Welding is an exciting and challenging job. Top welding specialists are considered heroes of a sort, are sought after around the world, and are handsomely paid wherever they go. The connections they create guarantee the safety of cars, bikes, planes, ships, trains, and more. Despite this, the profession sometimes suffers from a poor image and fewer young people want to learn this trade. Why is this? Well, welding produces welding fumes that are hazardous to health. However, unlike in the past, you can effectively protect yourself from them today!
Challenging and exciting
There are plenty of examples where joining metal not only requires extensive knowledge of welding technology and metallurgy, but is also extremely challenging in practice. Just think of the welding of aluminum mountain bike frames: when the bikers dash down the steepest mountains in the Downhill World Cup at over 70 km/h, up to 9000 newtons of force can be exerted on the rear frame. If a single weld breaks, dramatic falls often follow! That’s why true TIG professionals are in demand; they have in-depth specialist knowledge and dexterity when feeding the welding wire into the weld pool. Or consider steel sub-assemblies for freight cars: depending on their design, they have to withstand tensile forces of 22 tons or more. The MAG process and its variants such as PMC (Pulse Multi Control) are predominantly used here. Welding often has to be carried out in cramped spaces—especially vertical-up—so experience and skilled torch guidance are essential. Welding specialists have the power to control the level of emissions they produce.
Optimizing the arc
It is not just process variants and extraction technology that are important with regard to the emission rate. Process parameters play a particularly important role in gas metal arc welding (MIG/MAG): wire speed, arc length, and correction parameters all influence the harmful byproducts of welding. Together with the Welding and Joining Institute (ISF) at RWTH Aachen University, we took a closer look at the various parameter settings.
Fewer emissions with a pulsed arc
As the final report from our first joint welding fume investigation shows, the pulsed arc has the most advantageous material transfer and thus the lowest welding fume emission rate (FER) compared to the low spatter control arc (LSC) and the standard arc. In a new series of tests with the Aachen researchers, we examined how different welding torch positions, wire speeds, and arc length corrections affect the emission rate. Welding was carried out with our PMC arc and TPS 500i system welding machine.
The chosen conditions
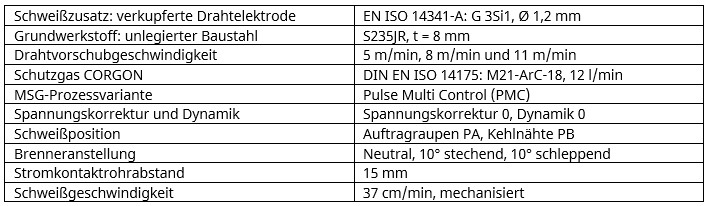
Fume emission rate when welding surfacing beads
During our tests, we found that welding fume emissions are comparatively low at a wire speed of 5 m/min and with a neutral welding torch position. However, it is striking that at the higher wire speed of 11 m/min, emissions are lower than at the reduced speed of 8 m/min, where our test led to increased short circuits (Figure 1).
If welding specialists optimize the arc using arc length correction (with a neutral welding torch position in the test), they can significantly reduce welding fume emissions at all wire speeds. In contrast to the non-optimized arc, the welding fume emissions are slightly lower at 8 m/min with 0.9 mg/s than at 11 m/min with 1.1 mg/s (Figure 1).
