Es liegt auf der Hand, warum die Zahl der Metallbau-Unternehmen, die auf 3D-Druck setzen – im Branchenjargon simpel WAAM (Wire Arc Additive Manufacturing) genannt –, im Steigen ist: Den vielfältigen Individualisierungsmöglichkeiten von modernen Produktionsanlagen folgt der Wunsch nach maßgeschneiderten Einzellösungen auf dem Fuß. Immer wieder benötigen wir vom Standard abweichende Ersatzteile binnen kürzester Zeit. Und im Prototypenbau wollen wir nicht nur Werkzeugkosten einsparen, sondern auch Entwicklungszeiten verkürzen. Bei all diesen Anforderungen spielt die additive Fertigung ihre großen Stärken aus. Bauteilgeometrien, die gestern noch unmöglich schienen, werden heute mit Metall-3D-Druck Schicht für Schicht real, und zwar genau dann, wenn wir sie brauchen.
WAAM – weniger Material, weniger Gewicht, weniger Kosten
Vergleichen wir den Metall-3D-Druck mit zerspanenden Prozessen wie dem Fräsen, fällt auf, dass Wire Arc Additive Manufacturing bedeutend weniger Werkstoff verbraucht. Je höher die Rohstoffpreise ausfallen, desto schneller rentiert sich diese Art der additiven Fertigung.
Aufwändig hergestellte Formen, wie wir sie beim Gießen benötigen, werden ebenfalls nicht gebraucht. Stattdessen können wir mit moderner Schweißtechnologie komplexe, Topologie optimierte Metallbauteile schichtweise nach Rezept fertigen. Im Fachjargon nennt man so eine Anleitung Additive Manufacturing Procedure Specification (AMPS). Eine AMPS enthält alles, was wir für den perfekten „Printprozess“ benötigen: die einzelnen Schweißanweisungen (Deposition Procedure Specifications, kurz DPS), die Bediener- und Materialzertifikate sowie die kinematische Strategie, die wir für die Pfadplanung und Bewegungssteuerung des Schweißroboters brauchen.
Materialzertifikate garantieren die produktionsgerechte Qualität von Schweißdrähten. Bedienerzertifikate stellen sicher, dass die in der additiven Fertigung üblichen DED-Arc-Roboterschweißzellen nur von fachkundigen Spezialisten bedient werden. DED-Arc steht für Directed Energy Deposition Arc, das ist ein Lichtbogen zum schichtweisen Abschmelzen von Schweißdraht.
„Bei der Topologie-Optimierung wollen wir die ideale Materialverteilung von Bauteilen sicherstellen. Genau genommen soll das Gewicht bei gleichzeitigem Erhalt der Steifigkeit reduziert werden“, erklärt Metall-3D-Druck-Experte Philipp Roithinger und fährt fort: „Typische Anwendungen sind bionische, der Natur entliehene Strukturen, wie wir sie zum Beispiel im Aerospace-Bereich vorfinden. Ein anderer Vorteil des Metall-3D-Drucks ist die dezentrale