In the distance it sounds like a storm brewing, however as it draws nearer, the initial murmuring noise grows into a menacing rumble – finally, the freight train thunders past the platform. The force of railway vehicles can be overwhelming, but so can their diversity…
What is a railway vehicle?
The term covers all vehicles, trains, and trams that run on one or more rails. These include railroad vehicles such as locomotives, railcars, rail tractors, and passenger or freight wagons, as well as monorails, suspension railroads, and funicular railroads.
When constructing these railway vehicles there is much to consider – including during welding. How does this look in practice?
Production of track construction machines at MATISA
Swiss company MATISA, which manufactures track construction and maintenance machines, provides an excellent case study. One specialty of the traditional company is individual custom adaptations: “Each of the 300 machines that we currently have in the field is unique,” says Rony Chiavone, welding coordinator and head of non-destructive weld testing at MATISA.
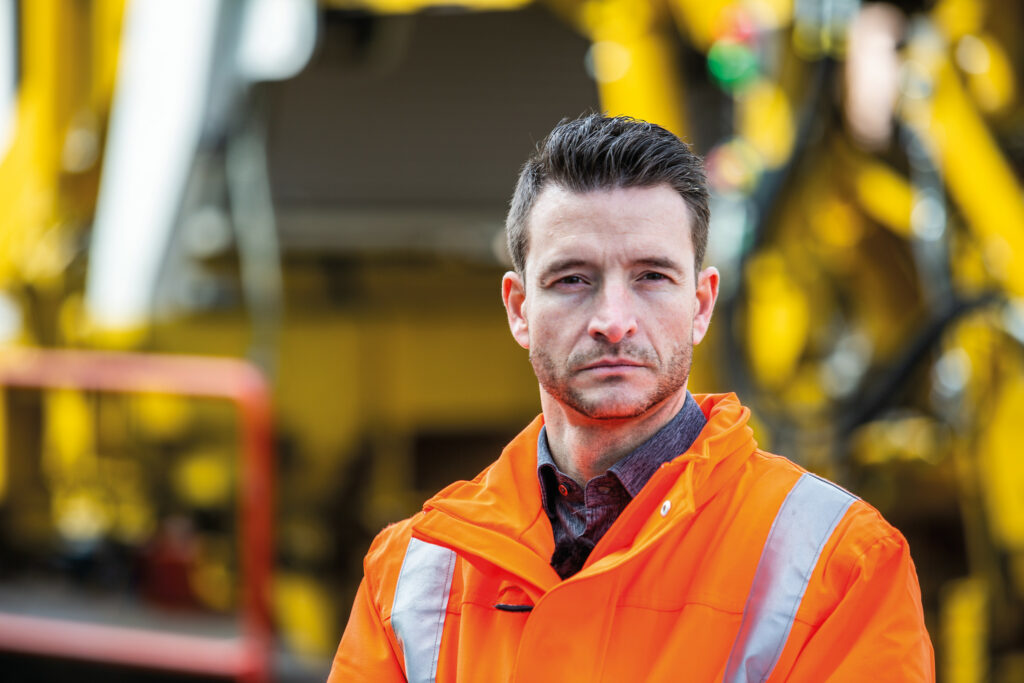
“This is because there are different track gauges and also customer requirements, such as the integration of a washroom.”
Rony Chiavone, welding coordinator and head of non-destructive weld testing at MATISA
…
For this reason, the Swiss firm produces all the important parts including the bogies themselves.
…
Accordingly, production and construction take high priority at MATISA: out of a total of 500 employees, 100 are engineers who look after the different levels of electrical and mechanical structures in the trains. Of the 400 staff in the production department, 50 are fitters and welders.
MATISA has specialized in custom machines for the construction, maintenance, and renewal of railroad tracks since 1945.
Typical welding task in railway vehicle construction: a butt weld with a root pass and several filling runs.
Digression: welding of railway vehicles – long seams
The average railway wagon is roughly 27 meters long. This means that many long seams have to be welded on containers for freight trains or trucks, which is carried out as a largely mechanized process. Joins between individual components as well as internal equipment are primarily welded manually. Regardless of the welding process, one thing is of the utmost importance in the manufacture of railway vehicles: safety during subsequent operation.
Wagon, truck, and bogie – welding according to EN 15085
In order to meet the strict requirements, MATISA is certified to EN 15085. The Swiss company generally uses sheet metal and profiles made from conventional construction steel with thicknesses from 10 to 200 millimeters for the trucks, bogies, and superstructures. Welding work, for example on a tamper, accounts for roughly one third of the production time.
Even for relatively simple products, such as transport wagons, hundreds of meters of weld seams are needed. In general, the experts weld seams up to 2 meters in length manually. For more extensive longitudinal seams however, the company relies on a welding carriage.
Digression: EN 15085 – European standard for welding railway vehicles
In the EU, the welding of rail vehicles is governed by EN 15085. This standard contains recommendations for production using welding technology and stipulates which component tests must be carried out. In addition, EN 15085 governs the required certification of manufacturing companies as well as the qualifications of the welders.
Depending on the safety relevance of parts and components, various requirements apply. For example, the welding of bogies and vehicle superstructures is subject to stricter rules than the joining of access doors and freight containers; simple fixtures such as seat frames and switch cabinets are not considered safety-critical.
A positioning device simplifies the welding of the 25-meter long truck of a transport wagon.
Welding a transport wagon in practice
To avoid out-of-position welding and ensure the required tolerances are met, at MATISA the five truck parts of the transport wagon are clamped on a positioning device. Then the staff start welding the box sections. Specific welding sequences are required so that the frame does not buckle or become warped.
In addition, the frame is turned around regularly to avoid deformation. Finally, the weld seams are subjected to both a visual inspection and non-destructive ultrasound and magnetic testing, as these are classified as a welded, safety-related component.
MATISA uses a total of 50 Fronius welding systems, including TPS 450, TPS 4000/5000, and eight TPS 400i systems
Even relatively simple train vehicles require hundreds of meters of weld seams
The quality requirements for the weld seams as well as the various welding tasks and production processes – which require high system availability and user friendliness – place high demands on the welding systems used. MATISA has been using systems from Fronius since the start of the 1990s. The railway vehicle construction company currently has 50 Fronius systems in use, including the new TPS/i.
…
Find out more about how MATISA welds railway vehicles:
Link to Reference MATISA MATÉRIEL INDUSTRIEL S.A. SWITZERLAND
Link to Application Story MATISA MATÉRIEL INDUSTRIEL S.A. SWITZERLAND
No Comments