Imagine someone telling you that a simple light bulb would completely revolutionize welding technology. Would you have believed them? “But that’s exactly what happened,” says Josef Artelsmair, one of the inventors of the Fronius CMT welding process. The fact is that two decades ago, no one expected an innovation as groundbreaking as this.
Today, “Cold Metal Transfer” (CMT) represents the most advanced form of droplet detachment. CMT’s reversing motion—that is, the back-and-forth movement of the wire—creates an exceptionally stable arc.
The result is nearly a third less heat input and almost twice the welding speed compared to the conventional dip transfer arc.
Wherever adhesive or solder had to be used before, CMT now makes welding an option as well—and with virtually no spatter. But that wasn’t the only breakthrough: for the first time in the history of welding, it was now possible to thermally join galvanized steel and aluminum.
It all started with a light bulb
The unique properties mentioned above make the CMT process suitable for almost any application. “Even we would never have expected that,” says Josef “Joe” Artelsmair, still somewhat amazed. After all, he and his colleagues were only supposed to find a solution for the light bulb manufacturer Osram.
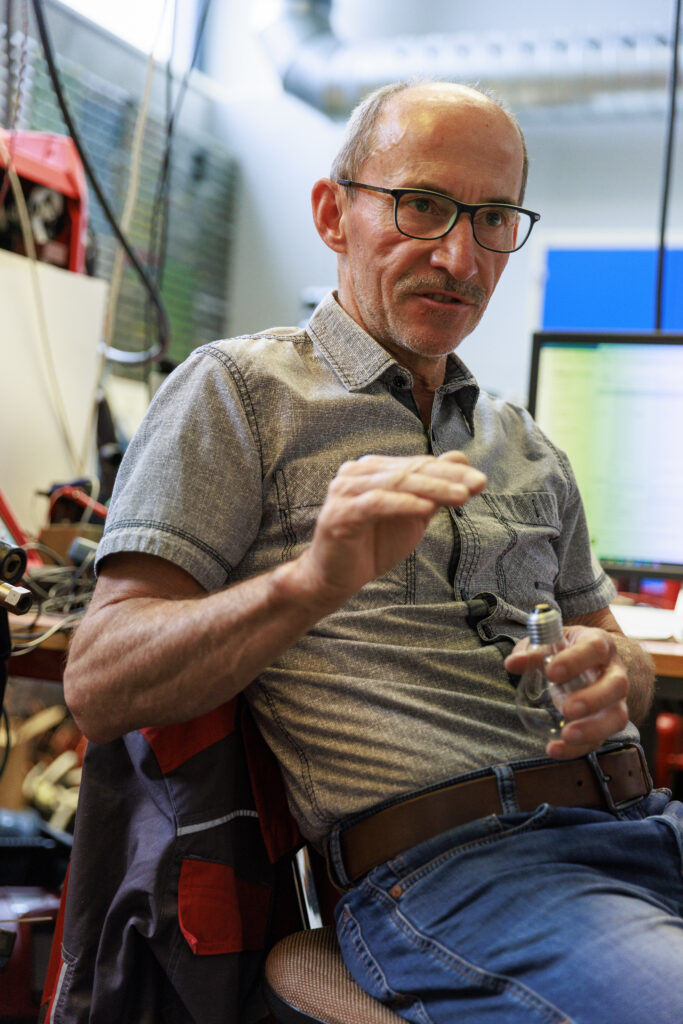
In countries with elevated levels of salt in the air, the sockets and contacts of the bulbs would become heavily corroded. In order to make the bulbs more durable in these regions, the idea was to replace the sockets with a different material and use welding rather soft solder as the joining method.
It was a simple idea, but one that wouldn’t work in practice because the welding processes were far too hot, causing the sockets to shatter time and again.
Osram turned to Fronius for a solution: “We already had spatter-free ignition as a basis to work from. By improving this process and continually working on the back-and-forth movement of the wire, we finally succeeded in welding the light bulb contacts or soldering them using brazing solder as the filler metal,” summarizes Artelsmair.
Nothing is impossible
The team’s work resulted in two machines that used one or two droplets to arc weld the connections for Osram. “It was actually just a special order that was never intended to go into series production,” adds Artelsmair—which meant the project was simply shelved after completion.
But Joe Artelsmair never let go of the idea of repeated droplet detachment, which could perhaps even be used to create a weld seam. “The key was that the wire needed to move faster, much faster. But that wasn’t possible with the wire drive motor we had at the time. The inertia of the gear unit only allowed us to make a maximum of ten forward and backward movements per second.”
