Nous vivons de nos jours des périodes mouvementées et changeantes. La transition énergétique, les tensions géopolitiques et les chaînes logistiques incertaines nous mettent quotidiennement à l’épreuve. Les débats sont souvent tendus et controversés. Une chose est sûre : les exigences en matière de production ne cessent de croître, car cette dernière devra à l’avenir être économe en ressources, rapide, flexible, rentable et respectueuse de l’environnement, sans compter qu’il faudra qu’elle s’effectue en lots de petite taille. C’est là qu’intervient l’impression 3D métallique.
Qu’est-ce que l’impression 3D métal ?
Comme tous les autres procédés d’impression 3D, l’impression 3D métallique est une méthode de fabrication qui a révolutionné l’élaboration de nombreux produits, tant du point de vue technique qu’économique. Impensable hier, la conception couche par couche devient aujourd’hui une réalité. Elle permet de réaliser des objets en trois dimensions par ajout successif de couches d’un matériau de base. De nos jours, l’impression 3D conquiert de plus en plus de domaines. Elle améliore la flexibilité et la compétitivité de nombreuses entreprises issues du secteur de l’automobile, de l’industrie de l’électronique et des biens de consommation, de l’industrie pétrolière et gazière, du secteur de l’aéronautique et de l’aérospatial, du secteur de la construction de centrales thermiques, de la technique médicale ou encore de la construction.
De nombreux avantages de l’impression 3D métal
Les techniques de production classiques nécessitent souvent des formes et des outils complexes, ainsi que de longs délais de mise en œuvre et des coûts d’installation élevés. Fabriquer par couches successives permet de raccourcir toujours plus les cycles de développement. L’impression de pièces à la demande accélère la construction de prototypes (prototypage rapide) et permet de pratiquer le juste-à-temps tout en renonçant au stockage ainsi qu’aux pièces et coûts de rechange. Elle facilite par ailleurs considérablement les travaux de réparation.
Si des pièces de rechange sont nécessaires, il suffit de sélectionner la « tâche » voulue dans le logiciel et de les imprimer/copier à volonté. En matière de pièces à géométries, il n’y a presque aucune limite. Même les constructions avec des géométries variables. L’impression 3D métallique offre un avantage conséquent en matière de construction de prototypes : les problèmes de design sont repérés précocement et résolus sans qu’il soit nécessaire de construire des formes et des outils complexes et onéreux. Ce procédé accélère l’élaboration d’innovations, tout en augmentant les performances des entreprises. En général, les composants conçus par impression et optimisés au niveau de la forme et de la charge (topologie optimisée) sont plus légers que les composants habituels, et réduisent par exemple la consommation de carburant des voitures ou des avions. La charge utile des véhicules de transport peut elle aussi être augmentée en utilisant des composants au poids optimisé, conçus par impression.
L’impression 3D métal en soudage
Pour l’impression 3D, il est possible de choisir parmi différents procédés génératifs. Les objets sont créés en associant successivement des couches de matériaux pour leur donner une forme. Dans le domaine de l’impression 3D métallique, on différencie les procédés à base de poudre et ceux à base de fil. Avec le procédé à base de poudre, la poudre métallique est fondue. La variante la plus courante, la fusion sur lit de poudre, se distingue par sa grande précision mais la production est comparativement plus lente. Les procédés à base de fil font fondre le fil et construisent ainsi la pièce à souder, soit avec un faisceau d’électrons, soit avec un laser ou un arc électrique. Ils permettent des taux de dépôt élevés et donc des temps de fabrication courts.
