Svařovací zdroj a roboty mohou vytvořit optimální základní podmínky pro MIG/MAG svařování, skutečná akce se však odehrává úplně vpředu na těle MIG/MAG hořáku. Teploty až 15 500 stupňů, rozstřiky z tekutého kovu a neustálé obrušování svařovacím drátem: tepelné a mechanické síly, které působí na spotřební díly, jako jsou průvlaky (kontaktní špičky) a plynové hubice, jsou obrovské. Co tedy dělat, abychom nevyhnutelný konec těchto dílů maximálně oddálili?
Čím méně často je třeba měnit spotřební díly, jako jsou průvlaky, plynové hubice nebo bovdeny v hadicových vedeních, tím lépe – chrání se životní prostředí a zákazníci profitují z nižších výrobních nákladů.
V zásadě platí, že spotřební díly, které jsou optimálně přizpůsobené svařovacím zdrojům a svařovanému materiálu, vydrží podstatně déle. Pro ocel a slitiny CrNi se proto musí používat jiné spotřební díly než při svařování hliníku, popř. CuSi.
Než přejdeme k zmíněným čtyřem opatřením, je třeba objasnit jednu otázku: Proč spotřební díly časem ztrácejí svou funkci?
Průvlak: permanentní kontakt – permanentní opotřebovávání
Bez průvlaku neboli kontaktní špičky není MIG/MAG svařování: V průvlaku – často označovaném také jako kontaktní špička, kontaktní trubice nebo kontaktní tryska – dochází k přenosu proudu na svařovací drát. To se děje prostřednictvím třecího kontaktu: Drát a průvlak jsou tedy v neustálém kontaktu a navzájem se otírají.
„Vybroušení“ je tak nejčastější příčinou, proč se průvlaky časem stanou nepoužitelnými. Neustálé tření drátu pozměňuje vnitřek průvlaku tak dlouho, až už nedochází k trvalému kontaktu mezi svařovacím drátem a průvlakem. Přenos proudu se stává nestabilním, stejně jako oblouk – a průvlak se musí vyměnit.
Může se však stát i opak: V důsledku otěru drátu a extrémního tepla v průvlaku se může vytvořit vrstva slitiny. V tomto případě průvlak uvnitř pomalu roste, až zablokuje podávání drátu.
Plynové hubice – boj proti rozstřikům
Druhým hlavním spotřebním dílem na těle MIG/MAG svařovacího hořáku je plynová hubice. Ta odpovídá za vytvoření ochranného plynového zvonu nad obloukem. Na životnost plynových hubic má rozhodující vliv teplota: Pokud je plynová hubice příliš horká, ulpívá na ní více rozstřiků, které se mohou s plynovou hubicí stavit a následně je už nelze odlepit. Když je hubice studená, rozstřiky jednoduše odskakují.
