Prototyping is an essential step in the conception and design of a new product. At this early stage of the product development process, designs and construction methods are tested and validated using models. Wherever welded joints are used, their quality is highly important. They are often safety-relevant and must comply with international standards. Not every company is equipped for costly prototype construction. Specialized Fachbetriebehigh-tech companies offer a 360° all-round service from the feasibility study to pre-series production and beyond.
Expertise in welding technology and metallurgy
The development of innovative products usually runs parallel to technical progress. New and difficult-to-join metals, such as high-strength steel or aluminum, magnesium, and titanium alloys, are often used in complex designs. In order for these materials to be welded to a high quality, extensive specialist knowledge is required—both in welding technology and metallurgy. High temperatures and rapid cooling times change the microstructure and significantly influence the mechanical properties of the components. If the wrong welding parameters are selected, this can lead to undesirable residual stresses, fusion defects, pores, cracks, or welding notches. Filler metals and shielding gas mixtures can also influence the properties of a weld. Contamination, for example with carbon, can have a negative effect on ductility (the ability of a material to deform under load without breaking).
Feasibility studies—the first steps in prototyping
Welding new types of components and materials is associated with risks, both legal and financial. Nobody wants to imagine what could happen if structural components of buildings, bridges, ships, vehicles, or airplanes were inadequately welded. Therefore it is not only large industrial enterprises, but also smaller firms, that rely on feasibility studies and prototyping. If welding robots will be used on the production line, simulations can help. With suitable software and virtual prototypes—so-called digital twins of physical components—strategies can be developed to avoid welding errors. Interfering contours and singularities are detected at an early stage, and measures to minimize distortions and stresses can be planned by integrating clamping devices.
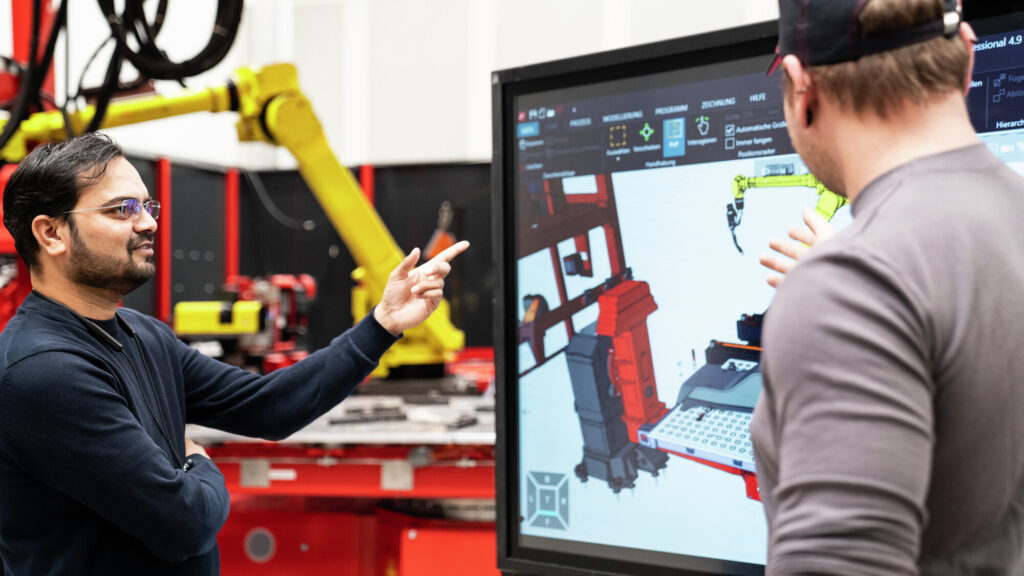
Welding tests reveal valuable data
As soon as the feasibility tests have been successfully completed, the welding tests on the physical component begin and the first prototypes are created. Depending on the base material and seam geometry, different sensors are used for weld seam detection and quality assurance. Welding data management software records every single parameter such as wire feed speed, voltage, or amperage, and ensures the subsequent reproducibility of welds.
