Napawanie to specjalna metoda spawania, która służy do wydłużania żywotności elementów i instalacji technicznych. W szczególności wtedy, gdy są one narażone na ekstremalne warunki, takie jak wysokie temperatury, ciśnienie lub żrące substancje, potrzebna jest dodatkowa warstwa ochronna, która pozwala zapobiec katastrofie.
Dlaczego napawanie jest tak ważne?
Napawanie odgrywa kluczową rolę zwłaszcza w przemyśle naftowo-gazowym. Oceany są stale zanieczyszczane dużymi ilościami ropy naftowej wyciekającymi z nieszczelnych rurociągów. Gazociągi też są podatne na takie zagrożenia, ponieważ łatwopalne gazy mogą w kontakcie ze źródłem zapłonu, jak tlen, wywołać pożar, a nawet wybuch. Przykładem takiej tragedii było „oko ognia” w Zatoce Meksykańskiej. W 2021 r. wskutek wycieku gazu w rurociągu 150 metrów od platformy wiertniczej pola naftowego Ku-Maloob-Zaap doszło do katastrofalnego podwodnego pożaru.
Jest zatem pewne, że jeśli chodzi o ochronę rurociągów i innych instalacji o znaczeniu krytycznym, nie wolno rezygnować z żadnych środków, które zapewniają dodatkową ochronę. Napawanie minimalizuje liczbę słabych punktów, które mogą stanowić zagrożenie. Dodatkowa warstwa ochronna sprawia, że ryzyko nieszczelności jest znacznie mniejsze, czyli zapobiega nie tylko stratom finansowym, ale także zanieczyszczeniu środowiska.
Napawanie jako uniwersalna metoda hartowania powierzchni
Napawanie jest przydatne nie tylko w przemyśle naftowo-gazowym. Wykorzystuje się je także w budowie elektrowni, aby chronić ściany membranowe i powierzchnie ogrzewalne grodzi przed substancjami żrącymi, np. w spalarniach odpadów i elektrowniach biomasowych, w których elementy metalowe są atakowane przez duże ilości siarki i halogenów.
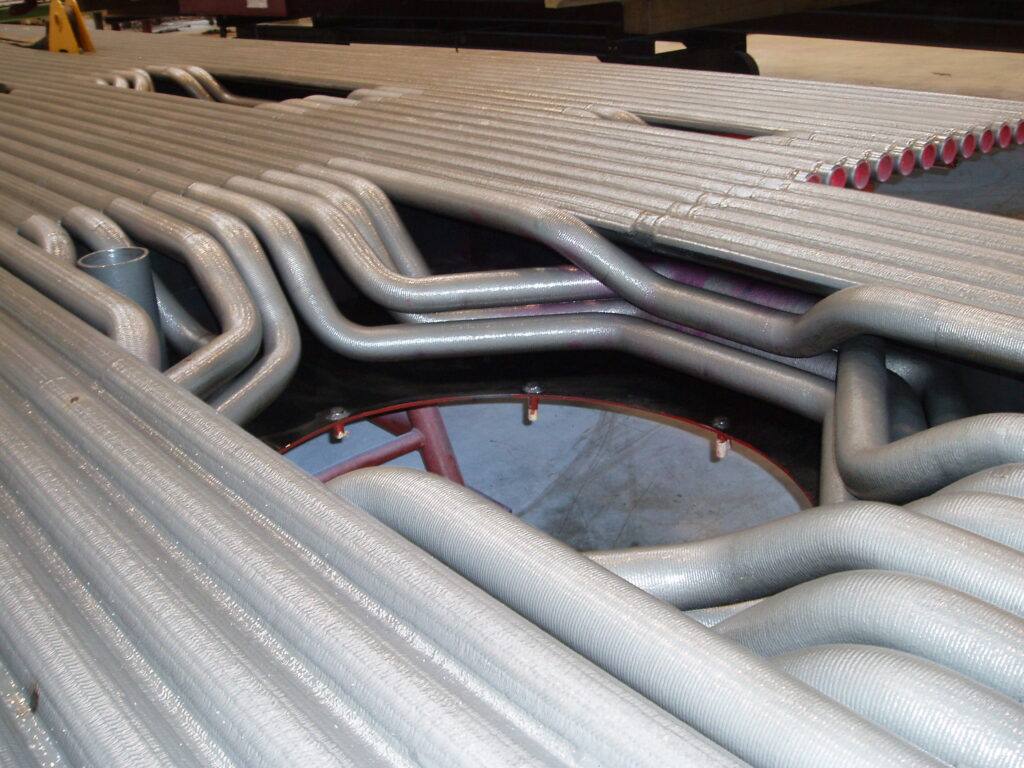
Napawanie przydaje się zatem zawsze tam, gdzie istotna jest punktowa poprawa właściwości powierzchni. Nadaje się zarówno do zwiększenia odporności na ścieranie i korozję, jak i do ekonomicznej naprawy komponentów – bez konieczności wymiany całego elementu.