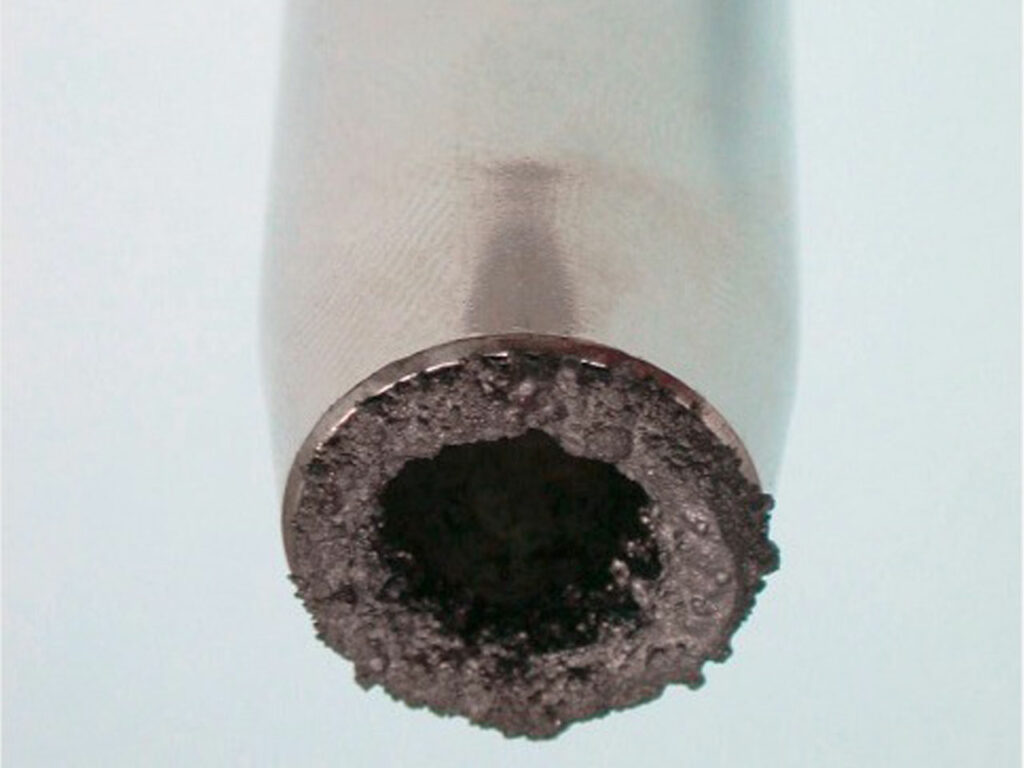
Rozhodující je používat různé druhy hubic pro ocel a hliník: Plynové hubice pro hliník jsou zpravidla potažené, takže poměrně měkké hliníkové rozstřiky lze snáze odstranit.
Bovdeny – vnitřní život hadicových vedení
Bovden vede svařovací drát skrz hadicové vedení a vznikajícím třením se přitom časem opotřebuje: Bovdeny začínají u přípojky FCS na svařovacím zdroji a končí v těle MIG/MAG hořáku na průvlaku.
Pro dosažení maximální životnosti a bezpečného provádění požadovaných svařovacích procesů by se měly vždy používat bovdeny, které jsou svou konstrukcí a vnitřním průměrem optimálně přizpůsobené použitému svařovacímu systému.
Co tedy dělat, aby opotřebení plynových hubic a průvlaků bylo co nejmenší?
Zatímco u bovdenů jde v podstatě jen o výběr správného výrobku, u průvlaků a plynových hubic je to poněkud složitější. Díky čtyřem uvedeným opatřením lze životnost těchto dílů výrazně prodloužit:
1. opatření: Optimální sladění průvlaku a svařovacího drátu
Správný poměr mezi svařovacím drátem a průvlakem – konkrétně mezi průměrem drátu a průměrem otvoru průvlaku – má rozhodující vliv na životnost průvlaku.
Kvůli složité interakci různých faktorů, jako je velikost proudu, stickout nebo vlastnosti drátu, je nezbytné kvalifikované odborné poradenství. Jen tak lze konkrétně řešit nejrůznější požadavky. Například pokud jde o použití průvlaku s nepatrně menším průměrem otvoru: Průvlak se tak může déle vybrušovat, a proto také déle vydrží.
Vliv na životnost průvlaku může mít také drezura drátu – tj. jak moc je drát v průvlaku ohnutý. Pokud je drezura drátu příliš malá, průvlak se příliš rychle vybrousí. Pokud je drezura drátu příliš velká, třecí kontakt – a následně ani svařovací proces – nefungují moc dobře. Řešení? Nové, inovativní typy průvlaků, např. poloskořepinového systému Contec, které jsou dnes na trhu, se opotřebovávají velmi rovnoměrně a tím zajišťují vysokou stabilitu svařovacích procesů. Contec doporučujeme pro hliník nebo pro svařování, při kterém je třeba opravdu optimální přechod proudu.
