Systemy zapewniające bezpieczeństwo jazdy w pojazdach i spawanie zrobotyzowane w produkcji przemysłowej — czy mają ze sobą coś wspólnego? Patrząc z punktu widzenia rozwoju pojazdów mechanicznych, na początku stosowano tylko analogowe systemy, takie jak wspomaganie kierowania, ułatwiające jazdę na całym świecie. Stopniowo pojawiało się coraz więcej cyfrowych „pomocników”, zapewniających bierne bezpieczeństwo, jak na przykład systemy ABS, ESP, asystenty utrzymywania pasa ruchu i wiele innych. Obecnie jesteśmy tuż przed narodzinami samochodu, który naprawdę „sam jeździ”…
Także rozwój spawania zrobotyzowanego, aż do osiągnięcia pełnej autonomii, jest tu istotnym przyczynkiem w przemysłowej produkcji seryjnej. Od dekad wielkie produkcje dążą w tym kierunku. Kluczem do tego może być zastosowanie cyfrowych systemów asystenckich do spawania zrobotyzowanego, instalowanych w systemach spawania. Umożliwiają one robotom coraz bardziej autonomiczne reagowanie bez zbytniej ingerencji człowieka.
Łatwe programowanie robota spawalniczego
Podstawowym warunkiem każdego dobrego, w pełni zautomatyzowanego spawania jest dokładne zaprogramowanie robota spawalniczego. Spawacz musi więc wskazać robotowi, gdzie przebiega spoina w trójwymiarowym układzie współrzędnych, na którym opiera się sterownik robota.
Profesjonalne systemy asystenckie do spawania zrobotyzowanego stosują na przykład przykładanie niskiego napięcia czujnikowego do drutu. Teraz, gdy spawacz steruje ruchem palnika robota w określonym punkcie początkowym i końcowym spawania elementu, zetknięcie z blachą wywołuje zwarcie — jednak z uwagi na niskie napięcie nie następuje spawanie. Źródło spawalnicze przekształca to zwarcie w sygnał cyfrowy, przekazywany ponownie do robota. Gdy następuje emisja sygnału, robot może zapisać dane o położeniu — w ten sposób rejestruje dokładne położenie punktu początkowego i końcowego spoiny.
Dotknięcie elementu spawanego wiąże się jednak z ryzykiem. W przypadku konwencjonalnych palników spawalniczych istnieje duże prawdopodobieństwo wygięcia drutu. Tu na pomoc śpieszą systemy z rewersyjnym podawaniem drutu — a więc ruchem drutu naprzód-wstecz. W chwili zetknięcia z blachą następuje automatyczne cofnięcie drutu, co wyklucza uszkodzenie drutu elektrodowego — a przez to zafałszowanie danych o położeniu.
Drut elektrodowy w roli czujnika
Już zastosowanie napięcia czujnikowego przyłożonego do drutu spawalniczego w połączeniu z rewersyjnym podawaniem drutu umożliwiało „wyczuwanie”: ale teraz możliwości są jeszcze większe! Najwydajniejsze systemy mogą wykonywać ruchy naprzód-wstecz z maksymalną częstotliwością 100 Hz. Jeżeli ten drut spawalniczy wprowadzić w nieskończony wysokodynamiczny ruch po ustawionych obok siebie torach nad elementem spawanym, można by było rejestrować każde uniesienie i opuszczenie palnika spawalniczego przy elemencie spawanym. Zasadniczo pozwalałoby to na odwzorowanie pełnych, trójwymiarowych konturów elementu.
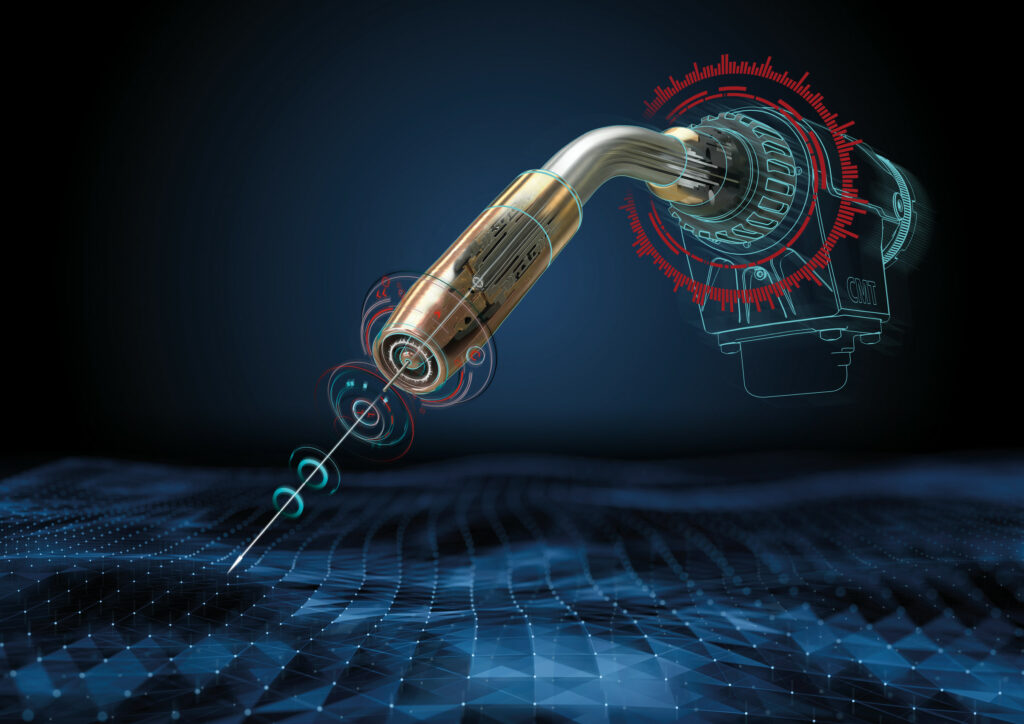
Wykrywanie krawędzi: korekta trasy robota
Ten nowy sposób wykorzystania drutu elektrodowego jako czujnika zastosowano już z wielkim powodzeniem w praktyce. Wykrywanie krawędzi w przypadku połączeń zakładkowych jest przy tym jedną z najważniejszych metod, zastosowanych w międzyczasie w produkcji przemysłowej. Wskutek stosowania zautomatyzowanych systemów, ustawiających dolną i górną blachę w odpowiednim położeniu do spawania, coraz częściej występują odchyłki — mówimy tu także o tolerancjach. Jeżeli położenie krawędzi górnej blachy odbiega zbyt mocno od zaprogramowanych wartości zadanych, skutkiem są błędy łączenia podczas spawania.