Le procédé DED-Arc (Wire Arc Direct Energy Deposition), également connu sous le nom de fabrication additive, fonctionne via un arc électrique et utilise le process de soudage à l’arc sous protection gazeuse avec fil électrode fusible (GMAW). Cette technologie d’impression 3D métallique nous permet d’atteindre des taux de dépôt pouvant atteindre 4 kg/h, qui seront à l’avenir encore augmentés grâce à des procédés et solutions à plusieurs fils spéciaux. Le coût des installations et des matériaux sont des facteurs essentiels pour le choix du procédé d’impression. Au cœur du procédé DED-Arc se trouve une installation de soudage stable. Les chambres à vide onéreuses, utilisées par exemple pour les procédés via faisceau d’électrons, sont ici inutiles. « Pour un bon résultat d’impression, il est surtout décisif de choisir les process et paramètres de soudage appropriés », explique Philipp Roithinger, expert en fabrication additive. « Une installation de soudage automatisée qui garantit l’exactitude du chemin de la torche de soudage est également requise. Le robots de soudage de qualité proposent de nos jours une précision des trajectoires allant jusqu’à 0,7 mm et une précision de répétition allant jusqu’à 0,06 mm. »
La production de composants grâce à l’impression 3D métal grande dimension
Pour le DED-Arc, la stabilité et la gestion de la température du process de soudage utilisé sont essentielles. Afin qu’un minimum d’énergie soit transmis au composant, ce procédé doit consommer le moins d’énergie possible, et donc être aussi « froid » que faire se peut. Par ailleurs, la couche soudée doit être uniforme, exempte de projections et régulière. En effet, si un défaut de soudage apparaît, celui-ci se répercute également sur les couches suivantes.
Grâce à ses variantes intelligentes de règles du process, le process de soudage Cold Metal Transfer (CMT) répond déjà aux exigences élevées que nous imposons à la fabrication additive dans le domaine des techniques de soudage. « Le process CMT se distingue par un arc électrique extrêmement stable et permet un apport d’énergie flexible », explique P. Roithinger. Et d’ajouter : « Grâce à ce process, le transfert de matière s’effectue presque sans aucune projection, ce qui permet d’éviter les défauts et de minimiser les retouches. Par ailleurs, nous atteignons avec le CMT des taux de dépôt exceptionnels, tout en contrôlant chaque détachement de goutte. Nous pouvons ainsi travailler avec encore plus de précision. En outre, nous avons optimisé un peu plus le process vis-à-vis de la fabrication additive, grâce à CMT Additive Pro, pour d’une part garantir une superposition constante, et d’autre part proposer une meilleure gestion thermique. »
