Can you imagine a firefighter tackling a blaze without a helmet? Or a surgeon operating on a critically ill patient without sterile protective clothing? It’s almost unthinkable. Safety is paramount in these scenarios and the same applies to welders, whose work can pose significant health risks. This makes it all the more important to ensure they have sufficient protection measures in place. Failing to do so can even result in hospitalization, as is the case for welding and application engineer Tobias Rieder. In this interview he tells us all about how he prevents this today, why milk used to be regarded as a supposed protective measure, and how health awareness among welding specialists and companies has changed over the years.
Tobias, what does health and safety in welding mean to you?
As a welder, paying attention to your own health and safety is essential. The best way to ensure maximum protection is to combine several measures to form a complete package, consisting of an effective extraction system, a proper welding helmet, adequate protective clothing, and full personal protective equipment in general. The workplace should also be optimally equipped to ensure sufficient levels of safety. Ultimately, you have to be able to move freely while working, so no trip hazards should be left lying around. The best possible level of protection is achieved when you can check the box next to all of these criteria.
Be honest now: Does this really happen in welding practice?
Yes, nowadays, it does. But, this wasn’t always the case. I’ve worked at several different companies and I can say that health and safety was most definitely not always a top priority, at least not in the companies I worked for. It wasn’t that there were no measures in place at all—I was always given protective clothing, for example. But additional equipment—such as extraction systems or ear protection—were mostly unavailable. Luckily, things are different these days.
How did you deal with not being properly protected when welding?
I just accepted the situation. It was quite simply considered normal to work like that. Nobody even gave a second thought to any further protective measures. In the early days of my apprenticeship I can remember asking if I could get some protective goggles to wear when sanding, at which point I was asked: “Are you a man or a woman?” That made things very clear to me. Back then nobody wore gloves at work either, which is barely imaginable today.
You say that people just accepted the situation and went about their job as if this was completely normal. But working without the necessary protection had just the same consequences then as it does today. Was there any awareness at all of what can happen without protection?
Definitely, because we felt the consequences with our own bodies. Be it welder’s flash—which is damage to the surface of the eye—,symptoms of poisoning, burns, or cuts: I genuinely experienced it all. So, yes, it’s not that we didn’t know about or feel how detrimental this way of working was to our health, but this issue just wasn’t a top priority in the welding world. The familiar saying at the time was: “Men know no pain.” Of course, this was just false pride talking, but that’s just the way it was back then. Things have since changed for the better, which can only be a good thing. These days I could never work without welding gloves, because I’ve become aware that protection and welding go hand in hand. Today, I can thankfully say that it has become normal to weld with protective equipment.
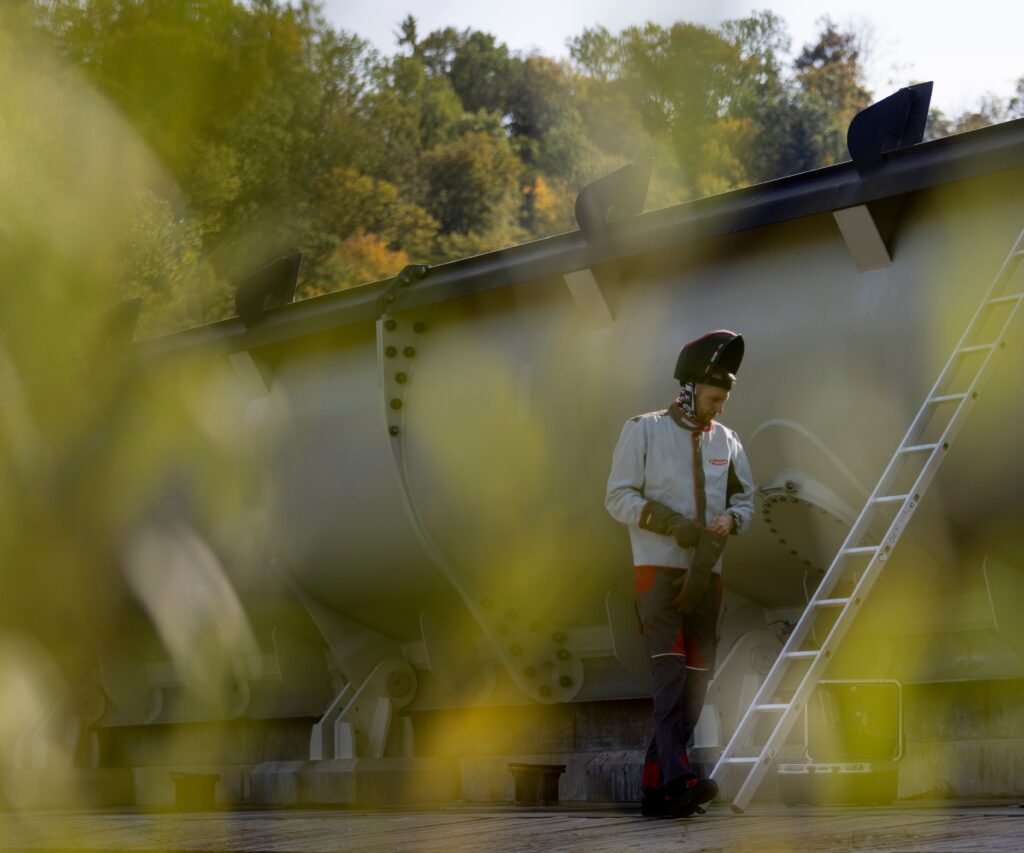
You’ve been a welder for around 20 years now and it would seem you’ve already had your fair share of experiences with the consequences of insufficient protection. Can you give us any more details?
