Svařování je vzrušující a náročná práce. Špičkoví svářečští odborníci jsou něco jako hrdinové, celosvětově vyhledávaní a všude dobře placení. Spoje, které vytvoří, zajišťují bezpečnost automobilů, jízdních kol, letadel, lodí, vlaků a mnoha dalších objektů. Přesto má toto povolání někdy špatnou pověst a stále méně mladých lidí se chce této profesi učit. Proč tomu tak je? Při svařování vznikají svařovací zplodiny, které jsou zdraví nebezpečné. Ale na rozdíl od minulosti se proti nim dnes lze chránit!
Náročné a vzrušující
Existuje mnoho příkladů, proč spojování kovů vyžaduje nejen obrovské znalosti svařovací techniky a metalurgie, ale je také v praxi opravdu náročné. Pomysleme jen na svařování hliníkových rámů horských kol: Když se cyklisté řítí z nejstrmějších kopců Světového poháru ve sjezdu rychlostí přes 70 km/h, může na zadní část rámu působit až 9 000 newtonů. Pokud praskne jediný svarový spoj, často následují dramatické pády! Proto jsou potřeba skuteční odborníci na svařování TIG. Vyznačují se hlubokými odbornými znalostmi a zručností při zavádění svařovacího drátu do tavné lázně. Nebo se podívejme na ocelové podsestavy pro nákladní vagony: V závislosti na konstrukci musí odolávat tahovým silám 22 tun a více. Zde se používá především proces MAG a jeho varianty, jako je PMC (Pulse Multi Control). Často se musí svařovat v nucených polohách – zejména svisle nahoru. Zkušenosti a zručné vedení hořáku jsou nezbytné. Kolik emisí svářeči vyprodukují, záleží na nich.
Optimalizace oblouku
S ohledem na míru emisí jsou důležité nejen varianty procesu a technologie odsávání. Zejména při svařování kovů v ochranném plynu (MIG/MAG) hrají důležitou roli parametry procesu: Rychlost drátu, délka oblouku a korekční parametry mají vliv na rozsah znečištění. Společně s Institutem pro svařovací techniku a technologii spojování (ISF) na univerzitě RWTH v Cáchách jsme podrobně zkoumali různá nastavení parametrů.
Méně emisí s pulzním obloukem
Jak vyplývá ze závěrečné zprávy z našeho prvního zkoumání svařovacích zplodin, pulzní oblouk má nejpříznivější přechod mezi materiály, a tedy nejnižší míru emisí svařovacích zplodin (FER = Fume Emission Rate) ve srovnání s obloukem LSC (Low Spatter Control) a standardním obloukem. V nové sérii testů s výzkumníky z Cách jsme zkoušeli, jak různá nastavení hořáku, rychlosti drátu a korekce délky oblouku ovlivňují míru emisí. Svařovalo se s obloukem PMC a systémovým svařovacím přístrojem TPS 500i.
Zvolené rámcové podmínky
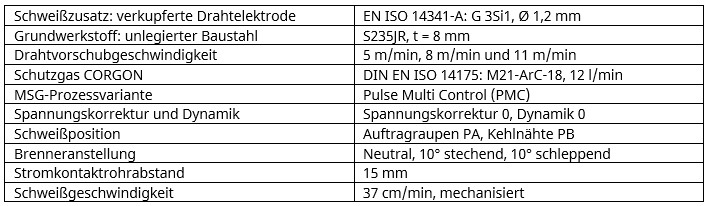
Emise svařovacích zplodin při svařování housenek
Během našich testů jsme zjistili, že emise svařovacích zplodin jsou při rychlosti drátu 5 m/min a neutrální poloze hořáku poměrně nízké. Je však patrné, že při vyšší rychlosti drátu 11 m/min vzniká méně emisí než při nižším výkonu 8 m/min, kdy náš pokus vedl ke zvýšenému počtu zkratů (Obr. 1).
Pokud svářečští odborníci optimalizují oblouk pomocí korekce délky oblouku (v pokusu s neutrální polohou hořáku), mohou výrazně snížit emise svařovacích zplodin při všech rychlostech drátu. Na rozdíl od neoptimalizovaných oblouků jsou zde emise svařovacích zplodin při 8 m/min s 0,9 mg/s o něco nižší než při 11 m/min s 1,1 mg/s (Obr. 1).
