¿Qué tiene que ver uno de los vehículos más prácticos y con mayor capacidad todoterreno del mundo con la documentación de los datos de soldadura? La enorme distancia al suelo y la gran altura de vadeo del Mercedes G dejan entrever inmediatamente que el vehículo debe poder soportar las condiciones todoterreno más duras. La fuerza de tracción y la larga vida útil deben estar siempre garantizadas. Los fuertes impactos a gran velocidad en terrenos irregulares suponen una continua carga elevada en todos los cordones de soldadura. Por este motivo la garantía de calidad y la optimización de los procesos de producción basados en un sofisticado sistema de gestión de datos de soldadura son tan cruciales en este aspecto.
Producción y soldado de bastidores del Mercedes G en Magna Presstec
Los elevados estándares de calidad de la Clase G, exigidos tanto por los fabricantes como por los consumidores finales, se plasman en la demanda: el interés por los todoterrenos de lujo está en constante aumento. Para poder cumplir con la cantidad de componentes requerida, es imprescindible que la producción del bastidor del chasis presente un alto grado de automatización.
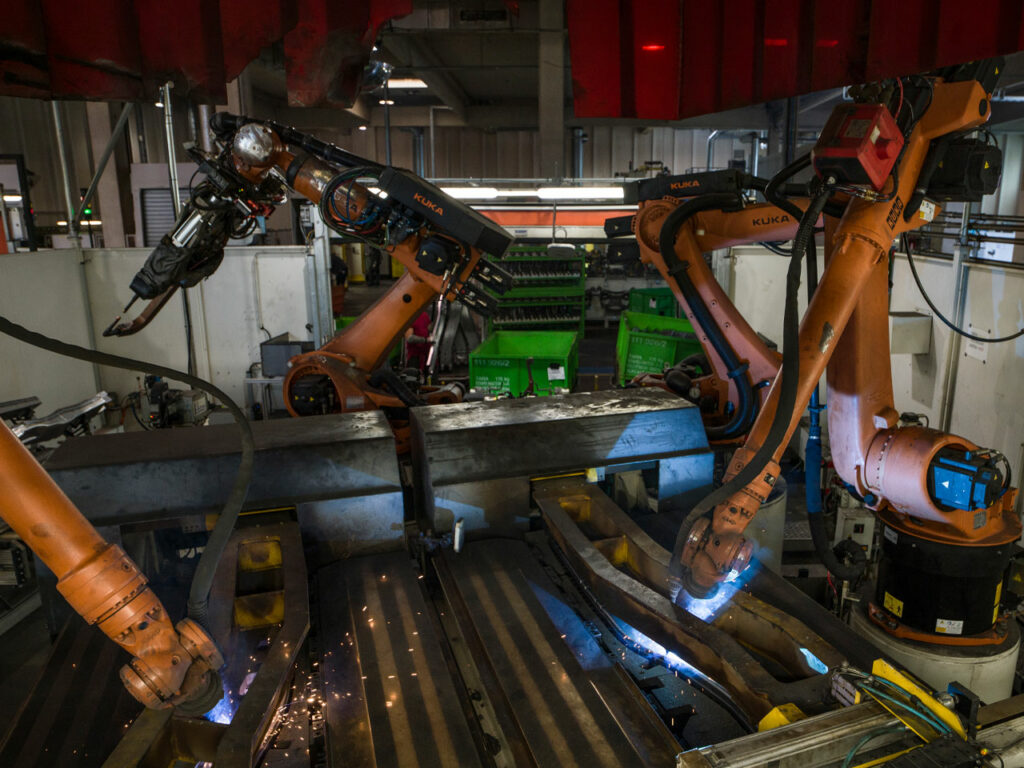
La línea de producción de alta tecnología del proveedor de primer nivel Magna Presstec, en Lebring, sur de Austria, cuenta con este requisito, pues sus sistemas robotizados de manipulación y soldadura encajan perfectamente en sus 100 metros de longitud. Un proceso de soldadura por arco pulsado (PMC de Fronius) extremadamente rápido, de gran precisión y controlado digitalmente satisface las altas exigencias en cuanto a la tecnología de unión. Las instalaciones de producción están equipadas con piezas individuales sólo al principio. Cada 10 minutos sale del taller un chasis Mercedes G listo para su uso, suspendido en la grúa aérea como por arte de magia.
