Puede que los sistemas y robots de soldadura proporcionen los requisitos indispensables básicos para la soldadura MIG/MAG, pero la verdadera acción tiene lugar en la parte delantera del cuello antorcha. Temperaturas de hasta 15 500 grados, proyecciones de metal líquido y abrasión permanente a través del hilo de soldadura: las fuerzas térmicas y mecánicas que actúan sobre los consumibles, como puntas de contacto y toberas de gas, son enormes. ¿Qué se debe hacer entonces para retrasar lo máximo posible el inevitable fin de estas piezas?
Cuanto menor sea la frecuencia a la que haya que cambiar los consumibles, como las puntas de contacto, las toberas de gas o las sirgas de avance de hilo de los juegos de cables, mejor. De este modo, se protege el medio ambiente y se reducen los costes de producción.
Por regla general, los consumibles que se adaptan de forma óptima al sistema de soldadura y al material de trabajo duran mucho más. Por lo tanto, los que se utilizan para el acero y las aleaciones de CrNi debe ser distintos de los que se emplean para la soldadura de aluminio o las aplicaciones de CuSi.
Antes de pasar a las 4 medidas, hay que aclarar una cuestión: ¿Por qué dejan de funcionar los consumibles con el tiempo?
Punta de contacto: contacto permanente, desgaste permanente
No se pueden realizar soldaduras MIG/MAG sin una punta de contacto. Esta pieza es donde se produce la transmisión de corriente al hilo de soldadura, que se lleva a cabo mediante el “contacto deslizante”, en el que el hilo y la punta están permanentemente en contacto y se pulen mutuamente.
Por lo tanto, la “abrasión” es una de las razones más comunes por las que las puntas de contacto se vuelven inutilizables con el tiempo. El pulido continuo del hilo cambia el interior de la punta de contacto hasta que se pierde el contacto permanente entre este y el hilo de soldadura. La transmisión de la corriente se vuelve inestable, al igual que el arco voltaico, lo que significa que la punta debe sustituirse.
Sin embargo, también puede ocurrir lo contrario, que la abrasión del hilo y el calor extremo en la punta de contacto provoquen la formación de una capa de aleación. En este caso, la punta de contacto se va cerrando lentamente por dentro hasta que el avance de hilo se bloquea.
Toberas de gas: la lucha contra las proyecciones
El segundo consumible principal en un cuello antorcha MIG/MAG es la tobera de gas. Este es responsable de la formación de la campana de gas protector sobre el arco voltaico. La temperatura tiene una influencia decisiva en la vida útil de las toberas de gas. Si la tobera de gas está demasiado caliente, se adhieren más proyecciones, que a su vez pueden fusionarse con el consumible y, por tanto, ya no pueden desprenderse. Si la tobera está fría, las proyecciones simplemente rebotan.
