Navařování je speciální svařovací postup, který zajišťuje prodloužení životnosti průmyslových součástí a zařízení. Zejména tam, kde jsou komponenty vystaveny extrémním podmínkám, například vysokým teplotám, tlaku nebo agresivním chemickým látkám, je potřebná přidaná ochranná vrstva, aby se zabránilo fatálním následkům.
Proč se ropný a plynárenský průmysl bez navařování nezaobejde
Především v ropném a plynárenském průmyslu hraje navařování zásadní roli. Stále znovu dochází v důsledku netěsnosti potrubí k únikům velkého množství těžkých olejů do oceánů. Tyto netěsnosti jsou nebezpečné i v případě plynových vedení, protože snadno zápalné plyny mohou při kontaktu se zápalným zdrojem, jako jsou kyseliny, způsobovat požáry či dokonce výbuchy. Smutným příkladem je „ohnivé oko“ v mexickém zálivu. V roce 2021 došlo v důsledku úniku plynu z potrubí 150 metrů od vrtné plošiny pro těžbu ropy Ku-Maloob-Zaap k ničivému podmořskému požáru.
Jisté je, že když se jedná o ochranu potrubí a jiných kritických zařízení, nemělo by se opomenout žádné opatření, které nabízí další ochranu. Navařování minimalizuje potenciálně nebezpečná slabá místa. Díky přidané ochranné vrstvě se prokazatelně snižuje riziko úniků, což může zabránit nejen hospodářským škodám, ale také škodám na životním prostředí.
Navařování jako univerzální talent v povrchové technice
Navařování ovšem není potřebné pouze v ropném a plynárenském průmyslu. Používá se i při výstavbě elektráren, aby se membránové stěny a deskové topné plochy chránily před agresivními škodlivými látkami. Příkladem jsou spalovny odpadů a elektrárny na biomasu, v nichž dochází k výraznému nárůstu podílu síry a halových prvků v kovových komponentách.
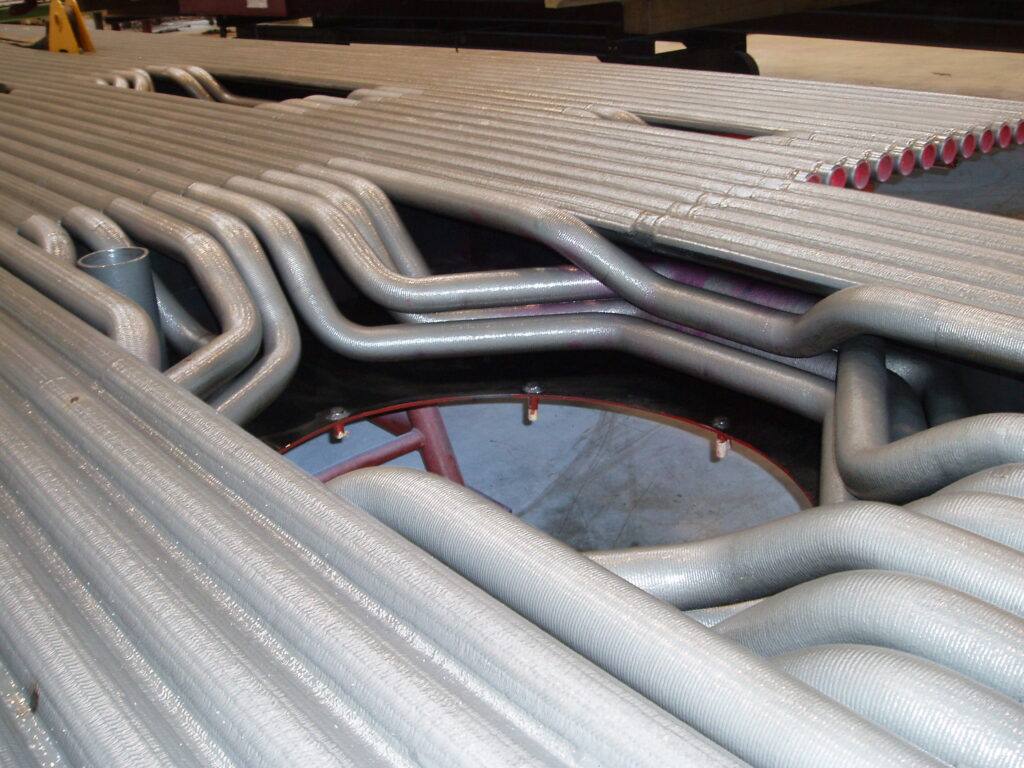
Navařování je proto vždy vyžadováno tam, kde je třeba cíleně zlepšovat vlastnosti povrchu. Jedná se o situace, kdy je třeba zvýšit odolnost vůči opotřebení a korozi, jako třeba v případě parních turbín, které jsou vystaveny kondenzující vlhkosti. Opravy a renovace navařovaním zároveň šetří i váš rozpočet – jsou totiž hospodárnou variantou, která nevyžaduje výměnu celé součásti.