Máxima producción automatizada al detalle. Extremadamente complejo
“Nuestro objetivo es que todos los bastidores sean idénticos. Debe descartarse cualquiera que sea diferente“, enfatiza Kurt Hartmann, Responsable de Producción y Supervisor de Soldadura en Magna Presstec.
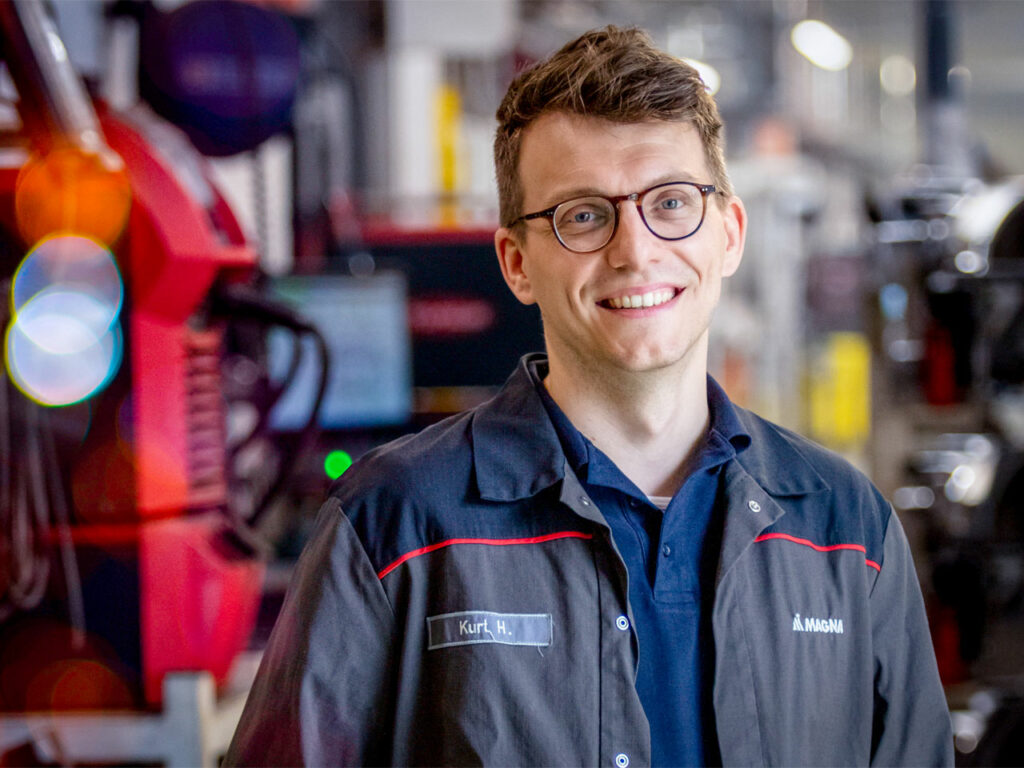
Producción y soldado de las partes delantera y trasera del bastidor:
“Aquí fabricamos en tres etapas“, detalla Hartmann. “Las partes delantera y trasera del bastidor, es decir, las dos primeras etapas en la planta de producción, se fabrican simultáneamente. Al principio, algunos empleados colocan las piezas en los sistemas de soldadura. En las celdas, los robots de soldadura ensamblan los componentes. Un robot de manipulación se encarga de recoger los componentes acabados, transportarlos a la siguiente celda y colocarlos. Al final de cada etapa hay una celda inaccesible para el personal en la que se sueldan cordones largos, pero que también se utiliza como estación de enfriamiento o como estación compleja, por ejemplo, para la compresión: las carcasas inferiores se anidan con las carcasas superiores de los soportes longitudinales, se colocan en posición y se sueldan bajo presión“.
