Všichni žijeme v eruptivní a nestálé době. Energetická transformace, geopolitické napětí a nejisté dodavatelské řetězce nás téměř denně vystavují zkouškám. Diskuse jsou často kontroverzní a bouřlivé. Ale jedna věc je jistá: Výroba je pro nás větší výzvou než kdy jindy, protože v budoucnu budeme muset efektivněji využívat zdroje, být rychlejší, flexibilnější, hospodárnější, šetrnější k životnímu prostředí a vyrábět v menších sériích. A právě zde přichází na řadu 3D tisk z kovů.
3D tisk kovů: Co to vlastně je a kde všude se využívá?
3D tisk kovů – stejně jako všechny ostatní 3D tiskové procesy – je výrobní proces, který způsobil revoluci ve výrobě mnoha produktů, a to jak z technického, tak i z ekonomického hlediska. To, co se včera zdálo nemožné, se dnes vrstvu po vrstvě stává skutečností. Trojrozměrné objekty jsou vytvářeny aditivními technologiemi navařování základního materiálu po vrstvách. 3D tisk se nyní úspěšně prosazuje ve stále více odvětvích. Zvyšuje flexibilitu a tím i konkurenceschopnost mnoha společností v automobilovém, elektronickém a spotřebním průmyslu, v ropném a plynárenském odvětví, v letectví a kosmonautice, při výstavbě elektráren, výrobě nástrojů, ve zdravotnické technice i ve stavebnictví.
Kovový 3D tisk nabízí mnoho možností a řadu výhod
Klasické výrobní techniky často vyžadují náročnou konstrukci forem a nástrojů spojenou s dlouhými dodacími lhůtami a vysokými pořizovacími náklady. Aditivní výroba pomáhá výrazně zkrátit vývojové cykly. 3d tisk kovových dílů na vyžádání urychluje prototypování (rapid prototyping), umožňuje výrobu just-in-time bez nutnosti nákladného skladování náhradních dílů a výrazně zjednodušuje opravy.
Pokud jsou potřeba náhradní díly, vyberou se v softwaru správné „recepty“ a podle potřeby se vytisknou nebo zkopírují. Geometrie dílů není téměř nijak omezená. Možné jsou i složité voštinové a dutinové konstrukce. 3D tisk kovů poskytuje speciální výhodu při konstrukci prototypů: Designové problémy lze včas identifikovat a odstranit bez složité a nákladné výroby forem a zařízení. Tento proces zároveň urychluje realizaci inovací a zvyšuje výkonnost společností. Tištěné komponenty s optimalizovaným tvarem a zatížením (topologicky optimalizované) jsou často lehčí než běžné komponenty a snižují například spotřebu paliva u automobilů nebo letadel. Díky tištěným dílům s optimalizovanou hmotností lze také zvýšit užitečné zatížení dopravních vozidel.
3D tisk z kovů pomocí špičkové svařovací technologie
Při 3D tisku si můžeme vybrat z různých generativních procesů. Objekty se přitom sestavují a tvarují vrstvu po vrstvě spojováním jednotlivých vrstev materiálu. U 3D tisku kovů rozlišujeme mezi práškovými a drátěnými procesy. Při práškovém procesu se taví kovový prášek. Nejběžnější varianta, metoda práškového lože, zaujme vysokou přesností, ale je poměrně pomalá. Při drátových procesech se svařenec zhotovuje odtavováním drátu – elektronovým, laserovým nebo obloukovým paprskem. Tyto procesy se vyznačují vysokým odtavným výkonem a přispívají tak ke krátkým dobám výroby.
Jak funguje řízená depozice energie drátu
Řízená depozice energie drátu (WDED, zkráceně i DED-Arc), známá také jako WAAM (Wire Arc Additive Manufacturing), je technologie založena na oblouku a využívá proces svařování v ochranném plynu (MSG). Tato varianta 3D tisku z kovů nám umožňuje dosahovat rychlosti tavení až 4 kg/h, která se budou v budoucnu dále zvyšovat díky speciálním procesům a vícedrátovým řešením. Náklady na zařízení a materiál jsou důležitými faktory při výběru tiskového procesu. Srdcem technologie DED-Arc je stabilní svařovací systém. Drahé vakuové komory, které se používají v procesu elektronového svazku, již nejsou zapotřebí. „Pro dobrý výsledek tisku je rozhodující především správná svařovací dráha s vhodnými parametry a procesy svařování,“ vysvětluje Philipp Roithinger, odborník na aditivní výrobu. „Kromě toho potřebujete automatizovaný svařovací systém, který zajistí přesnost dráhy svařovacího hořáku. Vysoce kvalitní svařovací roboty dnes nabízejí přesnost dráhy až 0,7 mm a opakovatelnost až 0,06 mm.“
Výroba dílů ve velkoobjemovém 3D tisku kovů
U technologie DED-Arc je zásadní stabilita a řízení teploty použitého svařovacího procesu. Ten musí mít minimální energii, tedy být co „nejstudenější“, aby se do dílu nedostalo příliš mnoho energie. Svarová vrstva musí být navíc konzistentní, bezrozstřiková a rovnoměrná. Pokud by při svařování došlo k chybě, projevila by se i ve vyšších vrstvách.
