Vivimos tiempos de inestabilidad y volatilidad. La transición energética, las tensiones geopolíticas y la incertidumbre en las cadenas de suministro nos ponen a prueba casi a diario, y son temas que suelen ser polémicos y controvertidos. Pero hay algo que es seguro: la producción nos plantea más retos que nunca, pues en el futuro tendrá que ser más eficiente en el uso de los recursos, más rápida, más flexible, más rentable, más respetuosa con el medio ambiente y llevarse a cabo en lotes más pequeños. Aquí es donde entra en juego la impresión 3D en metal.
¿Qué es la impresión 3D en metal?
La impresión 3D en metal, como todos los demás procesos de impresión 3D, es un proceso de fabricación que ha revolucionado la producción de muchos productos, tanto desde el punto de vista técnico como económico. Capa a capa, lo que ayer parecía ciencia ficción hoy es una realidad. En este proceso, los objetos tridimensionales se crean añadiendo capas de material base de forma aditiva. La impresión 3D está ganando terreno en cada vez más sectores, aumenta la flexibilidad y, por consiguiente, la competitividad de muchas empresas de los sectores de automoción, electrónica y bienes de consumo, así como las industrias del petróleo y el gas, aeroespacial, de construcción de centrales eléctricas, fabricación de herramientas, tecnología médica y construcción.
Ventajas de la impresión 3D en metal
Las técnicas de producción tradicionales suelen requerir la construcción de moldes y herramientas complejas, además de largos plazos de entrega y elevados costes de instalación. La fabricación aditiva ayuda a acortar enormemente los ciclos de desarrollo. A su vez, la impresión de componentes bajo demanda acelera la construcción de prototipos “Rapid Prototyping”, permite la producción “just in time” sin necesidad de mantener los costes o existencias de recambios, y simplifica considerablemente las tareas de reparación.
Cuando se necesitan recambios, se seleccionan las “fórmulas” correctas en el software y se imprimen o copian según sea necesario. Las geometrías de los componentes apenas tienen límites, incluso es posible realizar complicadas construcciones en forma de panal y con cavidades. La impresión 3D en metal ofrece una ventaja particular en la construcción de prototipos: los problemas de diseño pueden detectarse en fases tempranas y rectificarse sin necesidad de construir formas y dispositivos costosos que requieren mucho tiempo. Al mismo tiempo, el proceso acelera la innovación y aumenta el rendimiento de las empresas. Los componentes impresos optimizados en términos de forma y carga (topología optimizada) suelen ser más ligeros que los convencionales y pueden reducir el consumo de combustible de aviones o vehículos, al tiempo que aumentan la carga útil de los vehículos de transporte.
Impresión 3D en metal aplicando soldadura de alta gama
Los procesos de impresión 3D nos permiten elegir entre varios métodos de fabricación, en los que los objetos se construyen y moldean por capas individuales de material. En la impresión 3D en metal, se distingue entre los procesos basados en polvo y los basados en hilo. En el primer grupo, las capas se unen utilizando polvo de metal fundido. La variante de lecho de polvo, el proceso más común, se caracteriza por su gran precisión, pero es relativamente lenta. Los procesos basados en hilo, que conforman la pieza de trabajo fundiendo un hilo, ya sea mediante haz de electrones, láser o arco voltaico, tienen altas tasas de deposición y, por tanto, contribuyen a acortar los tiempos de producción.
La Wire Arc Direct Energy Deposition (deposición directa de energía por arco de hilo), o arco DED para abreviar, se basa en el arco voltaico y utiliza el proceso de soldadura por arco metálico con gas protector (GMAW). Esta variante de impresión 3D en metal nos permite alcanzar tasas de deposición de hasta 4 kg/h, que se incrementarán en el futuro mediante procesos especiales y soluciones multihilo. Los costes de instalaciones y materiales son factores importantes a la hora de elegir un proceso de impresión. Para el arco DED, es fundamental contar con un sistema de soldadura estable. Ya no son necesarias las costosas cámaras de vacío utilizadas en el proceso de haz de electrones. “Realizar el recorrido de soldadura correcto, con los parámetros y procesos de soldadura adecuados, es crucial para obtener un buen resultado de impresión“, explica Philipp Roithinger, Experto en Fabricación Aditiva. “También se necesita un sistema de soldadura automatizado que garantice la precisión del recorrido de la antorcha de soldadura. Hoy en día, los robots de soldadura de alta calidad ofrecen una precisión de recorrido de hasta 0,7 mm y una precisión de repetibilidad de hasta 0,06 mm“.
Producción de componentes con impresión 3D en metal de gran volumen
Con el arco DED, son esenciales la estabilidad y la regulación de la temperatura del proceso de soldadura utilizado. Este debe ser lo menos energético posible, es decir, lo más “frío” posible, para que no fluya demasiada energía hacia el componente. Además, la capa soldada debe ser continua, sin proyecciones y uniforme, ya que si se produjera un defecto de soldadura, este continuaría en las capas superiores.