Fertigungsmöglichkeit. Ortsunabhängig benötigt man keine Produktionsstraßen wie bei der Serienfertigung. Speziell ausgestattete Roboterschweißzellen, die weltweit flexibel zum Einsatz gebracht werden können, kennzeichnen die additive Fertigung mit Schweißdraht. Überall dort, wo wir im Metallbau Gewicht, Material, Kosten und die Umweltbelastung reduzieren wollen, setzen wir heute verstärkt auf den Metall-3D-Druck.“
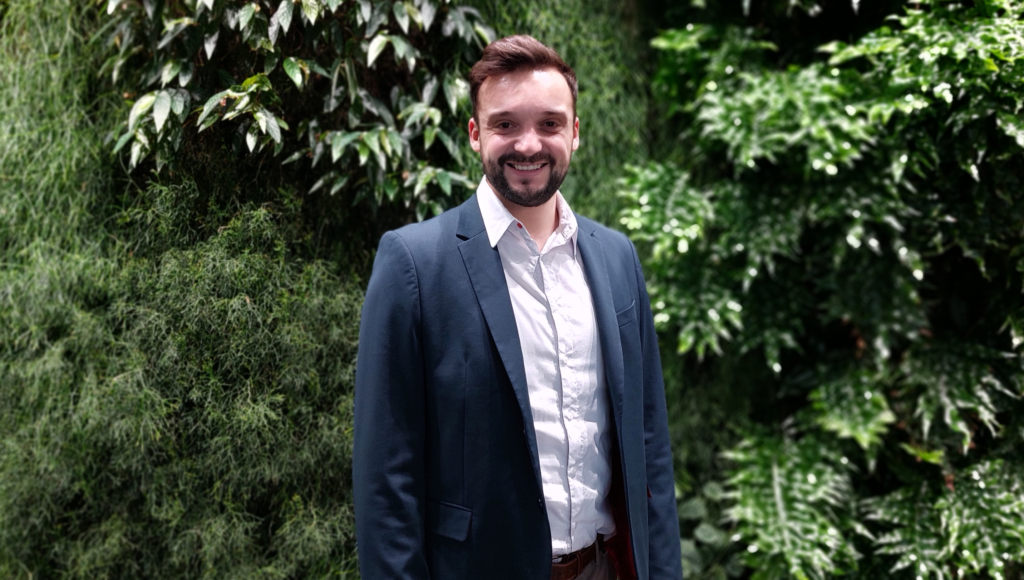
Beim Metall-3D-Druck unverzichtbar: ein stabiler Lichtbogen wie bei CMT
Damit wir die gewünschte Qualität erreichen, benötigen wir beim additiven Schweißen einen enorm stabilen Schweißprozess wie zum Beispiel CMT (Cold Metal Transfer). CMT ist ein „kühler“ Kurzlichtbogenprozess, der trotz seiner hohen Abschmelzleistung den Wärmeeintrag gering hält. Das funktioniert deshalb, weil die Tropfenablösung von einer reversierenden Drahtelektrodenbewegung ausgelöst wird.
Beim konventionellen, für WAAM wenig geeigneten Kurzlichtbogenprozess, der einen höheren Wärmeeintrag erzeugt, bewegt sich der Draht – anders als bei CMT – kontinuierlich zum Werkstück. Sobald das erweichte Drahtende das Schmelzbad berührt, entsteht ein Kurzschluss. Ein Großteil des flüssigen Schweißdrahtes fließt in das Schmelzbad – die sogenannte Tropfenablösung erfolgt. In der Kurzschlussphase strebt die Schweißspannung gegen Null, während der Strom auf einen hohen Wert ansteigt, der Kurzschluss aufgebrochen und der Lichtbogen erneut gezündet wird.
Tropfenablösung und Wiederentzünden des Lichtbogens erfolgen beim CMT-Prozess kontrollierter und mit weniger Energieeintrag als beim Kurzlichtbogen – nämlich durch eine Rückwärtsbewegung der Drahtelektrode in der Kurzschlussphase. Je nach Kennlinie für Zusatzwerkstoff, Schutzgas und Elektrodendurchmesser findet die reversierende Drahtbewegung in einem Frequenzbereich von 50 bis 170 Hz statt.
Der beim CMT-Schweißen entstehende Wärmeeintrag ist um bis zu 33 % geringer als beim herkömmlichen Kurzlichtbogen. Deshalb eignet sich dieser Prozess hervorragend für das additive Schweißen, wo das zyklische Auftragen von Schweißraupen eine hohe Wärmeeinbringung verursacht. Ist die Bauteiltemperatur zu hoch, mindert das die Werkstoffeigenschaften und führt zu Wartezeiten. In so einem Fall müsste der Schweißvorgang bis zum Abkühlen der Schweißlagen unterbrochen werden. Schwankungen des Kontaktrohrabstands sind bei CMT wenig kritisch, der Lichtbogen bleibt stabil und infolge des Ein-Draht-Systems ist ein zusätzlicher Freiheitsgrad bei der Roboterprogrammierung gegeben.