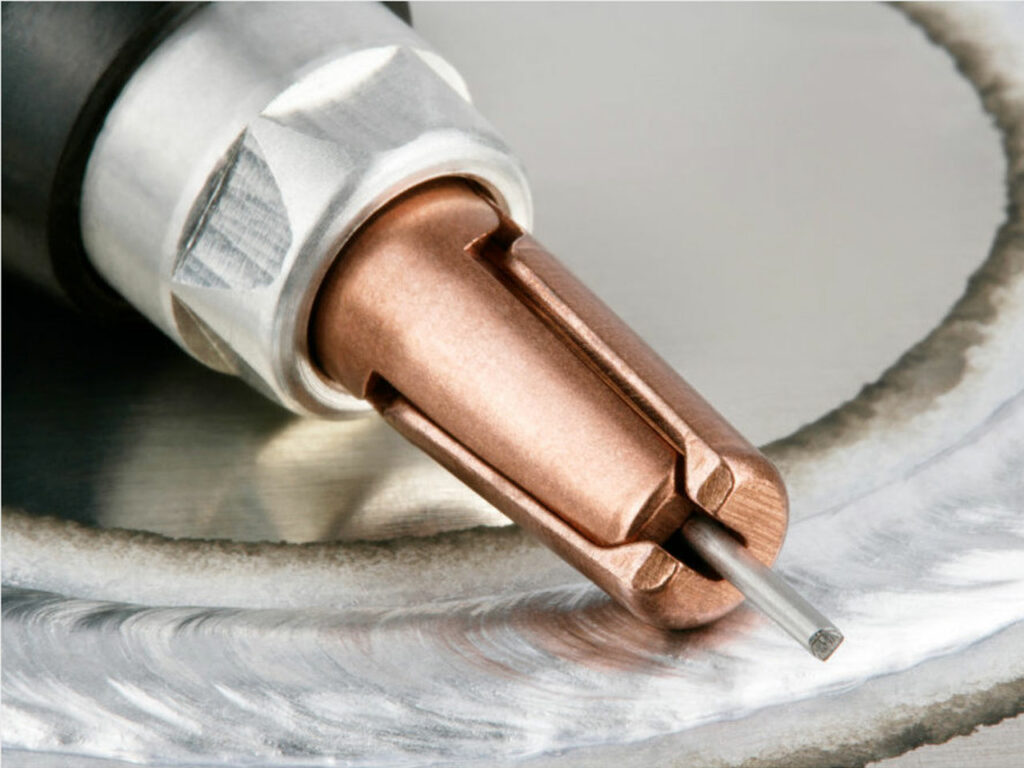
2. opatření: Používání průvlaků z vysoce kvalitního materiálu
To, jak dlouho průvlak vydrží, závisí mimo jiné na materiálu, ze kterého je vyroben. Dnes se používají tři různé typy kontaktních špiček:
Elektrolytická měď – E-Cu: Slabé výsledky: Vysoká čistota mědi sice zajišťuje velmi dobrý přenos proudu, ale průvlaky z elektrolytické mědi jsou velmi měkké a málo tepelně odolné, takže nemají dlouhou životnost – pro robotizované svařování se proto nedoporučují.
Měď-chrom-zirkonium – CuCrZr: Průmyslový standard. Nejčastěji se dnes používají průvlaky CuCrZr. Slitinové prvky chrom a zirkonium propůjčují průvlakům tvrdost a tepelnou zatížitelnost.
Wolfram-měď – WQ Quality: Špičkové výsledky v oblasti životnosti. Průvlaky WQ nejsou při pořízení levné – z dlouhodobého hlediska se však na nákladech ušetří, protože tyto průvlaky mají pětkrát až patnáctkrát delší životnost než průvlaky CuCrZr. Výsledek: Výroba se nemusí tak často přerušovat. Díky tomu je jejich použití velmi hospodárné, zejména u tvrdých ocelových drátů. Jejich „tajemství“: Přední část je vyrobena z extrémně odolné slitiny wolframu a mědi.