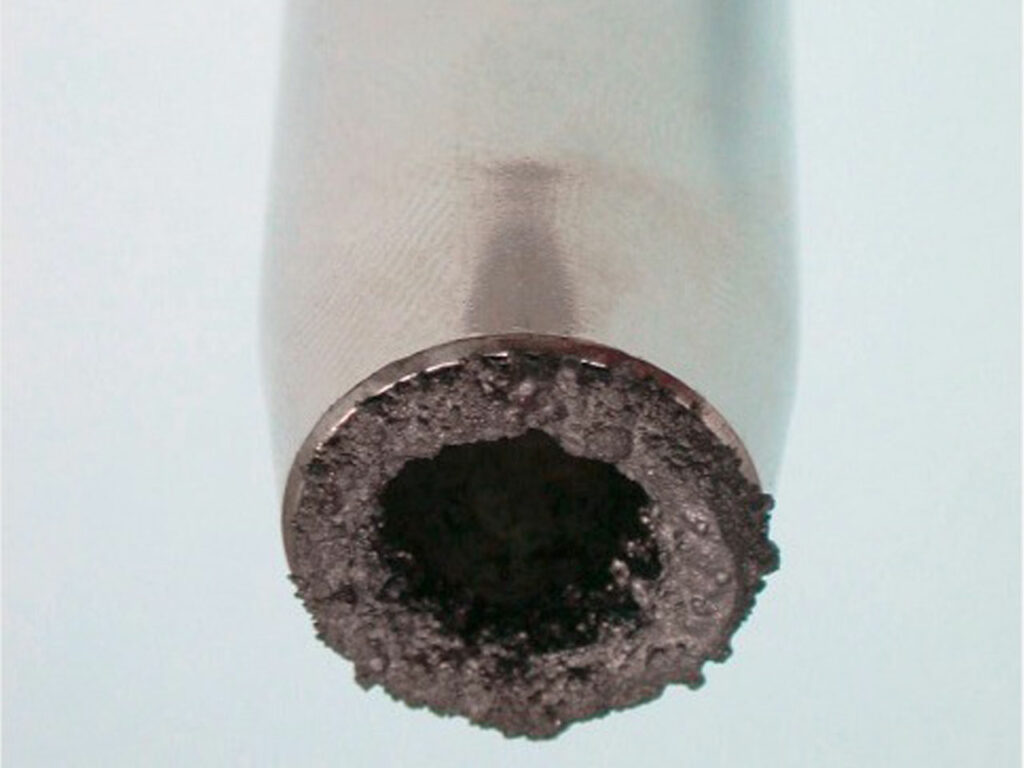
La clave es utilizar diferentes tipos de toberas para el acero y el aluminio respectivamente. Las toberas de gas para el aluminio suelen estar revestidas, lo que facilita la eliminación de las proyecciones de aluminio, que son relativamente blandas.
Sirgas de avance de hilo: el mundo interior de los juegos de cables
La sirga transporta el hilo de soldadura a través del juego de cables y se desgasta con el tiempo debido a la fricción resultante. Estas comienzan en la conexión FCS en la fuente de potencia y terminan en el cuello antorcha en la punta de contacto.
Para conseguir una vida útil lo más larga posible y una aplicación segura de los procesos de soldadura deseados, siempre se deben utilizar sirgas que estén adaptadas completamente al sistema de soldadura utilizado en lo que respecta al diseño y diámetro interno.
Qué hacer para reducir al mínimo el desgaste de las toberas de gas y las puntas de contacto
Mientras que con las sirgas solo se trata de elegir el producto adecuado, la cuestión es algo más compleja en el caso de las puntas de contacto y las toberas de gas. Si se siguen las 4 medidas que aparecen a continuación, la vida útil de estas piezas puede aumentar considerablemente:
Medida 1: Adaptar completamente la punta de contacto y el hilo de soldadura entre sí
La relación correcta entre el hilo de soldadura y la punta de contacto (en concreto, entre el diámetro del hilo y el diámetro del agujero de la punta de contacto) repercute de forma decisiva en la vida útil de este consumible.
El asesoramiento de expertos cualificados es indispensable debido a la compleja interacción de diferentes factores, como la intensidad de corriente, el stickout o las características del hilo. Solo así se pueden atender específicamente las necesidades más diversas, por ejemplo, cuando se trata de utilizar una punta de contacto con un agujero de un diámetro ligeramente menor. De este modo, este se puede desgastar durante más tiempo y, por tanto, durar más.
La vida útil de una punta de contacto también puede verse afectada por la dobladura del hilo, es decir, el grado de curvatura del hilo en la punta de contacto. Si esta es demasiado pequeña, el tubo de contacto se desgastará demasiado rápido. Si es demasiado grande, el contacto deslizante y, por lo tanto, el proceso de soldadura, no funcionará muy bien. ¿La solución? Gracias a los nuevos tipos de puntas de contacto (como los del sistema Contec de semipieza), ya se pueden encontrar en el mercado innovadoras puntas de contacto que se desgastan de manera uniforme y, por tanto, garantizan procesos de soldadura muy estables. Recomendamos Contec para el aluminio o para aplicaciones en las que realmente se necesita una transmisión de corriente óptima.