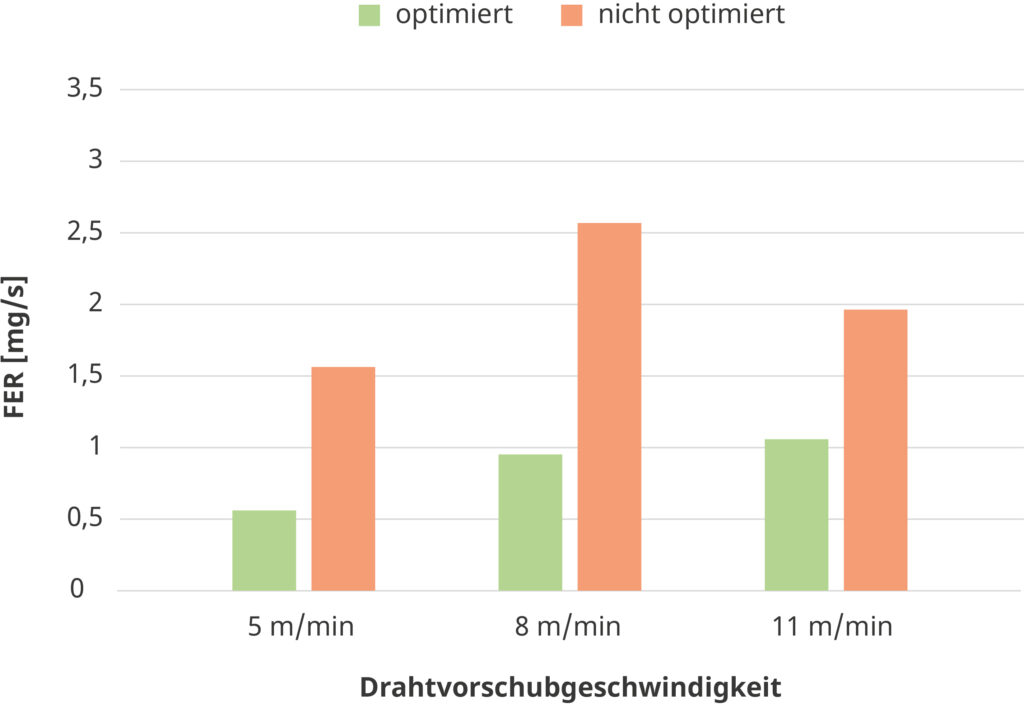
Welders therefore have a relatively large amount of leeway to design the arc so that exposure to welding fumes can be kept as low as possible, depending on the application.
Comparison of the voltage curves at a wire speed of 5 m/min
As our joint tests show, the welding fume emission rate is directly related to the number of short circuits. A high short-circuit rate leads to a significantly higher FER, and our test team believes that this is due to material transfer. Short-circuit phenomena cause process disruptions that result in metal vapor and metal spatter.
If welding specialists want to reduce emissions to a minimum, a process setting is recommended that brings arc length and short-circuit reduction down to a common denominator—that is, does not keep the arc too long or too short. With a slightly increased medium voltage, both short-circuit phenomena and emissions are reduced (Figure 2).
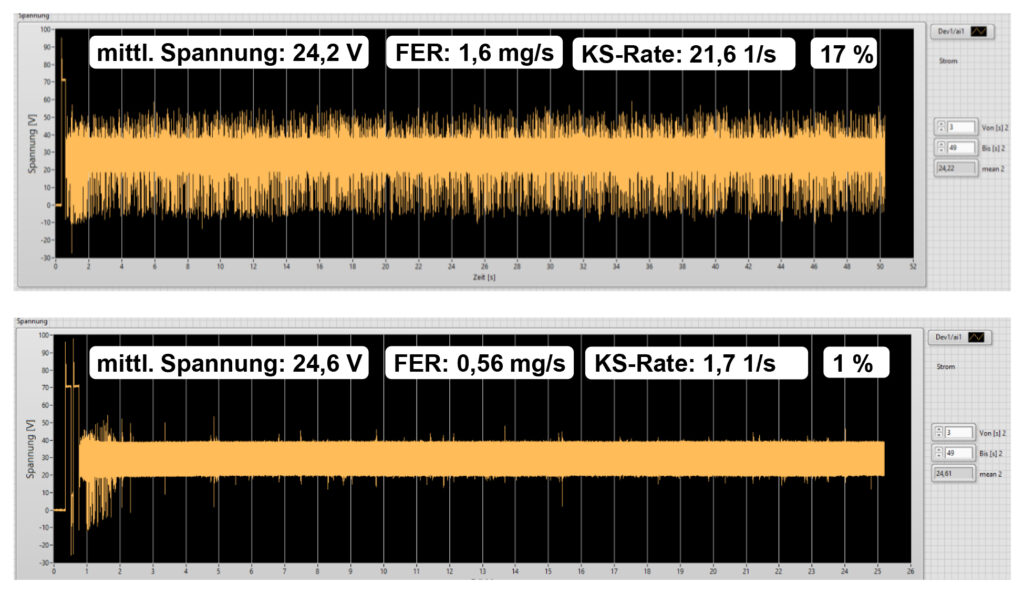
The welding processes at 8 and 11 m/min behave in the same way as the process at 5 m/min in terms of the interplay between medium voltage, short-circuit phenomena, and welding fume emissions.