Více než pouhé „přivaření na povrch“
Jednoduchý přístup „prostě je to přivařené a drží to“ při navařování nestačí. Aby kovové vrstvy odolaly extrémnímu zatížení, musí být spolehlivě spojeny se základním materiálem. Tento proces je velmi složitý a vyžaduje přesné nastavení parametrů svařování, aby nebyly ohroženy nákladné komponenty.
V praxi se proto navařování provádí nejčastěji automaticky s použitím svařování horkým drátem TIG (TIG-HD) nebo procesu CMT. Rozhodujícím faktorem pro kvalitu je takzvané promísení. Popisuje, kolik základního materiálu svařence se promísí s nanášeným materiálem. Potřebné je nízké promísení, aby si nanášený materiál udržel své speciální vlastnosti, jako je požadovaná vysoká odolnost vůči korozi.
Podrobný pohled na techniky navařování
V principu se při navařování mluví o přidávání objemu v podobě krycí vrstvy s použitím přídavného materiálu, jako je drát či prášek. Používají se speciální slitiny jako Alloy 50 a 625, CrMo 910 nebo Inconel 625. Z toho plyne zásadní výhoda povrchové krycí vrstvy: běžnou ocel lze kombinovat s vysoce kvalitními slitinami a díky tomu je navařování mimořádně hospodárné.
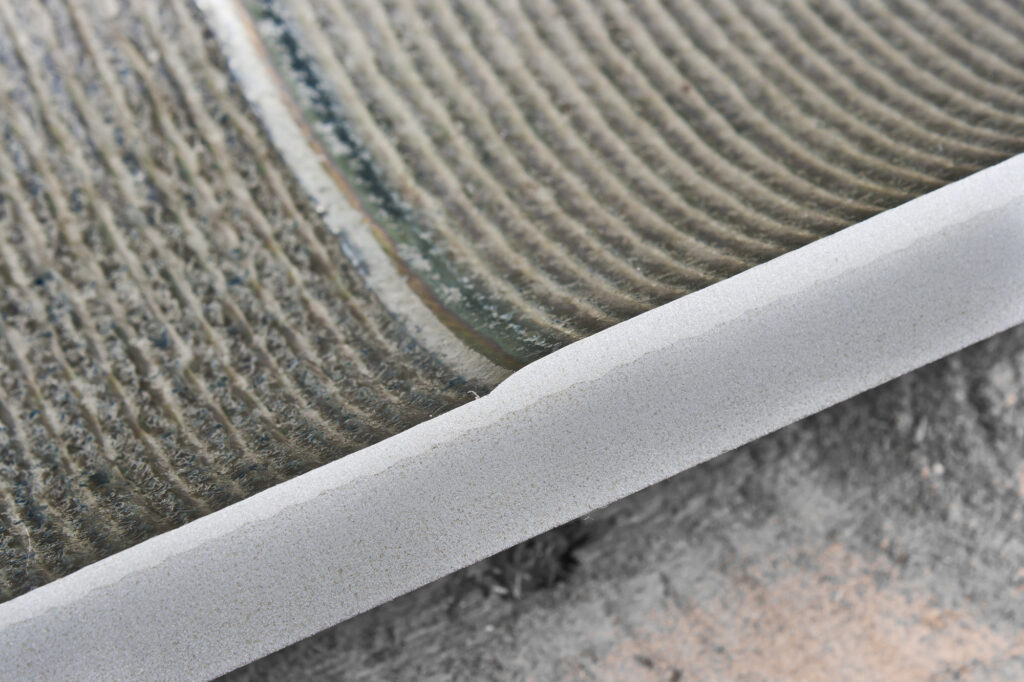
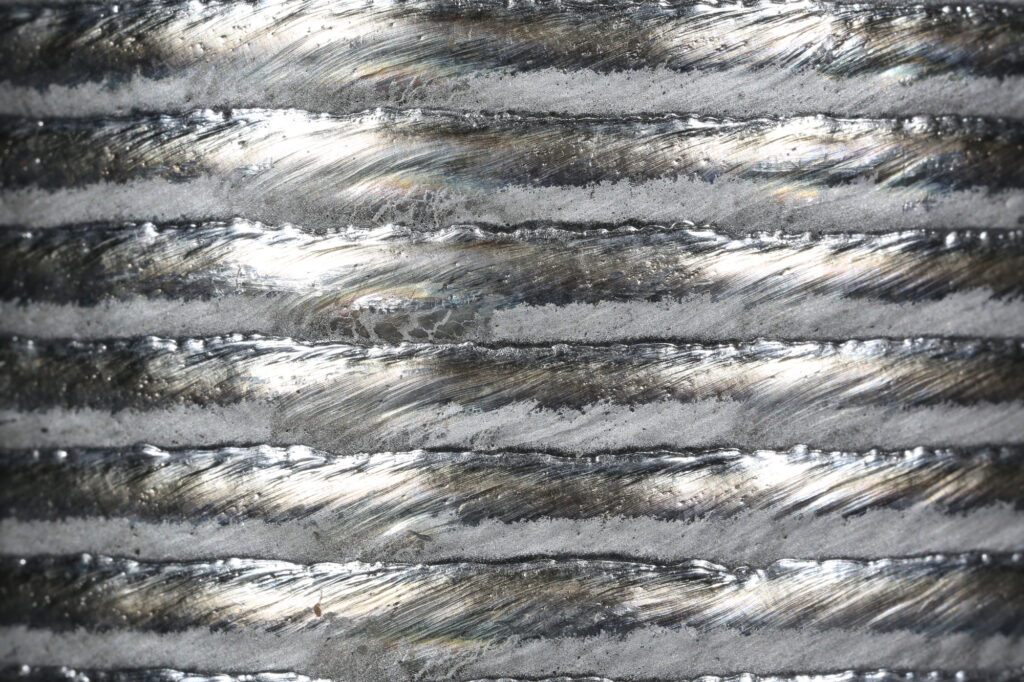
