualification de l’échantillon du réservoir sous pression pour une certification CE de TÜV-Süd sont disponibles dans cette vidéo : YouTube
Aucun commentaire