High-quality weld seams are a key criterion for many users of TIG welding processes. But in production environments which are constantly being streamlined to achieve maximum efficiency, time also plays an important role. With ArcTig, Fronius has developed a new TIG welding process for mechanized applications, which enables unprecedented speeds.
The science behind ArcTig
The newly developed ArcTig welding process builds on the foundations of traditional TIG welding. Yet in contrast to conventional TIG applications, the ArcTig welding torch has a special electrode clamping system that cools the electrode right through to the tip. The resulting increase in the electrode’s overall resistance ensures a high arc voltage. The electrons only leak out in a small area and with enormous density, making the arc thin and focused.
Advantages: high speed and top quality
ArcTig offers several advantages, such as perfect weld seam quality and up to double the speed and efficiency thanks to a reduction in the amount of preliminary work and reworking. The focused arc allows users to weld components with a material thickness of up to 10 millimeters in just a single pass, unlike with standard TIG welding, where several weld layers are often required. Time-intensive weld seam preparation, such as U-type joint preparation, is also no longer necessary in many cases. Significantly less post-processing work is required because the weld seam is barely superelevated and the relatively low heat input minimizes distortion. The process also enables higher welding speeds, thereby saving even more time. Thanks to the lower weld seam volume, the cost of filler metal is also reduced.
Container construction specialist Teknokrom is convinced
One of the first fans of the new TIG process was the Turkish container construction specialist Teknokrom. The company was introduced to ArcTig at the 2017 Schweissen & Schneiden trade fair in Düsseldorf and, immediately impressed by the high speed and quality of the weld seams, ordered an ArcTig welding torch there and then. ArcTig allows Teknokrom to triple its welding speed per weld layer. In addition, the new process enables an ideal result with just one weld layer, whereby classic TIG welding would require four weld layers. When the system was commissioned, Fronius application engineers carried out several tests with the customer and together they determined the correct welding parameters for the optimum weld seam.
