Con un flujo regular de intensidades de corriente en el arco voltaico de hasta 700 amperios, es evidente que la soldadura es un proceso que consume mucha energía. Esto plantea la siguiente pregunta: ¿se puede ahorrar energía? La respuesta es sí. Los equipos y procesos de soldadura eficientes desde el punto de vista energético desempeñan un papel fundamental. Te mostramos cinco características que deben tener los equipos de soldadura para incluirse en este grupo.
Como muchos otros procesos técnicos, la soldadura también tiene un impacto en el medio ambiente. Consume recursos como energía, gas protector, hilo de soldadura y diversos consumibles, al mismo tiempo que se libera humo de soldadura a la atmósfera.
Hay varias formas de ahorrar recursos durante la soldadura, empezando por una fabricación que conserve recursos, el empleo de equipos duraderos, reparables y reciclables, la utilización de sistemas multiproceso y el uso optimizado de consumibles. Pero, ¿cuál es el potencial de ahorro del consumo energético?
Esencialmente, se puede afirmar que las propiedades técnicas del equipo de soldadura utilizado desempeñan un papel fundamental cuando se trata de eficiencia energética. Entonces, ¿qué características técnicas debe tener un equipo para soldar de la forma que ahorre más energía?
Tecnología Inverter en lugar de los antiguos equipos de soldadura analógicos
El Transarc 500 con tecnología Inverter, lanzado al mercado por primera vez en 1981, representa un salto cualitativo en el desarrollo de equipos y procesos de soldadura. En comparación con los sistemas analógicos relativamente sencillos que se han estado utilizando hasta ahora, los modelos Inverter requieren hasta un tercio menos de energía.
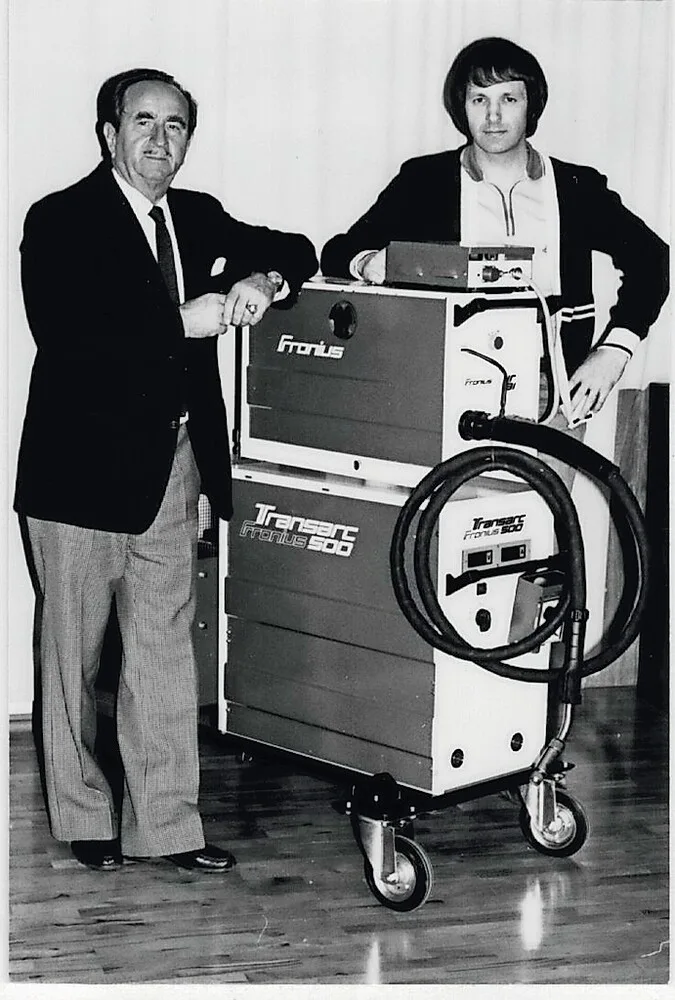
La eficiencia energética superior de los equipos Inverter puede comprobarse en la práctica por el hecho de que apenas se calientan en comparación con los sistemas analógicos. Por tanto, la electricidad que consumen se utiliza principalmente para soldar, mientras que con los dispositivos analógicos se desperdicia un gran porcentaje de la energía en forma de calor. Una diferencia clave es que los equipos de soldadura Inverter suelen ser más compactos, ligeros y, por consiguiente, más portátiles que los analógicos debido a que el diseño general del transformador de soldadura es significativamente más pequeño.
