To oczywiste, dlaczego coraz więcej przedsiębiorstw wytwarzających konstrukcje metalowe stawia na druk 3D — w branżowym żargonie określany mianem WAAM (Wire Arc Additive Manufacturing). Rozmaite możliwości indywidualizacji nowoczesnych instalacji produkcyjnych nie nadążają z poszukiwaniem jedynych w swoim rodzaju rozwiązań. Coraz częściej potrzebne są nietypowe części zamienne — i to na wczoraj. A w przypadku prototypowych konstrukcji chodzi nie tylko o koszty zakupu narzędzi, ale przede wszystkim o skrócenie czasu realizacji. Przy wszystkich tych wymaganiach produkcja addytywna sprawdza się najlepiej. Geometrie elementów, które jeszcze niedawno wydawały się wręcz niemożliwe, stają się obecnie faktem dzięki drukowi 3D w metalu — i to właśnie wtedy, kiedy są najbardziej potrzebne.
WAAM – mniej materiału, mniejsza waga, niższe koszty
Jeśli porównać druk 3D w metalu z procesami obróbki skrawaniem, da się zauważyć, że Wire Arc Additive Manufacturing zużywa znacznie mniej surowców. Im wyższe ich ceny, tym szybciej zwraca się inwestycja w tego rodzaju produkcję addytywną.
Mozolnie wytwarzane formy, jakie są potrzebne przy odlewaniu, stają się zbyteczne. Zamiast tego można wytwarzać złożone elementy metalowe o zoptymalizowanej topologii, warstwa po warstwie, zgodnie z recepturą. W fachowym żargonie tego rodzaju instrukcje wykonania określa się mianem Additive Manufacturing Procedure Specification (AMPS). Instrukcja AMPS zawiera wszystko, co potrzebne do idealnego „printu”: poszczególne instrukcje spawania (Deposition Procedure Specifications, w skrócie DPS), certyfikaty operatora i materiałów, jak również strategię kinematyczną potrzebną do zaplanowania ścieżek i sterowania ruchami robota spawalniczego. Certyfikaty materiałów gwarantują jakość drutów spawalniczych wymaganą przy produkcji.
Certyfikaty operatora są gwarancją, że powszechnie stosowane w produkcji addytywnej cele do spawania zrobotyzowanego DED-Arc są obsługiwane tylko przez znających się na rzeczy specjalistów. DED-Arc oznacza Directed Energy Deposition Arc, to znaczy łuk spawalniczy do warstwowego stapiania drutu spawalniczego.
„Optymalizacja topologii ma zapewnić idealną dystrybucję materiału w bryle powstającego elementu. Dokładniej chodzi o to, aby zredukować masę przy jednoczesnym zachowaniu sztywności”, wyjaśnia Philipp Roithinger, ekspert w dziedzinie druku 3D w metalu — i dopowiada: „Typowymi zastosowaniami są struktury bioniczne, zapożyczone z natury, jakie spotykamy na przykład w przemyśle lotniczym. Inną zaletą druku 3D w metalu jest możliwość decentralizacji produkcji. W danym miejscu i czasie nie potrzeba żadnych linii produkcyjnych, jak w przypadku produkcji seryjnej. Specjalnie wyposażone cele do spawania zrobotyzowanego, które można znaleźć na całym świecie, są wyróżnikiem produkcji addytywnej z użyciem drutu spawalniczego. Wszędzie tam, gdzie chcemy zredukować masę, ilość materiałów, koszty i uciążliwość dla środowiska, coraz częściej sięgamy dzisiaj po druk 3D w metalu”.