S ohledem na enormně vysoké bezpečnostní požadavky se v ropném a plynárenském průmyslu používá především svařování horkým drátem TIG. Běžnými metodami jsou však i laserové navařování a plazmové práškové navařování. Nejvhodnější postup nelze obecně určit, protože každý postup nabízí specifické výhody, které je třeba zohlednit podle materiálu, velikosti součásti a požadavků.
Svařování horkým drátem TIG pro absolutní přesnost
Svařování horkým drátem TIG představuje vylepšení běžného svařování TIG (svařování metodou wolfram-inertní plyn). Dochází při něm k elektrickému předehřívání dalšího drátu, než se přivede do tavné oblasti. To vede k výraznému zvýšení odtavného výkonu a účinnosti svařovacího procesu, čímž se minimalizuje riziko vzniku vad, jako jsou trhliny či deformace.
Ve výsledku je svařování horkým drátem TIG všestranně použitelné a umožňuje vytváření vysoce kvalitní krycí vrstvy s rovnoměrnými svarovými spoji bez rozstřiku, které splňují nejpřísnější bezpečnostní normy. Jedinou nevýhodou je, že svařování horkým drátem TIG je časově velmi náročné, především v případě velkých komponent nebo při sériové výrobě.
Tuto skutečnost lze obejít využitím systému SpeedClad 2.0. Proces technologicky pokročilého navařování vyvinutý společností Fronius umožňuje dosahovat výrazně vyšší rychlosti svařování až 110 cm/min jen s použitím speciálně tvarované elektrody a přídavného drátu. Úzký svařovací hořák navíc umožňuje vytváření krycí vrstvy s malým vnitřním průměrem do 100 milimetrů.