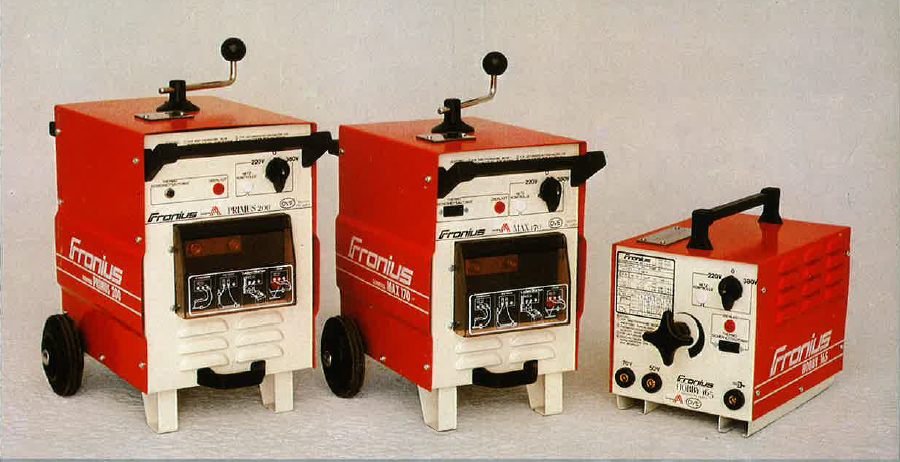
Así pues, cualquiera que aún tenga un equipo de este tipo y simplemente haya cambiado a la tecnología Inverter ya ha dado un gran paso hacia la eficiencia energética.
No todos los equipos Inverter son iguales
Sin embargo, también existen diferencias significativas entre los distintos equipos Inverter en cuanto al consumo energético, sobre todo teniendo en cuenta que los principales fabricantes trabajan constantemente en optimizar la eficiencia energética de sus productos.
Por ejemplo, la corrección del factor de potencia en los equipos de soldadura Inverter modernos ayuda a aumentar el rendimiento. En los modelos con factor de potencia superior a Cos φ 0,95, casi toda la energía obtenida de la red de corriente para la soldadura se utiliza específicamente para este fin.
En términos generales, podría decirse que los equipos Inverter de última generación consumen menos energía que aquellos de generaciones anteriores. Una serie de pruebas realizadas por Fronius a principios de 2024 lo confirma: En un caso práctico de funcionamiento industrial, se comparó directamente un modelo Inverter moderno con otro con una tecnología algo más antigua. El resultado estaba claro: El equipo Inverter antiguo consume 255 kWh más de electricidad al año.
En términos de costes de energía de un equipo individual, esto puede ser bastante insignificante. Sin embargo, cuando se tienen en cuenta los innumerables equipos de soldadura que se utilizan en todo el mundo, el hecho de que una unidad requiera unos 255 kWh adicionales anualmente supone una gran diferencia en términos de consumo energético global, capacidad de las centrales eléctricas y recursos necesarios para la generación de electricidad.
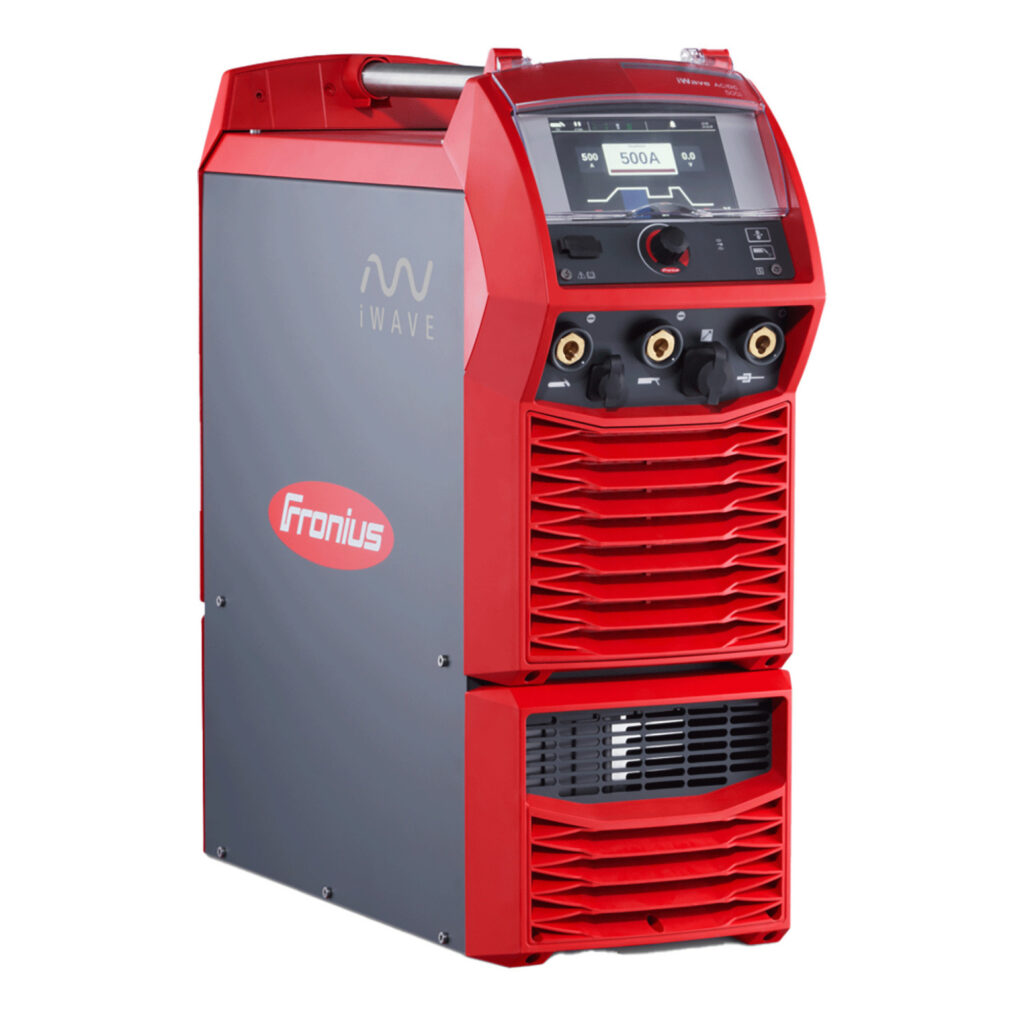
La digitalización aumenta la eficiencia energética