CMT Additive Pro: gezielter Wärmeeintrag für einen konstanten Lagenaufbau
Der CMT-Prozess unterstützt Funktionen, die speziell für den Metall-3D-Druck geeignet sind, zum Beispiel die „Leistungskorrektur“. Sie bewirkt, dass die elektrisch aufgewendete Leistung präzise an die jeweilige Prozessphase – an Lagenaufbau und Wärmeeintrag – angepasst werden kann. Die Abschmelzleistung bleibt dabei konstant.
„Mit unseren speziell für die additive Fertigung entwickelten CMT-Additive-Pro-Funktionen wie der Leistungskorrektur oder dem Deposition Stabilizer können wir den Leistungseintrag und somit die Höhe und Breite der Schweißnaht gezielt steuern“, führt Roithinger weiter aus.
Muss während des Lagenaufbaus – bedingt durch den Austausch leerer Drahtfässer – ein neuerlicher Schweißstart erfolgen, kann das eine nicht zu unterschätzende Fehlerquelle darstellen. Daraus resultierende Bindefehler oder Nahtüberhöhungen im Schweißstartbereich würden die Qualität von additiv gefertigten Bauteilen massiv beeinträchtigen. Hier schafft die Pulsed-Hot-Start-Funktion Abhilfe. Ist sie aktiv, wird beim erneuten Schweißstart im Impulslichtbogen so viel Einbrand wie nötig erzielt und die Lagenhöhe konstant gehalten.
360°-Service im Fronius Prototypenzentrum
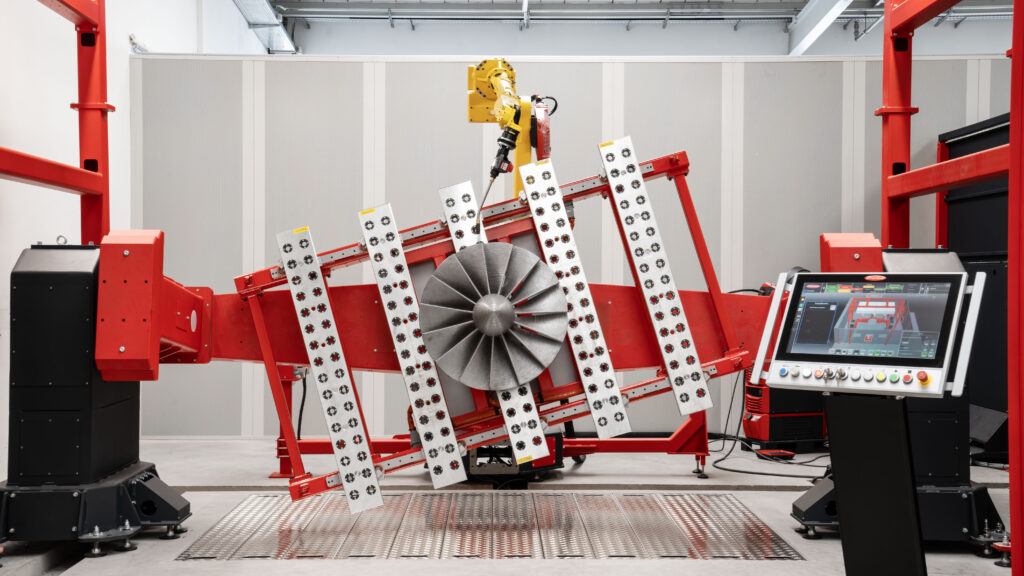
Im Prototypenzentrum am Standort Wels, Österreich, stellen wir ein breit gefächertes Dienstleistungspaket zur Verfügung. Es beinhaltet Machbarkeitsstudien, maßgeschneiderte Lösungen für individuelle Kundenanforderungen, Prozessoptimierung und Prototypenfertigung – abgestimmt mit unseren Auftraggebern und streng vertraulich. Im Prototypenbau wollen wir die Zeitspanne von der Entwicklung bis zur Produktreife so kurz wie möglich halten. Dafür schöpfen wir unser volles schweißtechnologisches Potenzial aus.