Przejazd wyszukujący po ustalonym torze przed rozpoczęciem spawania rejestruje w najdokładniejszy sposób, jak bardzo wartość rzeczywista krawędzi blachy odbiega od wartości zadanych. W ten sposób sterownik robota może samoczynnie i odpowiednio skorygować przebieg spoiny, czego rezultatem jest idealne połączenie blachy górnej z dolną.
Pomiar wysokości: niezawodne spawanie mimo rowka
Ale blachy przesuwają się nie tylko w poziomie. Oczywiście, mogą wystąpić także niezamierzone różnice wysokości między blachą górną i dolną. Również one w razie zbyt dużych wymiarów rowka wywołują błędy łączenia.
Ponieważ wraz z sygnałem cyfrowym przekazywana jest także dokładnie wymierzona wysokość krawędzi blachy, czujnikowy drut spawalniczy może dokładnie obliczyć rowek między obiema blachami. Ponadto wcześniej można dokładnie określić, jak źródło spawalnicze ma reagować na różne rozmiary rowka: w zależności od rozmiaru rowka sięga ono automatycznie do różnych, zapisanych programów spawania — tak zwanych Jobów (zadań). W efekcie każde wyzwanie spawalnicze pokonuje się z zastosowaniem dokładnie takich parametrów spawania, które są idealnie dostosowane do wymiaru rowka.
Śledzenie i korekta spoiny w czasie spawania
Dotychczas wymienione możliwości sensoryki mają za zadanie przeciwdziałać odchyleniom położenia blach przed rozpoczęciem spawania. Ale co począć, gdy w trakcie spawania wystąpią większe odchylenia? Właśnie w branży spawania grubych blach, podczas produkcji pojazdów szynowych lub budowlanych wskutek wysokich wartości ciepła oddawanego może wystąpić wypaczenie geometryczne, na które trzeba zareagować w czasie spawania.
Jeżeli np. trzeba spawać spoiną pachwinową lub dopasowaną spoiną doczołową, robot spawa ruchem oscylacyjnym. Wówczas stale ulega zmianie położenie wolnego wylotu drutu z jednej strony na drugą. Zmieniają się naturalnie także parametry spawania, takie jak napięcie i natężenie prądu. Jeżeli wskutek działania wysokiej temperatury jedna z dwóch blach zmieni swoje położenie, różnice znajdą odzwierciedlenie w wartościach zadanych i rzeczywistych parametrach spawania.
Na podstawie tych informacji robot spawalniczy może automatycznie skorygować przebieg spoiny w czasie spawania. W ten sposób błędy łączenia stają się nadzwyczaj mało prawdopodobne.
Oszczędność na kosztach dzięki zastosowaniu systemów asystenckich do spawania zrobotyzowanego
Spawanie zrobotyzowane ma krok po kroku dążyć w stronę autonomicznej produkcji. Podsumowując: zastosowane w tym celu systemy asystenckie umożliwiają wydajniejsze i bardziej niezawodne przebiegi procesów. Dzięki temu można znacząco zmniejszyć liczbę poprawek elementów, inne nakłady pracy oraz obniżyć koszty materiałów. Przyczynia się to do maksymalnego obniżenia kosztów produkcji.
Firma Fronius stała się w międzyczasie także pionierem i liderem w zakresie technologii na polu spawania zrobotyzowanego. Dzięki licznym innowacjom, jak np. zaprezentowany w 2020 roku system WireSense, firmie Fronius udaje się kierować produkcję w stronę pełnej automatyzacji z zastosowaniem robotów spawalniczych. Źródło spawalnicze nie jest już tylko systemem spawania, ale staje się także inteligentnym mózgiem robota.
Brak komentarzy