Welding fume emission rate when welding fillet welds
Pulse welding at wire speeds of 5 m/min and 8 m/min results in significantly lower emission rates, 0.55 mg/s and 0.7 mg/s respectively, than at a wire speed of 11 m/min. Here the emissions amount to 1.7 mg/s, a good three times higher than those generated at a wire speed of 5 m/min.
As with welding the surface beads, the reason for the lower welding fume exposure at wire speeds of 5 m/min and 8 m/min is the smaller number of short circuits: here too a pull torch guidance technique produces fewer welding fumes than the push technique. At a wire speed of 11 m/min, the emission rate is reduced significantly (Figure 3). It is even lower than with a neutral welding torch position!
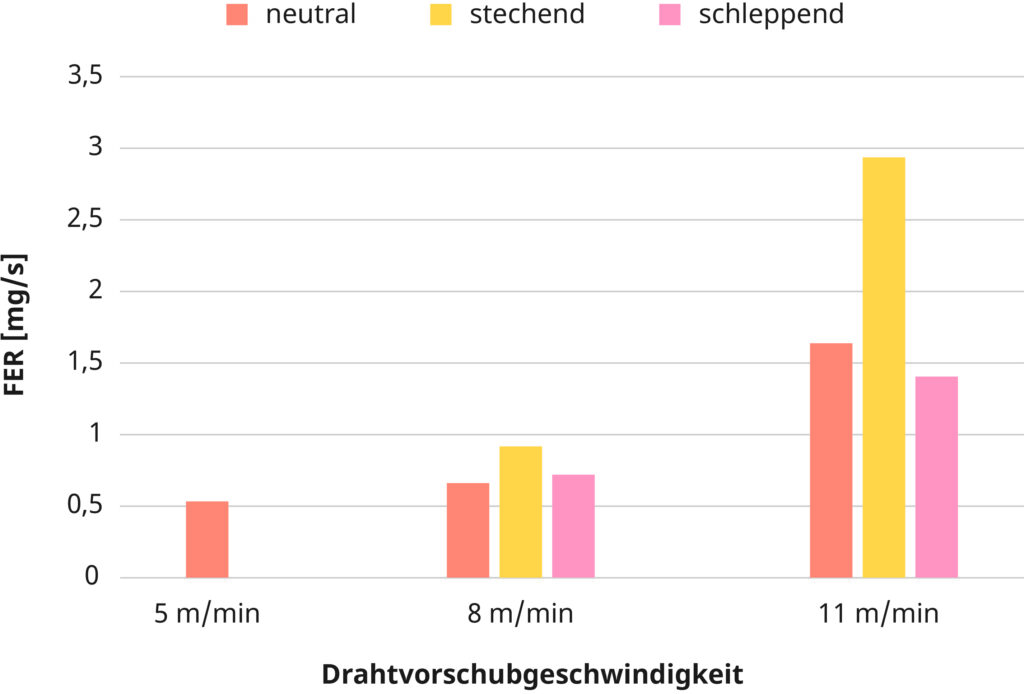
Overall, the welding fume emissions are at a lower level compared with welding the surface beads. The lowest value of each of the wire speeds is comparable to the emissions of the optimized processes (see Figure 1, green bars) with which the surface beads were welded.
At a wire speed of 8 m/min, the welding fume emission rates for the push and pull welding torch position are very similar in absolute values—as was also the case with the surfacing beads (Figure 1). By contrast, the push welding process at 11 m/min reveals a significantly higher FER at around 2.8 mg/s.