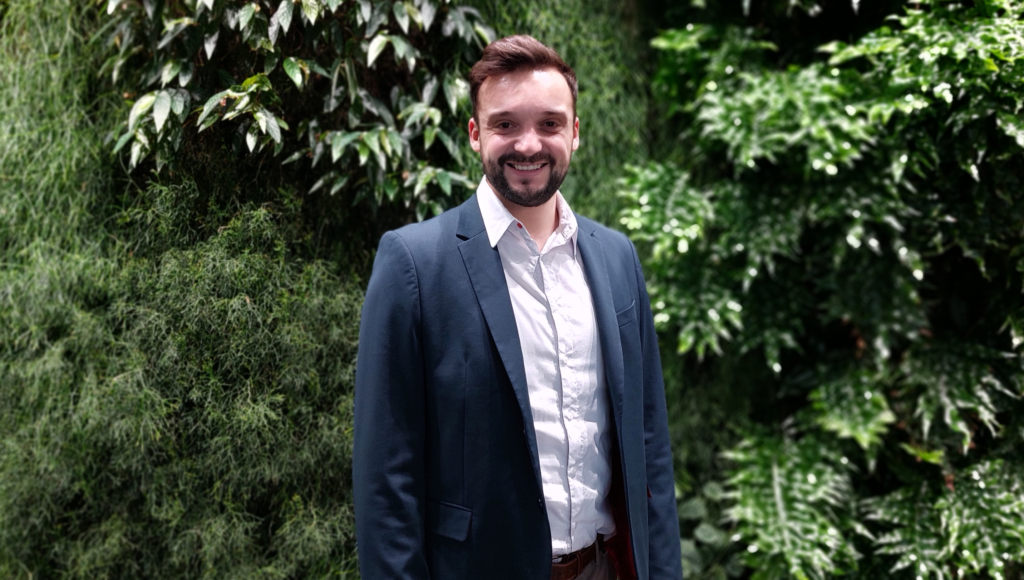
Nieodzowny do druku 3D w metalu: stabilny łuk spawalniczy, taki jak w procesie CMT
Aby osiągnąć pożądaną jakość spawania addytywnego, potrzebny jest niesamowicie stabilny proces spawania, taki jak CMT (Cold Metal Transfer). CMT to „chłodny” proces spawania łukiem zwarciowym, który pomimo wysokiej wydajności stapiania utrzymuje ciepło wprowadzane do spoiny na stosunkowo niskim poziomie. Funkcjonuje to w ten sposób, że odrywanie kropli jest wywoływane poprzez cofanie drutu elektrodowego.
Konwencjonalny proces spawania łukiem zwarciowym niezbyt nadaje się do produkcji WAAM, ponieważ generuje więcej ciepła wprowadzanego do spoiny. Drut porusza się stale w kierunku elementu spawanego — czyli inaczej niż w przypadku CMT. Gdy tylko zmiękczony koniec drutu zetknie się z jeziorkiem spawalniczym, powstaje zwarcie. Większość spływającego drutu spawalniczego wpada do jeziorka spawalniczego, czyli ma miejsce tzw. odrywanie kropli. W fazie zwarcia napięcie spawania zbliża się do zera, podczas gdy prąd rośnie do wysokiego poziomu. Zwarcie zostaje przerwane, po czym dochodzi do ponownego zajarzenia łuku spawalniczego.
Odrywanie kropli i ponowne zajarzenie łuku spawalniczego w przypadku procesu CMT jest bardziej kontrolowane i wymaga mniej energii niż w przypadku łuku zwarciowego. Dzieje się tak dzięki cofaniu drutu elektrodowego w fazie zwarcia. Zależnie od charakterystyki dla danego spoiwa, gazu osłonowego i średnicy elektrody cofanie drutu odbywa się z częstotliwością od 50 do 170 Hz.
Ciepło wprowadzane do spoiny powstające przy spawaniu CMT jest nawet o 33% mniejsze niż w przypadku zwykłego łuku zwarciowego. Dlatego proces ten nadaje się doskonale do spawania addytywnego, gdzie cykliczne napawanie ściegów spawalniczych generuje znaczne ilości ciepła wprowadzanego do spoiny. Jeśli temperatura elementu będzie za wysoka, pogorszą się właściwości użytego materiału. Dlatego trzeba przerywać proces spawania i czekać, aż schłodzą się napawane warstwy. Wahania długości wolnego wylotu drutu elektrodowego od elementu spawanego mają mniejsze znaczenie w przypadku metody CMT, łuk spawalniczy pozostaje stabilny, a dzięki zastosowaniu systemu pojedynczego drutu można korzystać z większej swobody przy programowaniu robota.
