Co należy zrobić, gdy w procesie produkcji wykorzystującym spawanie wymagane jest wytworzenie wielu tych samych elementów? Rozwiązaniem są zrobotyzowane cele spawalnicze. Wymagania dotyczące wykonania takich stanowisk spawalniczych są jednak ogromne: elementy o różnym kształcie, masie i wymiarach wymagają specjalnych rozwiązań.
Podstawowe zadania zrobotyzowanych stanowisk spawalniczych (inaczej nazywanych zrobotyzowanymi celami spawalniczymi) powtarzają się jednak nieustannie, niezależnie od elementu. Do stałego repertuaru należy na przykład pozycjonowanie elementu, wymiana końcówki prądowej lub czyszczenie uchwytu spawalniczego. Dlatego projektanci nie muszą ciągle wymyślać wszystkiego od nowa. W przypadku koncepcji nowoczesnych zrobotyzowanych cel spawalniczych sięgają oni po kombinację dostępnych rozwiązań modułowych – co pomaga też spełnić cele związane ze zrównoważonym rozwojem. Wszystko, czego trzeba specjalistom, aby to osiągnąć, to odpowiednia platforma. Jest to system modułowy złożony ze standardowych i specjalnych podzespołów.
Wydajne oprogramowanie projektowe
Przy projektowaniu zrobotyzowanych cel spawalniczych wykorzystuje się potężne oprogramowanie. Zawiera ono rozbudowane biblioteki złożone ze standardowych modułów do wszystkich systemów peryferyjnych robota. Projektanci nie muszą więc za każdym razem na nowo projektować standardowych elementów takich jak tory jezdne robota, stojaki lub stoły obrotowe. Mogą oni raczej skupić się na spełnieniu głównych wymagań klienta: Na przykład na zaprojektowaniu odpowiedniego urządzenia mocującego lub ustaleniu prawidłowej kolejności spawania w celu uniknięcia wypaczenia elementu. Kolejną zaletą systemów modułowych jest ich wysoka rentowność. Mniejszy nakład na projektowanie obniża koszty, a tym samym ceny i wymagania dotyczące finansowania dla klientów.
Widok 3D zrobotyzowanej celi spawalniczej wraz z elementem, budowa pojazdu szynowego
Moduły i ich funkcje
Moduły spełniają zatem indywidualne wymagania klientów, a tym samym pełnią ważne funkcje w zrobotyzowanym systemie spawania. Te moduły dzielą się na zespoły, podzespoły i komponenty. Mogą one być prefabrykowane z myślą o przyszłych zastosowaniach: w sposób wirtualny (biblioteka oprogramowania projektowego) i w sposób fizyczny (potrzeby produkcyjne zrobotyzowanych stanowisk spawalniczych).
Przykładowe moduły cel spawalniczych
/ moduł spawania (źródła energii, podajnik drutu, uchwyt spawalniczy…)
Źródło energii z chłodzeniem i podajnik drutu
/ moduł pozycjonowania elementu (urządzenie pozycjonujące, robot manipulacyjny, tor jezdny, wysięgnik, stojak…)
Robot manipulacyjny z ramieniem chwytaka Stół obrotowo-przechylny
/ moduł pozycjonowania robota (oś liniowa, portal wysięgnikowy…)
Robot na torze (oś liniowa)
/ moduł podawania elementu (śluza, przenośnik taśmowy…)
Elementu śluza
/ moduł bezpieczeństwa (ogrodzenie ochronne, kurtyna świetlna, zapora świetlna, kurtyna rolowana…)
Zrobotyzowana cela spawalnicza z fotokomórką wykorzystującą podczerwień
/ moduł pozycjonowania uchwytu spawalniczego (robot)
Spawalnik „teacht” robotów i uchwyt spawalniczy
/ moduł sterowania systemem (szafa sterownicza, interfejs HMI sterowania systemowego)
Intuicyjne sterowanie systemem z wizualizacją 3D w czasie rzeczywistym
Funkcje modułów można rozszerzyć poprzez różne opcje, np. okienka kontrolne, zwijacz kabla do urządzenia zdalnego sterowania, zabezpieczenie przed oślepieniem.