Teknokrom has been working in container construction since 2001 and produces chrome-nickel tanks for the food industry for export to anywhere from Europe to Australia. These tanks are used in the production of goods such as olive oil, wine, and chocolate.
Find out more about the advantages and application areas of ArcTig on the Fronius website.
Read more about TIG welding:
Synchronized TIG welding – two welders working in sync saves time
TIG welding: top quality connections
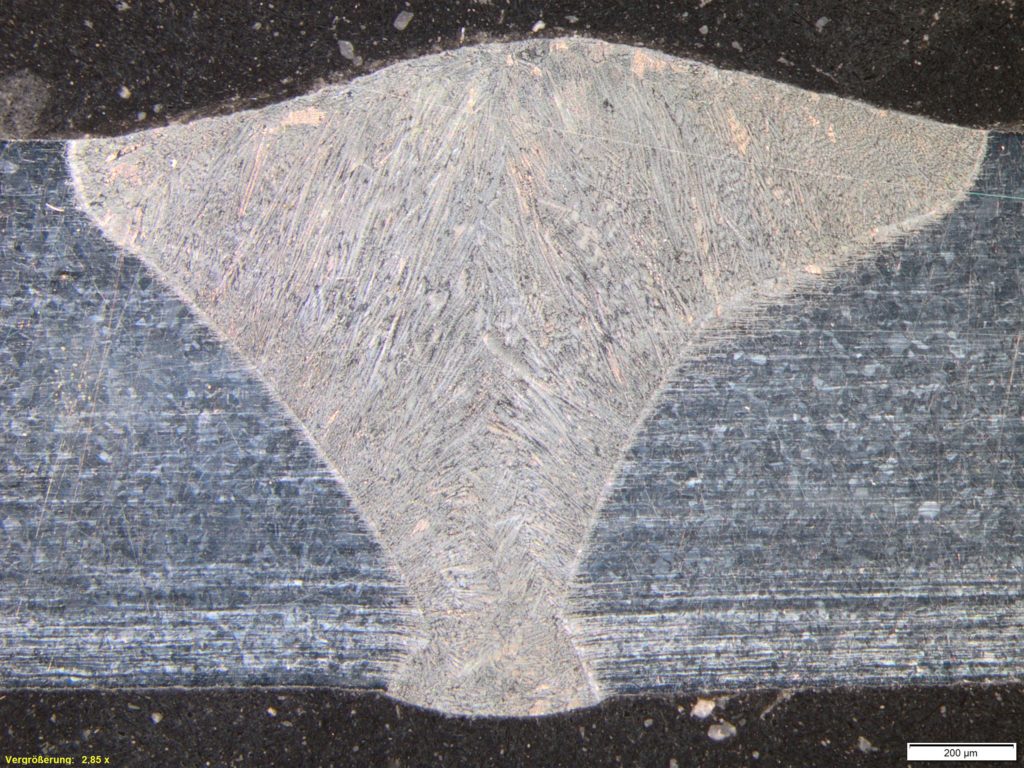
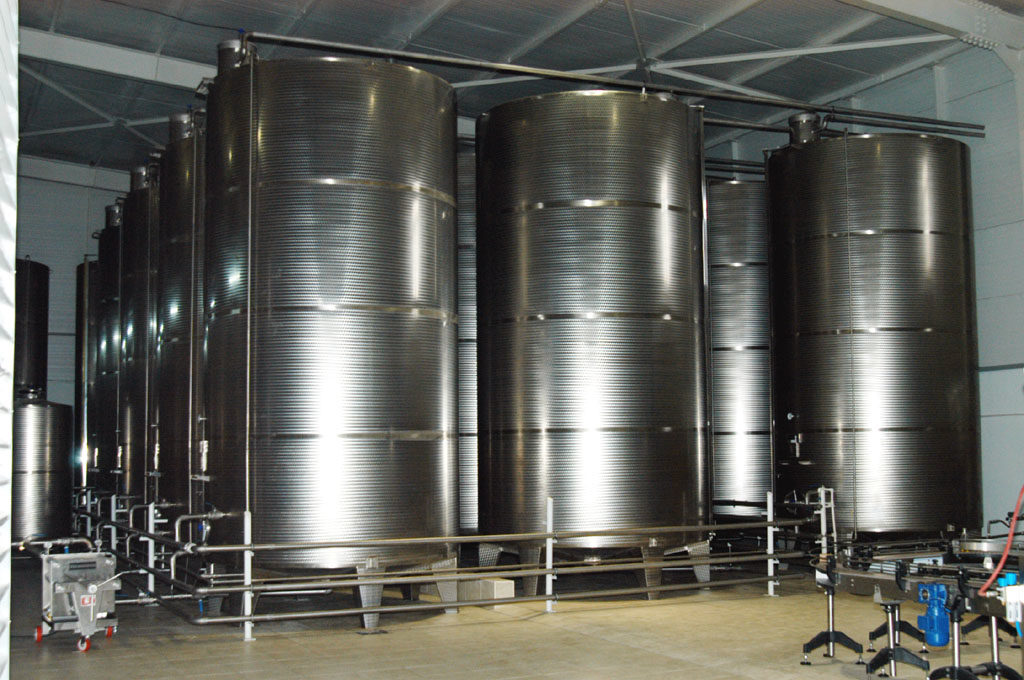
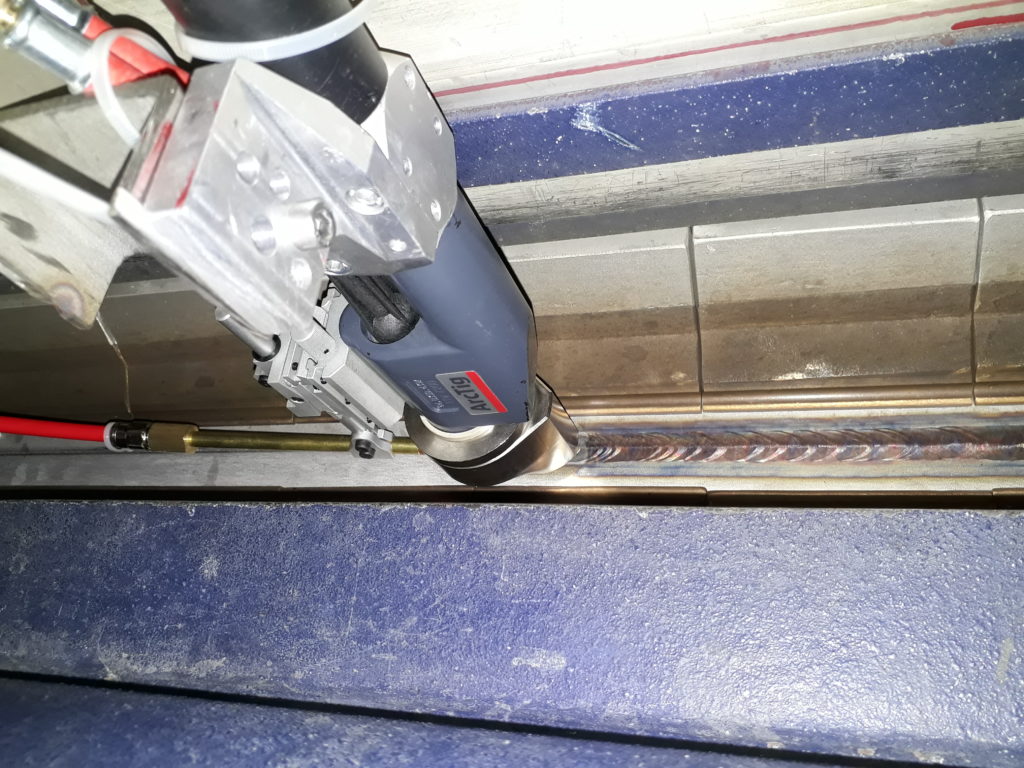
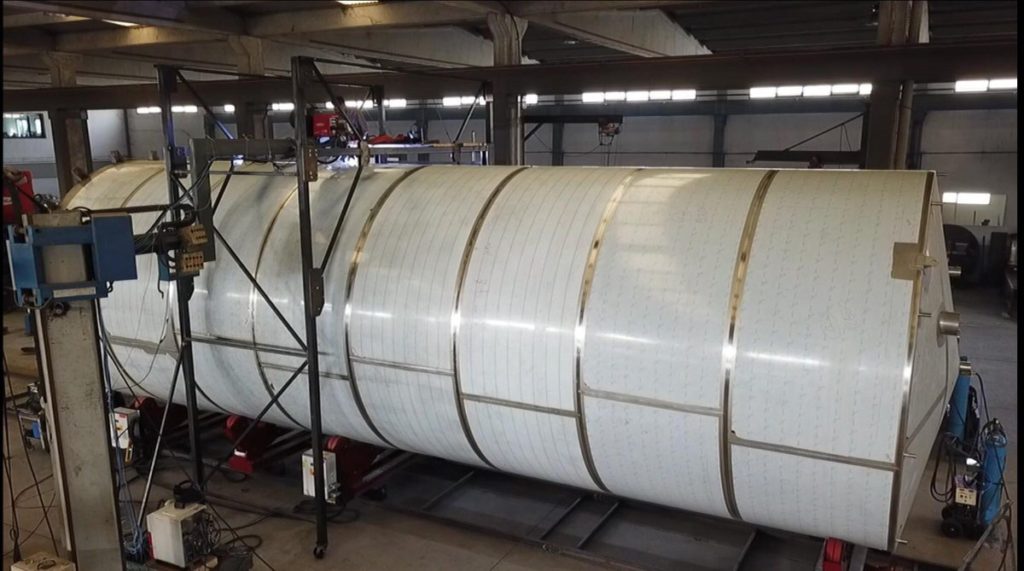
3 Comments
Gerald Austin
23. August 2018 at 21:07Interested in equipment for the Arc tig. Can you send prices?
Jamie M.
2. July 2019 at 3:12Impressive piece of machinery! My shop would no doubt benefit from having an ArcTig.. I’m also convinced. Thanks for the read.
–Jamie M.
redakteur
12. July 2019 at 10:35Hello Jamie! Thank you for your very nice feedback! Glad to hear that. If you are interested, please get in touch with us at: contact@fronius.com
Thanks and have a nice day!