Es evidente por qué está aumentando el número de empresas de construcción metálica que confían en la impresión 3D (conocida simplemente como WAAM, o Wire Arc Additive Manufacturing en la jerga del sector). Esta situación se debe a que las diversas opciones de personalización que ofrecen los modernos sistemas de producción han generado una demanda de soluciones individuales a medida. Cada vez necesitamos más piezas de recambio que no se fabrican en serie en el plazo más breve posible. Además, en la construcción de prototipos, no solo queremos ahorrar en costes de herramientas, sino también acortar los plazos de desarrollo. Donde la fabricación aditiva demuestra mejor sus puntos fuertes es en el cumplimiento de estos requisitos. Geometrías de componentes que ayer parecían imposibles ahora se realizan capa a capa mediante la impresión 3D con metal, exactamente cuando las necesitamos.
WAAM: Menos material, menos peso, menos costes
Si comparamos la impresión 3D con metal con los procesos de mecanizado como el fresado, está claro que el Wire Arc Additive Manufacturing consume mucho menos material. Cuanto más suben los precios de las materias primas, más rápido se amortiza este tipo de producción.
Tampoco se requieren moldes elaborados, pues ya no es necesaria la fundición. En su lugar, podemos utilizar la moderna tecnología de soldadura para fabricar componentes metálicos complejos y de topología optimizada, capa por capa y a medida. En la jerga del sector, estas instrucciones se denominan Additive Manufacturing Procedure Specification (AMPS). Una AMPS contiene todo lo que necesitamos para completar un “proceso de impresión” perfecto: las instrucciones de soldadura individuales (Deposition Procedure Specifications o DPS), los certificados del operario y de materiales, así como la estrategia cinemática que necesitamos para la planificación de la trayectoria y el control del movimiento del robot de soldadura. Los certificados de materiales garantizan una calidad conforme a la producción de hilo de soldadura.
Por otra parte, los certificados de operario garantizan que las celdas de soldadura robotizadas DED-Arc utilizadas habitualmente en la fabricación aditiva solo sean manejadas por especialistas cualificados. DED-Arc son las siglas de Directed Energy Deposition Arc, que es un arco voltaico empleado para fundir hilo de soldadura capa por capa.
“Con la optimización de la topología, queremos garantizar la distribución ideal del material de los componentes. En sentido estricto, el objetivo es reducir el peso manteniendo la rigidez”, explica Philipp Roithinger, Experto en Impresión 3D con Metal, y prosigue: “Las aplicaciones típicas son las estructuras biónicas inspiradas en la naturaleza, como las que se encuentran en el sector aeroespacial. Otra ventaja de la impresión 3D con metal es la posibilidad de la producción descentralizada. No se requieren líneas de producción, independientemente de la ubicación, como en el caso de la producción en serie. La fabricación aditiva con hilo de soldadura se caracteriza por celdas de soldadura robotizadas especialmente equipadas que pueden utilizarse de forma flexible en cualquier parte del mundo. Confiamos cada vez más en la impresión 3D con metal cuando se trata de reducir el peso, el material, los costes y el impacto medioambiental en la construcción metálica”.
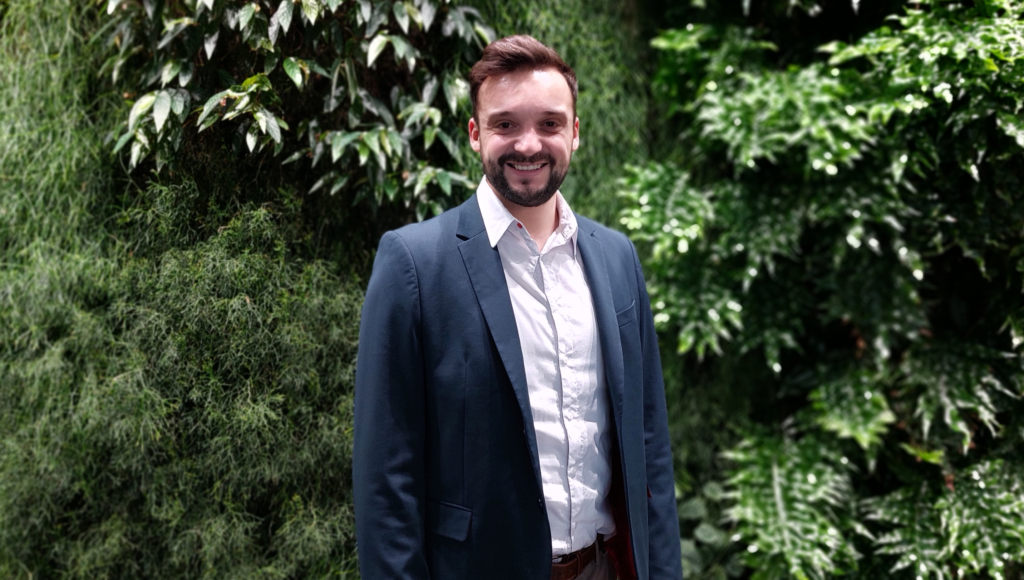
Indispensable para la impresión 3D con metal: Arco estable como en la soldadura CMT
Para conseguir la calidad deseada, necesitamos un proceso de soldadura extremadamente estable para la soldadura aditiva, como CMT (Cold Metal Transfer). CMT es un proceso de arco voltaico corto “frío” que mantiene una aportación térmica reducida a pesar de su alta tasa de deposición. Esto funciona debido a que se desencadena el desprendimiento de gota por el movimiento retráctil del electrodo de hilo.