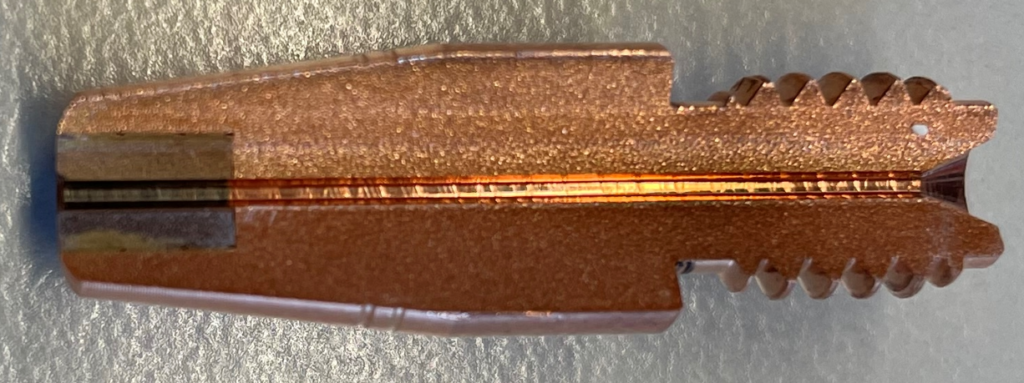
3. opatření: Snížení vlivu tepla na průvlaky a plynové hubice
Plynová hubice i průvlak jsou umístěné úplně vpředu na těle MIG/MAG hořáku a jsou vystavené extrémnímu tepelnému zatížení. Existují dva způsoby, jak toto zatížení snížit:
1) Dodržování vzdálenosti: Čím větší stickout – tedy vzdálenost mezi pracovní částí a tělem hořáku – tím menší tepelné záření, které působí na průvlak a plynovou hubici. Obecně platí pravidlo, že na každý milimetr vzdálenosti od pracovní části klesá teplota v přední části těla MIG/MAG hořáku o 50 stupňů. Při prodloužení stickoutu o pouhé čtyři milimetry klesá působení tepla na plynovou hubici o 200 stupňů – což je podstatný rozdíl.
2) Výběr správného tvaru průvlaku a hubice: Nezanedbatelný vliv na teplotu v plynové hubici a průvlaku má jejich tvar. Pokud se svařuje s krátkým stickoutem, doporučují se ostré průvlaky a plynové hubice. Ty mají relativně malý průměr předního otvoru, takže do trysky proniká méně tepelného záření.
4. opatření: Čištění těla MIG/MAG hořáku – prodloužení životnosti
Systematické odstraňování rozstřiků významně prodlužuje životnost průvlaků a plynových hubic. Způsob čištění těla MIG/MAG hořáku závisí především na tom, zda se svařuje ocel, nebo hliník:
Metody čištění u oceli a CrNi ocel
Mechanicky: Nejosvědčenější metodou odstraňování rozstřiků ze spotřebních dílů v těle hořáku je frézování. Některé frézky přitom pronikají zespodu do vnitřku spotřebního dílu až 5 cm hluboko a odstraňují rozstřiky osvědčeným mechanickým způsobem. Dobré frézky přitom čistí i čelní plochu plynové hubice.
Magneticky: Výhodou magnetického čištění je to, že nedochází k mechanickému kontaktu se spotřebními díly. V magnetických čisticích zařízeních se nacházejí cívky a proudovým impulsem se generuje silné magnetické pole. Síla magnetického pole vytáhne ze spotřebních dílů všechny ocelové rozstřiky. Tato metoda se zcela vyrovná frézování, ale nefunguje u hliníku.
Čištění u hliníku a CuSi – kartáčování
Hliníkové rozstřiky jsou příliš měkké na to, aby se daly odfrézovat – při frézování by se jenom rozmazaly. Proto se při svařování hliníku, resp. CuSi provádí čištění pomocí kartáčů. Základní princip je stejný jako při frézování.
Závěr
Životnost spotřebních dílů v procesu MIG/MAG svařování závisí hlavně na následujících faktorech:
- Správný výběr spotřebních dílů – optimální přizpůsobení konkrétní oblasti použití
- Kvalita použitých spotřebních dílů, zvláště s ohledem na tepelné a mechanické zatížení
- Sladění spotřebních dílů s ostatními komponentami svařovacího systému
- Efektivní čisticí systémy
Všechny průvlaky a plynové hubice od společnosti Fronius se vyvíjejí v Rakousku a jsou – jako všechny spotřební díly Fronius – cíleně přizpůsobené konkrétní oblasti použití. Společnost Fronius tak má ve svém portfoliu například přes 300 plynových hubic pro svařování oceli.
Pokud se chcete dozvědět více o tom, které průvlaky neboli kontaktní špičky, plynové hubice nebo bovdeny je nejlepší použít v konkrétní situaci, neváhejte nás kontaktovat. Některá z našich 27 poboček po celém světě je i ve vaší blízkosti – a naši odborníci jsou vám k dispozici, aby vám poradili a pomohli!
Žádné komentáře