Modern hydraulic excavators effortlessly clear over 20 tons of earth, rock, and rubble like a huge mechanical arm. Yellow goods, such as excavators, wheel loaders, caterpillar bulldozers, and agricultural machinery are subjected to enormous strain. Alongside maneuvering heavy loads on unpaved ground, the equipment also has to withstand the immense pressure- and tractive forces of the constant digging, lifting, and swiveling movements.
This is a major challenge for the joints, whose job it is to reliably hold together the load-carrying components. Every weld must be perfectly executed to avoid cracks and fractures, which can lead to machine failures or even accidents at work.
High standards and requirements
When manufacturing yellow goods, heavy steel plates have to be joined together over and over. Components with material thicknesses of over 50 mm and meter-long welds are not the exception, but rather the rule. In addition to the weld quality, the seam appearance also plays a huge role, given that the numerous visible seams are crucial to the product’s overall, high-quality appearance. For these reasons, advanced welding technology is essential.
Tandem welding for optimum filling volumes
“The challenges welders face when welding yellow goods are reliable gap bridging to overcome component tolerances, and filling the large weld volumes,” says Bernd Rutzinger, Segment Manager for Yellow Goods at Fronius Perfect Welding. According to the expert, a high duty cycle and deposition rate is needed to deposit the required filling volume and precisely control the wire electrodes. But how is this done? “With tandem welding,” he confirms.
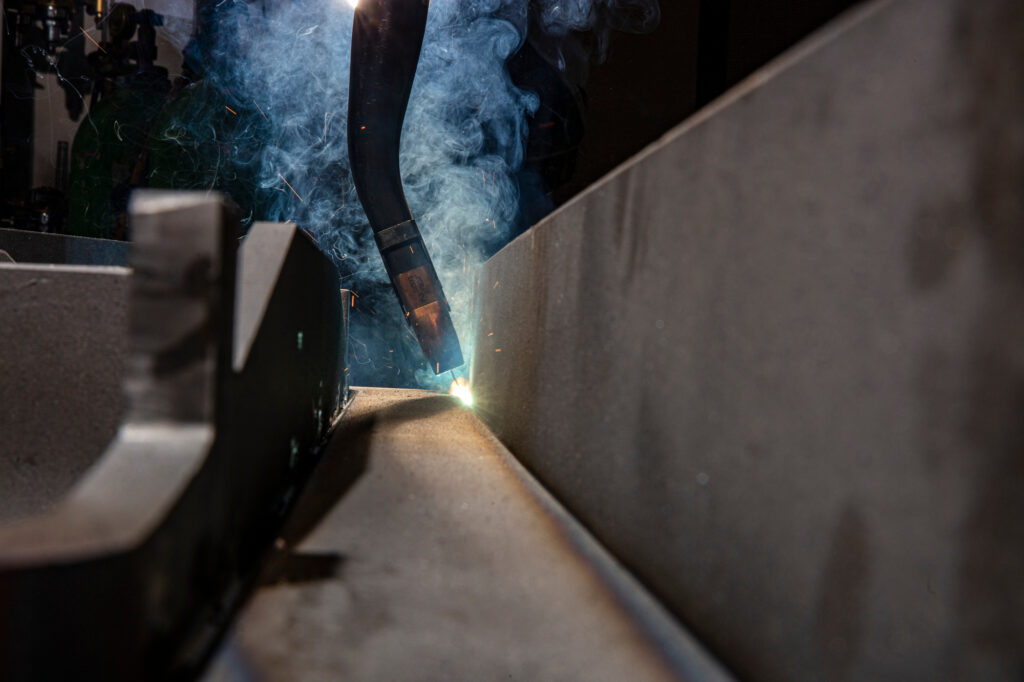
Reliable process for high-strength steels
Tandem welding is high-performance MIG/MAG welding using two wire electrodes. It is a fully automated process using robots, which increases the welding speed and makes a higher deposition rate possible. As two wire electrodes are melted at the same time, it is particularly suitable for bridging the larger gap widths of yellow goods.
The wire electrodes are routed through two electrically isolated contact tips, which creates separate electrical potentials. The advantage of this separation is that the arcs can be controlled independently and, despite differing outputs, can be precisely coordinated.
Twice the speed with the same level of quality
Both wires still work in the same gas atmosphere and form one weld pool. However, each one performs a different task: the first wire—known as the “lead wire”—is responsible for the penetration, while the second, or trail wire, is primarily used to fill the weld volume.
The higher deposition rate results in increased welding speeds and shorter production times compared to single-wire welding. What’s more, only the occasional manual readjustment is needed, saving a considerable amount of time. “However, the key selling points of this process are the outstanding weld quality and appearance,” adds Bernd Rutzinger.
Switching from two wires to one
Tandem welding is therefore not only a time-saver, but also produces high-quality welding results. It is extremely flexible, as the arcs can be controlled independently and precisely. Out-of-position welding is much easier to avoid as it is possible to change the direction of the welding torch.