Spawanie zrobotyzowane i wymiarowanie
Precyzja i powtarzalność podczas spawania są głównymi zaletami spawania zrobotyzowanego. Aby obok wysokiej jakości spoin zapewnić również elastyczność w zakresie elementów oraz kolejności spawania, należy uwzględnić podczas planowania perspektywiczną konstrukcję, zasięg i udźwig:
Jeżeli małe powierzchnie ustawienia są połączone z wąskimi ramionami robota i dużym zasięgiem, możliwe jest spawanie również w ciasnych przestrzeniach. Typowymi przykładami są osie, uchwyty, fotele, układy wydechowe, elementy podwozia, nadbudowy dźwigów, elementy zbiorników i przewodów rurowych.
Jeżeli stosowany jest ciężki uchwyt spawalniczy, np. w przypadku punktowego zgrzewania oporowego lub hybrydowego spawania laserowego, wymagany jest robot o dużym udźwigu.
Smukłe ramię robota z dużym zasięgiem i długim wygięciem rury Szerokie, krótkie ramię robota z drążonym wałem
Zapobieganie problemom z kablami
Przegubowe osie robotów z ramionami drążonymi umożliwiają prowadzenie przewodów sterowniczych, czujników i zasilających wewnątrz osi. Dzięki temu podczas wykonywania złożonych ruchów zapobiega się owinięciu połączonych w wiązki przewodów wokół przednich osi robota. Kolejna zaleta wersji z ramieniem drążonym: potencjalne problemy z kablami można symulować za pomocą oprogramowania.
Ramię przegubowe robota z ramieniem drążonym
Wszystko pod kontrolą
Wszystkie moduły zrobotyzowanego stanowiska spawalniczego muszą precyzyjnie ze sobą współdziałać w celu zapewnienia zarówno idealnych wyników spawania, jak również bezpieczeństwa operatorów urządzenia. Z reguły jest to zapewnione przez centralne sterowanie systemowe. Steruje ono wszystkimi komponentami peryferyjnymi, takimi jak robot, źródło energii, urządzenie pozycjonujące, systemy regałowe, urządzenie do czyszczenia uchwytu spawalniczego lub fotokomórka, oraz je monitoruje.
Intuicyjne sterowanie systemem z wizualizacją 3D w czasie rzeczywistym
…
Edytory programu, kontrola danych spawania i zarządzanie użytkownikami
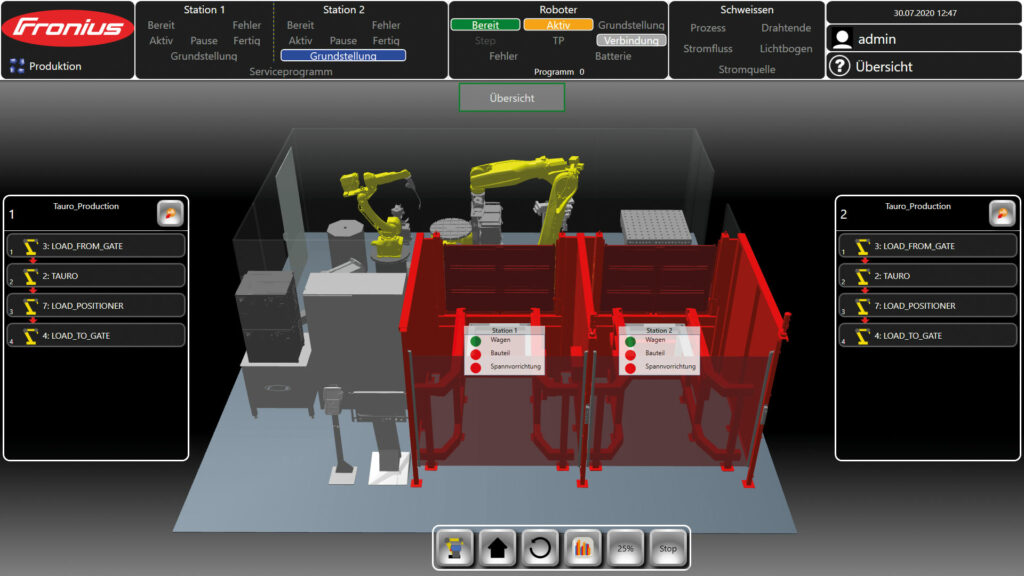
/ Nowoczesne, zaawansowane technologicznie sterowania systemowe wyróżniają się intuicyjnymi edytorami programu. Z ich pomocą technicy spawalnictwa określają krok po kroku niezbędne przebiegi programu i zapisują je jako łańcuchy kroków roboczych. Zostają one następnie przyporządkowane do poszczególnych stanowisk obróbki.
