O que um dos veículos mais completos do mundo para offroad tem a ver com a documentação dos dados de soldagem? A enorme distância ao solo e a enorme profundidade de travessia de água do Mercedes G sugerem imediatamente uma coisa: o veículo deve ser capaz de suportar as mais rìgidas condições de offroad. Tração e durabilidade devem ser sempre garantidas. Quando o Classe G é submetido a fortes impactos em alta velocidade em terreno acidentado, também significa uma tensão elevada constante em todas as costuras de solda. É por isso que a garantia de qualidade e a otimização dos processos de produção com base em um sistema sofisticado de gerenciamento de dados de soldagem são tão cruciais.
Produção do chassi do Classe G da Mercedes na Magna Presstec
Os mais altos padrões de qualidade para o Classe G, exigidos pelos fabricantes e consumidores finais, também se refletem na demanda: o interesse pelo offroad de luxo está aumentando constantemente. Para poder atender às quantidades exigidas, é necessário um alto grau de automação na produção do chassi.
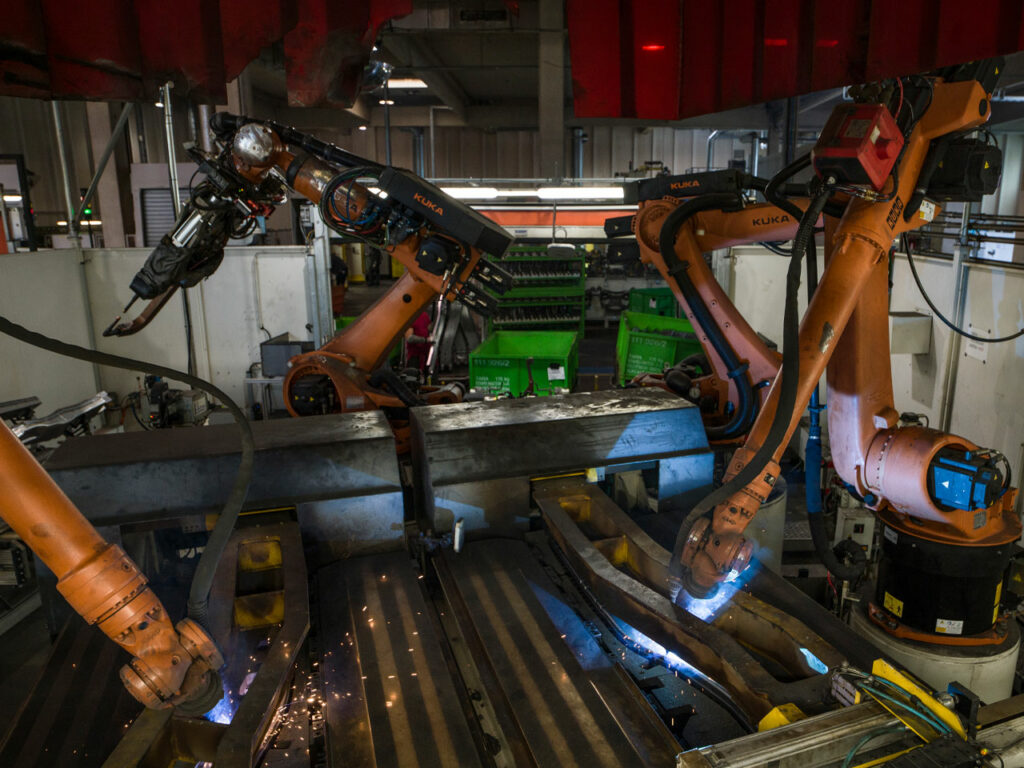
A linha de produção de alta tecnologia do fornecedor de primeiro escalão Magna Presstec em Lebring, no sul da Áustria, tem tudo isso: em um comprimento de 100 metros, os sistemas e os robôs de solda interagem perfeitamente. Um processo de soldagem por impulso extremamente rápido, preciso e controlado digitalmente (PMC da Fronius) atende às altas exigências no que diz respeito à tecnologia de soldagem fundamentalmente necessária.