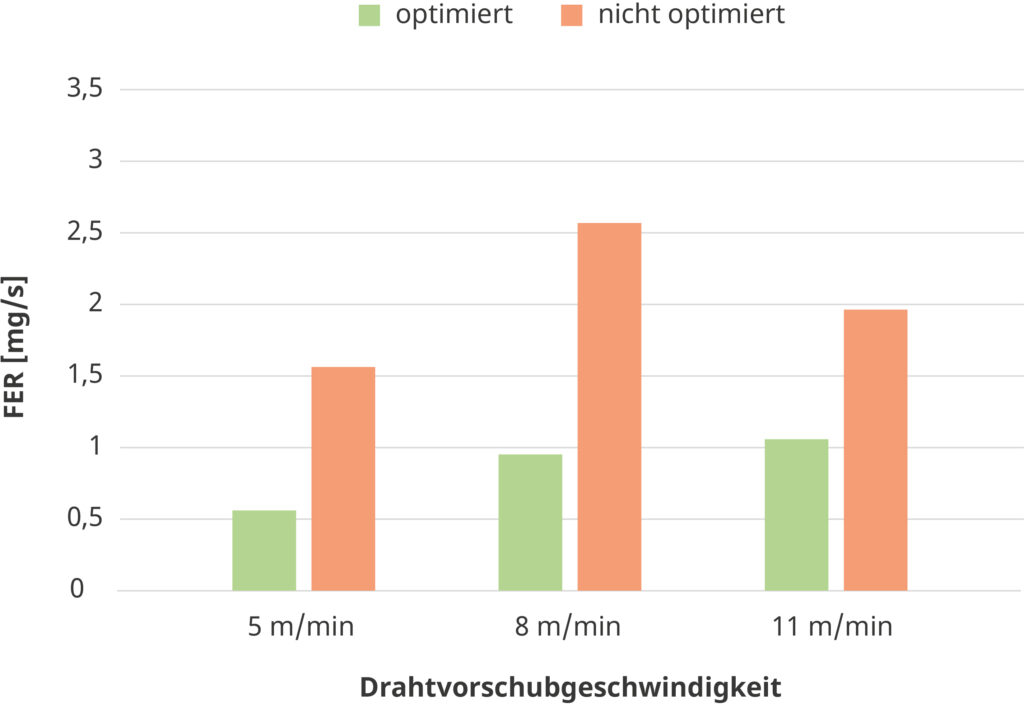
To znamená, že svářeči mají poměrně široký prostor pro nastavení oblouku tak, aby expozice svařovacím zplodinám byla v závislosti na použití co nejnižší.
Porovnání průběhu napětí při rychlosti drátu 5 m/min
Jak ukazují naše společné pokusy, míra emisí svařovacích zplodin přímo souvisí s počtem zkratů. Vysoký počet zkratů vede k výrazně vyšší hodnotě FER. Náš testovací tým se domnívá, že je to způsobeno přechodem mezi materiály. Zkratové jevy způsobují narušení procesu, které vede ke vzniku kovových par a kovových rozstřiků.
Pokud chtějí svářeči minimalizovat emise, je vhodné nastavit proces tak, aby délka oblouku a redukce zkratu byly stejné – tj. aby oblouk nebyl ani příliš dlouhý, ani příliš krátký: Při mírném zvýšení středního napětí se sníží jak zkratové jevy, tak emise (Obr. 2).
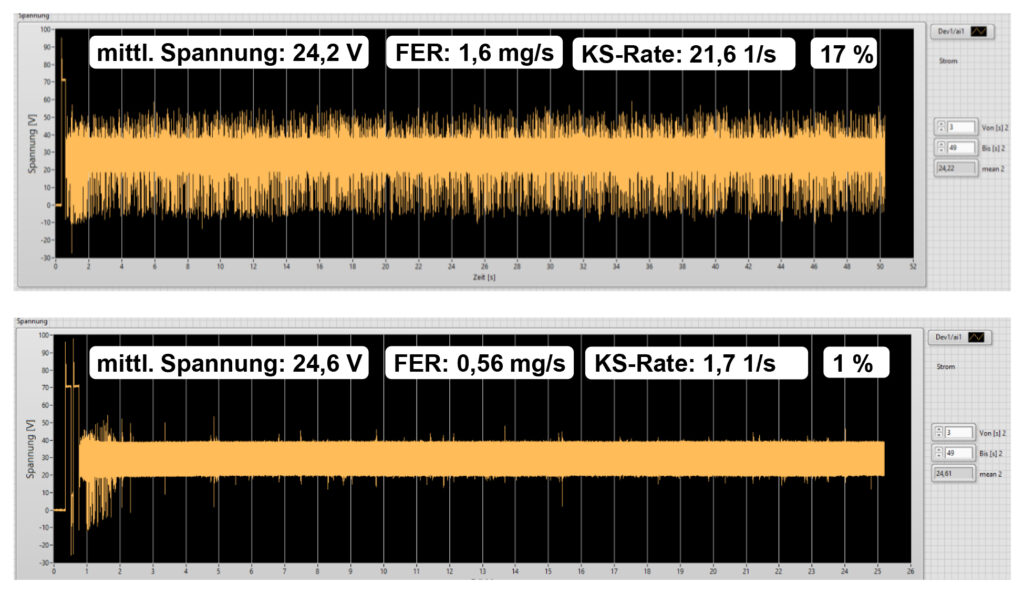
Svařovací procesy při 8 a 11 m/min se chovají analogicky k procesu při 5 m/min, pokud jde o souvislosti mezi středním napětím, zkratovými jevy a emisemi svařovacích zplodin.