Więcej niż tylko „nadtopienie”
Zwykłe „wystarczy nadtopić na wierzchu i będzie trzymać” nie ma szans w porównaniu z napawaniem. Metalowe warstwy muszą być solidnie spojone z materiałem podstawowym, aby wytrzymywały ekstremalne obciążenia. Ten proces jest wysoce skomplikowany i wymaga precyzyjnego ustawienia parametrów spawania, aby nie narażać kosztownych komponentów.
W praktyce napawanie jest zatem wykonywane najczęściej w trybie automatycznym metodą TIG z drutem gorącym lub metodą CMT. Czynnikiem decydującym o jakości jest tak zwana mieszanina. Określa ona, ile materiału podstawowego z elementu spawanego zostanie wymieszane z nanoszonym materiałem. Niewielka mieszanina jest niezbędna, aby nanoszony materiał zachował swoje szczególne właściwości, jak pożądaną wysoką odporność na korozję.
Techniki napawania w szczegółach
Zasadniczo napawanie polega na nakładaniu dodatkowej warstwy wierzchniej spoiwa, jak drut lub proszek. W tym celu są stosowane specjalne stopy, jak Alloy 50 i 625, CrMo 910 lub Inconel 625. Przekłada się to na duże korzyści ekonomiczne: zwykła stal może zostać uszlachetniona wysokogatunkowymi stopami.
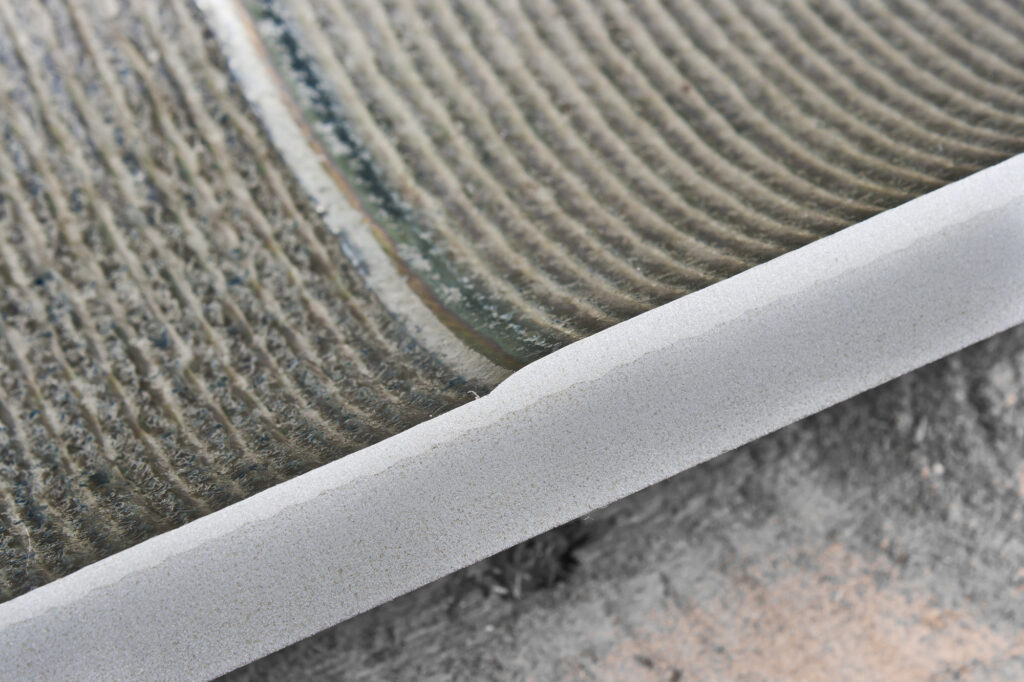
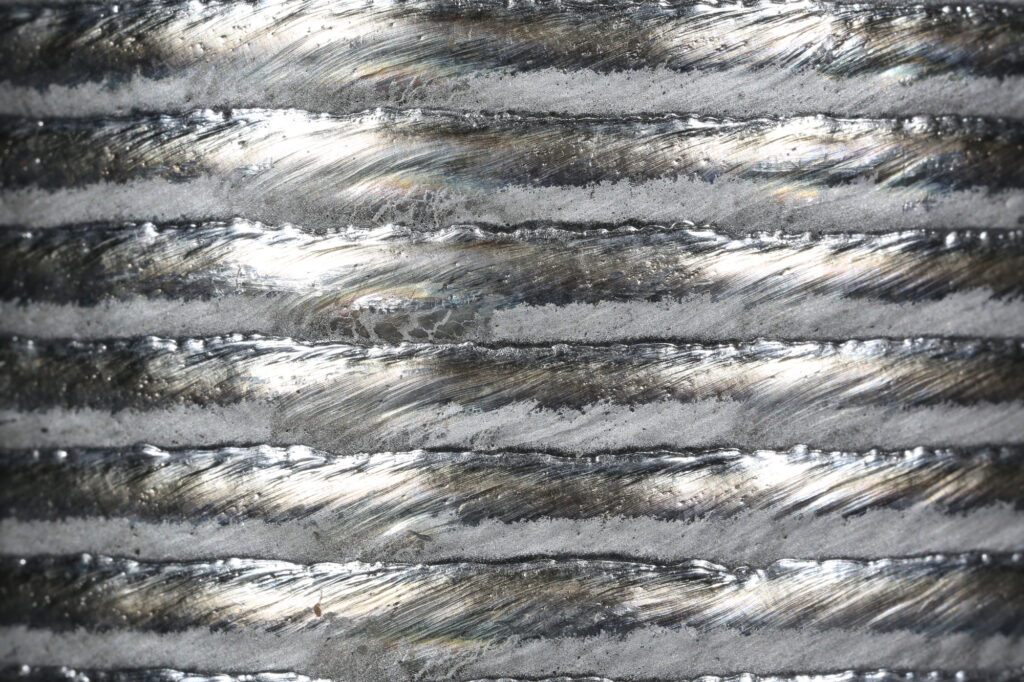