Aunque el desarrollo del hardware sigue desempeñando un papel importante en la tecnología de soldadura, actualmente se están produciendo innovaciones significativas en relación con el software. Estas sientan la base de nuevos métodos y procesos que mejoran la eficiencia de la soldadura y repercuten en el consumo de energía.
Un ejemplo de ello es el proceso CMT desarrollado por Fronius. CMT (Cold Metal Transfer) se caracteriza por un suministro de corriente controlado con precisión, un arco voltaico extremadamente estable y una aportación de calor muy baja. De este modo, se minimiza la deformación de la pieza de trabajo base y se reduce la cantidad de productos defectuosos. Todos estos factores ayudan a ahorrar energía.
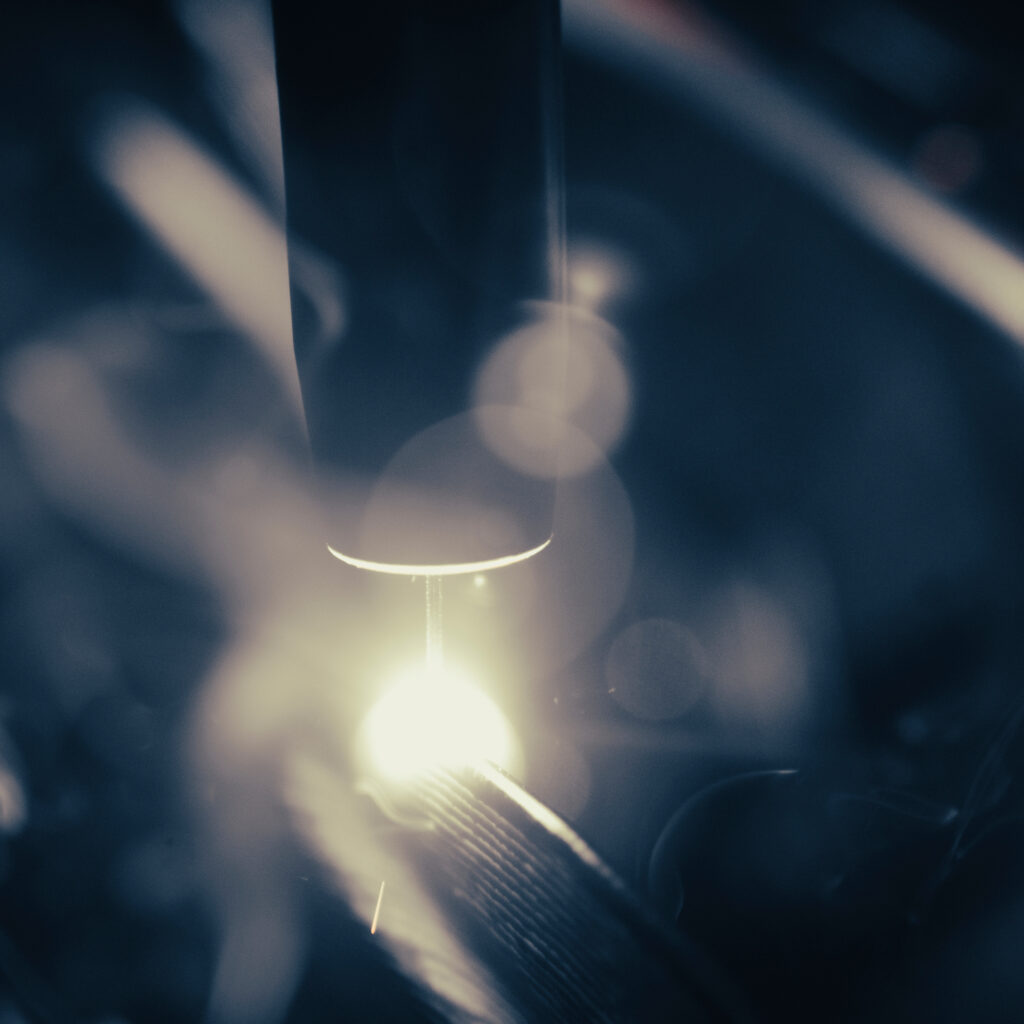
Procesos de soldadura modernos = Soldadura más rápida = Menor consumo de energía
Los procesos que garantizan mayores velocidades de soldadura con la misma o mejor estabilidad del arco voltaico también tienen un efecto positivo en el consumo de energía. Un buen ejemplo de ello es el proceso de soldadura Pulse Multi Control (PMC):
En comparación con el arco voltaico pulsado convencional, el arco voltaico pulsado optimizado permite un arco muy estable con una calidad de cordón constante o incluso superior, una velocidad de soldadura entre un 15 % y un 20 % mayor y, en consecuencia, una menor aportación de energía al material base. El fundamento técnico de los procesos de soldadura como PMC reside principalmente en los estabilizadores digitales de penetración y de arco voltaico.
Refrigeración adaptada a la potencia
La antorcha de la mayoría de los equipos de soldadura MIG/MAG de alto rendimiento se enfría mediante líquido refrigerante que, por desgracia, no siempre es lo suficientemente eficiente desde el punto de vista energético. En muchos equipos antiguos, el líquido refrigerante circula siempre a la misma velocidad, independientemente de cuánta energía se introduzca en el arco voltaico y, por tanto, de cuánto calor se genere en la parte delantera de la antorcha.