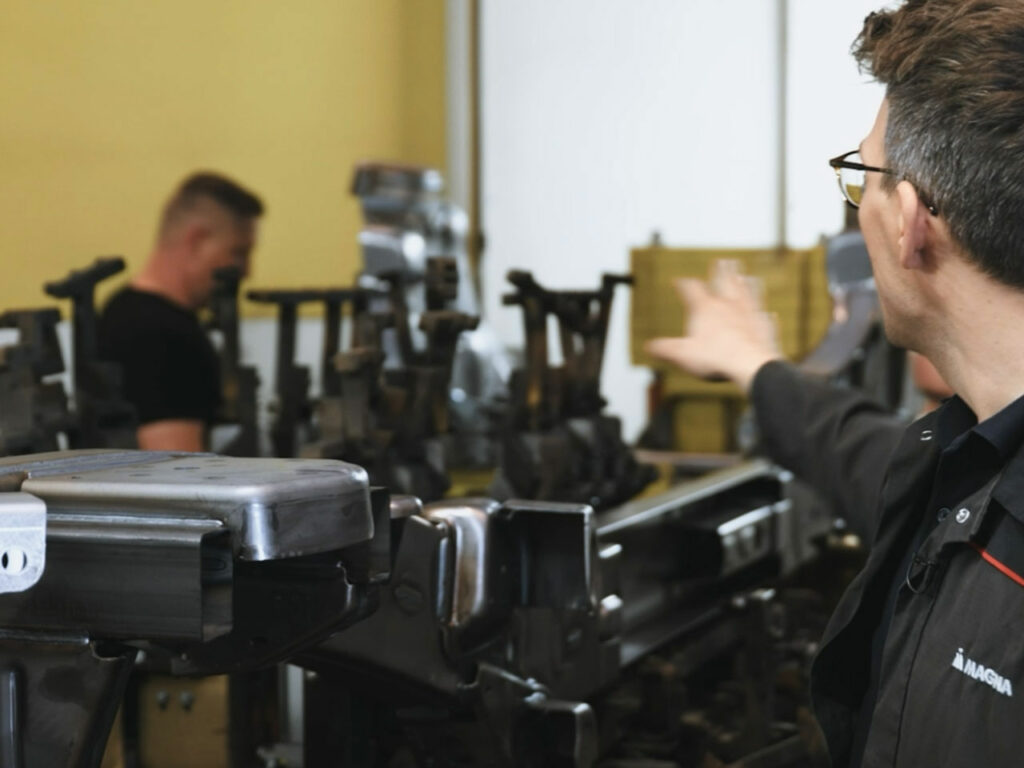
Soldadura de la subestructura:
“En la subestructura, la última etapa del proceso de producción, se unen las partes delantera y trasera. El bastidor adquiere su forma distintiva“, continúa Hartmann. Los últimos pasos consisten en perforar los puntos de unión para el chasis que no estén acoplados. Además, se disparan 192 pernos en el bastidor mediante ignición de arco. A continuación, un soldador formado comprueba la calidad de los cordones de soldadura, elimina las últimas proyecciones y retoca los cordones si es necesario.
Para garantizar la máxima calidad, el bastidor se mide en su totalidad con tecnología de medición láser robotizada. Una vez que el bastidor se ha revisado por última vez, sale del taller de carrocería a través de un sistema Power&Free (cinta transportadora) y sigue su camino en el proceso de producción.
Monitorización de los datos de soldadura con WeldCube Premium para garantizar la calidad:
No obstante, un excelente proceso de soldadura no es suficiente para que Magna Presstec pueda cumplir los enormes estándares de calidad del modelo G. También se requiere un sistema que sustituya los “ojos” que faltan en los 100 metros de longitud de la línea de producción, es decir, es necesario poder monitorizar y documentar completamente el proceso de soldadura.
