Was Batteriewannen im Fahrzeugbau und Seilbahngondeln gemeinsam haben? Die Antwort ist überraschend einfach: die sicherheitsrelevante Rolle vieler Schweißnähte. Sowohl Batteriewannen als auch Seilbahngondeln müssen hohe Qualitäts- und Sicherheitsstandards erfüllen. Aber auch in anderen Branchen sind die Ansprüche an Schweißnähte hoch. Notwendige Hightech-Schweißsysteme für den Prototypenbau kosten jedoch meist ein Vermögen …
Fokus auf Kernkompetenzen mit großem Einsparpotenzial
Dort haben wir eine Marktlücke entdeckt. Unser Gedanke seitens Fronius dabei: Lagern Hersteller von E-Fahrzeugen, Nutzfahrzeugen, Waggons, Gondeln oder anderen Hightech-Produkten das Prototypen-Schweißen aus, können sie sich vermehrt auf ihre Kernkompetenzen konzentrieren. Diese Firmen haben infolge mehr Potenzial, sich um die Entwicklung erfolgreicher Innovationen zu kümmern.
Kunden, die den Prototypenbau dann tatsächlich zu uns auslagern, werden infolge hohe Investitionskosten einsparen. Sie können das Finanzrisiko somit minimieren – auch bei den Personalkosten.
Fronius-Prototypen-Zentrum: Rundumservice von der Machbarkeitsstudie bis zur Vorserie
Alles nur Fantasie? Nein. Wir haben diese Geschäftsidee bereits letztes Jahr erfolgreich an unserem österreichischen Standort Wels realisiert. Unsere Schweißtechniker sind überaus begabt und verfügen – in enger Kooperation mit der Fronius-Entwicklung – über großes Know-how.
Gerade deshalb sind sie sehr daran interessiert, ihr Können unter Beweis zu stellen: In den unterschiedlichsten und teilweise überaus komplexen Schweißherausforderungen unserer Kunden sehen die Kollegen eine sportliche Herausforderung. Wer bei uns mit einer Problemstellung im Prototypenbau aufschlägt, dem können wir eine Expertenlösung bieten.
Das Angebot beginnt bei Machbarkeitsstudien und endet mit fertig geschweißten Prototypen. Auf Kundenwunsch produzieren wir auch kleinere Stückzahlen für die Vorserie.
Mehr als neunhundert Quadratmeter für den Prototypenbau
Wir haben uns richtig Mühe gegeben, auf über neunhundert Quadratmetern alles einzusetzen, was die Fronius-R&D an Hightech hervorgebracht hat. Und somit bietet unser Prototypen-Zentrum ausgeklügelte Simulations-, Schweiß- und Vermessungstechnik. Damit können wir Bauteile bis zu einem Ausmaß von 3 x 2 Metern und einem maximalen Gewicht von 1,5 Tonnen schweißen.
Geheimhaltung hat im Prototypenbau natürlich oberste Priorität und ist uns ein essenzielles Anliegen. Deshalb sind die Anlagen völlig abgeschottet – wodurch wir höchste Diskretion gewährleisten können.
CMT- und LaserHybrid-Schweißtechnik geben den Ton an
Unser Prototypen-Zentrum verfügt über zwei Roboterschweißzellen, ausgestattet mit CMT-Technologie. Der „kalte“ CMT-Schweißprozess reduziert Spritzer und Verzug auf ein Minimum. In Kombination mit der Schweißgeräteplattform TPS/i meistert er Blechverbindungen unterschiedlicher Materialien und Wandstärken von 0,5 bis 6 mm. Gerade im Dünnblechbereich ist dieses Verfahren daher attraktiv.
Die TPS/i ist quasi ein digitaler Hightech-Schweißcomputer, womit wir auch Schweißprozesse wie Low Spatter Control (LSC) oder Pulse Multi Control (PMC) einsetzen können.