Ze względu na surowe wymogi dotyczące bezpieczeństwa w przemyśle naftowo-gazowym spawanie jest wykonywane głównie metodą TIG z drutem gorącym. Popularność zyskują jednak również takie metody, jak napawanie laserowe i napawanie plazmowe proszkowe. Nie można z góry określić, która metoda jest najlepsza, ponieważ każda z nich ma swoje zalety, a przy porównaniu trzeba uwzględnić materiał, wielkość elementu i wymagania.
Spawanie TIG z drutem gorącym zapewnia największą precyzję
Spawanie TIG z drutem gorącym to ewolucja typowego spawania TIG (elektrodą wolframową w osłonie gazów obojętnych). W tej metodzie dodatkowy drut jest podgrzewany elektrycznie, zanim zostanie doprowadzony do obszaru topienia. Przekłada się to na znaczną poprawę wydajności stapiania i efektywności procesu spawalniczego, co z kolei minimalizuje ilość wad, jak pęknięcia lub odkształcenia.
Ponadto spawanie TIG z drutem gorącym jest uniwersalną metodą, która pozwala uzyskać wysokiej jakości powłokę z równomiernymi spoinami bez odprysków, które spełniają nawet najwyższe standardy bezpieczeństwa. Jedyną wadą jest to, że spawanie TIG z drutem gorącym jest bardzo czasochłonne, w szczególności w przypadku dużych komponentów lub w produkcji seryjnej.
Ten mankament można obejść, wykorzystując SpeedClad 2.0. Opracowany przez firmę Fronius, zaawansowany proces napawania umożliwia spawanie z prędkością do 110 cm/min przy użyciu tylko jednej specjalnie uformowanej elektrody i jednego dodatkowego drutu. Wąski uchwyt spawalniczy umożliwia ponadto powlekanie średnic już od 100 mm.