Con sus variantes inteligentes de control de procesos, el exclusivo proceso MIG/MAG Cold Metal Transfer (CMT) ya satisface los elevados estándares que exigimos a la tecnología de soldadura para la fabricación aditiva. “La soldadura CMT se caracteriza por un arco voltaico extremadamente estable y permite una aportación de calor flexible”, explica Roithinger, y añade: “El proceso permite una transferencia de material casi sin proyecciones. De este modo, se evitan errores y se reducen los retrabajos. Además, con CMT podemos alcanzar excelentes tasas de deposición y controlar el desprendimiento de cada gota de forma individual, de modo que trabajamos con mayor precisión. También hemos optimizado aún más el proceso de fabricación aditiva mediante CMT Additive Pro para garantizar, por un lado, una creación de capas más constante y, por otro, permitir una mejor regulación del calor”.
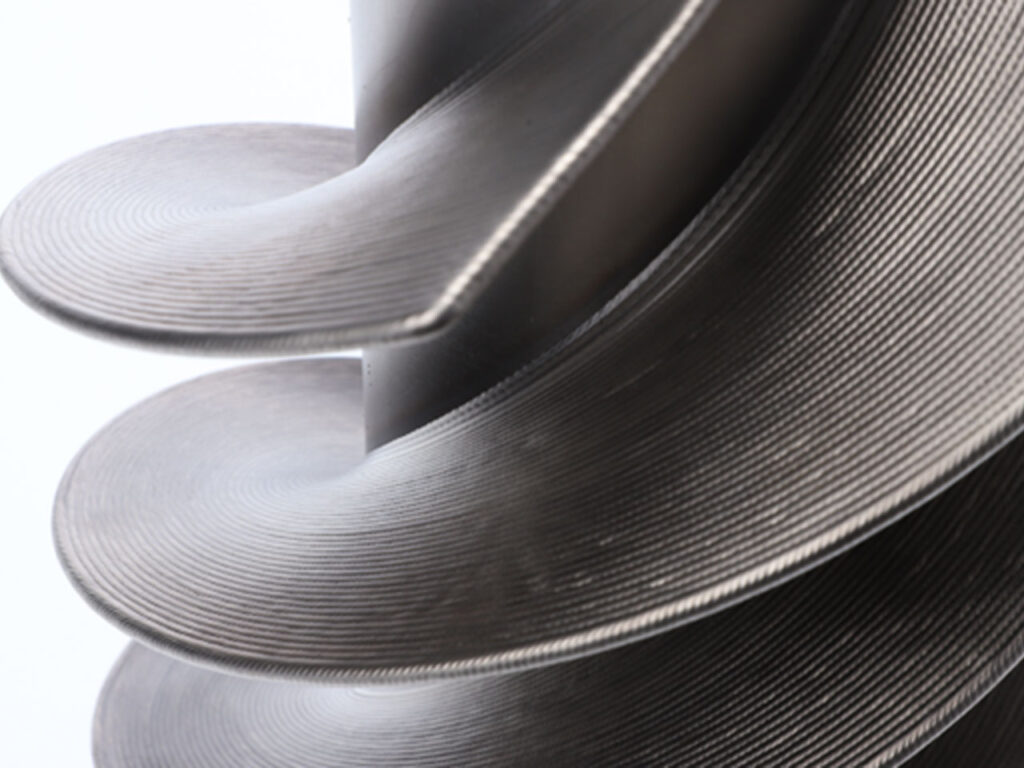
Vigilancia constante del arco voltaico durante la impresión 3D en metal
A pesar de los equipos de alta tecnología, es recomendable que los expertos en soldadura vigilen el arco voltaico y el desprendimiento de gotas. Es posible utilizar sistemas de cámaras especiales para supervisar los trabajos de soldadura y detectar fallos potenciales, así se puede intervenir a tiempo en los casos que sea necesario. ArcView 2, por ejemplo, es una cámara activada por el proceso que permite la supervisión directa en remoto desde el lugar de trabajo, puesto que ofrece imágenes nítidas en cuestión de milisegundos. Cada foto se toma en la fase de cortocircuito, es decir, justo cuando no hay arco voltaico. Un sinfín de imágenes proporcionan a los especialistas en soldadura un vídeo perfecto en tiempo real para el control del proceso, el cual se puede visualizar en un monitor que se encuentra fuera de la celda de soldadura del robot. Así, los soldadores disfrutan de una protección óptima ante la radiación del arco voltaico.
Impresión 3D en metal más económica y sostenible
Los métodos de producción alternativos para la fabricación aditiva son el fresado o el mecanizado. No obstante, estos producen muchos residuos, ya que las piezas necesarias se cortan a partir de bloques de metal, a menudo de un tamaño considerable. Cuando se trabaja con un cuerpo hueco, la cantidad de material desperdiciado es enorme. Con la fabricación aditiva, creamos el componente capa por capa, después, solo faltarían los retrabajos. Sin embargo, estos no tienen por qué realizarse necesariamente. Por tanto, la cantidad de material utilizado es muy inferior en comparación con los métodos de producción convencionales. Mientras que el fresado puede provocar una contracción del material de hasta el 80 % en determinados cuerpos, la fabricación aditiva (por ejemplo, con el arco DED), a menudo solo provoca una contracción del 20 % durante los retrabajos.