Comparison of the voltage curves at a wire speed of 11 m/min
Together with the Aachen researchers, we took a closer look at the relationship between the emission rate and the average voltage at a wire speed of 11 m/min: with a total of three measured values, there is a welding fume minimum at 1.36 mg/s (optimized with arc length correction -1.5 V). This is the operating point at which short-circuit phenomena occur sporadically, but the arc is not unnecessarily long. The process without arc length correction generates more emissions (1.72 mg/s) due to the longer arc. As the number of short-circuit phenomena increases with decreasing average voltage (arc length correction -2.5 V), the welding fume emissions (1.6 mg/s) also increase, see Figure 4.
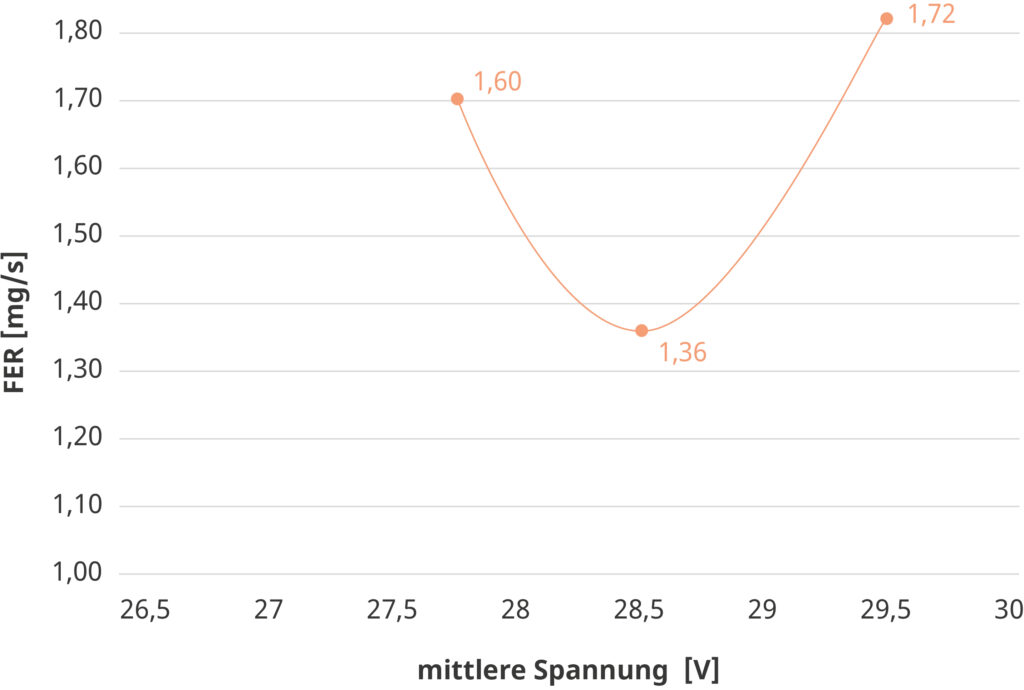
Welders can take matters into their own hands
Welding fume production can be significantly reduced through the targeted selection of welding process, wire speed, and arc length.
To summarize, in addition to other aspects such as material or impurities (scale), the welding fume emission rate depends on the deposition rate or process performance, with the material transfer being decisive. If an arc is too short, this leads to higher short-circuit rates and therefore to more welding fume emissions.
If, on the other hand, the welding process is perfected using arc length correction and joining is done with a fume extraction torch such as our MTW 500i Exento used with our Exento HighVac extraction system, then up to 99% of welding fumes can be extracted.