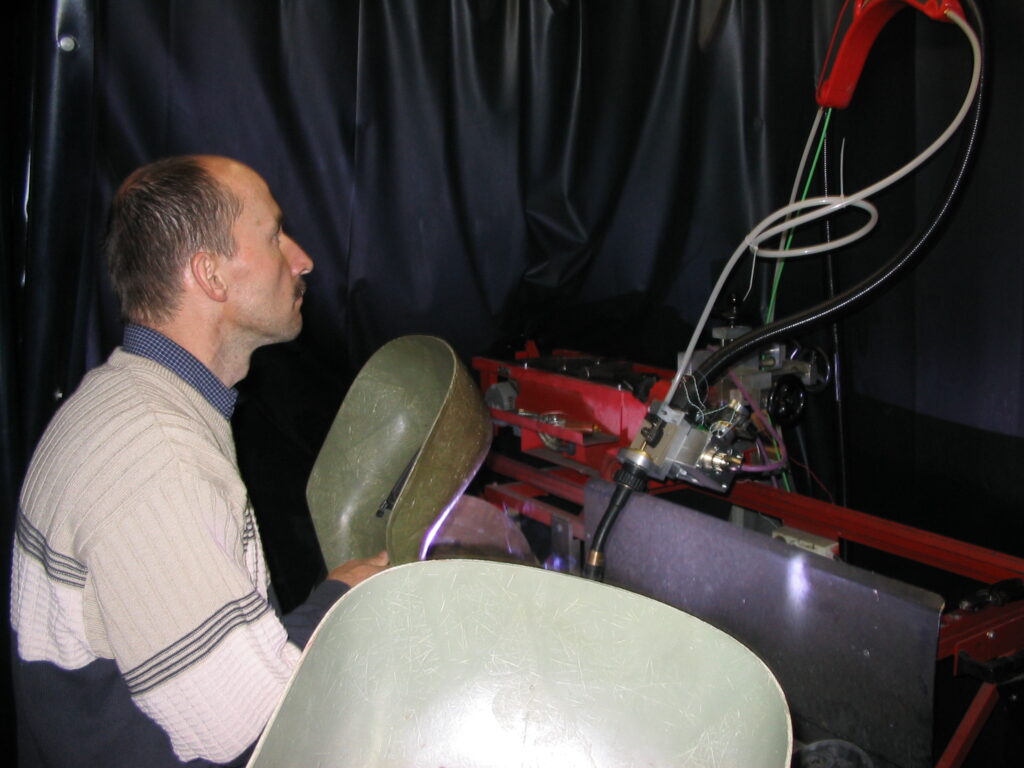
When the decision was made to take up the project again with a larger team, the inventor and his colleagues spent a lot of time developing a gearless drive that would further increase the frequency. The current and wire speed had to be precisely combined and controlled to deliver a perfect welding result.
Perfectionism drives innovation
“No one was thinking about steel at the time. The focus was on aluminum and very thin sheet metal, though there wasn’t really a market for it at the time. But we never gave up and kept running tests with more power,” explains Artelsmair, a trained electrical engineer.
The team continued to tweak things—tightening another screw here, giving the motor even more control power there. It was a long road that included a number of setbacks and even more work before CMT welding as we now know it had matured to perfection. This is also reflected in the staying power of the process, which will be celebrating its 20th anniversary in 2025.
“One colleague even told us that CMT would always be a ‘niche’—that it wasn’t worthwhile and we might as well forget it,” the inventor recalls.
Who wouldn’t give up at that point? “Well, I’ve always been a bit of a perfectionist,” laughs Artelsmair. Even as a small child, he was interested in electronics and loved tinkering on his own.
“I set up a small workshop where I mainly worked on radios,” Artelsmair recalls. So it only made sense that he would start an apprenticeship as an electrical and mechanical engineer at Fronius in Pettenbach in 1977.
After completing his training, he has worked as a developer at the Thalheim site ever since and will be entering his well-earned retirement at the end of May 2025.
Passion and drive—the secret to success
But when he goes, Josef Artelsmair will be leaving a piece of welding history behind him thanks to the Fronius CMT welding process.
“Never lose heart—show you’ve got fight and keep at it. Don’t let anyone or anything tell you it’s impossible,” he says, imparting his top tips to all future developers.
“Technical progress not only requires ambition but a great deal of passion. This is the only way we can continuously develop our welding technology!”
What do you think it takes to create a real innovation? Share your thoughts in the comments!
If you’d like to learn more about current developments in welding technology, read our latest blog articles now Metal 3D printing: The future of additive manufacturing and What is clad welding? Basics and application areas explained!
No Comments