En el proceso de arco corto convencional, que es menos adecuado para WAAM y genera una mayor aportación térmica, el hilo se mueve continuamente hacia la pieza de trabajo, a diferencia de lo que ocurre con CMT. En cuanto el extremo del hilo reblandecido toca el baño de fusión, se produce un cortocircuito. Una gran parte del hilo líquido fluye hacia el baño de fusión, produciéndose el denominado desprendimiento de gota. En la fase de cortocircuito, la tensión de soldadura tiende a cero, mientras que la corriente aumenta hasta un valor elevado, el cortocircuito se interrumpe y el arco se vuelve a encender.
El desprendimiento de gota y el nuevo cebado del arco se producen de forma más controlada en el proceso CMT y con una menor aportación térmica que en el arco corto, concretamente mediante un movimiento de retroceso del electrodo de hilo en la fase de cortocircuito. En función de la curva característica del material de aporte, del gas protector y del diámetro del electrodo de soldadura, el movimiento retráctil del hilo se produce en una gama de frecuencias de 50 a 170 Hz.
La aportación térmica generada durante la soldadura CMT es hasta un 33 % inferior a la de la soldadura convencional por arco corto. Por lo tanto, este proceso es ideal para la soldadura aditiva, en la que el recargue cíclico de cordones de soldadura provoca una elevada aportación térmica. Si la temperatura del componente es demasiado alta, se reducen las propiedades del material y se producen tiempos de espera. En tal caso, el proceso de soldadura debe interrumpirse hasta que las capas de soldadura se hayan enfriado. Las fluctuaciones de distancia de la punta de contacto son menos críticas con CMT, el arco permanece estable y el sistema de hilo único proporciona un grado adicional de libertad a la hora de programar el robot.
CMT Additive Pro: Aportación térmica específica para una formación de capa constante
El proceso CMT admite funciones especialmente adecuadas para la impresión 3D con metal, como la “corrección de potencia”. Esto significa que la potencia eléctrica utilizada puede adaptarse con precisión a cada fase del proceso, a la estructura de las capas y a la aportación térmica. La tasa de deposición permanece constante.
“Con nuestras funciones CMT Additive Pro especialmente desarrolladas para la fabricación aditiva, como la corrección de potencia o el estabilizador de deposición (Deposition Stabilizer), podemos controlar de forma específica la entrada de potencia y, por tanto, la altura y la anchura del cordón”, prosigue Roithinger.
Si el proceso de soldadura tiene que reiniciarse durante la formación de la capa debido a la sustitución de bidones de hilo vacíos, esto puede constituir una fuente de error que no debe subestimarse. Los defectos de unión resultantes o las sobreelevaciones de cordón en la zona de inicio de la soldadura perjudicarían enormemente la calidad de los componentes de fabricación aditiva. Aquí es donde entra en juego la función Pulsed HotStart. Cuando está activa, se logra la penetración necesaria en el nuevo inicio de la soldadura con arco pulsado, al mismo tiempo que la altura de capa se mantiene constante.
