Los sistemas de seguridad vial en automóviles y la soldadura robotizada en la producción industrial, ¿hay puntos en común? Si nos fijamos primero en las etapas de desarrollo de los vehículos, en principio fueron los sistemas analógicos, como la dirección asistida, los que facilitaron la conducción a usuarios de todo el mundo. Poco a poco se fueron desarrollando cada vez más sistemas de asistencia digitales para la seguridad pasiva; por ejemplo, el sistema antibloqueo de frenos, el sistema de control de estabilidad, el asistente de mantenimiento de carril, y muchos más. En la actualidad, falta poco para que los vehículos autónomos sean una realidad.
El desarrollo de la soldadura robotizada hacia la autonomía también es importante para la producción industrial en serie. Durante décadas, las grandes producciones se han esforzado por avanzar en esta dirección. Una clave importante podrían ser los sistemas de asistencia digitales para la soldadura robotizada, que se instalan en los sistemas de soldadura y permiten a los robots trabajar de forma cada vez más independiente, sin apenas necesitar intervención externa.
Fácil programación del robot de soldadura
El requisito indispensable para lograr una soldadura automática sólida es programar correctamente el robot de soldadura. Es decir, el soldador debe enseñar al robot dónde se encuentra exactamente la trayectoria del cordón de soldadura en el sistema de coordenadas tridimensional en el que se basa el control del robot.
Para ello, los sistemas de asistencia profesionales para la soldadura robotizada aplican al hilo una tensión de sensor baja. Cuando el soldador dirige la antorcha de robot hacia el componente en los puntos de inicio y final establecidos, se produce un cortocircuito al tocar la chapa (debido a la baja tensión, pero sin soldadura). La fuente de potencia transforma este cortocircuito en una señal digital para transmitirla al robot. Al recibir la señal, el robot puede almacenar sus datos de posición, así quedan registrados los puntos exactos de inicio y final del cordón de soldadura.
Sin embargo, el contacto con la pieza de trabajo conlleva riesgos. En antorchas de soldadura convencionales, inclusive su sistema de transporte de hilo estándar, existe una gran probabilidad de que el hilo se deforme. Los sistemas con transporte de hilo reversible, o sea, con movimiento tanto de avance como de retroceso, ofrecen una solución para ese problema. En el momento en que entra en contacto con la chapa, el hilo retrocede automáticamente, de forma que no es posible dañar el electrodo de soldadura ni obtener resultados de posición alterados.
El electrodo de soldadura como sensor
Si es posible aplicar tensión de sensor al hilo de soldadura y conseguir que el transporte de hilo sea reversible, entonces… ¡debe haber muchas más posibilidades! ¿Verdad? Los sistemas más potentes pueden realizar movimientos de avance y retroceso de hasta 100 Hz. Si bajo este movimiento altamente dinámico, se dejara al hilo de soldadura recorrer el componente siguiendo trayectorias consecutivas sin interrupciones, se podrían registrar todas las elevaciones y descensos del componente para luego poder visualizar los contornos completos en 3D.
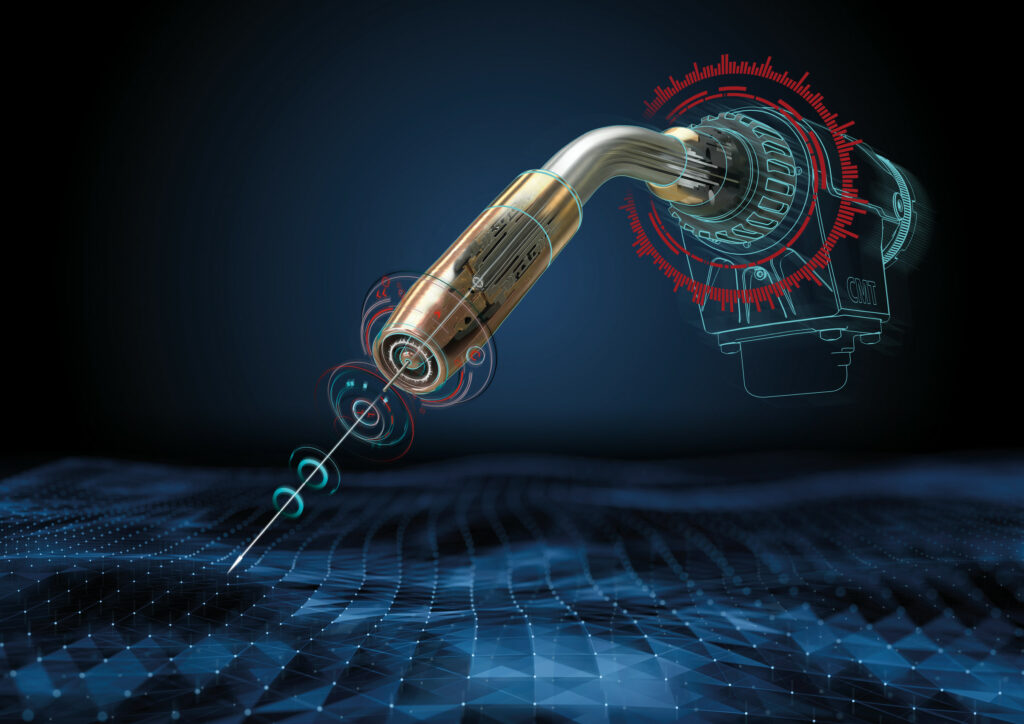
Detección de bordes: corrección de la trayectoria del robot
En la práctica, esta nueva tecnología de sensores del electrodo de soldadura ya se puede utilizar satisfactoriamente. La detección de bordes de la soldadura a solape es una de las funciones más importantes que aplican actualmente en la producción industrial. Debido a los sistemas automatizados que posicionan las chapas superiores e inferiores para la soldadura, se producen con frecuencia desviaciones, también llamadas tolerancias. Si la posición del borde de la chapa superior se desvía demasiado de los valores programados, se producen fallos de unión en la soldadura.