A linha de produção é abastecida com peças individuais apenas no início. A cada 10 minutos, sai da oficina um chassi do Mercedes Classe G pronto e suspenso na ponte rolante como se fosse mágica.
Extremamente complexa: pico de produção autônoma em detalhes
“Nossa exigência é que cada estrutura seja absolutamente idêntica, os desvios devem ser descartados”, explica Kurt Hartmann, gerente de produção e supervisor de soldagem da Magna Presstec.
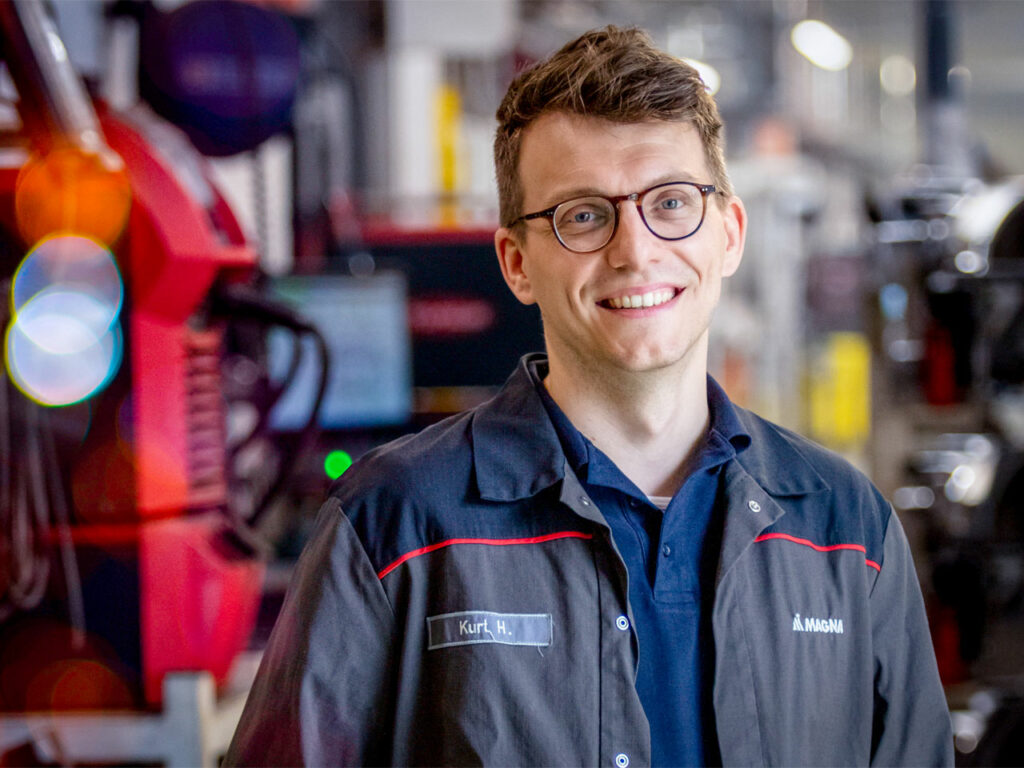
Dianteira e traseira:“Aqui fabricamos em três seções”, detalha Hartmann. “A parte dianteira e traseira (da estrutura), ou seja, as duas primeiras seções da linha de produção, são produzidas simultaneamente. No início, alguns funcionários equipavam as fontes de solda.
Nas células, os componentes são então unidos por robôs de solda. Um robô de manipulação pega os componentes acabados, transporta-os para a próxima célula e os posiciona. No final de cada seção há uma célula inacessível para os funcionários. Ela serve para fazer as costuras de solda longas. Mas as células também são usadas como estação de resfriamento ou como estação complexa, como para apertar: aqui as chapas inferiores são encaixadas com as chapas superiores das longarinas, posicionadas e soldadas sob pressão.”