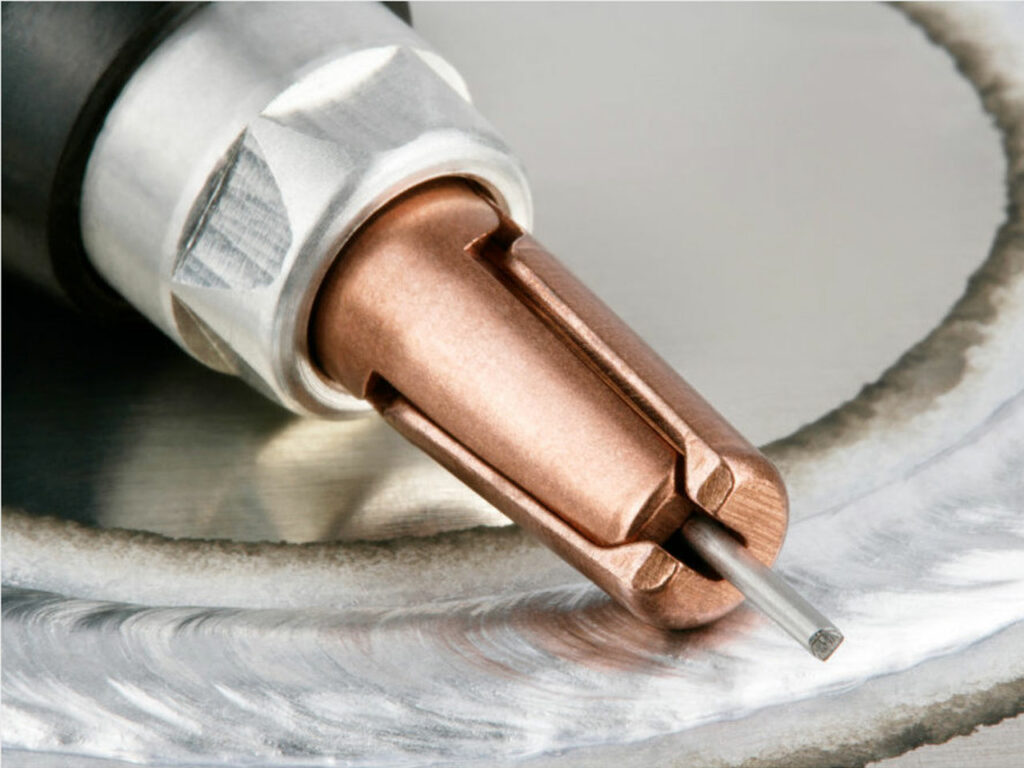
Medida 2: Utilizar puntas de contacto de material de alta calidad
La vida útil de una punta de contacto depende, entre otros, del material con el que se ha fabricado. En la actualidad, se utilizan tres tipos diferentes de puntas de contacto:
Cobre electrolítico o E-Cu: material de bajo rendimiento. Aunque la alta pureza del cobre garantiza una muy buena transmisión de corriente, las puntas fabricadas con cobre electrolítico son muy blandas, poco resistentes al calor y, como consecuencia, poco duraderas, por lo que no se recomiendan para aplicaciones de robot.
Cobre-cromo-circonio o CuCrZr: el estándar del sector. Las puntas de contacto de CuCrZr son las más utilizados actualmente. Los elementos de aleación cromo y circonio hacen que las puntas de contacto sean duras y térmicamente resistentes.
Cobre de tungsteno, calidad WQ: mejor opción para una larga vida útil. Aunque las puntas de contacto WQ no son asequibles en absoluto, ahorran costes a largo plazo porque tienen una vida útil entre cinco y quince veces mayor que las puntas de CuCrZr. Como resultado, la producción no tiene que interrumpirse tan a menudo. Esto hace que su uso sea muy rentable, especialmente en el caso de los hilos duros de acero. Su “secreto”: la parte delantera está hecha de una aleación de tungsteno y cobre extremadamente resistente.