Following the joining work, the components are measured to detect any warpage. Where the necessary resources are available, the welded components are tested in the laboratory. In addition to non-destructive testing, destructive testing methods are also used. Common methods are ultrasonic, dye penetrant, and X-ray tests as well as tensile, bending, and notch impact tests. Prototyping is an iterative process in which prototypes are repeatedly adapted and refined based on the knowledge gained.
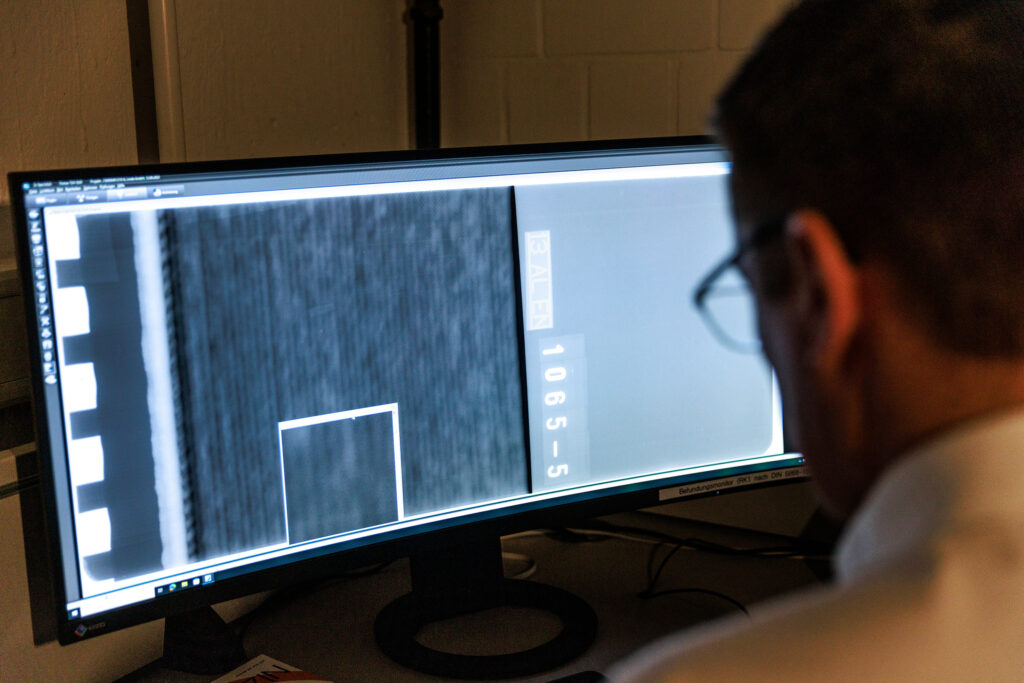
Purchasing welding expertise reduces costs and risks
In such a dynamic environment as we find today in both the industrial and commercial sectors, not every company can meet every challenge. Sometimes there is a lack of skilled personnel, fully automated high-tech welding systems, and production lines. Robot welding cells cost hundreds of thousands of dollars and qualified programmers are anything but cheap.
It may be more sensible to outsource feasibility studies and prototype production before immediately investing in new systems, employees, and products. This provides valid parameters for the start of production as well as for integrating new welding systems. By outsourcing the welding-relevant parts during the product development phase, companies can save themselves a considerable amount of the costs and risks that are always associated with developing new products. Equally as valuable is the ability to learn what will definitely not work to avoid future mistakes.