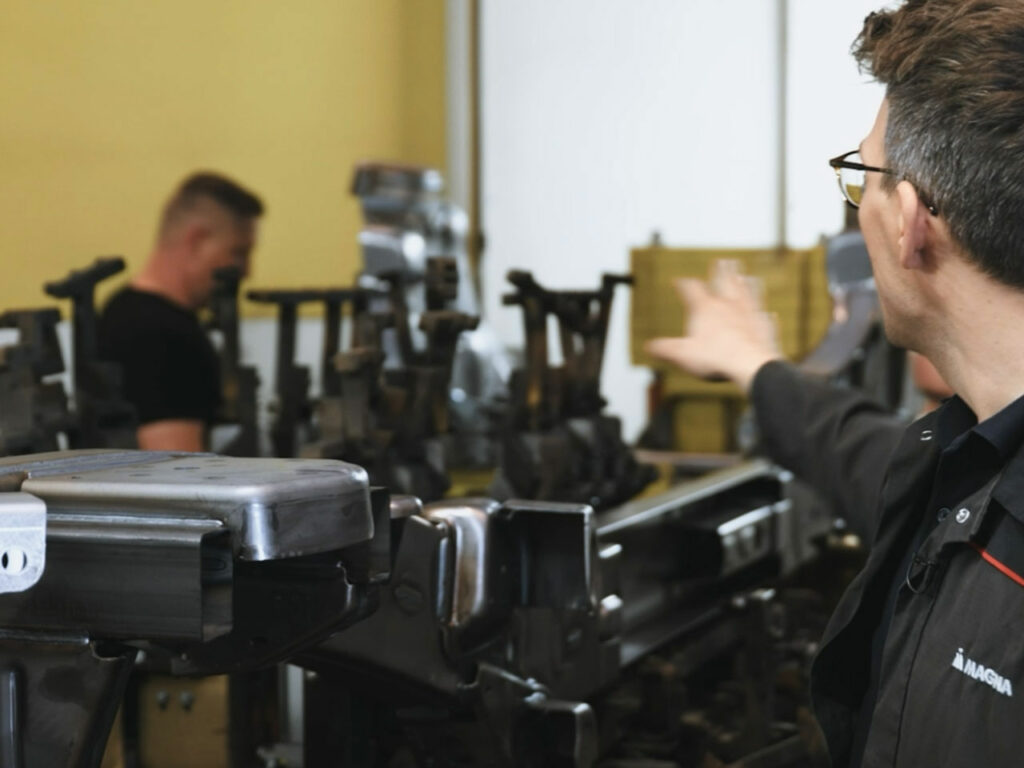
Estrutura inferior:“Na estrutura inferior, a última etapa da produção, as estruturas dianteira e traseira são combinadas. O chassi assume sua forma distinta”, prossegue Hartmann. As etapas finais de trabalho envolvem então a perfuração de pontos de conexão desacoplados para o mecanismo de traslado. Além disso, 192 parafusos são disparados na estrutura por meio de ignição por arco elétrico. Um soldador treinado verifica então a qualidade dos cordões de solda, remove os últimos respingos de solda e refaz as costuras, se necessário.
Para garantia total da qualidade, a estrutura é então medida por completo usando tecnologia de medição a laser controlada por robô. Depois de inspecionado pela última vez, o quadro sai da construção através de um sistema Power&Free (esteira transportadora). O quadro é então transferido para outras etapas do processo.
Para garantia de qualidade: monitoramento dos dados de soldagem usando WeldCube Premium
Mas um processo de soldagem excepcional por si só não é suficiente para que a Magna Presstec atenda às enormes exigências de qualidade do Classe G. É necessário um sistema que substitua os “olhos” ausentes ao longo dos 100 metros da produção, ou seja, a possibilidade de 100% de monitoramento e documentação completa do processo de soldagem.
