The deep underwater world of our planet can be as alien as outer space. Bridges, oil platforms, and other structures reach into and over these areas requiring skilled workers to build and maintain them. Above the surface, welding, cutting, and assembling these structures requires only the training and skill to do the job. Performing those same jobs underwater requires an entirely new set of skills, understanding, and equipment. Welcome to the world of commercial diving, and more specifically, underwater welding.
Often referred to as one of the most dangerous jobs on earth, underwater welding faces challenges from the environment, the tools, and even from the welding process itself. What makes a good underwater welder? “Grit,” says fifteen-year veteran diver Kirk Hooker. “Grit and patience.” A taste for adventure might lead someone to become a welder-diver, but patience and tenacity will help them succeed. Hooker began welding about twenty years ago. He became a certified commercial diver to take his love of welding underwater. In the past few years he designed and built a patent-pending mobile dive tank to teach others about underwater welding.
Wet- vs Dry-welding?
Underwater welding comes in two forms. Wet welding, our focus here, and hyperbaric or dry welding. Hyperbaric welding is done underwater, but a dry habitat protects the weld. This can be small, just encompassing the weld area, or large enough to hold a team of welders. Underwater dry welding has its own challenges including high costs. The biggest benefit over wet welding is that it mimics surface welding, allowing for the use of multiple processes that can provide a stronger weld.
The Challenges of Underwater Welding
Wet welding uses shielded metal arc welding (SMAW) and specially coated electrodes. As any welder knows, a solid weld requires keeping a keen eye on the arc and weld puddle. Visibility is the biggest challenge of wet welding. Murky water, lack of light, and floating particulates are just the beginning. Inside the helmet the view is limited, as with a regular welding hood, but welder-divers need to keep track of their environment more than surface welders do. Air bubbles from exhalation and those created by the welding process are constantly obscuring the view. If the diver can get a good position where bubbles aren’t in their face, seeing the arc is still difficult because the water is constantly quenching the weld puddle. Keeping a close arc gap is important, and there isn’t a lot of puddle to watch. Maintaining a fluid weld is difficult and creating attractive welds underwater is significantly more challenging than above the surface.
Welding training under water Underwater welding seam
Poor Visibility, Current Flows, and Pressure
Diving in man-made underwater environments is sometimes worse for visibility compares to natural bodies of water. Commercial divers provide support and maintenance to a variety of sites from nuclear power plants to wastewater treatment facilities. Some of these dive environments require haz-mat suits for safety. The water is so thick and dark that divers work blind, using touch and hearing when visibility fails.
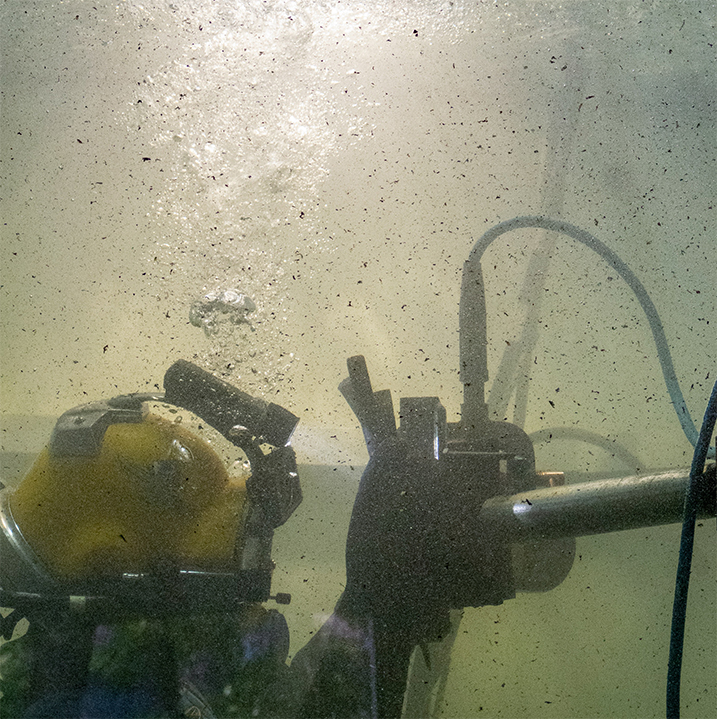
Water flow is another challenge. Water currents can be unpredictable, pushing and pulling as divers try to complete work. Weight belts and buoyancy aids can help, but depending on the location, the water may be stagnant or constantly moving. Welder-divers have to understand their work environment and depth of site to plan accordingly. The pressure on deep dives is intense. One of the most hazardous situations is when divers encounter differential pressure. This happens when bodies of water of different elevations intersect, such as in a dam or other bottleneck. The pressure from the higher elevation compounds pushing water from one area to the next, often through a small opening. If the diver becomes trapped in this flow, the force of pressure on the body against the opening can cause severe injury or death.