Díky svým variantám inteligentního řízení procesu již jedinečný proces MSG Cold Metal Transfer (CMT) splňuje vysoké nároky, které klademe na svařovací techniku pro aditivní výrobu. „CMT se vyznačuje mimořádně stabilním obloukem a umožňuje flexibilní vnos tepla,“ vysvětluje pan Roithinger a dodává: „Tento proces umožňuje téměř bezrozstřikový přechod mezi materiály. To pomáhá předcházet chybám a minimalizovat dokončovací práce. Kromě toho s CMT můžeme dosáhnout vynikajícího odtavného výkonu a kontrolovat uvolnění každé jednotlivé kapky. To nám umožňuje pracovat ještě přesněji. Také jsme dále optimalizovali proces s CMT Additive Pro pro aditivní výrobu, abychom jednak zajistili konstantnější strukturu vrstev a jednak umožnili lepší řízení tepla.“
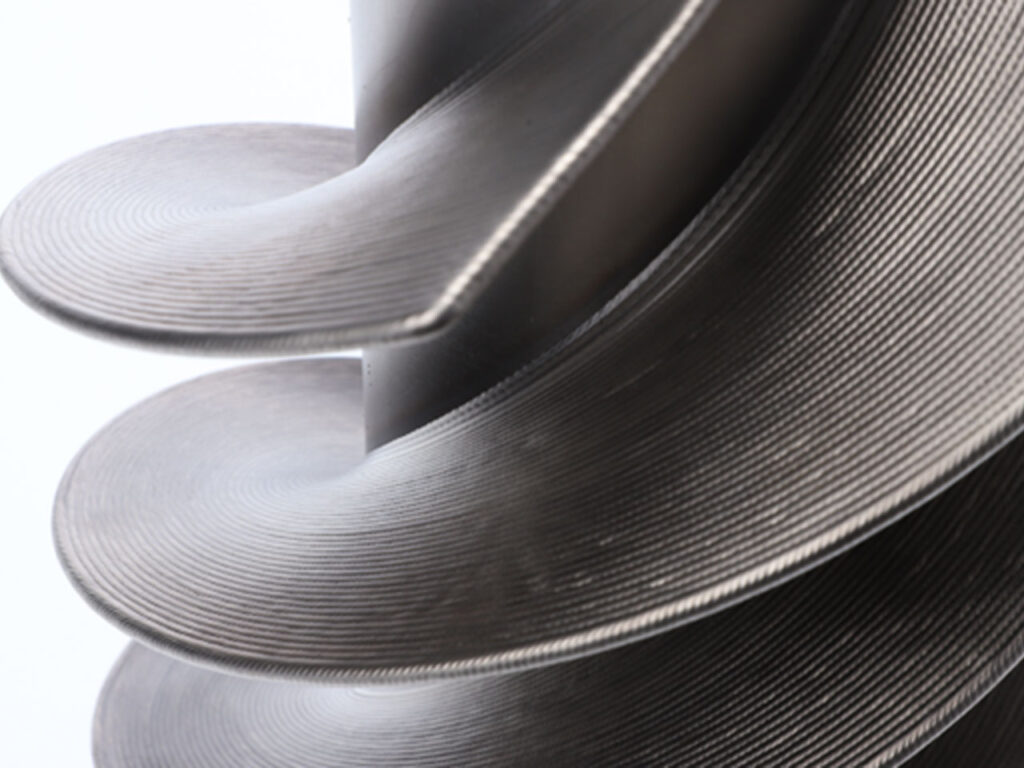
Neustálé sledování oblouku při kovovém 3D tisku
Navzdory špičkovému vybavení je pro svářeče výhodou, že mohou neustále sledovat oblouk i uvolnění kapky. K monitorování svařovacích prací a detekci potenciálních chyb lze použít speciální kamerové systémy. V případě potřeby je pak možné včas zasáhnout. Například ArcView 2 je kamera spouštěná procesem, která umožňuje monitorování procesu přímo z pracoviště. Tato kamera poskytuje snímky ostré jako břitva, a to v rozmezí milisekund! Jednotlivé fotografie jsou pořizovány ve fázi zkratu, tedy přesně ve chvíli, kdy není žádný oblouk. Bezpočet z nich poskytuje profesionálním svářečům dokonalé video v reálném čase pro řízení procesu. Video lze sledovat na obrazovce mimo robotickou svařovací buňku. Svářeči jsou tak optimálně chráněni před obloukovým zářením.
Ekonomicky a ekologicky zajímavý proces
Alternativními výrobními metodami pro aditivní výrobu by bylo frézování nebo obrábění. Při nich však vzniká velké množství odpadu, protože požadované díly se vyřezávají z kovových bloků – často obrovských. U dutého tělesa je odpad enormní. V případě aditivních technologií zhotovujeme díly vrstvu po vrstvě, tedy materiál postupně přidáváme na rozdíl od obrábění, kde se materiál odebírá. Poté jsou nutné už jen dokončovací práce. To se však nemusí nutně stát. Spotřeba materiálu je proto ve srovnání s běžnými výrobními metodami mnohem nižší. Jestliže během frézování dochází až k 80 % úbytku materiálu, v aditivní výrobě – například s DED-Arc – je to často pouze 20 %, a to při dokončovacích pracích.
