Wszyscy żyjemy w burzliwych i nieprzewidywalnych czasach. Transformacja energetyczna, napięcia geopolityczne i zakłócenia łańcuchów dostaw wystawiają nas codziennie na próbę. Dyskusje często kończą się gwałtownymi kłótniami. Jedno jest jednak pewne: wymagania wobec produkcji są większe niż kiedykolwiek, ponieważ w przyszłości musi ona odbywać się bardziej elastycznie, z większym poszanowaniem zasobów i wyższym zyskiem, a zarazem mniejszą szkodliwością dla środowiska i w krótszych seriach. I tutaj pojawia się drukowanie 3D z metalu.
Drukowanie 3D z metalu: Co to właściwie jest?
Drukowanie 3D z metalu — podobnie jak każde inne drukowanie 3D — to technologia produkcji, która zrewolucjonizowała wytwarzanie wielu produktów pod względem zarówno technicznym, jak i ekonomicznym. Krok po kroku realne okazuje się dzisiaj to, co jeszcze wczoraj wydawało się niewykonalne. W tej technologii trójwymiarowe przedmioty są wytwarzane metodą addytywnego nakładania warstw materiału podstawowego. Drukowanie 3D jest już z powodzeniem stosowane w wielu branżach. Zwiększa elastyczność, a w konsekwencji konkurencyjność, wielu przedsiębiorstw z branży motoryzacyjnej, elektronicznej i towarów konsumpcyjnych, w przetwórstwie ropy i gazu, lotnictwie i kosmonautyce, energetyce, produkcji narzędzi, technice medycznej i budownictwie.
Możliwości i zalety drukowania 3D z metalu
Klasyczne technologie produkcji wymagają często pracochłonnej budowy form i narzędzi, co wydłuża etap przygotowań i podnosi koszty wyposażenia. Oto zalety produkcji addytywnej: • skrócenie cykli rozwoju • przyspieszenie tworzenia prototypów • produkcja just in time • zmniejszenie kosztów zakupu i magazynowania części zamiennych • uproszczenie prac naprawczych • wykrywanie wad konstrukcyjnych na wczesnym etapie • zwiększenie innowacyjności i wydajności przedsiębiorstw • produkcja lżejszych podzespołów • zwiększenie ładowności pojazdów transportowych
Produkcja addytywna może radykalnie skrócić cykle rozwoju. Drukowanie elementów w formule on demand przyspiesza tworzenie prototypów (rapid prototyping), umożliwia produkcje just in time, czyli bez kosztów zakupu i magazynowania części zamiennych, oraz znacznie upraszcza prace naprawcze. Jeśli są potrzebne części zamienne, wybiera się ich „modele” w oprogramowaniu i drukuje lub kopiuje dokładnie tyle sztuk, ile jest potrzebnych. Żadna geometria nie jest zbyt skomplikowana. Możliwe są nawet konstrukcje w formie plastra miodu i z pustymi przestrzeniami. Szczególnie dobrze drukowanie 3D z metalu sprawdza się w tworzeniu prototypów: wady konstrukcyjne są wykrywane na wczesnym etapie i można je usunąć bez pracochłonnego i kosztownego budowania form i urządzeń. Jednocześnie technologia ta napędza innowacyjność i zwiększa wydajność przedsiębiorstw. Wydrukowane podzespoły zoptymalizowane pod względem formy i rozkładu obciążeń (topologii) są często lżejsze od konwencjonalnych i zmniejszają przykładowo zużycie paliwa samochodów lub samolotów. Korzystanie z drukowanych, lżejszych elementów umożliwia także zwiększenie ładowności pojazdów transportowych.
Metody drukowania 3D z metalu
Jeśli chodzi o drukowanie 3D mamy wyboru różne metody generatywne. Oznacza to warstwowe budowanie przedmiotów z poszczególnych warstw metalu, które są spajane ze sobą, aby nadać określony kształt. W przypadku drukowania 3D w metalu rozróżniamy procesy oparte na proszku i drucie. Technologia proszkowa polega na stapianiu sproszkowanego metalu. Najpopularniejszy wariant, technologia sproszkowanego łoża (LBPF), wyróżnia się wysoką precyzją, ale jest dość wolna. Materiał może być też podawany w formie drutu, który jest stapiany pod działaniem wiązki elektronów, lasera lub łuku spawalniczego. Zapewnia to wysoką wydajnością stapiania i skraca czas produkcji.