La refrigeración adaptada a la potencia implica el acoplamiento permanente al consumo de corriente respectivo y, por tanto, al desarrollo de calor en la antorcha de soldadura. Para la refrigeración, solo se utiliza la cantidad de energía necesaria para obtener unos resultados de soldadura óptimos. De este modo, se evita la refrigeración innecesaria de alto consumo.
¿Y qué pueden hacer los soldadores?
Todos los puntos anteriores hacen referencia a las características técnicas que debe tener un equipo de soldadura que ahorre energía. Si los soldadores optan por un equipo Inverter moderno y eficiente desde el punto de vista energético, ya habrán contribuido significativamente al ahorro de energía.
Asimismo, es aconsejable el ajuste de procesos de soldadura modernos que facilitan la soldadura, mejoren la calidad y aumenten la eficiencia energética. Cuanto más limpia sea la soldadura, menos retrabajos serán necesarios y menos energía se consumirá en general.
Conclusión:
La alta calidad del cordón y el ahorro de energía durante la soldadura no son excluyentes, sino que van de la mano. Los soldadores que utilizan equipos modernos para producir cordones de alta calidad de forma eficiente, prácticamente sin proyecciones y en poco tiempo no solo están haciendo un trabajo excelente; también actúan de forma sostenible en términos ecológicos y económicos, simplemente utilizando la energía y nuestros recursos naturales de la forma más eficiente y rentable posible.
¿Quiere saber más sobre la soldadura con conservación de recursos? Los artículos “Soldadura y sostenibilidad: ¿Cómo se relacionan?” y “Sostenibilidad en Fronius: ¿Qué estamos haciendo?” ofrecen más información. Y si deseas saber cómo prolongar el ciclo de vida de tu equipo de soldadura, te recomendamos el artículo “8 consejos para evitar el desgaste de tu equipo de soldadura“. ¡Esperamos que disfrutes leyéndolo!
No hay comentarios