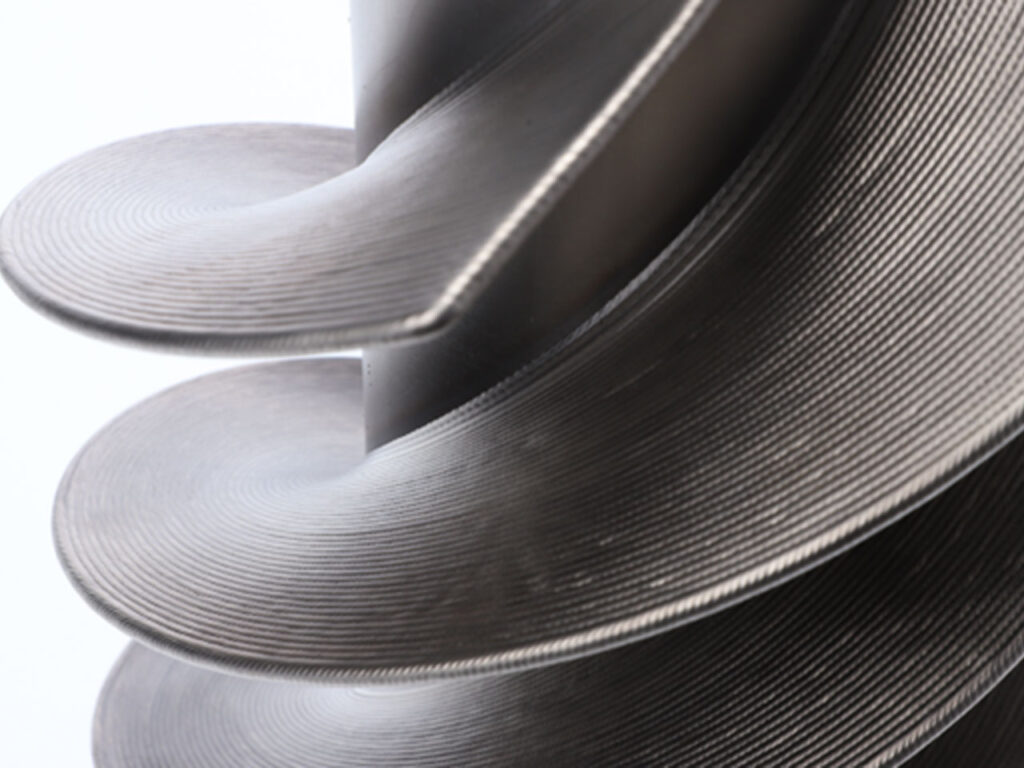
Conserver un arc électrique stable lors de l’impression 3D métallique
Même s’ils disposent d’équipements haut de gamme, il est toujours préférable que les soudeurs professionnels gardent un œil sur l’arc électrique et le détachement de la goutte. Grâce à des systèmes de caméras spéciales, le soudage peut être surveillé afin de détecter les défauts éventuels. Si besoin, il est possible d’intervenir en conséquence. ArcView 2 est par exemple une caméra déclenchée par le process, permettant de surveiller ce dernier directement depuis le poste de travail. Elle fournit des images d’une grande netteté, capturées à la milliseconde près ! Les photos sont réalisées lors de la phase de court-circuit, c’est-à-dire en l’absence d’arc électrique. Leur grand nombre permet aux soudeurs professionnels de disposer d’une vidéo en temps réel parfaite, visant à contrôler le process. Cette dernière peut être consultée depuis une console d’écran, hors de la cellule de soudage robotisé. Les soudeurs sont ainsi idéalement protégés du rayonnement d’arc électrique.
Des avantages économiques et écologiques
Le fraisage ou l’enlèvement de copeaux seraient des méthodes alternatives à la fabrication additive. Cependant, de nombreux déchets sont ainsi produits, puisque les pièces nécessaires sont découpées à partir de blocs de métal, souvent gigantesques. Si le corps doit être creux, les chutes sont alors énormes. La fabrication additive consiste à créer la pièce couche par couche. Seules quelques retouches sont recommandées, sans toutefois être nécessaires. Par rapport aux méthodes de production habituelles, la quantité de matériaux utilisés est ainsi considérablement réduite. Avec le fraisage de certains corps, la perte de matériaux peut atteindre jusqu’à 80 %, contre souvent seulement 20 % pour la fabrication additive (par exemple avec DED-Arc), lors des retouches.
« Voyons avec un exemple parlant : l’hélice en métal représentée a été fabriquée par impression 3D métallique. Si elle avait été fraisée depuis un bloc de métal, ce dernier aurait dû mesurer 60 x 90 x 90 cm, pour un poids d’environ 4 t. Ici, la pièce achevée pèse à peine 100 kg », déclare P. Roithinger.