Nízký vnos tepla díky CMT
Ačkoli se v ropném a plynárenském průmyslu využívá především svařování horkým drátem TIG, mnohé podniky v oblasti výstavby elektráren sázejí na procesy MIG/MAG (případně na proces CMT) například při vytváření krycí vrstvy membránových stěn nebo jiných součástí. Výhodou je, že díky digitální regulaci procesů jsou zkraty rozpoznávány nezávisle. Kromě toho je při zatahování drátu podporováno uvolnění kapky.
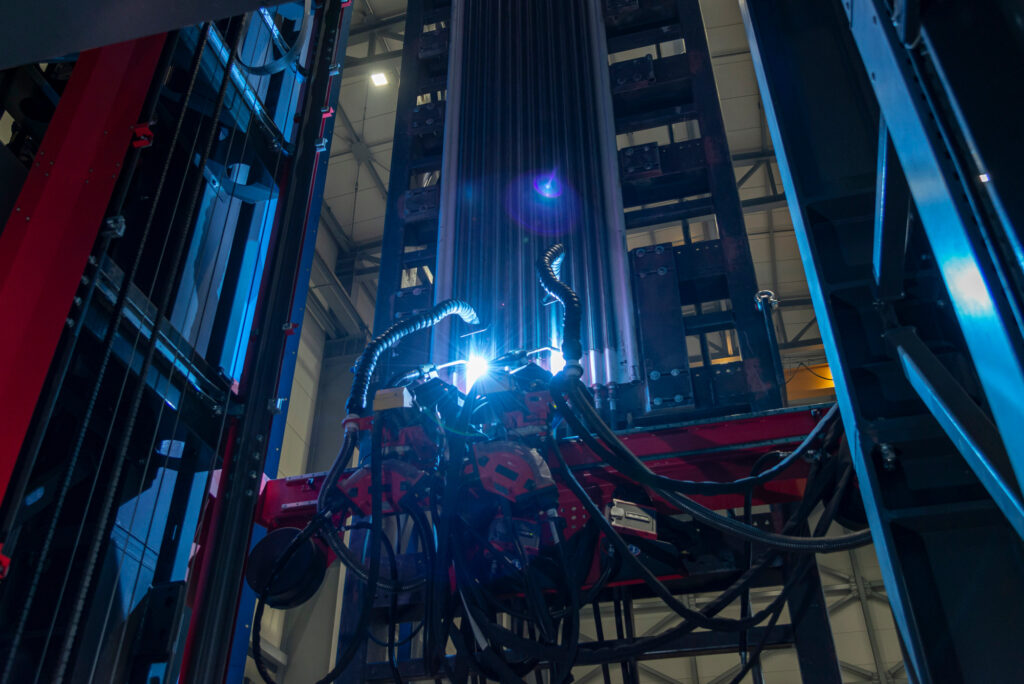
Tento pohyb vpřed a vzad zajišťuje krátkou fázi hoření oblouku, čímž se výrazně snižuje vnos tepla. Dochází k téměř bezrozstřikovému vytváření krycí vrstvy s mimořádně hladkým povrchem, měkkými překryvy svarů a konstantní tloušťkou.
Snazší navařování TIG
V dodavatelském průmyslu výrobní podniky rády sahají po takzvaných navařovacích buňkách, aby dosáhly stabilního svařovacího prostředí. Osvědčil se zde systém Fronius Compact Cladding Cell (CCC) jako výkonné a hospodárné řešení. Na pouhých 6 metrech čtverečních půdorysu nabízí dostatečnou kapacitu pro jednoduché geometrie součástí s průměrem až jeden metr a výškou až 1,9 metru při maximální hmotnosti 2 500 kilogramů – a je tedy dokonale vhodný pro vytváření vnitřní krycí vrstvy ventilů.