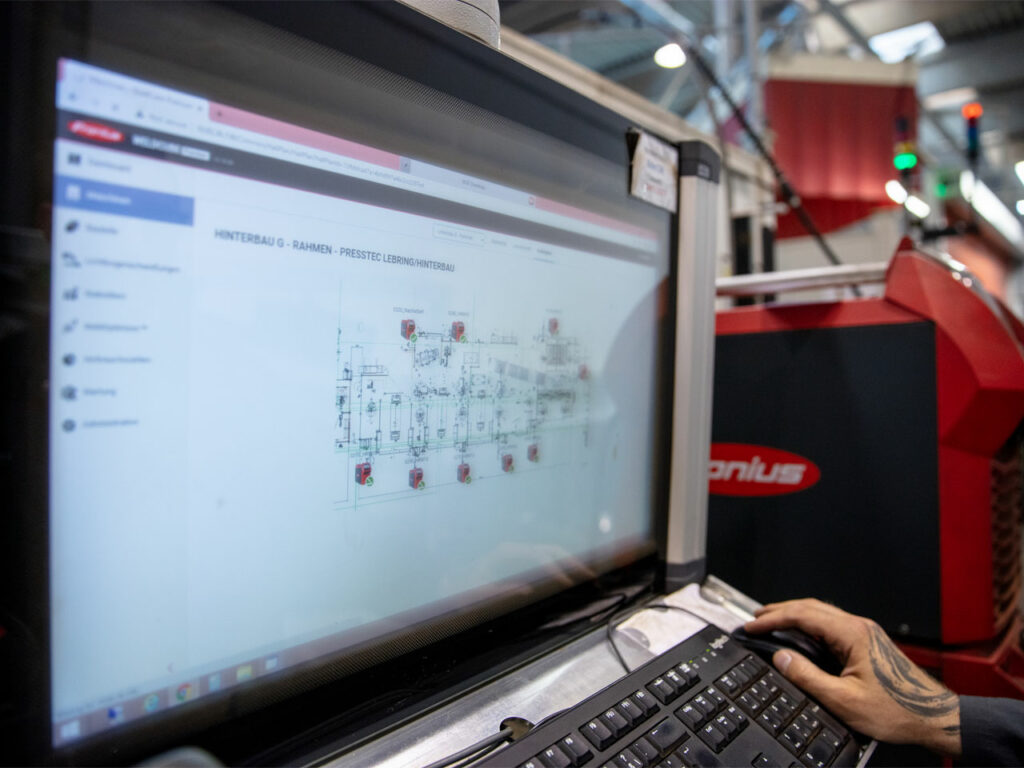
WeldCube Premium
“En la nave de producción, el software WeldCube Premium es un pilar esencial de nuestra gestión de calidad“, afirma Hartmann convencido. “La trazabilidad total de cada cordón de soldadura es sumamente importante para nosotros. En los puestos de control de calidad, los empleados formados reciben información precisa a través de un terminal: ¿hay cordones llamativos o defectuosos?
A través de WeldCube, es decir, según los datos de soldadura, se muestra dónde se encuentran los posibles defectos, que se someten a una detallada inspección visual y, si es necesario, se retrabajan. Solo entonces se permite que el bastidor G pase a los siguientes pasos del proceso“. Los datos recogidos contribuyen a la optimización de los procesos de soldadura automatizados.
De la monitorización al mantenimiento predictivo gracias a WeldCube
“Como WeldCube Premium registra sin excepción cada milímetro de los cordones de soldadura, podemos utilizar las herramientas de análisis para calcular fácilmente los costes de los materiales de consumo, como el gas y el hilo de soldadura. Sin embargo, podemos sacarle mucho más partido. El mantenimiento predictivo ofrece la posibilidad de pedir los consumibles y los materiales a tiempo y en cantidades suficientes“, señala Hartmann.
“El mantenimiento predictivo con WeldCube Premium tiene un enorme potencial de ahorro, por ejemplo, si la gestión de los datos de soldadura permite fijar intervalos de mantenimiento precisos. De este modo, podemos conocer siempre el estado de los tubos de contacto y sus codos, las antorchas y los alimentadores. Esto nos permitiría realizar el mantenimiento de los equipos en el momento oportuno, lo que a su vez evitaría cordones de soldadura defectuosos, retrabajos o incluso desechos de componentes“.
Para documentar tareas especiales: ¡solo especialistas!