/ Trójwymiarowe obrazy wyświetlane na monitorze wizualizują w czasie rzeczywistym wszystkie ruchy robota oraz czynności spawalnicze. Zapewniają one szczegółowy przegląd stanu komponentów peryferyjnych i obszarów chronionych – i to w czasie rzeczywistym!
…
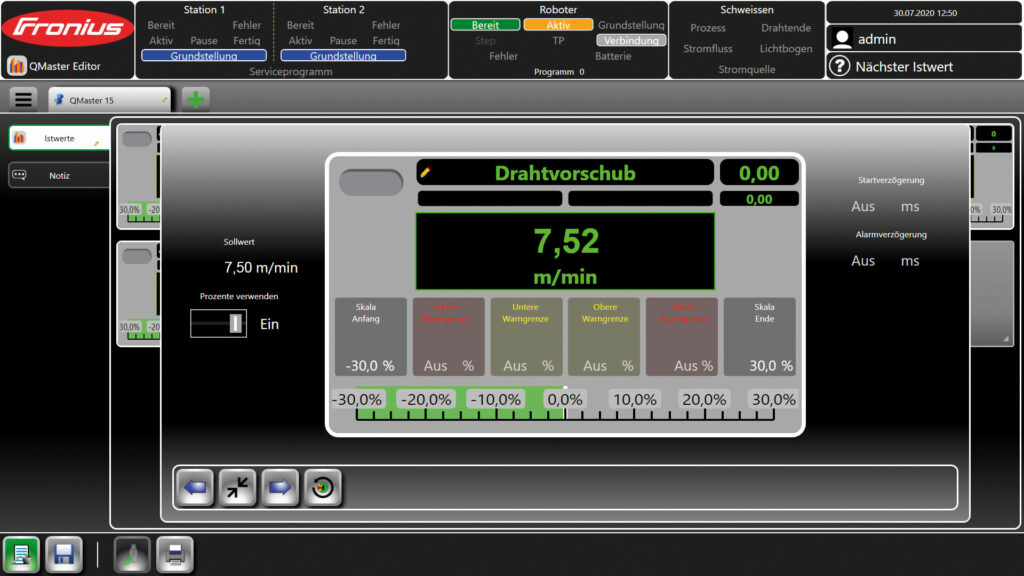
/ Funkcje kontrolne umożliwiają wybór granicznych wartości ostrzegawczych i granicznych wartości błędu. Można również ustawić opóźnienie uruchomienia i alarmu.
…
…
…
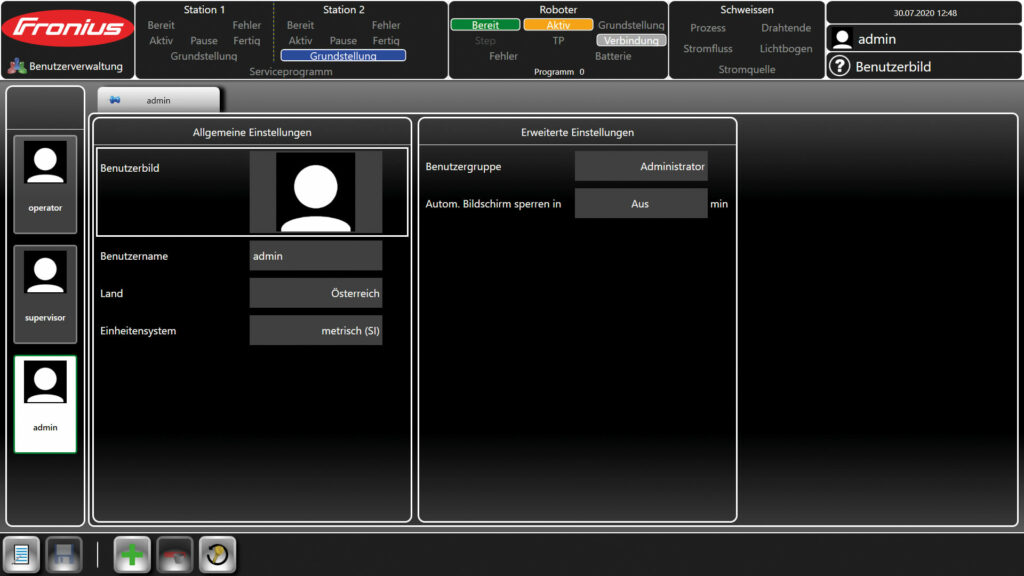
/ Za pomocą spersonalizowanego systemu zarządzania użytkownikami można tworzyć i edytować użytkowników oraz przydzielać im uprawnienia związane z zadaniem. Można ustawić w sposób indywidualny język obsługi i układ jednostek. Zapisane ustawienia są zabezpieczone osobistymi hasłami.