Emise svařovacích zplodin při svařování koutových svarů
Pulzní svařování s rychlostí drátu 5 m/min a 8 m/min vede k výrazně nižším emisím: 0,55 mg/s, resp. 0,7 mg/s, než je tomu při rychlosti drátu 11 m/min, kdy jsou emise značné, a to 1,7 mg/s – tedy třikrát vyšší než při rychlosti drátu 5 m/min.
Důvodem nižší expozice svařovacím zplodinám při rychlostech drátu 5 m/min a 8 m/min je – stejně jako u navařovaných housenek – menší počet zkratů. Přitom tažné vedení hořáku produkuje méně svařovacích zplodin než bodavé. Při rychlosti drátu 11 m/min se míra emisí výrazně snižuje (Obr. 3). Je dokonce nižší než při neutrální poloze hořáku!
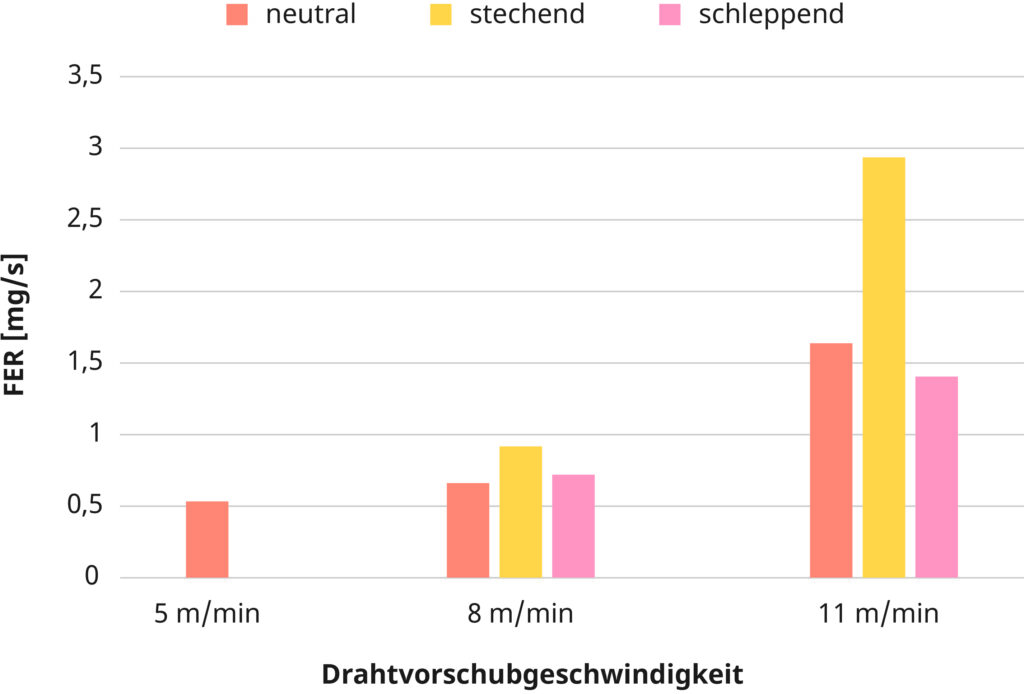
Celkově jsou emise svařovacích zplodin na nižší úrovni než u navařovaných housenek. Nejnižší hodnota rychlosti drátu je ve všech případech srovnatelná s emisemi optimalizovaných procesů (Obr. 1, zelené sloupce), kterými byly navařeny housenky.
Při rychlosti drátu 8 m/min jsou emise svařovacích zplodin při bodavé a tažné poloze hořáku v absolutních hodnotách velmi podobné – stejně jako v případě navařovaných housenek (Obr. 1). Naopak výrazně vyšší hodnota FER, přibližně 2,8 mg/s, byla zjištěna při bodavém svařovacím procesu při rychlosti 11 m/min.