CMT Additive Pro: celowe wprowadzanie ciepła do spoiny pozwala na ciągłe napawanie warstw
Proces CMT obsługuje funkcje przydatne zwłaszcza przy druku 3D w metalu, jak na przykład „korekcję mocy”. Powoduje ona, że elektrycznie wydatkowana moc może zostać precyzyjnie dostosowana do poszczególnych faz procesu — do napawanych warstw i ciepła wprowadzanego do spoiny. Wydajność stapiania utrzymuje się przy tym na stałym poziomie.
„Dzięki naszym funkcjom CMT Additive Pro, takim jak korekcja mocy albo Deposition Stabilizer, które zaprojektowano specjalnie pod kątem produkcji addytywnej, możemy dokładnie kontrolować dostarczaną moc, a tym samym wysokość i szerokość spoiny”, objaśnia dalej Roithinger.
Jeśli podczas napawania jednej z warstw będzie trzeba zatrzymać — ponieważ skończył się zapas drutu i trzeba go uzupełnić — a następnie wznowić spawanie, może to okazać się istotnym źródłem błędów. Powstające przy tym błędy wiązania albo przewyższenia spoin w miejscu wznowienia spawania mogłyby poważnie zaszkodzić jakości elementów z produkcji addytywnej. W tym momencie pomocna okazuje się funkcja Pulsed Hot Start. Kiedy jest aktywna, przy ponownym rozpoczęciu spawania łuk pulsujący zapewnia niezbędne wtopienie, a grubość warstwy może zostać utrzymana na stałym poziomie.
Serwis 360° w centrum prototypowania Fronius
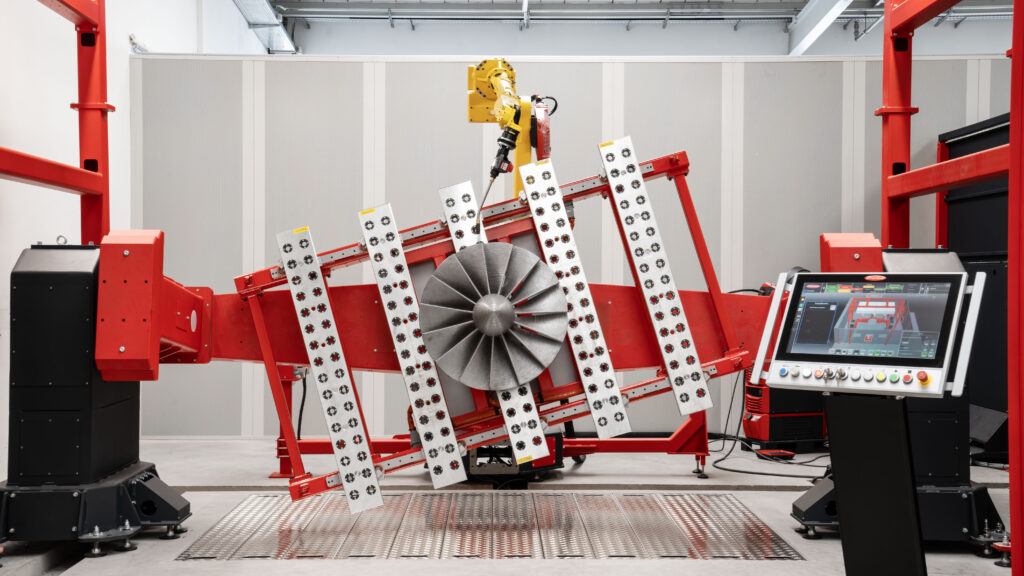
W centrum prototypowania zlokalizowanym w Wels na terenie Austrii oferujemy szeroki wachlarz usług. Obejmują one studium wykonalności, konkretne rozwiązania dostosowane do indywidualnych potrzeb klientów, optymalizację procesu i wreszcie wykonanie prototypu — na podstawie ustaleń z naszymi zleceniodawcami i ściśle poufnie. Przy tworzeniu prototypów chcemy, aby czas od prac rozwojowych do dojrzałości produktu był możliwie jak najkrótszy. Do tego celu zaprzęgamy cały nasz technologiczny potencjał.