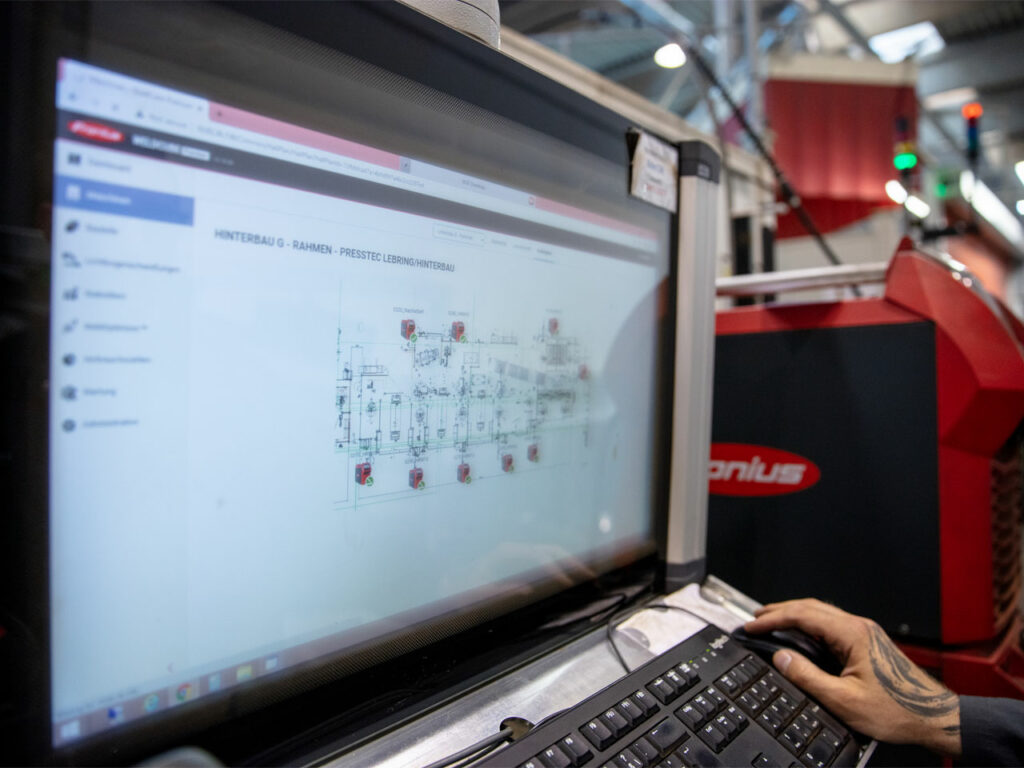
“Na área de produção, o software WeldCube Premium é um pilar essencial da nossa gestão de qualidade”,diz Hartmann com convicção.“A rastreabilidade absoluta de cada solda é intrinsecamente importante para nós. Nas estações de controle de qualidade, os funcionários treinados recebem as informações mais precisas via terminal: há costuras visíveis ou há de fato costuras defeituosas?
Com o WeldCube, e com base nos processos de soldagem, possíveis pontos defeituosos são apontados, submetidos a uma inspeção visual detalhada e, se necessário, retrabalhados. Somente então o quadro do Classe G é liberado para outras etapas do processo. “Os dados coletados ajudam na otimização dos processos automatizados desoldagem.
Do monitoramento à manutenção preventiva
“Como o WeldCube Premium registra cada milímetro de solda sem exceção, podemos usar as ferramentas de análise para calcular de modo prático os custos de consumo, como gás e arame de soldagem. Mas vemos aqui muito mais potencial: um ponto certamente seria a Predictive Maintenance (manutenção preventiva) ou a possibilidade de encomendar peças e materiais de desgaste em tempo hábil e em quantidades suficientes”, Hartmann delineia perspectivas claras para o futuro.
“A manutenção preventiva com WeldCube Premium também pode nos oferecer um enorme potencial de economia, por exemplo, se o sistema de gerenciamento de dados de soldagem especificar intervalos de manutenção precisos. Sempre sabemos exatamente qual é a condição dos tubos de contato, tubos curvados, tochas de solda e alimentadores. Desta forma, podemos reparar os dispositivos em tempo hábil para evitar soldas defeituosas, retrabalho ou até mesmo rejeições de componentes.”