Wire Arc Direct Energy Deposition, w skrócie DED-Arc, to technologia oparta na łuku spawalniczym, która wykorzystuje proces spawania metali w osłonie gazów (MSG). Ten wariant drukowania 3D z metalu umożliwia stapianie w tempie aż do 4 kg/h, które w przyszłości może jeszcze wzrosnąć za sprawą specjalnych procesów i systemów wielodrutowych. Koszty instalacji i materiałów są ważnymi czynnikami w wyborze metody drukowania. Rdzeniem technologii DED-Arc jest stabilny system spawania. Kosztowne komory podciśnieniowe wymagane do topienia wiązką elektronów są w tym przypadku niepotrzebne. „Warunkiem uzyskania dobrego wydruku jest przede wszystkim prawidłowa ścieżka spawania z odpowiednimi parametrami i procesami spawania” — tłumaczy Philipp Roithinger, znawca produkcji addytywnej. Ponadto potrzebny jest zautomatyzowany system spawania, który sprawi, że uchwyt spawalniczy będzie dokładnie trzymał się ścieżki. Wysokiej klasy roboty spawalnicze oferują obecnie dokładność ścieżki do 0,7 mm i powtarzalność do 0,06 mm.”
Produkcja elementów w technologii drukowania 3D z metalu na dużą skalę
W technologii DED-Arc kluczowe znaczenie ma stabilność i regulacja temperatury stosowanego procesu spawania. Proces ten musi być jak „najzimniejszy”, aby ilość energii doprowadzana do elementu nie była zbyt duża. Ponadto spawana warstwa powinna być ciągła, bez odprysków i równomierna. Każda niezgodność spawalnicza przełożyłaby się na kolejne warstwy.
Jedyny w swoim rodzaju proces MSG CMT (Cold Metal Transfer) z wariantami inteligentnej regulacji temperatury już teraz spełnia wysokie wymagania stawiane systemom spawania przez produkcję addytywną. „CMT wyróżnia się niezwykle stabilnym łukiem spawalniczym i umożliwia elastyczne wprowadzanie ciepła do spoiny” — tłumaczy Roithinger i dodaje – „Proces ten umożliwia przejście materiału niemal całkowicie bez odprysków”. Ułatwia to uniknięcie niezgodności i zmniejszenie liczby poprawek. Ponadto dzięki CMT jesteśmy w stanie osiągnąć rewelacyjne wskaźniki wydajności stapiania i sterować odrywaniem każdej kropli. W ten sposób praca jest jeszcze bardziej precyzyjna. W wersji CMT Additive Pro proces ten został jeszcze lepiej przystosowany do wymogów produkcji addytywnej, aby z jednej strony zapewnić konsekwentne nakładanie warstw, a z drugiej umożliwić lepszą regulację ciepła”.