Jeśli zajdzie taka potrzeba, nasi eksperci pomagają nie tylko przy tworzeniu prototypu, ale także przy wdrażaniu produkcji seryjnej. Pomagają rozpocząć przygodę ze zrobotyzowanym drukiem 3D w metalu i udzielają porad na temat procesu spawania, rentowności, jakości i produkcji. W centrum prototypowania na powierzchni 900 m² stoją systemy robotyczne z zaawansowaną technologią spawania oraz czujnikami i systemami pomiarowymi. Jest również laboratorium, w którym wykonujemy próby nieniszczące i niszczące. Nasz pakiet Full Service obejmuje programowanie offline, symulacje, badania metalurgiczne, trójwymiarowe pomiary elementów, dokumentację danych spawalniczych i wiele innych składników.
Nowe normy druku 3D w metalu
W międzyczasie w rozmaitych branżach powstają pierwsze normy produkcji addytywnej opartej na łuku spawalniczym. Razem z firmą Linde Engineering, która udostępniła swój przypadek zastosowania, producentem drutu Migal.co i niemieckim instytutem TÜV Süd pracowaliśmy nad kwalifikacją wzorcową addytywnej produkcji zbiornika ciśnieniowego w postaci odgałęzienia rury. Sprawdzaliśmy przy tym trafność założeń projektu normy preEN 13445-14 w przypadku zbiorników ciśnieniowych powstających metodą addytywną.
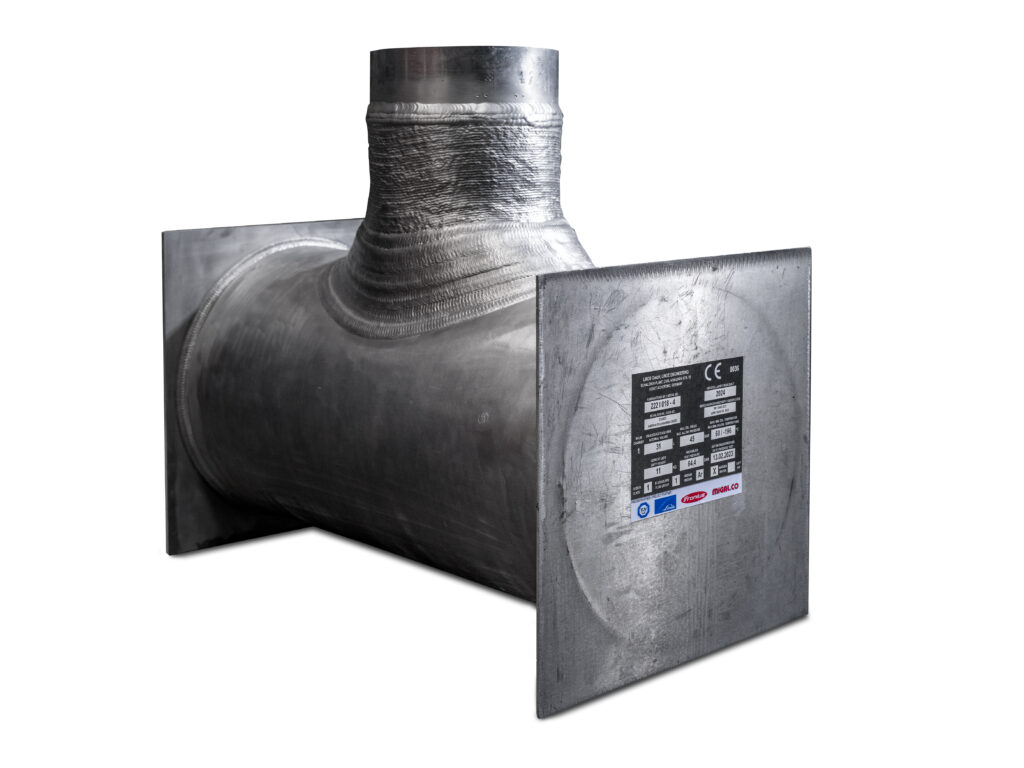
Podczas druku 3D w metalu decydujące znaczenie ma jakość użytych materiałów. W tym konkretnym przypadku wybór padł na stop aluminium do obróbki plastycznej o naturalnej twardości. Z powodu znakomitej wytrzymałości w niskich temperaturach, sięgających nawet -273°C, ten stosowany również do lekkich konstrukcji surowiec nadaje się zwłaszcza do budowy instalacji rurowych.