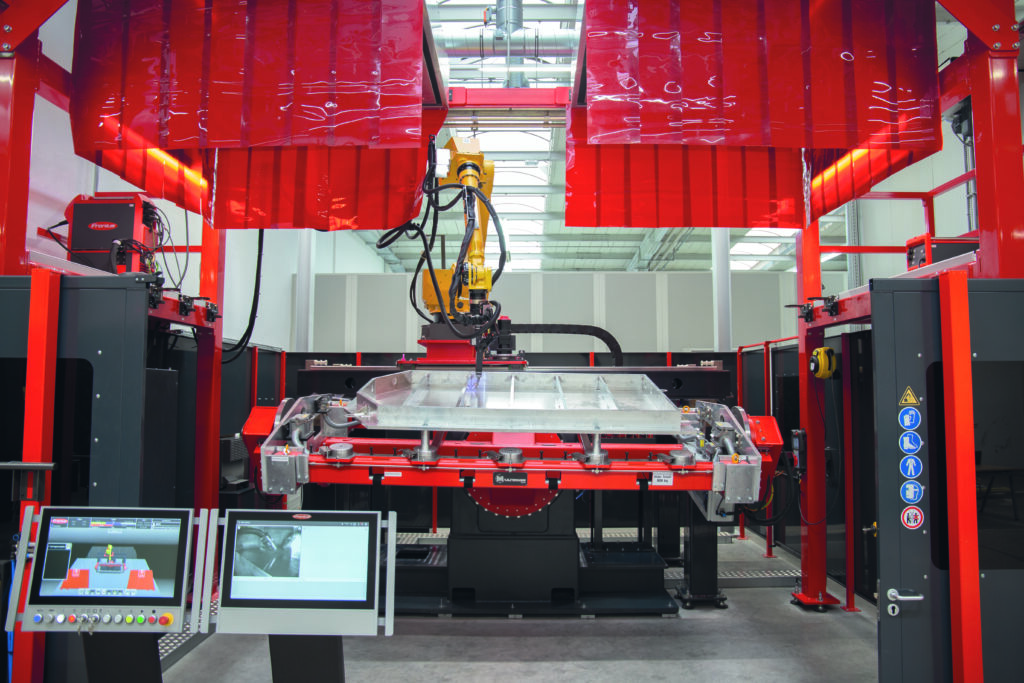
Fronius supports the welding of critical components
The Austrian company offers metalworking companies a customized service in compliance with the relevant standards, consisting of feasibility studies and prototyping as well as pre-series and series production. Experienced, certified welding professionals support commercial and industrial customers with state-of-the-art technology and comprehensive expert knowledge in joining difficult-to-weld components and materials.
Feasibility studies are initially carried out at the Fronius site in Wels, followed by prototype production if requested. This requires that the client submit their welding specifications as well as the 3D data of components and clamping devices. Fronius performs a virtual analysis of this information, in order to draw conclusions about weldability, accessibility, and cycle time. Problems that arise are discussed together with the customer and optimization and solution options are developed.
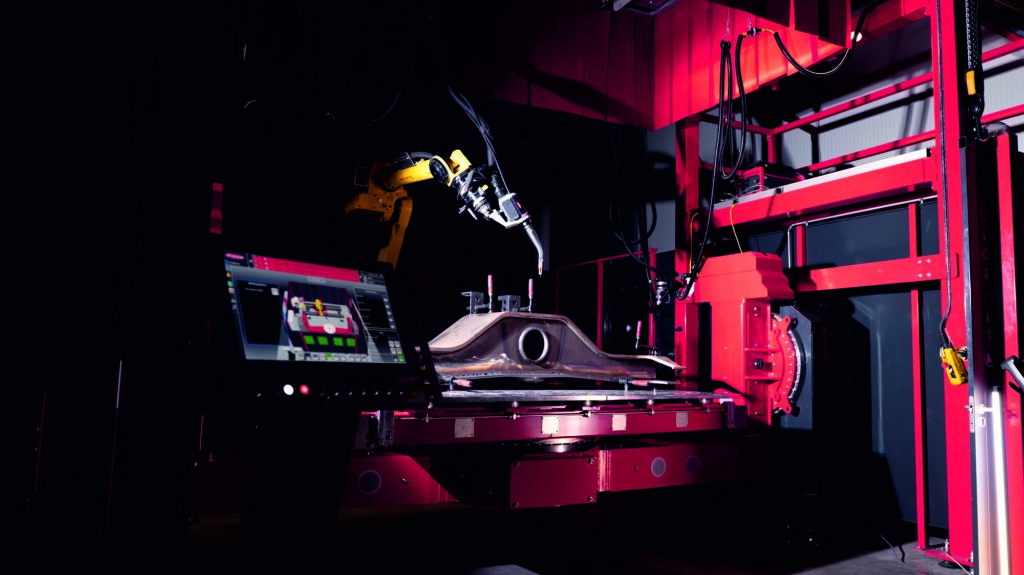
Complete service package—from the feasibility study to the finished product
As soon as valid welding data is available and the first prototypes have been successfully welded, Fronius develops a production concept and, if requested, takes over the series production. If the customer is to manufacture the product themselves, Fronius can also design, build, and supply all the customized robotic welding systems needed on request.