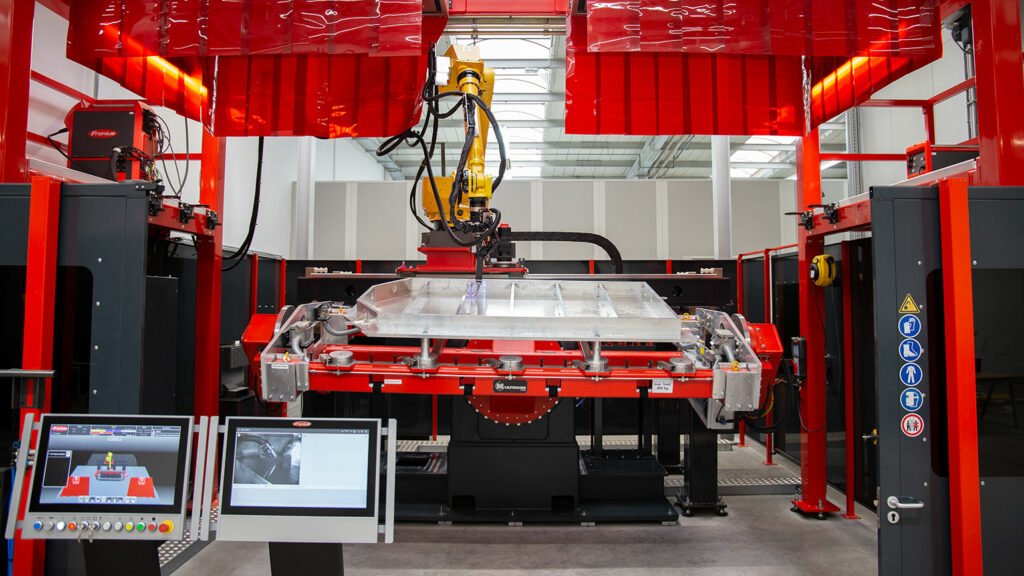
Die LaserHybrid-Schweißzelle kombiniert hingegen ein leistungsstarkes Metall-Schutzgas-Schweißsystem (MSG) mit moderner Lasertechnik. So werden die Vorzüge beider Welten kombiniert: hervorragende Spaltüberbrückbarkeit sowie hohe Schweißgeschwindigkeit mit geringem Wärmeeintrag und tiefem Einbrand.
LaserHybrid liefert bei fast allen Materialien verzugsarme Ergebnisse in hoher Qualität. Mit diesem Schweißprozess lassen sich Schweißgeschwindigkeiten bis zu 8 m/min erzielen.
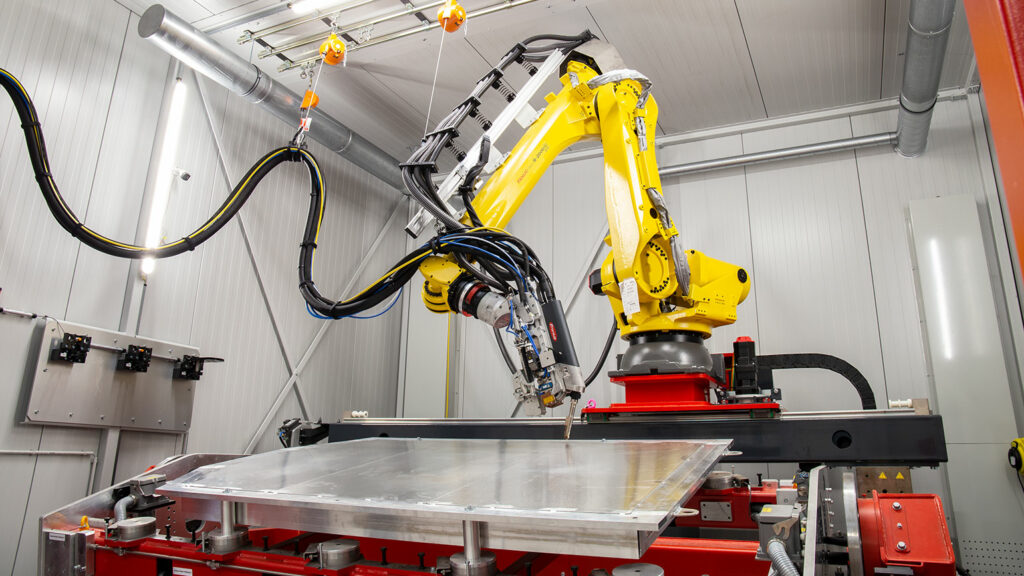
Gereinigt wird mit Heißplasma-Technologie
Zum Reinigen von Fügebereichen nutzen wir unser revolutionäres Acerios-Oberflächenreinigungssystem. Es arbeitet mit Heißplasma-Technologie und verzichtet auf umweltschädliche Chemikalien. Alle Oberflächen werden exakt dort gereinigt, wo geschweißt wird. Und zwar nur dort!