„Podívejme se na názorný příklad: Zobrazená kovová vrtule byla vyrobena 3D tiskem z kovů. Pokud by byla vyfrézována z bloku, měl by rozměry 60 x 90 x 90 cm a hmotnost kolem 4 t, zatímco hotový díl váží necelých 100 kg,“ říká pan Roithinger.
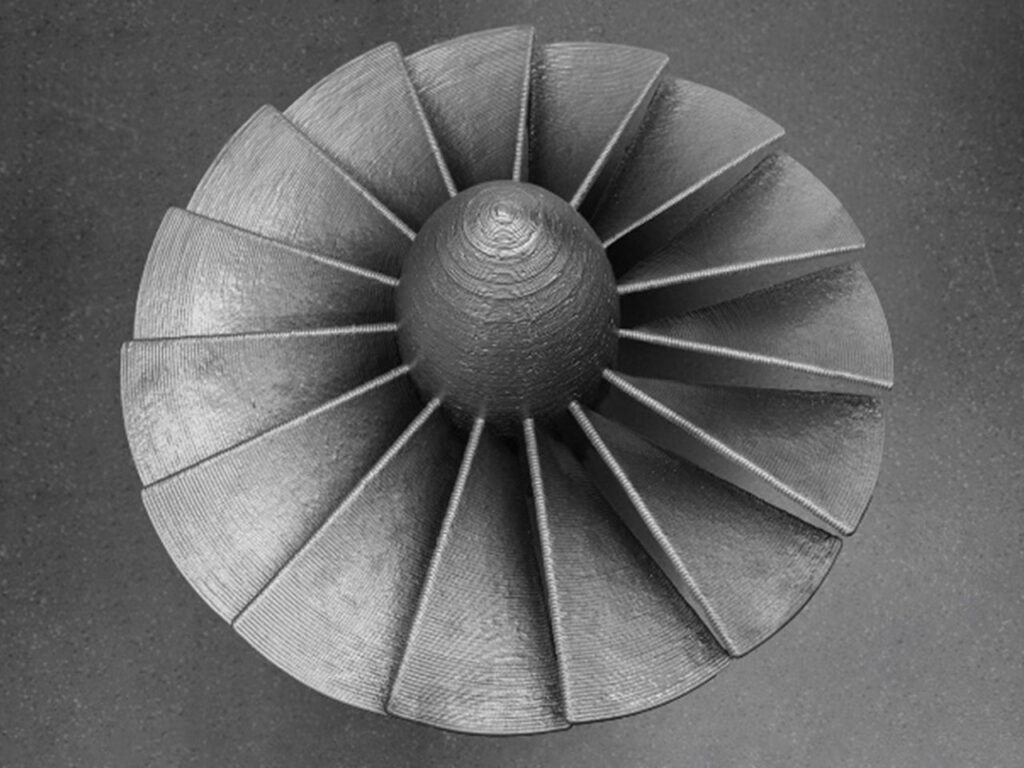
Budoucnost 3D tisku z kovů ve společnosti Fronius – výhled
„Aditivní svařovací proces má obrovský potenciál. Ale jako vždy, když se na trhu objeví nové technologie, nějakou dobu trvá, než se ujmou, najdou vhodné uplatnění a začnou se prosazovat. Technologie DED-Arc je ve srovnání s jinými 3D metodami ještě mladá,“ vysvětluje Philipp Roithinger. „Již nyní je však velká poptávka po rekonstrukci a opravě poškozených dílů. Díky 3D tisku kovových dílů můžeme prodloužit životnost komponentů, jako jsou vrtule nebo šnekové dopravníky, o několik let. Ale nejen to: Na vyžádání lze vytisknout všechny možné náhradní díly. Mnoho obchodních a průmyslových společností se stává nezávislými na místě a době dodání. Díky tomu jsou konkurenceschopnější, a to zásadně. Navíc šetří zbytečné náklady na skladování.“
Inženýři společnosti Fronius snaží posunout aditivní výrobu na novou úroveň, aby rozšířili škálu možného využití kovového 3D tisku a dosáhli ještě větší stability procesu. „Vize spočívá v tom, že dříve nebo později půjdeme do tisku ihned po konstrukční fázi a 3D tiskárna vydá dokonalý výsledek. Jakmile se tato technologie prosadí, lze předpokládat, že se místo dílů budou jednoduše posílat digitální recepty. Ty by pak obsahovaly požadované pokyny pro tisk včetně svařovací dráhy, parametrů svařování, čekacích dob a dalších informací. Zákazníci by museli už jen nahrát digitální recept do palubního počítače automatizovaného systému – nadřízeného systému – a stisknout tlačítko pro tisk,“ poskytuje pan Roithinger poslední vhled do myšlenkového světa inovačního týmu společnosti Fronius.
Žádné komentáře