Porovnání průběhu napětí při rychlosti drátu 11 m/min
Společně s výzkumníky z Cách jsme se blíže zaměřili na vztah mezi mírou emisí a středním napětím při rychlosti drátu 11 m/min: Při celkem třech naměřených hodnotách je minimum svařovacích zplodin 1,36 mg/s (optimalizováno pomocí korekce délky oblouku -1,5 V). V tomto pracovním bodě dochází k občasným zkratovým jevům, ale oblouk není zbytečně dlouhý. Proces bez korekce délky oblouku generuje v důsledku delšího oblouku více emisí (1,72 mg/s). Pokud se počet zkratových jevů zvyšuje s klesajícím středním napětím (korekce délky oblouku -2,5 V), zvyšují se také emise svařovacích zplodin (1,6 mg/s), viz Obr. 4.
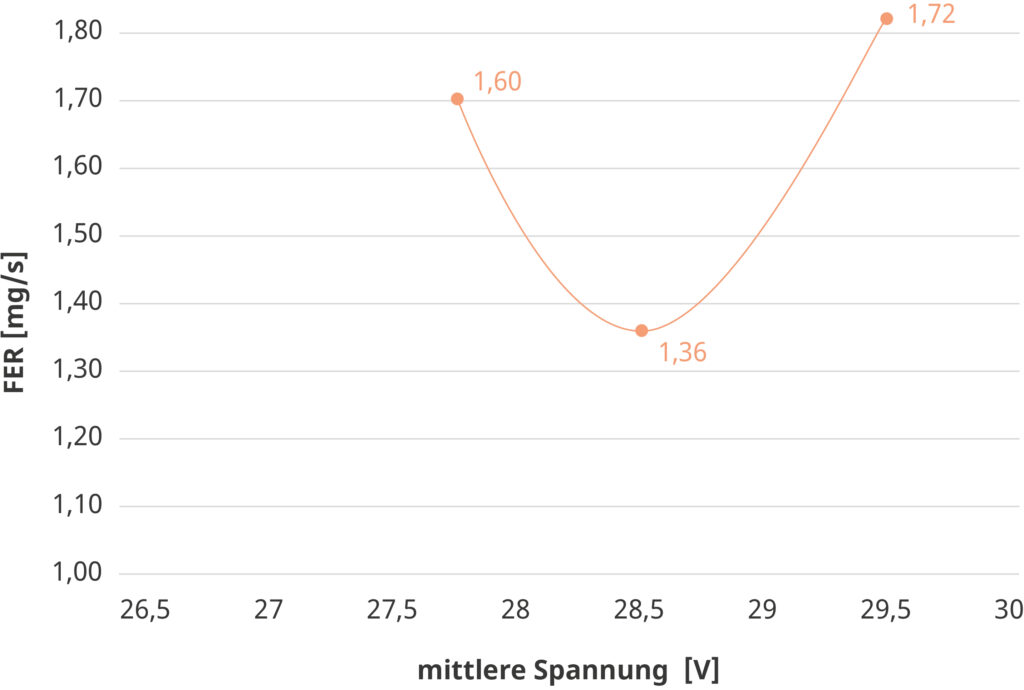
Svářeči mohou vzít věci do vlastních rukou
Svařovací zplodiny je možné významně omezit pečlivou volbou svařovacího procesu, rychlosti drátu a délky oblouku.
Shrňme si to: Kromě dalších aspektů, jako je materiál nebo znečištění (okuje), závisí míra emisí svařovacích zplodin také na odtavném, resp. procesním výkonu, přičemž rozhodující je přechod mezi materiály. Je-li oblouk příliš krátký, vede to k vyššímu počtu zkratů, a tedy k vyšším emisím svařovacích zplodin.
Pokud se však svařovací proces optimalizuje pomocí korekce délky oblouku a použije se při spojování odsávací hořák, například MTW 500i Exento v kombinaci s odsáváním Exento-HighVac, lze odsát až 99 % svařovacích zplodin.