Im Vergleich zur chemischen Reinigung, wo die Oberflächen großflächig in Chemikalien eingetaucht werden, schont Acerios beides: Umwelt und Budget.
Sensortechnik für präzise Schweißnahtverläufe
Alle Schweißzellen im Prototypen-Zentrum verfügen über ausgeklügelte Roboterassistenz- und Kontrollsysteme. Ein Laser-Überwachungssystem, das am Schweißbrenner montiert ist, stellt sicher, dass der Roboter exakt an der richtigen Stelle schweißt. Bei Versatz, Verzug oder Toleranzen korrigiert der Roboter den vorprogrammierten Schweißnahtverlauf automatisch und schweißt zuverlässig an der richtigen Position. SeamTracking wiederum erkennt die Bauteilkanten bei Kehl- und Stumpfnähten durch Pendelbewegungen des Brenners.
Eine weitere Möglichkeit zur Nahtverfolgung haben wir mit WireSense geschaffen. WireSense benötigt keine zusätzliche Sensor-Hardware, sondern nutzt die Drahtelektrode als Sensor. Der Brenner tastet mit reversierenden Drahtbewegungen das Bauteil ab und sendet Höheninformationen sowie Kantenpositionen an die Robotersteuerung.
Real-Time-Blick auf die Schweißnaht
ArcView – unser hochauflösendes Kamerasystem – liefert detaillierte Bilder von Lichtbogen und Schweißnaht auf einen 21-Zoll-Monitor. Auf diese Weise können wir den Schweißvorgang live überwachen und bei Bedarf korrigierend eingreifen.
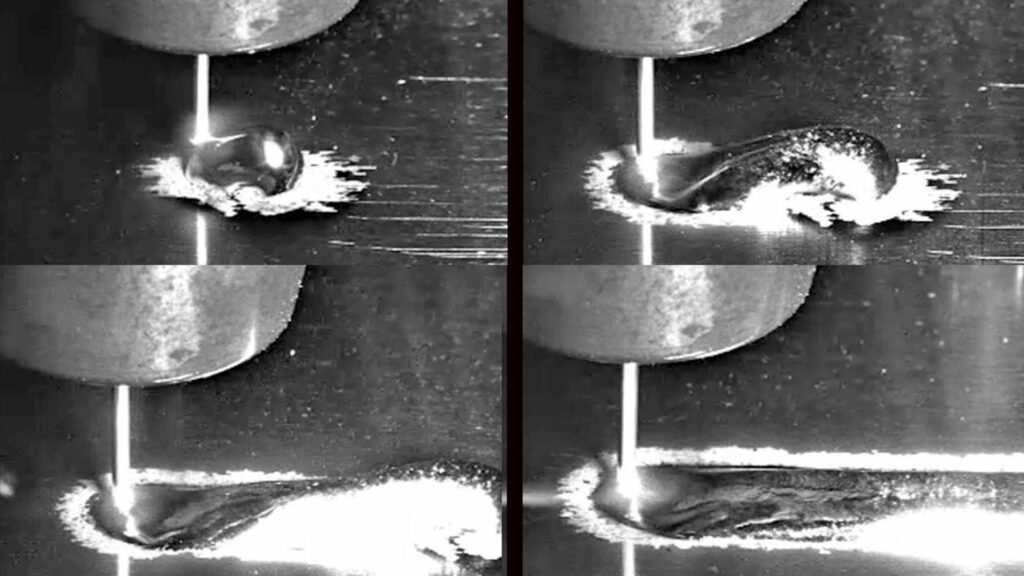
Fehlerfreie Bauteile durch Laser-Nahtkontrolle
Wirklich perfekte Nähte sind jedoch nur mit einer verlässlichen Fehlererkennung möglich. Nach dem Schweißen scannen wir die Schweißnähte mithilfe eines Laser-Systems und finden auch kleinste Fehler sicher und zuverlässig. So können wir Korrekturmaßnahmen rechtzeitig und kostenschonend einleiten.