…
Standardowe funkcje
Wiele sterowań systemowych obejmuje standardowo zarządzanie użytkownikami i programem, różne wskazania usterek, liczniki cyklów i sztuk, wskazania stanu instalacji i zmianę języka. Często dostępne są interfejsy do popularnych systemów ERP i Web-API umożliwiające przesyłanie danych do innych systemów.
Programowanie offline: mniejsze koszty przestojów, większa wydajność
Wydajność prac spawalniczych jest miarodajnym wskaźnikiem rentowności procesów produkcyjnych. Ale jak można zwiększyć ten współczynnik? Jedną z możliwości jest programowanie przebiegów spawania offline – a więc bez połączenia ze zrobotyzowaną celą spawalniczą. Tym samym można z wyprzedzeniem zoptymalizować wszystkie szczegóły.
Programiści robotów nie muszą już więc czekać na zakończenie bieżących czynności spawalniczych. Zamiast tego mogą zaprogramować robota za pomocą komputera stacjonarnego lub laptopa poza instalacją, a następnie przeprowadzić symulację offline całego przebiegu spawania – spoina po spoinie.
Wydajne oprogramowanie programistyczne i symulacyjne online rozpoznaje ograniczenia osi, oblicza punkty startowe i położenia końcowe oraz drogi najazdu oraz niezależnie ustawia punkty położenia. Kontury zakłócające są wizualizowane, a dosunięcia uchwytu spawalniczego korygowane. Wszystko to dzieje się z wyprzedzeniem, a nie dopiero podczas prac spawalniczych.
Autonomia i bezpieczeństwo
Połączenie wszystkich modułów i układu sterowania cyfrową siecią umożliwia w pełni zautomatyzowane przebiegi i zapewnia w ten sposób wysoki stopień autonomii w przebiegu pracy zarówno w zakresie manipulowania elementami, jak i podczas spawania. Czynności ręczne nie są już konieczne, operator może skoncentrować się na tym, co najważniejsze. Kolejną zaletą autonomicznego trybu pracy instalacji jest zwiększone bezpieczeństwo operatora. Odciągi dymu, obudowa ochronna, zapory świetlne i wyłącznik awaryjny zapobiegają uszczerbku na zdrowiu i obrażeniom ciała.
Zrobotyzowana cela spawalnicza z fotokomórką wykorzystującą podczerwień
Przyszłościowa technologia
Firma Fronius ustandaryzowała projektowanie zrobotyzowanych cel spawalniczych, stawiając przy tym na koncepcję platformy. Poszczególne moduły ze specyficznymi zadaniami zapewniają dużą elastyczność w zakresie wielkości, kształtu i masy elementów. Po prostu genialne: sterowanie systemowe HMI-T21 RS, lecz również oprogramowanie programistyczne i symulacyjne offline Pathfinder®. Przede wszystkim HMI T21 RS jest pionierskim rozwiązaniem, jeżeli chodzi o zakres funkcji i wygodę obsługi. Otwiera on całkowicie nową generację sterowania systemowego. Z kolei program Pathfinder ustanawia nowe standardy w zakresie programowania offline i symulacji spawania.
Brak komentarzy