Wprowadzanie do spoiny małej ilości ciepła dzięki CMT
O ile w przemyśle naftowo-gazowym stosowane jest głównie spawanie TIG z drutem gorącym, to w budownictwie energetycznym wiele firm stawia na metodę MIG/MAG lub CMT, np. przy powlekaniu ścian membranowych lub innych części instalacji. Dużą zaletą tych metod jest samoczynne wykrywanie zwarć dzięki cyfrowej regulacji procesu. Dodatkowo cofanie drutu wspomaga odrywanie kropli.
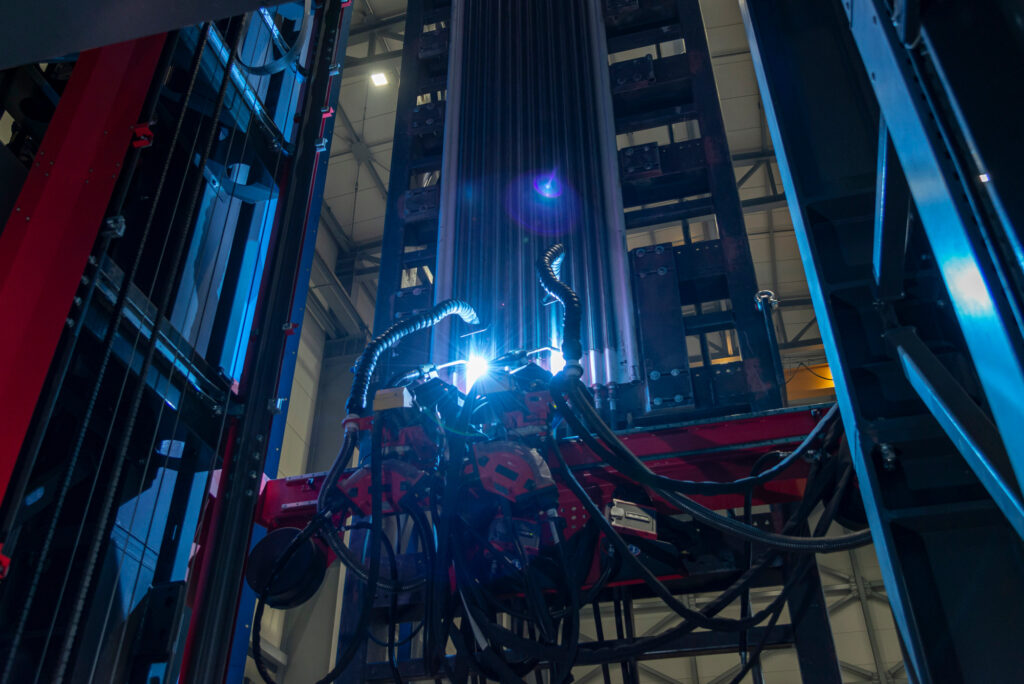
Ten ruch posuwisto-zwrotny skraca fazę jarzenia łuku spawalniczego, dzięki czemu do spoiny wprowadzana jest mniejsza ilość ciepła. W ten sposób powstaje powłoka prawie bez odprysków o szczególnie gładkiej powierzchni, z miękkimi przejściami spoiny i stałą grubością warstwy.
Łatwiejsze napawanie metodą TIG
W przemyśle kooperacyjnym zakłady produkcyjne chętnie korzystają z tak zwanych cel do napawania, aby stworzyć stabilne warunki pracy. Takim wydajnym i ekonomicznym systemem jest Fronius Compact Cladding Cell, w skrócie CCC. Na powierzchni zaledwie 6 metrów kwadratowych oferuje on wystarczającą pojemność do spawania elementów o prostej geometrii, średnicy do jednego metra, wysokości do 1,9 metra i masie do 2500 kg – oznacza to, że idealnie nadaje się do powlekania wnętrz zaworów.