Jede Naht lässt sich nachverfolgen
Unsere Dokumentationssoftware WeldCube überwacht und speichert alle relevanten Daten aus dem Schweißprozess. Mit ihrer Hilfe lässt sich jede einzelne Schweißnaht nachverfolgen und eins zu eins reproduzieren.
Bauteilvermessung mit Spezialkamera und Roboter
Sobald das Bauteil fertig geschweißt ist, vermessen wir es in einer speziellen Robotermesszelle. Abweichungen vom virtuellen Bauteil und Toleranzüberschreitungen – zum Beispiel beim Bauteilverzug – erkennen wir daher schon in der Frühphase des Prototypenbaus und können noch während der Schweißversuche die Parameter optimieren.
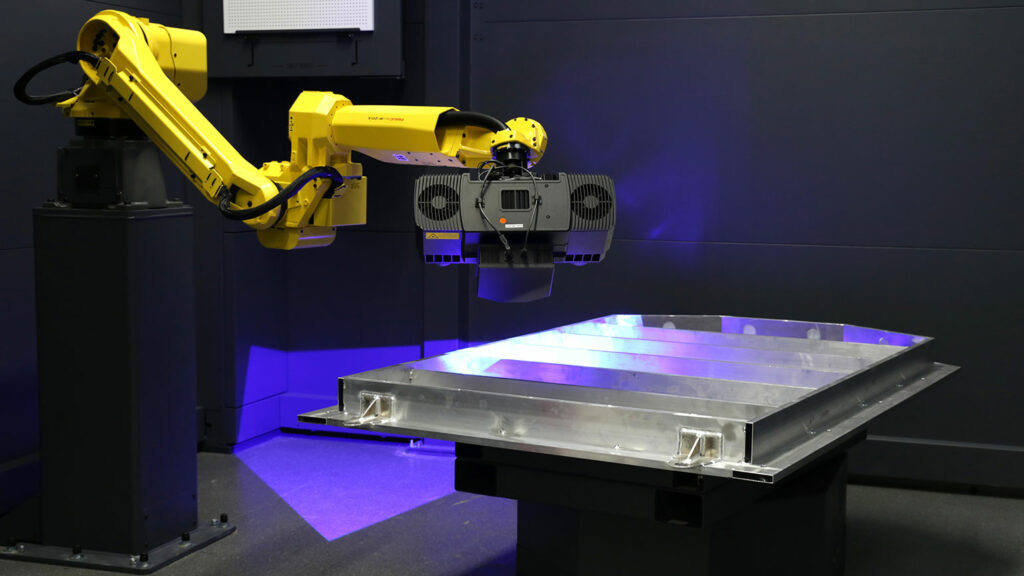
Last but not least bieten wir unseren Kunden die Möglichkeit, die gefertigten Prototypen einer metallurgischen Überprüfung zu unterziehen. Dafür betreiben wir bei Fronius ein eigenes Labor.
Interesse am Fronius-Prototypen-Zentrum?
Ist es uns gelungen, euer Interesse an unserem Prototypen-Zentrum zu wecken? Wollt ihr genauere Informationen oder habt vielleicht selbst eine herausfordernde Schweißaufgabe, bei der wir euch unterstützen können? Hier geht’s zur Auslagerung des Prototypenbaus hin zu Fronius …
Keine Kommentare