Wenn nötig, unterstützen unsere Expertinnen und Experten nicht nur beim Prototypenbau, sondern auch bei der Vorserienfertigung. Sie helfen beim reibungslosen Einstieg in den robotergestützten Metall-3D-Druck und geben valide Empfehlungen zu Schweißprozess, Wirtschaftlichkeit, Qualität und Produktion. Im rund 900 m² großen Prototypenzentrum stehen Robotersysteme mit fortschrittlicher Schweiß-, Sensor- und Vermessungstechnologie zur Verfügung. Ebenso vorhanden ist ein Schweißlabor, wo zerstörungsfreie und zerstörende Bauteilprüfungen durchgeführt werden können. Unser Full-Service-Paket umfasst Offline-Programmierung, Simulationen, metallurgische Untersuchungen, 3D-Bauteilvermessung, Schweißdatendokumentation und vieles mehr.
Neue Normen für den Metall-3D-Druck
Mittlerweile entstehen in unterschiedlichen Branchen erste Normen für die lichtbogenbasierte additive Fertigung. Gemeinsam mit Linde Engineering, das den Anwendungsfall zur Verfügung gestellt hat, dem Drahthersteller Migal.co und TÜV Süd Deutschland haben wir bei Fronius an der Musterqualifizierung eines additiv gefertigten Druckbehälters in der Form eines Rohrabzweigs mitgewirkt. Überprüft worden ist die Anwendbarkeit des Normentwurfs preEN 13445-14 für den Einsatz von additiv gefertigten Druckbehältern.
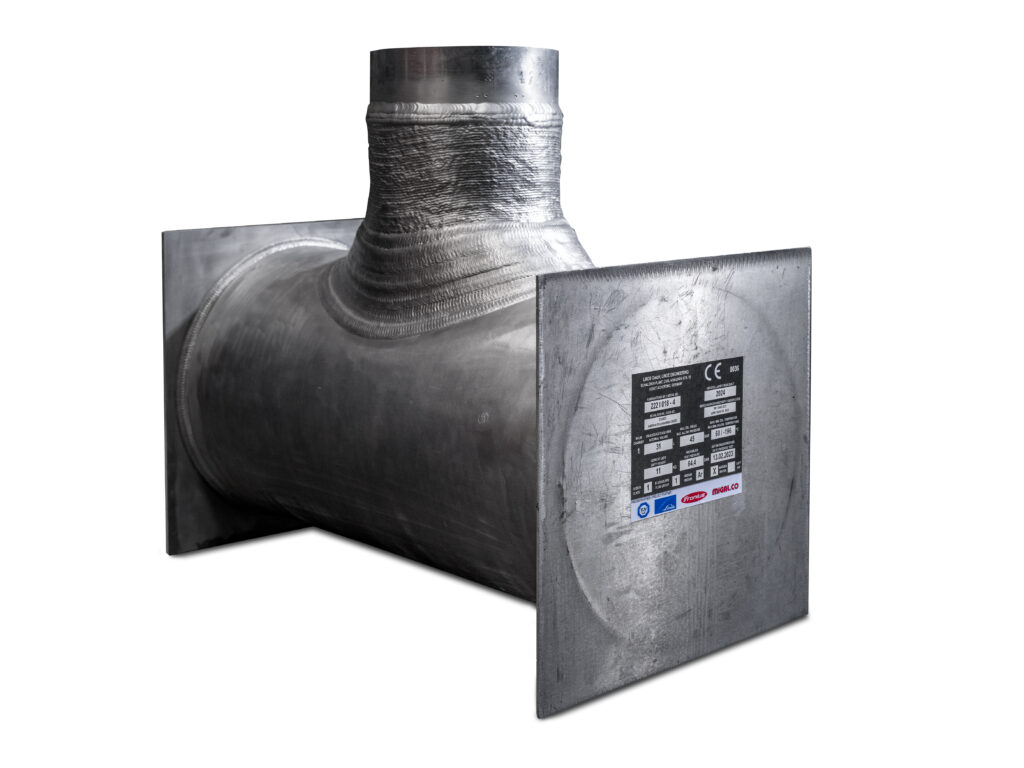
Beim Metall-3D-Druck ist die Qualität der verwendeten Werkstoffe entscheidend. Im konkreten Fall hat man sich für eine naturharte Aluminium-Knetlegierung entschieden. Wegen seiner hervorragenden Tieftemperaturzähigkeit von bis zu –273 °C eignet sich dieser Werkstoff, der auch im Leichtbau verwendet wird, besonders gut für den Bau von Rohrleitungsanlagen.