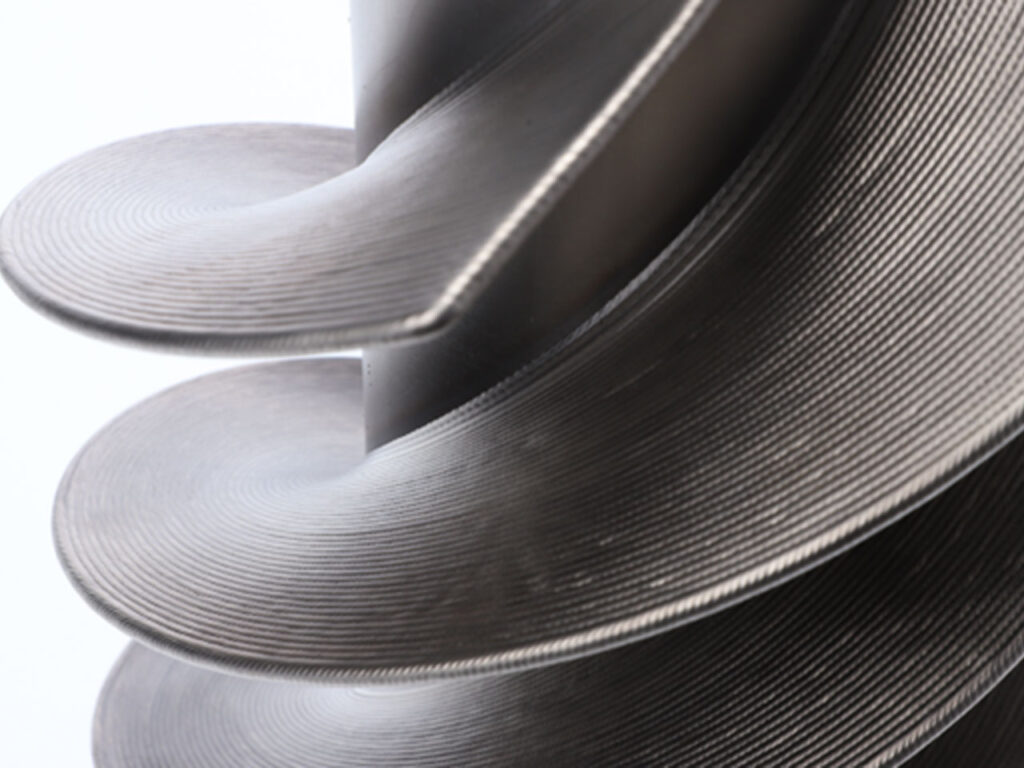
Łuk spawalniczy zawsze pod kontrolą w trakcie drukowania 3D z metalu
Niezależnie od tego, jak zaawansowany jest system, spawacz powinien cały czas utrzymywać kontrolę nad łukiem spawalniczym, włącznie z odrywaniem kropli. Specjalne kamery umożliwiają monitorowanie prac spawalniczych i wykrywanie potencjalnych niezgodności. W razie potrzeby można szybko reagować. Przykładowo ArcView 2 to kamera, która umożliwia monitorowanie procesu bezpośrednio ze stanowiska pracy. Kamera dostarcza obrazy wysokiej rozdzielczości w ułamku sekundy! Poszczególne zdjęcia powstają w fazie zwarcia, czyli dokładnie wtedy, gdy występuje łuk spawalniczy. Powstaje z nich idealne wideo w czasie rzeczywistym, które pozwala spawaczom kontrolować proces. Można go obserwować na konsoli z ekranem poza celą spawania zrobotyzowanego. Chroni to w jak najlepszy sposób spawaczy przed skutkami promieniowania łuku spawalniczego.
Drukowanie 3D z metalu to racjonalne połączenie ekonomii i ekologii
Metodami produkcji alternatywnymi wobec technologii addytywnej byłoby frezowanie lub skrawanie. Metody te wiążą się jednak z wytwarzaniem dużej ilości odpadów, ponieważ wymagane elementy muszą być wycinane z — często olbrzymich — bloków metalu. Jeśli w produkcji jest wydrążona bryła, ilość ścinek jest ogromna. W produkcji addytywnej element jest wytwarzany warstwa po warstwie. Na zakończenie mogą być potrzebne tylko poprawki. Jednak nie są one w wielu przypadkach wymagane. Zużycie materiału jest zatem znacznie mniejsze niż w przypadku konwencjonalnych metod produkcji. Jeśli podczas frezowania określonych brył straty na materiale wynoszą do 80%, to w produkcji addytywnej — przykładowo DED-Arc — jest to tylko 20%, które jest usuwane podczas poprawek.
„Zobaczmy to sobie na konkretnym przykładzie: widoczne na zdjęciu metalowe śmigło zostało wytworzone metodą drukowania 3D w metalu. Gdyby frezować je z bloku, musiałby on mieć wymiary 60 x 90 x 90 cm i masę około 4 t, chociaż gotowy element waży zaledwie 100 kg” — mówi Roithinger.