I cut through the tendons in my fingers a few times when pre-processing welding sheets, for example. I still have scars from that. Burns were also a daily occurrence and were particularly catastrophic when welding aluminum, as these wounds take a long time to heal. And then there are the effects of welder’s flash, which I suffered from very often. There were four or five occasions when that led to severe consequences.
What do you mean by severe consequences?
I ended up having to go hospital each time to have my eyes sealed up. My eyes felt absolutely terrible, as if there was some kind of foreign object in them, like sand. The headaches were unbearable, too. They eventually treated my eyes with a special ointment and drops, and then I had to spend two days back at home completely blind. I really couldn’t see anything at all.
After that happens to you several times, don’t you promise yourself that you’ll be more careful next time?
Yes, of course. It’s just like with alcohol. “I’m never drinking again” is a statement that we’re all familiar with. But I’m still careless sometimes, even though my awareness of welding protection is very different today than it used to be. Only recently I unfortunately suffered from a mild flash when I was teaching beginners. I was concentrating too much on what the others were doing and for a few seconds I forgot all about protection.
What else have you experienced?
I once contracted a bad case of pneumonia caused by welding fumes, which put me out of action for a long time. And I have twice suffered from metal fume fever when I was welding galvanized components. This illness is brought on by inhaling zinc oxide fumes, which are highly toxic. The headaches I had as a result were extreme. I also had the shivers, a fever, and sweating to contend with, so a visit to the doctor was inevitable. The first time I suffered from metal fume fever was during my first year as an apprentice. At the time I was told that I should drink milk, as this has a detoxifying effect on the body. This is only a myth, though, and has never been scientifically proven, but in welding circles this recommendation still circulates today. It’s now clear that using an effective extraction system and a welding helmet with ventilation is the only proven way to prevent this condition.
Why was no extraction system used at the time?
Because it simply didn’t exist at the company I worked for. This was probably due to cost reasons. The halls there were open and that was that. Nothing else was done. Thankfully we know better today.
You say that awareness among welding specialists and companies has taken a turn for the better nowadays, as far as health and safety in welding is concerned. Yet your own experience also confirms that this issue is still not given as much attention as it deserves. What further measures could be considered to give more weight to this crucial part of the industry?
I think it’s great that companies have changed their views in this regard and invested in protective measures. However, it’s vital that individual welders also get on board with this issue. And, in my opinion, an authentic approach is the only way to achieve that. By that I mean leading by example, as young workers are ultimately influenced by older, more experienced professionals. This approach means the use of protective equipment becomes endorsed and ingrained within the industry. Guidance from above is, of course, required, but it’s the belief that we have to take responsibility for our own actions that really makes the difference. After all, as people, our health is the most important asset we have.
Which measures could really make a tangible contribution here?
Authentic advertising material for protective products is certainly one way to help. I often come across welders sitting together during their breaks and flicking through the same newspaper for the umpteenth time. If, for a change, they were to find a brochure showcasing the latest welding helmets, for example, this would surely grab their attention. Design is another important factor here, as authentic images that really resonate, alongside clearly presented advantages, are more likely to appeal to welders. Illustrations showing what happens if you don’t use a particular protective product would also be an effective way to get the message across.
You mean like on a pack of cigarettes?
Yes, exactly. For instance, you could show a welder standing with their head surrounded by fumes and a colleague next to them wearing the latest welding helmet complete with ventilation and welding fume extraction. That’s got to make a lasting impression. Be it via images like these or other approaches, in principle you can’t do any more than highlight the issue. But the more often and more effectively this happens, the better. What’s certain is that you have to give it time.
Measures such as these give issues like health and safety in welding the space they deserve and also create an effective instrument for tackling the shortage of professional welders. Health awareness within the general public is also different nowadays to how it was in the past, so making this job as safe as possible is a crucial part of the struggle to increase the number of skilled workers. This will allow us to safeguard this splendid craft for generations to come.
Is there anything else you would like to add?
Yes, there is. We’ve spoken about which illnesses and accidents I’ve been affected by that were down to a lack of protective equipment. At this point, I would like to appeal to all welders to generally just look after themselves. All too often we hear about accidents at work caused by carelessness. If someone tall like me bumps their head on something for what feels like the hundredth time due to their height, then they really only have themselves to blame.
Would you like to find out more about health and safety in welding? If so, then feel free to head over to our landing page. Be it welding fume exposure, welder’s flash, or other dangers—we have collated all the key information about the risks and effective protection measures in one handy place. You’ll also find more information on our poster about welding fume protection. Check out our 8 tips today!
2 Comments
Fluix
11. March 2023 at 12:12Worker safety is primarily the responsibility of the project manager, not even the welder. A personal protective equipment checklist is what you need to make sure you provide a safe enough working environment for all employees.
One of the class :D
29. September 2023 at 13:53THX this help me a lot for my homework, Now i can copy and paste eazy´er
Because the teacher only printed it