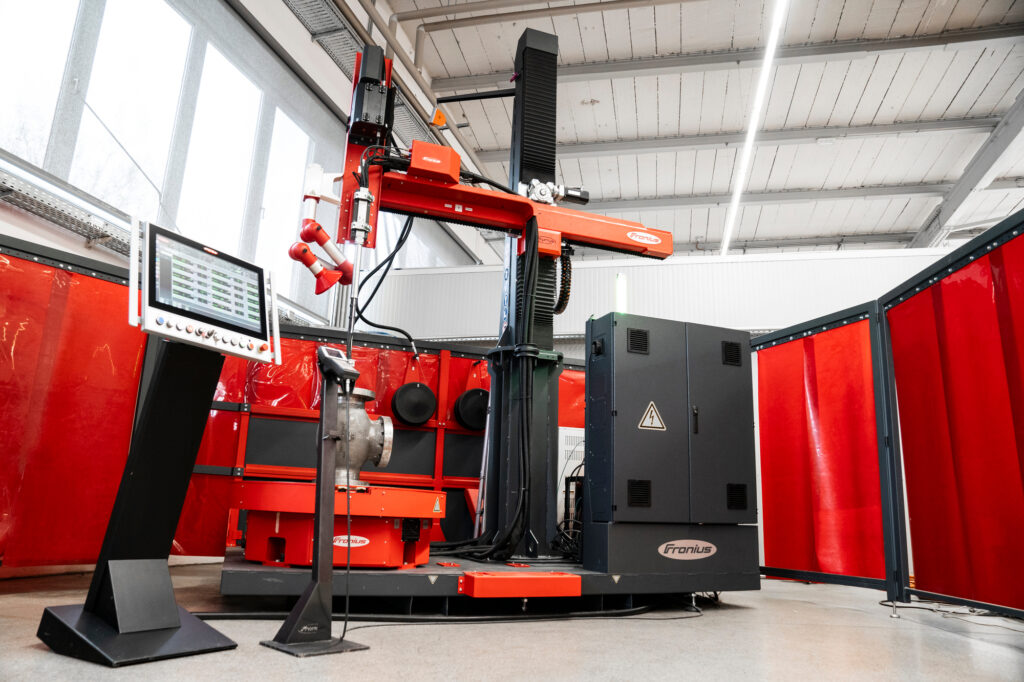
Systém Compact Cladding Cell provádí výlučně svařování horkým drátem TIG nebo systémem SpeedClad 2.0 pro dosažení maximální kvality svarových spojů. Díky funkcím, jako je ergonomické uchycení cívky drátu, 21-palcový dotykový displej nebo vizualizace procesu v reálném čase, je proces vytváření krycí vrstvy nejen uživatelsky komfortní, ale lze jej rovněž velmi dobře monitorovat, aby se zabránilo vzniku chyb. Díky kompaktní konstrukci lze systém CCC snadno přepravovat z místa na místo pomocí vysokozdvižného vozíku – jedná se o prostorově úspornou možnost pro malé dodavatelské firmy zpracovávající objednávky vytvoření krycí vrstvy v ropném a plynárenském průmyslu.
ETR: přesné navařování pro složité geometrie součástí
V případě větších a složitých součástí bodují systémy ETR (Endless Torch Rotation) díky neomezeně rotující svařovací hlavě, která umožňuje automatické zjišťování určování polohy svařovacího hořáku v 3D prostoru – a doba přípravy je tudíž krátká. Další výhodou jsou synchronizované osy pohybu, takže se svařovací hořák a polohovadlo, na kterém se součást nachází, pohybují vzájemně synchronně.
Svařovací hořák se může neustále nacházet na pozici optimální pro proces navařování a zabraňuje se vytékání svarových spojů. Krycí vrstvu lze tedy automaticky vytvářet i na složitých geometriích. Díky 21palcovému dotykovému displeji, který je součástí výbavy, jsou systémy ETR kompatibilní se systémem SpeedClad 2.0 a nabízejí uživatelsky komfortní ovládání, vizualizaci v reálném čase – a ve výsledku vysokou produktivitu.
Závěr: Navařování jako nepostradatelné řešení
Ať už se využívají moderní navařovací buňky nebo systémy jako ETR, navařování je zůstává nepostradatelným procesem, který nás chrání před nebezpečnými selháními materiálu v důsledku koroze a abraze. Díky skutečné všestrannosti moderních procesů navařování je možné najít optimální řešení pro každý požadavek.
Chcete se dozvědět více o jednotlivých procesech a řešeních navařování? Další informace najdete na naší webové stránce.
Žádné komentáře