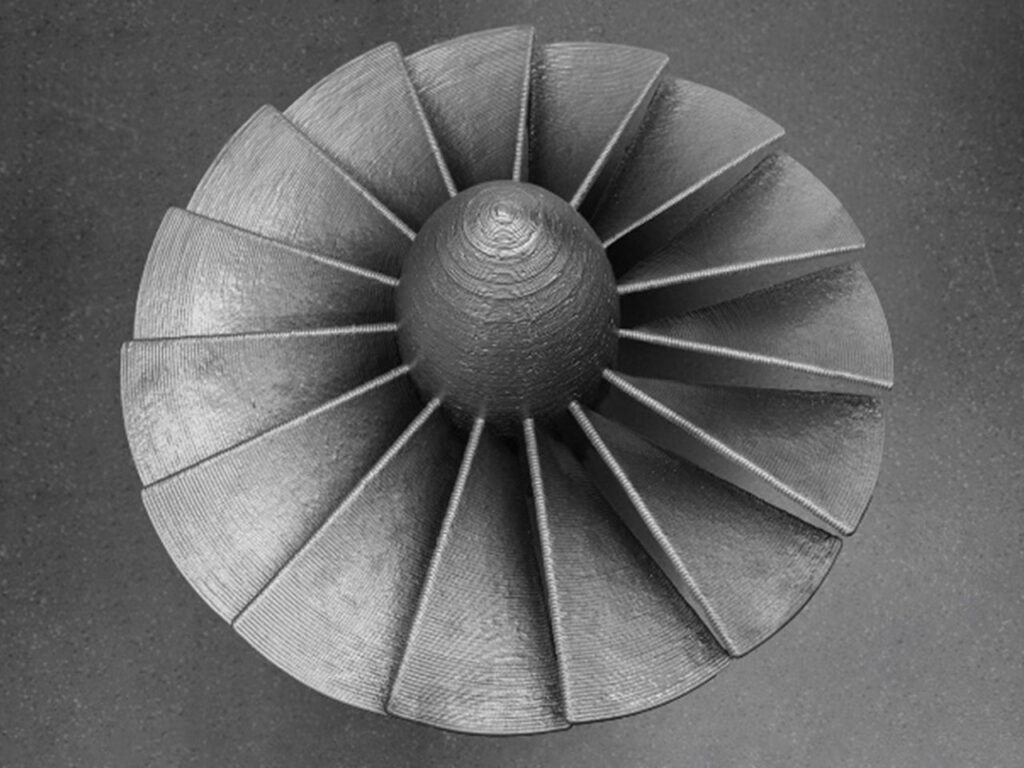
Przyszłość drukowania 3D z metalu w firmie Fronius — perspektywa
„Addytywna metoda spawania ma olbrzymi potencjał. Jednak jak każda nowa technologia, potrzebuje nieco czasu, aby zyskać akceptację i odpowiednie zastosowania oraz zacząć się dynamicznie rozwijać. DED-Arc jest metodą relatywnie młodą w porównaniu z innymi metodami 3D” — podkreśla Roithinger. „W odbudowie i naprawie uszkodzonych elementów już dzisiaj jest jednak duży popyt. Za pomocą drukowania 3D z metalu możemy wydłużyć żywotność podzespołów — np. śmigieł czy przenośników ślimakowych — o całe lata. Ale nie tylko to: Wszystkie możliwe części zamienne można drukować w formule on demand. Pozwoli to wielu przedsiębiorstwom handlowym i zakładom przemysłowym uniezależnić się od miejsca i czasu dostawy. Zwiększy to ich konkurencyjność — i to znacznie. Ponadto będzie można zaoszczędzić na kosztach magazynowania.”
Inżynierowie Fronius są do dyspozycji, aby zwiększyć zakres możliwości zastosowania drukowania 3D w metalu i osiągnąć jeszcze większą stabilność procesu, a w konsekwencji przenieść proces addytywny na nowy poziom. „Wizja polega na tym, że wcześniej czy później natychmiast po fazie konstrukcji będziemy przechodzić do druku i drukarka 3D będzie wypluwać idealny wynik. Gdy ta technika się rozpowszechni, może się zdarzyć, że zamiast elementów będą wysyłane tylko ich cyfrowe modele. Będą one zawierały stosowną instrukcję drukowania ze ścieżką spawania, parametrami spawania, czasami oczekiwania i innymi informacjami. Klienci będą musieli tylko wczytać cyfrowy model do komputera pokładowego zautomatyzowanej instalacji — systemu sterowniczego — i nacisnąć przycisk drukowania” — tak Philipp Roithinger przedstawia na koniec wizję zespołu innowacji Fronius.
Brak komentarzy