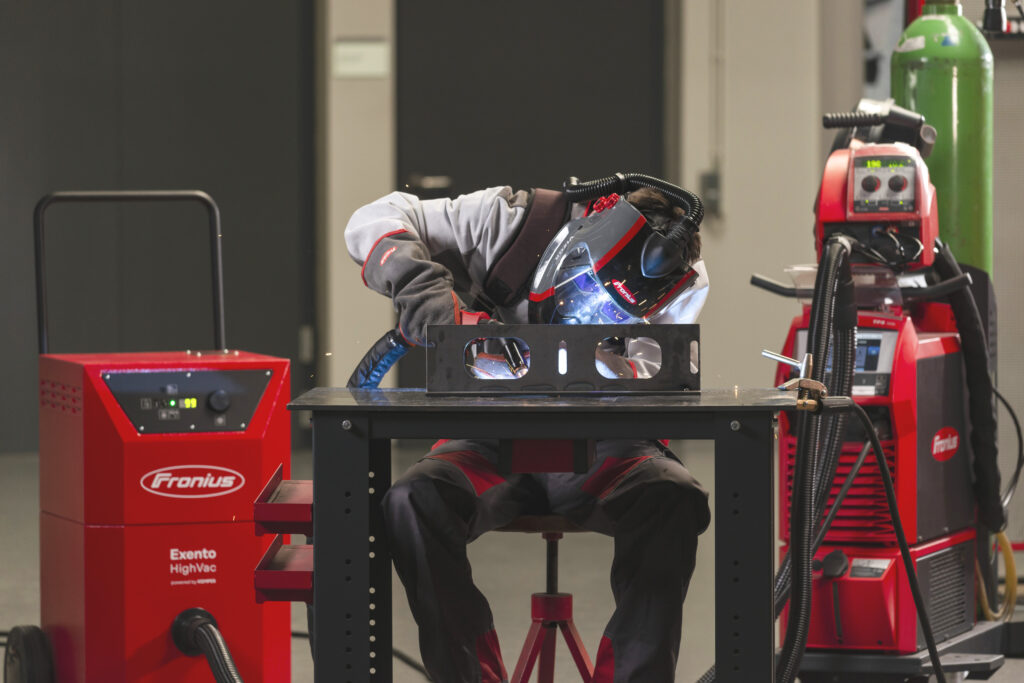
Naše svářečské ochranné kukly s filtroventilační jednotkou jsou třešničkou na dortu, pokud jde o ochranu před svařovacími zplodinami. Odfiltrují ze vzduchu plných 99,8 % zbývajících částic svařovacích zplodin. Pokud svářeči dodržují všechna možná ochranná opatření, je svařování nejen vzrušující, ale také docela bezpečné povolání.
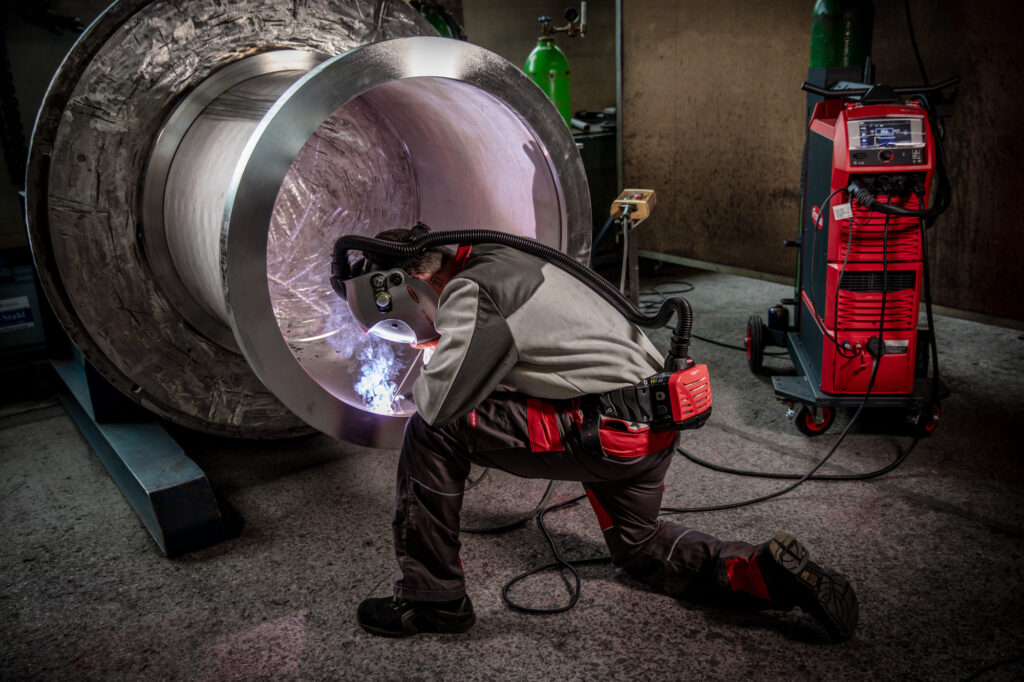
Žádné komentáře