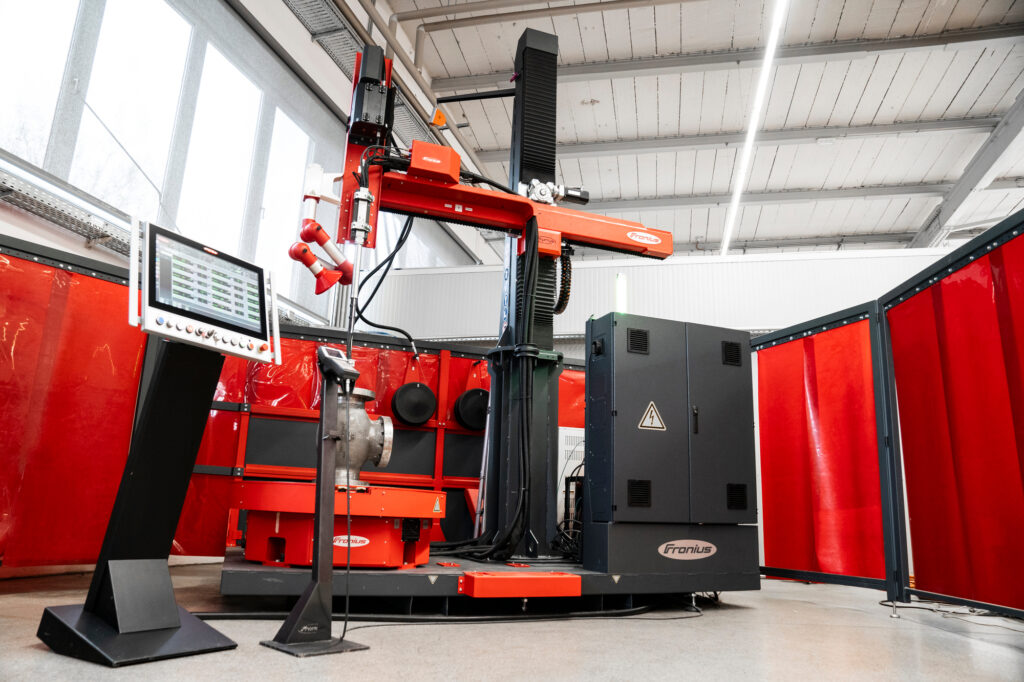
W Compact Cladding Cell można spawać wyłącznie metodą TIG z drutem gorącym albo SpeedClad 2.0, aby uzyskać spoiny jak najwyższej jakości. Takie funkcje, jak ergonomiczny uchwyt szpuli drutu, 21-calowy wyświetlacz z ekranem dotykowym i wizualizacja procesu w czasie rzeczywistym sprawiają, że proces powlekania jest nie tylko łatwy w obsłudze, ale też łatwo jest go obserwować, aby nie popełnić błędu. Dużą zaletą jest także zwarta konstrukcja, która sprawia, że CCC można z łatwością przewozić na wózku widłowym – ułatwia to małym podwykonawcom niedysponującym dużą powierzchnią wykonywanie zleceń powlekania dla przemysłu naftowo-gazowego.
Precyzyjne napawanie elementów o złożonej geometrii
W przypadku większych i bardziej złożonych elementów przydatna okazuje się wirująca bez limitów głowica spawalnicza systemów Endless Torch Rotation (ETR), która umożliwia automatyczne wyznaczanie pozycji uchwytu w trójwymiarowej przestrzeni, co skraca czas uzbrajania. Kolejną zaletą jest synchronizacja ruchu osi, czyli przemieszczanie się uchwytu i obrotnicy ze znajdującym się na niej elementem synchronicznie względem siebie.
Uchwyt spawalniczy może być trzymany zawsze w optymalnej pozycji do procesu napawania, aby spoina się nie rozpływała. Pozwala to zautomatyzować powlekanie nawet elementów o złożonej geometrii. Wyposażone w wyświetlacz z 21-calowym ekranem dotykowym systemy ETR są kompatybilne ze SpeedClad 2.0 i zapewniają łatwe sterowanie i wizualizację w czasie rzeczywistym, co przekłada się na wysoką wydajność.
Podsumowanie: napawanie jest nieodzownym rozwiązaniem
Zarówno za pomocą nowoczesnych cel do napawania, jak i systemów w rodzaju ETR: napawanie jest i pozostanie nieodzowną metodą, która chroni nas przed niebezpiecznym zużyciem materiałów wskutek korozji i ścierania. Dzięki dużej różnorodności nowoczesnych procesów napawania można znaleźć optymalne rozwiązanie do każdego zastosowania.
Dowiedz się wiecej o o poszczególnych procesach i rozwiązaniach do napawania!
Brak komentarzy