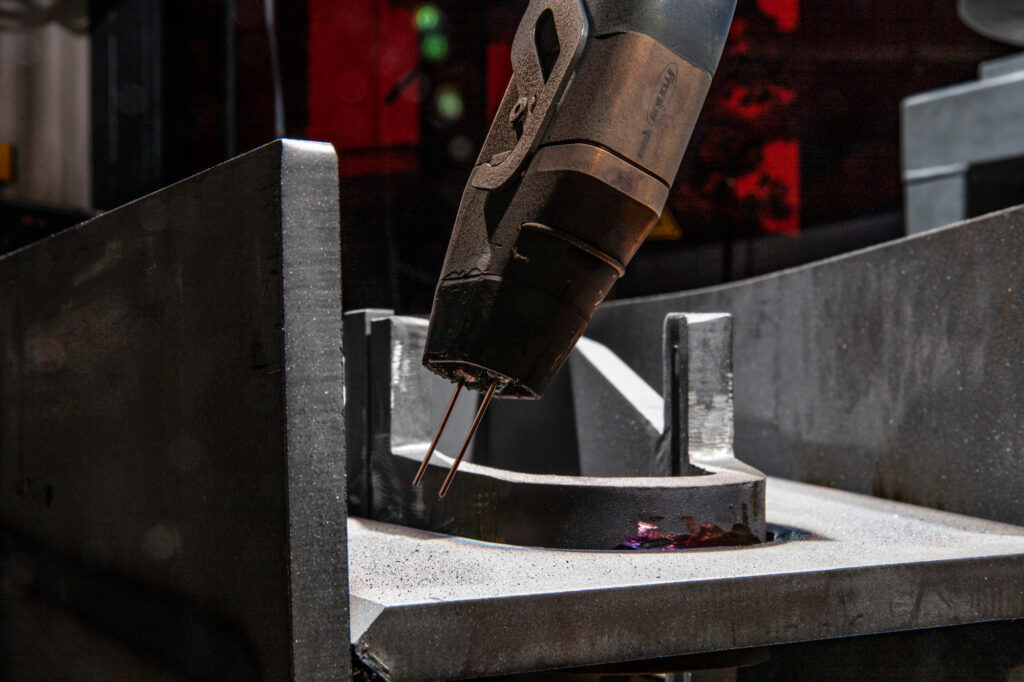
For example, for difficult-to-access welds, the torch body can be changed from tandem to single wire, increasing the system’s range of applications. This feature requires the welding process not to be interrupted: the TWIN Controller, which is connected to the robot controller, is used to switch from two wires to one. What’s more, it is also possible to use different arc types with the two wires, such as a spray arc and PMC (Pulse Multi Control).
Coordination skills required
Despite its many advantages, there are a few things to consider when employing tandem welding. The biggest challenge is successfully controlling both arcs. Our TPS/i TWIN welding system, which provides intelligent welding parameters, is a great help for this. The arc length correction and penetration stabilizer are two functions used in combination to compensate for minor deviations like fluctuating distances between the contact tip and workpiece or improper preparation.
Synchronized arcs thanks to intelligent assistance
The TPS/i TWIN welding system has two independent welding machines, two wire drives, and two contact tips. The electrically isolated contact tips are housed in one torch body. Once the welder has configured a few settings, such as the wire speed or welding voltage, the TWIN system is ready to use.
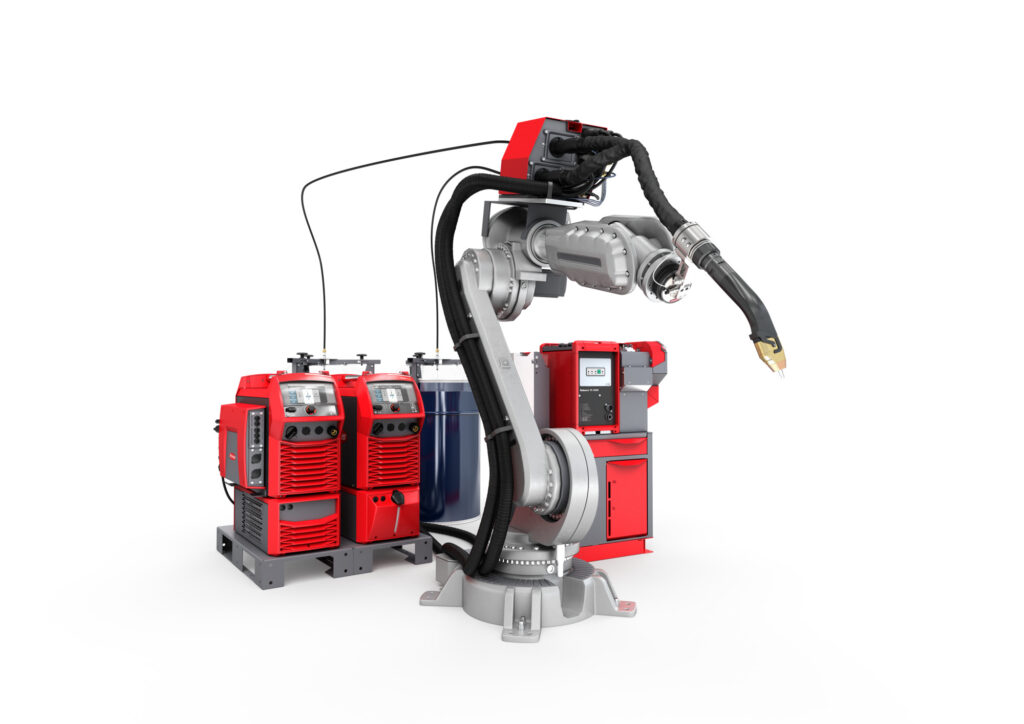
The two welding machines can be perfectly coordinated using the TWIN Controller, which serves as an interface to intuitively operate the robot. The welding system is also ideal for high-strength and low-alloy steels, making it an effective solution for the weld requirements of yellow goods. “The new TPS/i TWIN system is easy to operate thanks to the synchronization and full-text display. For the user, this means an efficient production process with less rework required and increased productivity,” summarizes Rutzinger.
The all-rounder for yellow goods
Whether it’s used with or without the intelligent assistance, tandem welding has become an established process for joining thick materials. As a true superhero among the welding processes, it masters the most demanding weld requirements of construction vehicles and agricultural machinery with ease.
No Comments