The Differences to Welding on Land
Everything underwater takes longer. Where a simple T-joint can take less than a minute on the surface, just suiting up in dive gear takes about ten minutes. Based on the dive, an average set of gear weighs a hundred pounds or more. Divers don’t work alone, so in addition to the regular weld and site prep, welder-divers have to check their communication system. It takes a team to safely get the diver ready and welding. Even getting to the weld site takes time—whether it’s straight down or several hundred feet into an underwater tunnel. There really isn’t such a thing as a “quick weld” when working underwater.
Welding safety under the water includes wearing clothing that gives protection from electricity and water temperature. Electricity travels the shortest route from one point to another, including straight through the body. Knowing the location of the welding ground line in relation to the weld site is imperative. Being between the two risks electric shock.
The welding/diving helmet is significantly heavier than the standard welding hood. It allows the diver to breathe, communicate, and often has a light attached for visibility. While the high end of welding hoods can cost $2,500, new diver helmets start there and can run up to $10,000 or more. Add in the costs for wet and dry suits, power supplies and consumables, and it’s easy to see why welder-divers aren’t often self-employed.
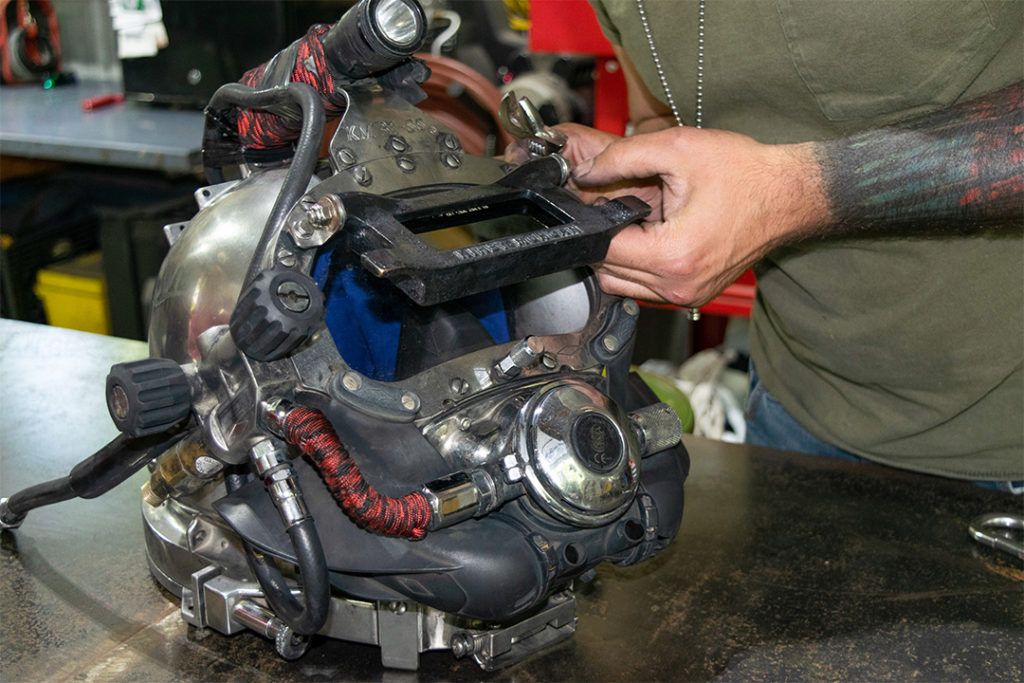
One Common Feature
Though much is different about the process and the gear, the welding power supply used for underwater SMAW welding is the same as above. Hooker uses his Fronius TransPocket 180 for both welding and cutting underwater. Cutting, also referred to as “burning,” uses the arc with pressurized oxygen and a magnesium-cored rod to establish and control the cut. This allows them to cut through up to six inches of steel or to fracture concrete for non-welding jobs. Underwater welding is usually just a small part of a commercial divers skill set.
A mobile dive tank for welding trainings under water. Kirk Hooker from Hooker Welding Service, LLC
Underwater welding truly is an “Ultimate Welding Challenge”. In the blog series of the same name, we take a look at welding in extreme and unusual situations. From the deepest oceans to the depths of outer space: find out more under “Welding for Space Travel”. You can look forward to many more exciting topics too!
By Rhonda Zatezalo, freelance writer for the fabrication industry. Crearies Marketing Design.
1 Comment
Castard
25. December 2019 at 11:39Bonjour je suis soudeur je vis en région parisienne sa m’intéresse la soudure sous marine mais je vis en ville si je peux avoir un contact pour travailler sur paris ou me déplacer vers vous je fais du grand déplacement en temps que plombier soudeur tuyauteur tig de profession depuis 17 ans d’expérience merci cordialement a l’équipe fronuis.