Para tarefas especiais: apenas especialistas!
No entanto, a documentação e análise dos dados de soldagem não é suficiente para a Magna Presstec: “Além disso, já estamos usando a solução de software Central User Management (CENTRUM) que também nos apoia na gestão da qualidade. Com ela,concedemos autorizações de usuário e de soldagem de modo controlado e centralizado. Desta forma, podemos garantir que somente funcionários treinados para tarefas específicas estejam trabalhando no local certo com os parâmetros de soldagem previstos para isso. E descartamos outras fontes de erro da melhor maneira possível”, conta Hartmann.
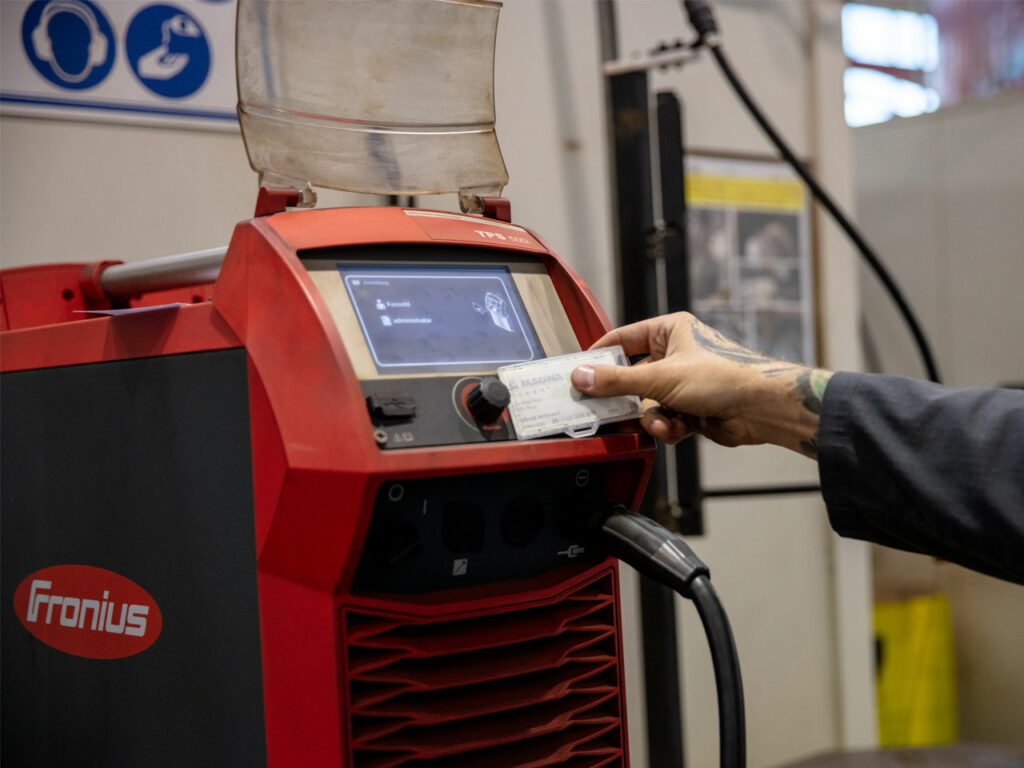
Soluções da Fronius para a documentação dos dados de soldagem
As soluções de software utilizadas pela Magna Presstec foram todas desenvolvidas pela Fronius. No entanto, desde o WeldCube Premium até o Central User Management todos os produtos foram criados em estreita cooperação com a Magna Presstec: somente foi possível obter as informações necessárias e atingir a maturidade do mercado graças aos testes de longo prazo dos protótipos na produção da Magna.
Veja agora mesmo o nosso breve documentário sobre a produção de chassis do Mercedes Classe G no fornecedor de primeiro escalão Magna Presstec:
Caso também tenha interesse em nossas soluções orientadas para o futuro para apoiar a produção autônoma, fornecemos aqui mais informações sobre o produto.
Nenhum comentário