We wspomnianym projekcie normy europejskiej bierze się pod uwagę cały łańcuch powstawania wartości w produkcji addytywnej, wraz ze wszystkimi niezbędnymi szczegółami wymagającymi nadzoru. Ma to zagwarantować całkowitą zgodność z zasadniczymi wymogami bezpieczeństwa, które są zdefiniowane w dyrektywie w sprawie urządzeń ciśnieniowych.
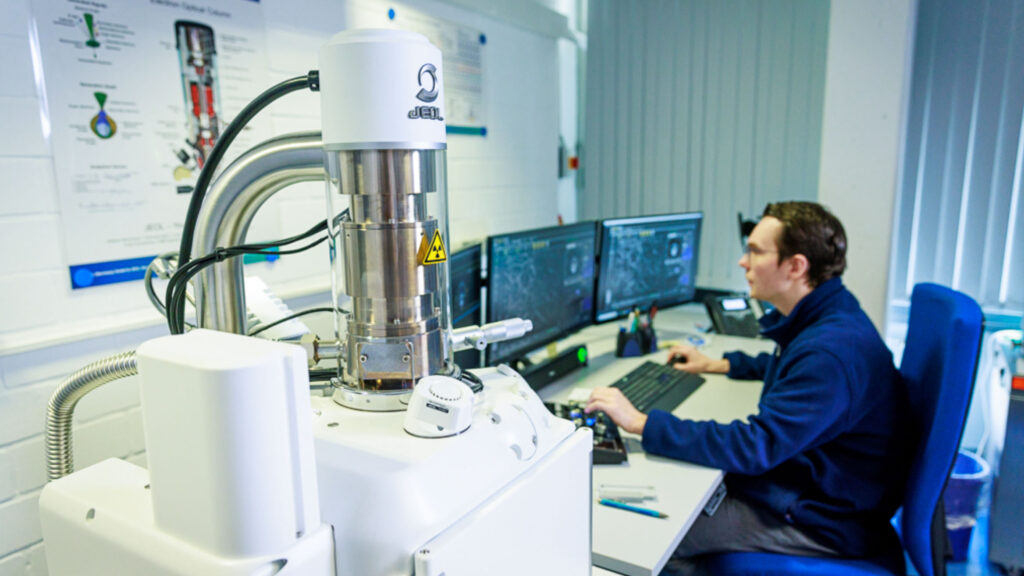
Podczas kwalifikacji wzorcowej sprawdzaliśmy i udokumentowaliśmy cały łańcuch procesowy: od opracowania charakterystyk poprzez prace konstrukcyjne, opracowanie procesu produkcji, planowanie torów ruchu i nadzorowanie procesu, aż po końcową próbę ciśnieniową.
Szczegółowe informacje na temat kwalifikacji wzorcowej zbiornika ciśnieniowego z końcową certyfikacją CE przez instytut TÜV-Süd znajdują się w materiale wideo: YouTube
Brak komentarzy