Servicio 360° en el centro de prototipos de Fronius
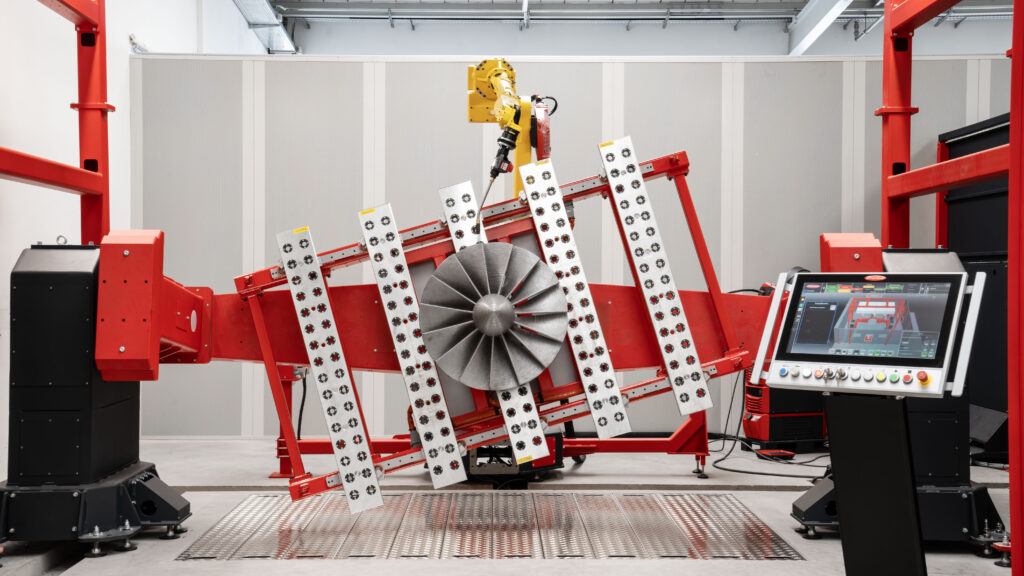
Ofrecemos una amplia gama de servicios en el centro de prototipos de Wels (Austria). Entre ellos se incluyen los estudios de viabilidad, soluciones personalizadas para los requisitos individuales de los clientes, optimización de procesos y producción de prototipos, todo ello en cooperación con nuestros clientes y de forma estrictamente confidencial. En la construcción de prototipos, queremos que el periodo desde el desarrollo hasta la madurez del producto sea lo más corto posible. Para ello, aprovechamos todo nuestro potencial de tecnología de soldadura.
Si es necesario, nuestros expertos prestan apoyo no solo en la construcción de prototipos, sino también en la producción de preseries. Permiten a los clientes dar sus primeros pasos fácilmente en la impresión 3D con metal robotizada y ofrecen recomendaciones pertinentes sobre el proceso de soldadura, la rentabilidad, la calidad y la producción. En el centro de prototipos, de unos 900 m² de superficie, se dispone de sistemas robotizados con tecnología avanzada de soldadura, sensores y medición. También hay un laboratorio de soldadura donde se pueden realizar ensayos no destructivos y destructivos de componentes. Nuestro paquete de servicio completo incluye programación offline, simulaciones, análisis metalúrgicos, medición de componentes en 3D, documentación de datos de soldadura y mucho más.
Nuevas normas para la impresión 3D con metal
Las primeras normas sobre fabricación aditiva basada en arco voltaico se están elaborando ahora en diversas industrias. Junto con Linde Engineering, que ha proporcionado su caso de uso, el fabricante de hilo Migal.co y TÜV Süd Deutschland, trabajamos con Fronius en la cualificación de modelos de tanque a presión de fabricación aditiva en forma de desvío de tubo. Se ha revisado la aplicabilidad del proyecto de norma preEN 13445-14 para el uso de tanques a presión de fabricación aditiva.