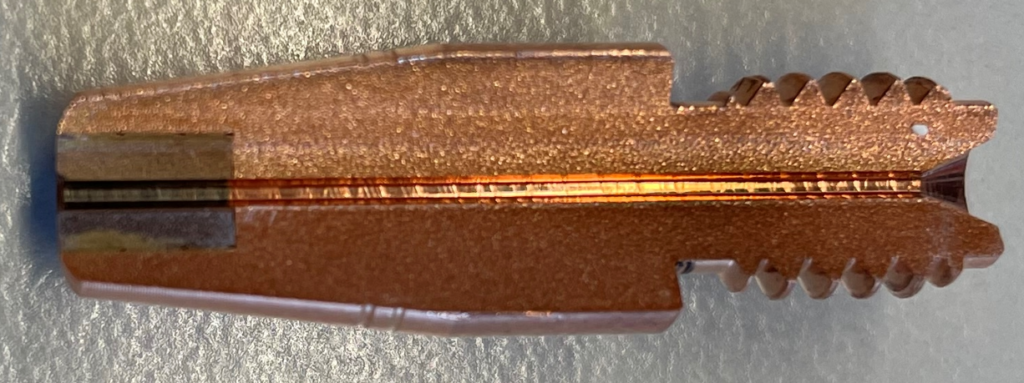
Medida 3: Reducir la influencia del calor de las puntas de contacto y las toberas de gas
Al estar situados en la parte delantera del cuello antorcha, tanto la tobera de gas como la punta de contacto están expuestas a cargas térmicas extremas. Hay dos maneras de reducirlas:
1) Mantener la distancia: cuanto mayor sea el stickout, es decir, la distancia entre la pieza de trabajo y el cuello antorcha, menor será la radiación térmica que actúa sobre la punta de contacto y la tobera de gas. Como regla general, la temperatura en la zona delantera del cuello antorcha baja 50 grados por cada milímetro que se aleja de la pieza de trabajo. Si se aumenta el stickout solo cuatro milímetros, el efecto del calor en la tobera de gas disminuye 200 grados, lo que supone una diferencia significativa.
2) Elegir la forma correcta de punta de contacto y tobera: la forma ejerce una influencia en las temperaturas de la punta de contacto y la tobera de gas que no debe subestimarse. Si se suelda con un stickout corto, se recomiendan puntas de contacto y toberas de gas “afiladas”. Estas tienen un diámetro relativamente pequeño en su abertura frontal, lo que significa que entra menos radiación térmica en el consumible.
Medida 4: Limpiar los cuellos antorcha para prolongar la vida útil
La eliminación sistemática de las proyecciones prolonga considerablemente la vida útil de las puntas de contacto y las toberas de gas. La forma de limpiar un cuello antorcha depende principalmente de si se suelda acero o aluminio:
Para la limpieza del acero y el acero CrNi contamos con estos tres métodos:
Mecánico: el fresado es el método de eficacia más comprobada para la eliminación de proyecciones en los consumibles del cuello antorcha. Varias fresadoras penetran hasta 5 cm en el interior del consumible desde abajo y eliminan las proyecciones de forma mecánica y demostrada. Una buena fresadora también limpia la superficie frontal de la tobera de gas.
Magnético: la ventaja del método de limpieza magnética es que no se establece contacto mecánico con los consumibles. En los dispositivos de limpieza magnética hay bobinas y se genera un fuerte campo magnético mediante un impulso de corriente. La fuerza del campo magnético extrae todas las proyecciones de acero de los consumibles. Este método equivale al fresado, pero no funciona en el aluminio.
Limpieza de aluminio y CuSi: cepillado
Las proyecciones de aluminio son demasiado blandas para eliminarse mediante el fresado, que solo las mancharía. Por lo tanto, la limpieza en la soldadura de aluminio o las aplicaciones de CuSi se realiza mediante cepillos. El principio básico es el mismo que el del fresado.
Conclusión
La vida útil de los consumibles en el proceso MIG/MAG depende principalmente de los siguientes factores:
- Selección correcta de los consumibles: adaptación óptima al campo de aplicación correspondiente.
- Calidad de los consumibles utilizados, especialmente en lo que respecta a las cargas térmicas y mecánicas.
- Interacción de los consumibles con los demás componentes del sistema de soldadura.
- Sistemas de limpieza eficientes
Todas las puntas de contacto Fronius y las toberas de gas se desarrollan en Austria y, al igual que todos los consumibles Fronius, se adaptan de forma específica a la aplicación correspondiente. Por ejemplo, Fronius tiene en su gama de productos más de 300 toberas de gas para la soldadura del acero.
Si deseas saber más sobre qué puntas de contacto, toberas de gas o sirgas de avance de hilo son las más adecuadas para una situación concreta, no dudes en ponerte en contacto con nosotros. Además, puedes ponerte en contacto con una de nuestras 27 subsidiarias internacionales, donde nuestros expertos estarán a tu disposición para ayudarte y asesorarte.
No hay comentarios