“Un claro ejemplo de ello es: La hélice metálica que aquí se muestra se fabricó mediante impresión 3D con metal. Si se hubiera fresado a partir de un solo bloque, este habría medido 60 x 90 x 90 cm y pesado unas cuatro toneladas, mientras que el componente acabado pesa algo menos de 100 kg”, explica Roithinger.
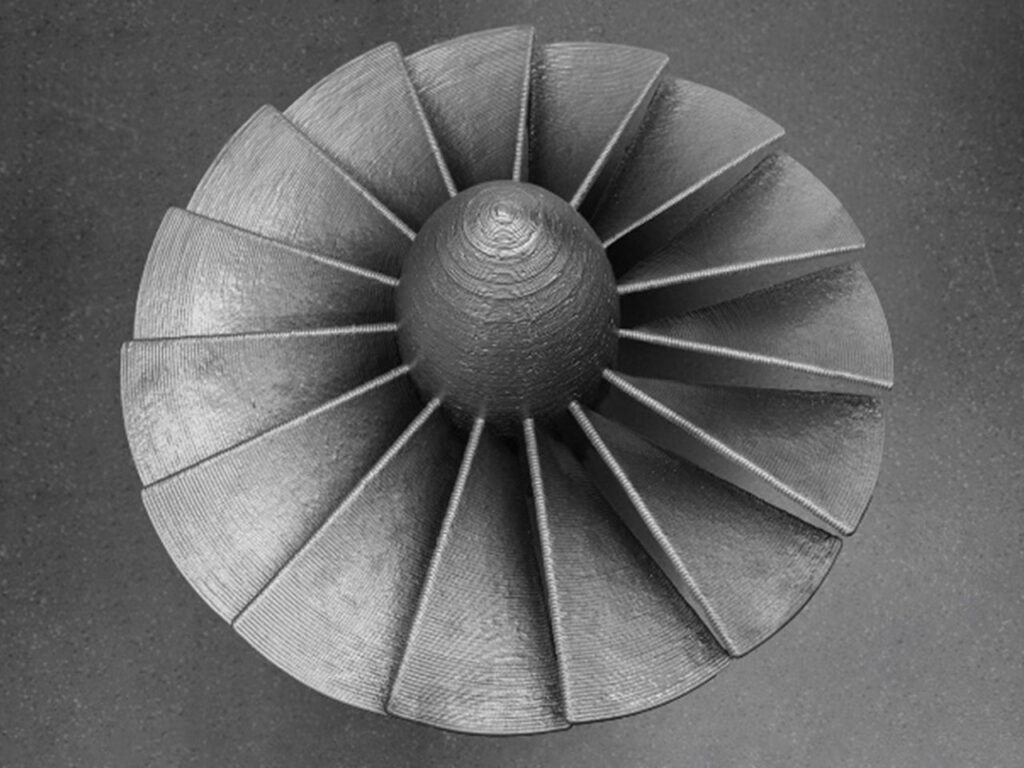
El futuro de la impresión 3D en metal con Fronius
“El proceso de soldadura aditiva tiene un potencial enorme, pero, como siempre, cuando aparecen nuevas tecnologías en el mercado, pasa algún tiempo antes de que estas se acepten, se encuentren las aplicaciones adecuadas y empiecen a tener auge. El arco DED aún es joven en comparación con otros métodos de impresión 3D“, explica Roithinger. “Sin embargo, ya existe una gran demanda de reconstrucción y reparación de piezas dañadas. Con la impresión 3D en metal, podemos prolongar durante años la vida útil de componentes como las hélices o los tornillos sin fin. Pero no solo eso: se puede imprimir cualquier recambio bajo demanda. Esto hace que muchas empresas comerciales e industriales dejen de depender de terceros. Esto las hace más competitivas y les da un mayor valor añadido, ahorrando costes de almacenamiento innecesarios“.
Con el fin de aumentar la variedad de posibles aplicaciones de impresión 3D con metal y conseguir una estabilidad del proceso aún mayor, los ingenieros de Fronius están llevando el proceso aditivo a un nuevo nivel. “Nuestra visión es que tarde o temprano pasaremos a la impresión inmediatamente después de la fase de diseño, y que la impresora 3D producirá el resultado perfecto. Una vez establecida esta tecnología, sería posible distribuir “fórmulas digitales” en lugar de componentes. Estas contendrían las instrucciones de impresión necesarias junto con el recorrido de soldadura, los parámetros de soldadura, los tiempos de espera y otra información. Lo único que tendría que hacer el cliente es cargar la fórmula digital en el ordenador de la instalación automatizada, el sistema de control, y pulsar el botón de impresión“, dice Roithinger, ofreciendo una perspectiva final de las ideas del equipo de innovación de Fronius.
No hay comentarios