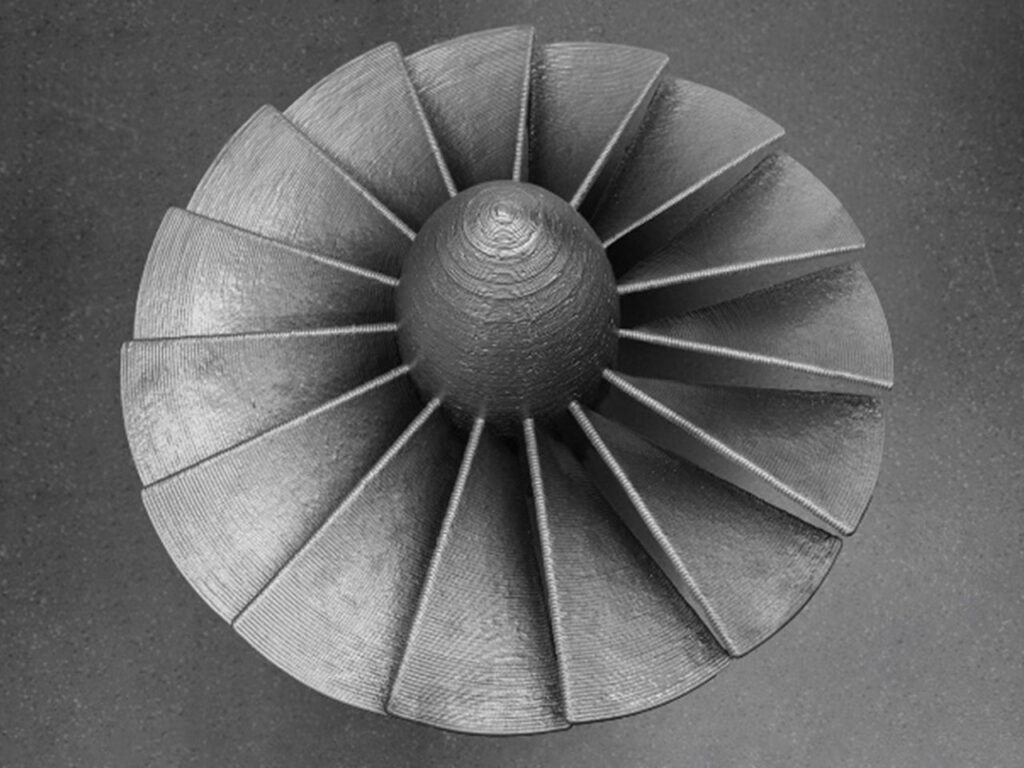
Un aperçu de l’avenir de l’impression 3D métallique chez Fronius
« Le process de soudage additif recèle un réel potentiel. Toutefois, comme à chaque introduction de nouvelles technologies sur le marché, il faut du temps avant qu’elles ne soient acceptées et mises en pratique, jusqu’à devenir réputées. Par rapport aux autres méthodes employant la 3D, DED-Arc est encore relativement jeune », explique P. Roithinger. « La demande est déjà forte pour les restaurations et réparations de pièces endommagées. Avec l’impression 3D métallique, nous pouvons prolonger de plusieurs années la durée de vie des composants, tels que les hélices ou les vis sans fin. Mais ce n’est pas tout : toutes les pièces de rechange sont imprimables sur demande. De nombreuses entreprises commerciales et industrielles ne dépendent ainsi plus des lieux et des délais de livraison. Cette amélioration les rend compétitives, et est donc décisive. Cela permet par ailleurs d’économiser des frais de stockage. »
Afin d’améliorer encore la diversité d’applications rendues possibles par l’impression 3D métallique et d’augmenter davantage la stabilité des procédés, les ingénieurs de Fronius œuvrent à faire passer le process additif au niveau supérieur. « Nous avons pour ambition de passer tôt ou tard directement à l’impression après la phase de construction, et d’obtenir de l’imprimante 3D des résultats parfaits. Une fois cette technologie répandue, il sera possible d’envisager d’envoyer à la clientèle non pas des composants, mais simplement des « tâches » numériques permettant de fabriquer ces derniers. Elles incluraient les instructions nécessaires, avec trajectoires de soudage, paramètres de soudage, temps d’attente et autres informations utiles. Il suffirait alors de télécharger la « tâche » numérique sur l’ordinateur de bord de l’installation automatisée, et d’appuyer sur une touche pour démarrer l’impression », propose P. Roithinger, qui livre un aperçu de ce qui est envisagé par l’équipe chargée des innovations chez Fronius.
Aucun commentaire