Furthermore, on-site commissioning services, employee training, and regular maintenance and calibration of the systems are all part of the comprehensive service package, which is supported around the world by a network of 38 subsidiaries and Fronius Sales and Service Partners in over 60 countries.
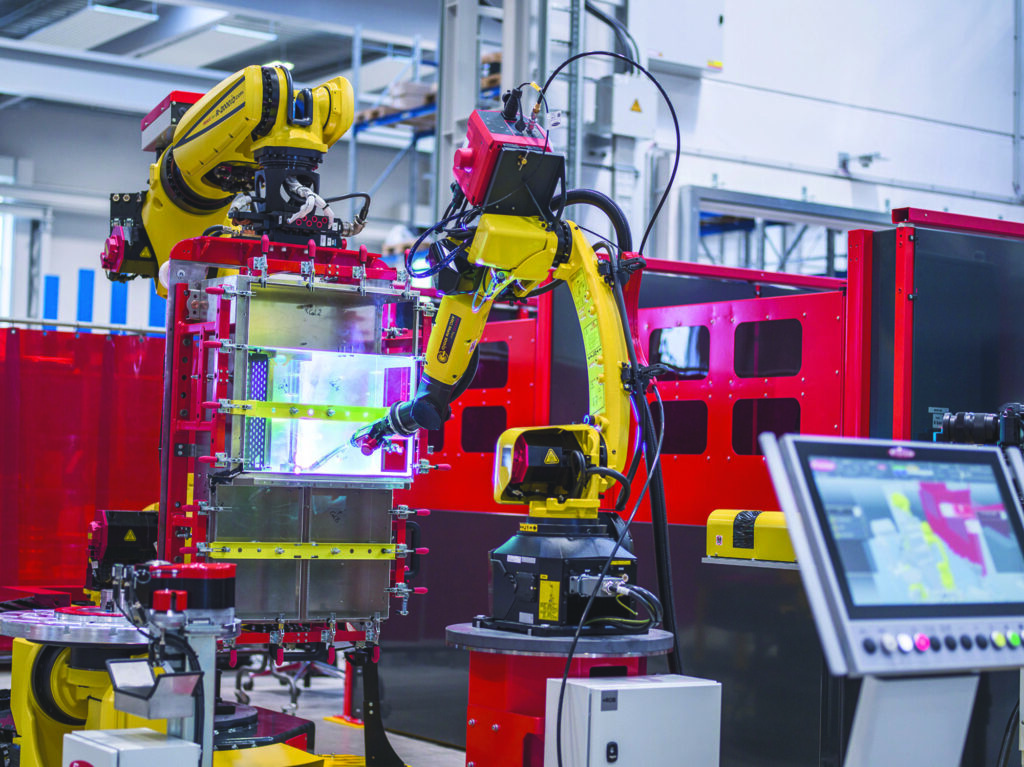
Additive manufacturing on the rise
Additive manufacturing places specific requirements on the welding process. This technology enables complex, custom-designed components to be produced with high precision and low material consumption. One example of this is pipeline construction, where completely new standards and requirements are currently under development. As a member of the “Joint working group for additively manufactured components under the Pressure Equipment Directive of the German Institute for Standardization (DIN)”, Fronius is at the forefront of this work. Working in collaboration with MIGAL.CO, Linde Engineering, and TÜV SÜD, the Austrian welding experts took part in the model qualification of an additively welded pipe branch in the form of a pressure vessel. The working group assessed the applicability of the draft standard prEN 13445-14 to the components of unfired pressure vessels. This collaboration resulted in the Fronius Additive Pro characteristic for the Wire Arc Additive Manufacturing (WAAM) process, which enables fast, cost-efficient, and precise component production.
Working together towards a sustainable future
With comprehensive services and cutting-edge technology, Fronius ensures that companies are ideally equipped to master the challenges of technological transformation and shape a sustainable future.
No Comments