La documentación y el análisis de los datos de soldadura no son suficientes para Magna Presstec: “Ya utilizamos la solución de software Central User Management (CENTRUM), que contribuye a gestionar la calidad. Esto nos permite conceder autorizaciones de usuario y de soldadura controladas de forma centralizada. Los soldadores deben autentificarse mediante una tarjeta inteligente en el sistema de soldadura. De este modo, nos aseguramos de que solamente los empleados formados para tareas específicas trabajen en el lugar adecuado con los parámetros previstos. Así, eliminamos en la medida de lo posible otras fuentes de error“, afirma Hartmann convencido.
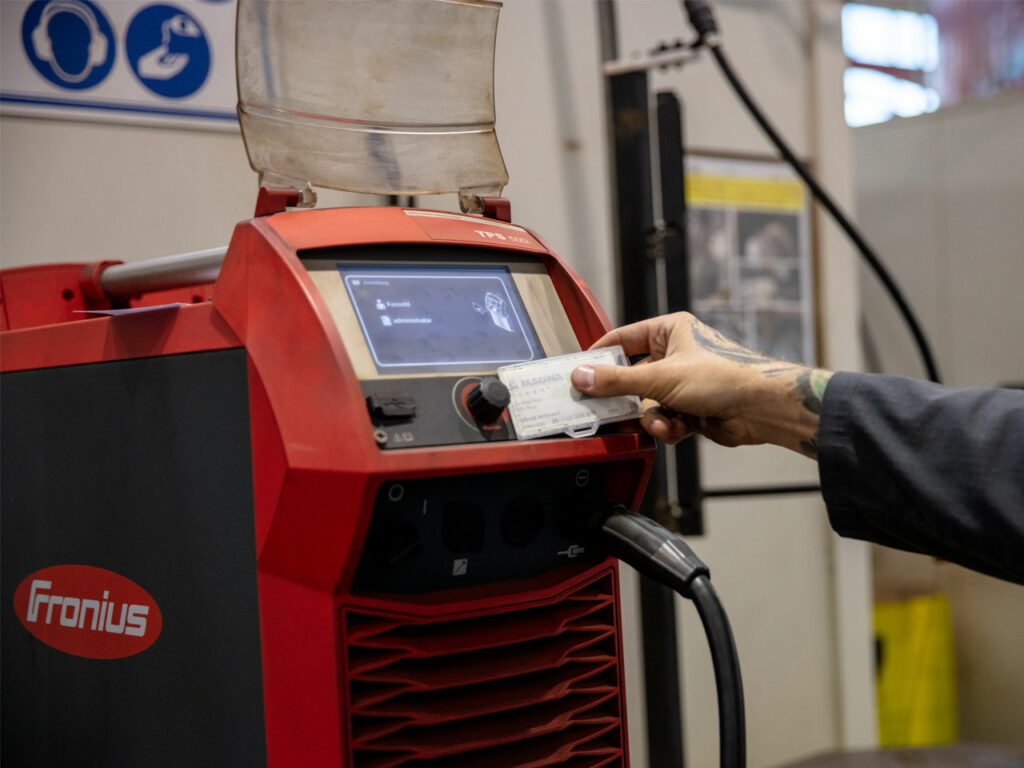
Soluciones para la documentación de los datos de soldadura en Fronius
Fronius desarrolla todas las soluciones de software que se utilizan en Magna Presstec. Si bien, hay que mencionar que todos los productos, desde WeldCube Premium hasta Central User Management, se han desarrollado gracias a un intenso intercambio de información con Magna Presstec, que ha llevado a cabo pruebas de larga duración de los prototipos durante el proceso de producción, lo que ha permitido obtener la información necesaria para que los productos estén listos para lanzarse al mercado.
Echa un vistazo a nuestro breve documental sobre la producción del bastidor del Mercedes G por el proveedor de primer nivel Magna Presstec:
Si estás interesado en nuestras soluciones orientadas al futuro para facilitar la producción automatizada, puedes encontrar más información sobre nuestros productos haciendo clic aquí.
No hay comentarios