Realizar un recorrido de búsqueda en trayectorias definidas antes de iniciar el proceso de soldadura permite registrar las desviación exacta entre los valores reales y los valores nominales de los bordes de la chapa. De esta forma, el control del robot puede corregir automáticamente la trayectoria del cordón de soldadura y así lograr una unión perfecta entre la chapa superior e inferior.
Medición de la altura: soldadura fiable a pesar de los espacios
Las posiciones de los componentes no solo se desplazan en horizontal, sino que también pueden darse diferencias de altura involuntarias entre la chapa superior e inferior. Generalmente, estas diferencias también pueden causar errores de unión si la ranura es demasiado grande.
Dado que la señal digital táctil también transmite la altura precisa de los bordes de la chapa, WireSense es capaz de calcular exactamente las ranuras entre las chapas. Además, también se puede definir previamente la forma exacta en que la fuente de potencia debe reaccionar a las diferentes dimensiones de ranura: para hacerlo, recurre automáticamente a diversos programas de soldadura almacenados, llamados “Jobs” en función del tamaño de la ranura. Es decir, en cada reto de soldadura se utilizan unos parámetros de soldadura adaptados perfectamente al tamaño de ranura.
Seguimiento y corrección del cordón durante la soldadura
Las diferentes funciones de la tecnología de sensores mencionadas hasta ahora tienen como objetivo contrarrestar las desviaciones de posición de las chapas antes del inicio de la soldadura. ¿Pero qué ocurre con las desviaciones que se dan durante el proceso de soldadura? Cuando se utilizan chapas gruesas, por ejemplo en la producción de vehículos ferroviarios o de construcción, la aportación de calor masiva puede causar una deformación geométrica a la que se debe reaccionar durante la soldadura.
Por ejemplo, si hay que soldar un cordón de garganta o un cordón a tope preparado, el robot realiza la soldadura con un movimiento pendular. La posición del stickout cambia continuamente de un lado a otro y, como consecuencia, también cambian los parámetros de soldadura individuales, como la tensión y la intensidad de corriente. Si una de las dos chapas se desviase de su posición por efecto del calor, esto se vería reflejado en una diferencia entre los valores nominales y los valores reales de los parámetros de soldadura.
Gracias a esta información, el robot de soldadura puede corregir automáticamente el cordón durante el proceso de soldadura, de forma que la probabilidad de que se produzca un error de unión es realmente baja.
Ahorro de costes gracias a los sistemas de asistencia para la soldadura robotizada
La soldadura robotizada se debe implementar poco a poco en la producción autónoma. Los sistemas de asistencia utilizados para este fin realizan procesos más eficientes y fiables, y permiten reducir considerablemente el retrabajo, la carga de trabajo y los costes de material. En definitiva, consiguen optimizar al máximo los costes de producción globales.
En la actualidad, Fronius también es pionero y líder tecnológico en sistemas de asistencia para la soldadura robotizada. Con numerosos desarrollos, como el sistema WireSense lanzado en 2020, Fronius ha conseguido un exitoso progreso en la producción automatizada mediante robots de soldadura. En otras palabras, la fuente de potencia ya no es un simple sistema de soldadura, sino que también actúa como el cerebro inteligente del robot.
No hay comentarios