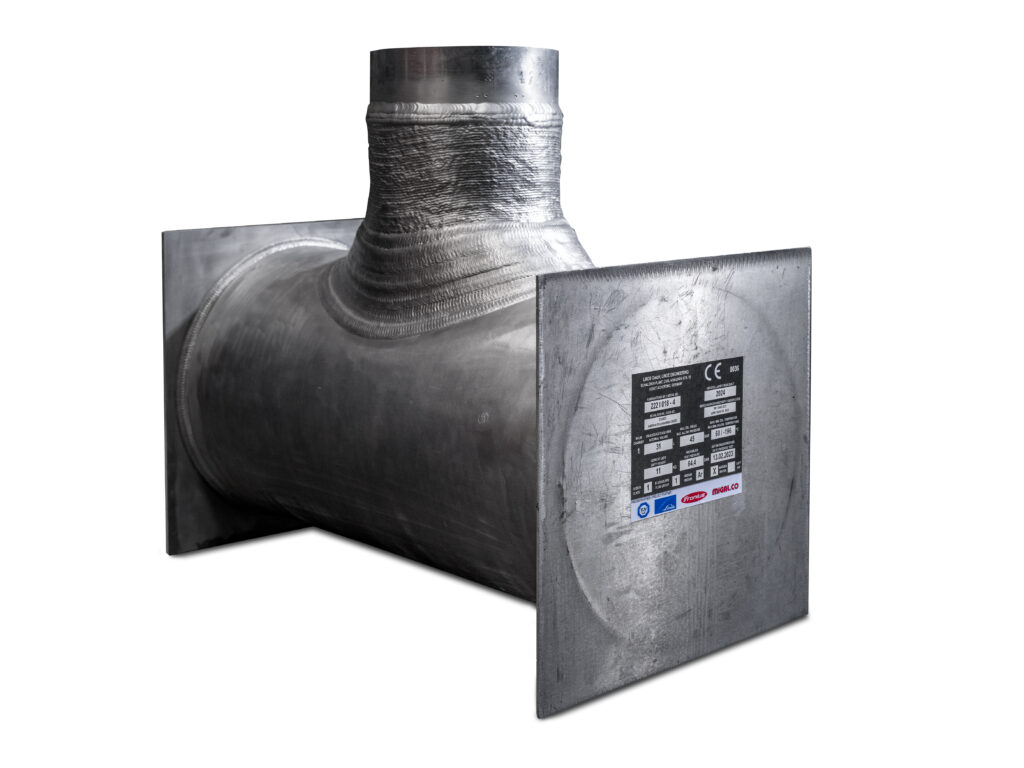
En la impresión 3D con metal, la calidad de los materiales utilizados es decisiva. En este caso concreto, se eligió una aleación de aluminio forjado de dureza natural. Gracias a su excelente tenacidad a bajas temperaturas, de hasta -273 °C, este material, que también se utiliza en la construcción ligera, es especialmente adecuado para la construcción de sistemas de tuberías.
El mencionado proyecto de normativa europea tiene en cuenta toda la cadena de valor de la fabricación aditiva, incluidos los detalles de supervisión necesarios. De este modo, se garantiza el correcto cumplimiento de los requisitos básicos de seguridad definidos en la Directiva de Equipos a Presión.
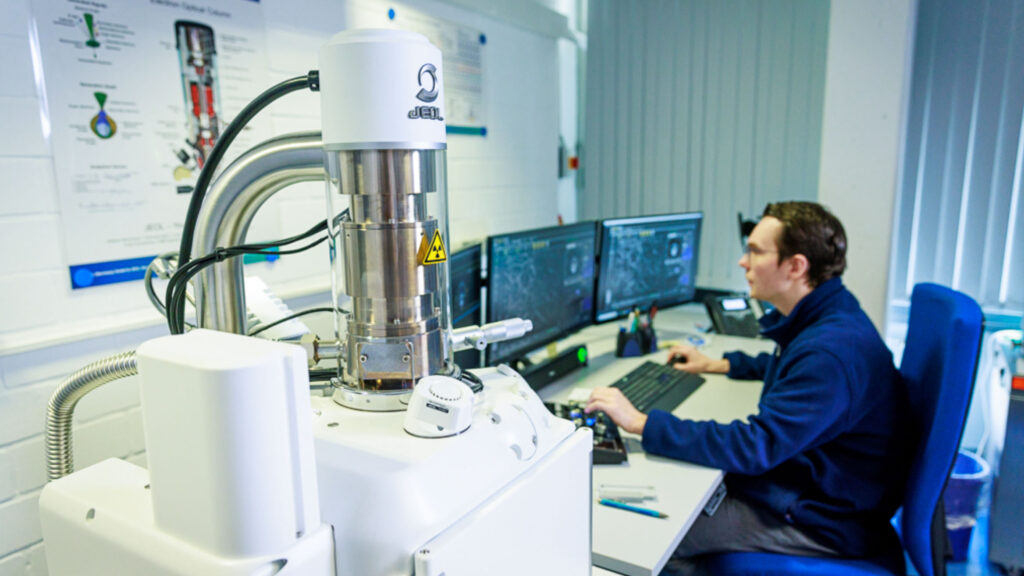
Durante la cualificación de modelos, comprobamos y documentamos toda la cadena del proceso, desde el diseño, la construcción, la producción y la planificación de la trayectoria, la supervisión del proceso hasta el ensayo de presión final.
Podrás encontrar más información sobre la cualificación de modelos de tanque a presión con la certificación CE final de TÜV Süd en el siguiente vídeo: YouTube
No hay comentarios