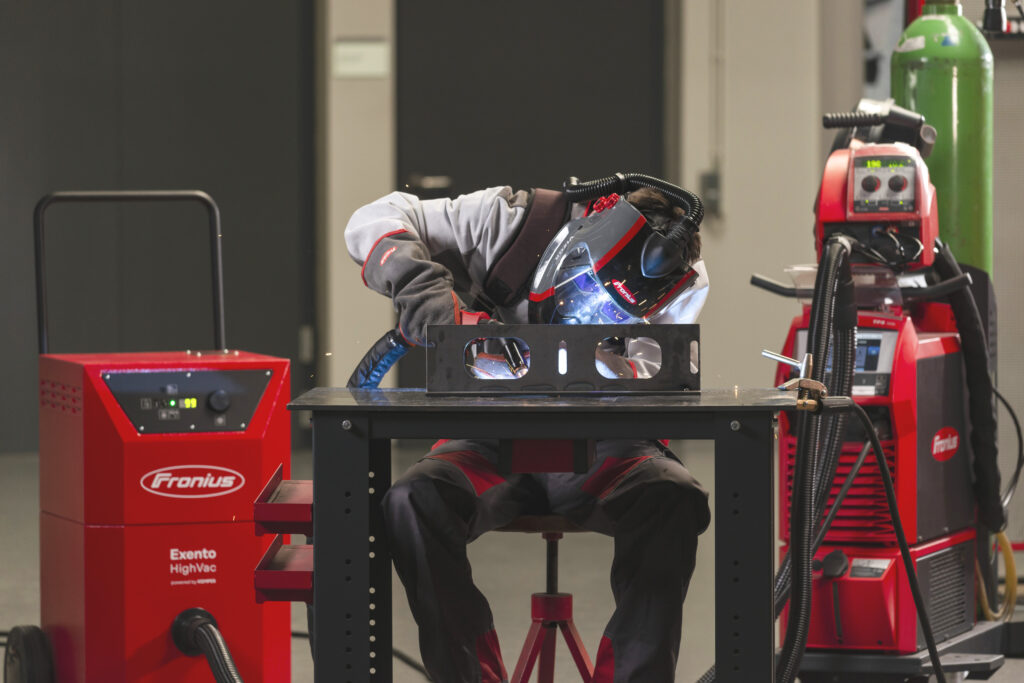
What’s more, our welding helmets with air-purifying respirator are the icing on the cake when it comes to protection against welding fumes. They filter a whole 99.8% of the remaining welding fume particles from the air. If welding specialists comply with all possible protective measures, welding is not only an exciting profession, but now also quite a safe one.
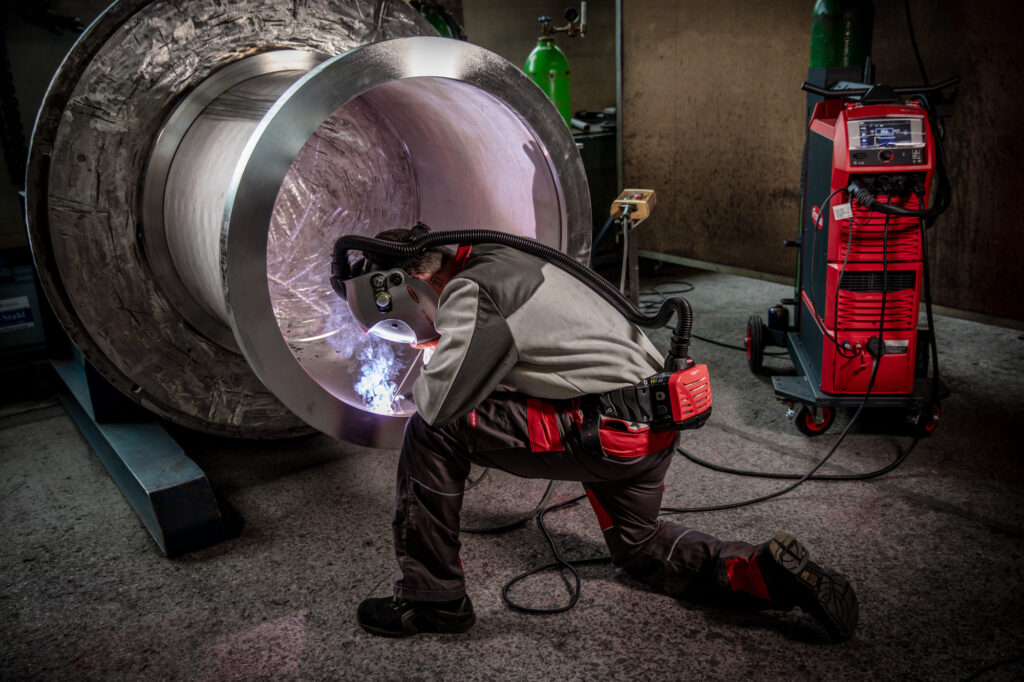
No Comments