Im oben erwähnten europäischen Normentwurf wird die gesamte Wertschöpfungskette für die additive Fertigung inklusive aller notwendigen Überwachungsdetails betrachtet. Auf diese Weise will man sicherstellen, dass die grundlegenden Sicherheitsanforderungen, die in der Druckgeräterichtlinie definiert sind, sauber erfüllt werden.
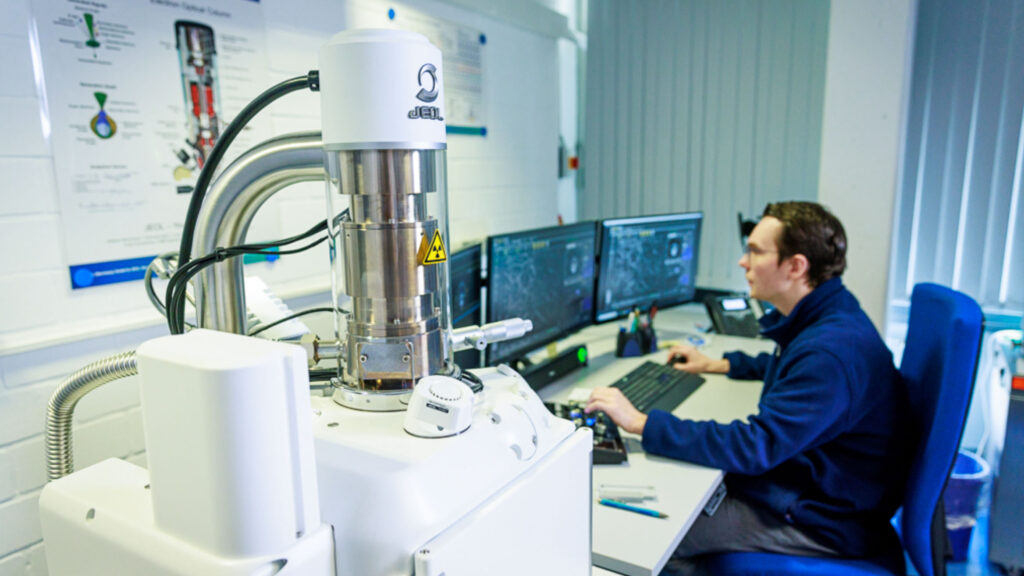
Während der Musterqualifizierung haben wir die gesamte Prozesskette von der Auslegung über die Konstruktion, die Fertigung und Bahnplanung, die Prozessüberwachung bis hin zur abschließenden Druckprüfung überprüft und dokumentiert.
Detaillierte Informationen zur Musterqualifikation des Druckbehälters mit abschließender CE-Zertifizierung durch den TÜV-Süd bietet dieses Video: YouTube
Keine Kommentare