Wie ein riesiger mechanischer Arm trägt ein moderner Hydraulikbagger mühelos über 20 Tonnen Erde, Gestein und Schutt ab. Diese sogenannten Yellow Goods wie Bagger, Radlader, Planierraupen und landwirtschaftliche Maschinen sind enormen Belastungen ausgesetzt. Neben dem Manövrieren von schweren Lasten auf unbefestigtem Untergrund müssen die Geräte den immensen Druck- und Zugkräften der ständigen Bewegungen beim Graben, Heben und Schwenken standhalten.
Das ist eine große Herausforderung für die Verbindungsstellen, die tragende Teile zuverlässig zusammenhalten sollen. Jede Schweißnaht muss perfekt ausgeführt sein, um Risse und Brüche zu vermeiden, die zu Maschinenausfällen oder im schlimmsten Fall zu Arbeitsunfällen führen können.
Hohe Standards und Anforderungen
Bei der Herstellung von Yellow Goods müssen immer wieder schwere Stahlbleche miteinander verbunden werden. Komponenten mit Materialstärken von über 50 mm und meterlange Schweißnähte sind hier nicht die Ausnahme, sondern die Regel. Neben der Nahtqualität spielt auch die Nahtoptik eine große Rolle, da die vielen Sichtnähte ausschlaggebend für ein hochwertiges Erscheinungsbild des gesamten Produktes sind. Fortschrittliche Schweißtechniken sind somit unerlässlich.
Tandemschweißen für optimales Füllvolumen
„Die Herausforderungen beim Schweißen von Yellow Goods sind eine zuverlässige Spaltüberbrückung zur Bewältigung der Bauteiltoleranzen und das Füllen der großen Nahtvolumen“, weiß Bernd Rutzinger, Segmentmanager für Yellow Goods bei Fronius Perfect Welding. Dazu brauche es eine hohe Einschaltdauer und Abschmelzleistung, um das nötige Füllvolumen aufzubringen, sowie eine präzise Regelung der Drahtelektroden. Wie das geht? „Mit Tandemschweißen“, bestätigt der Experte.
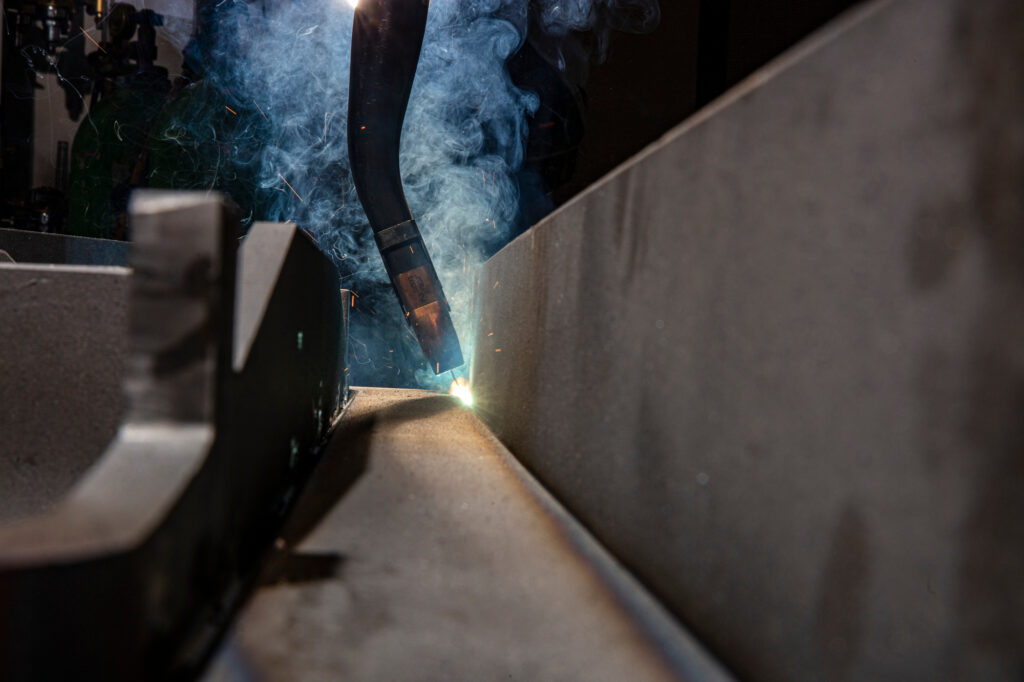
Zuverlässiger Prozess bei hochfesten Stählen
Tandemschweißen beschreibt das MIG-/MAG-Hochleistungsschweißen mittels zwei Drahtelektroden. Dieser Prozess erfolgt voll automatisiert, wird also von Robotern durchgeführt. Die Folge: Einerseits ist eine Steigerung der Schweißgeschwindigkeit, andererseits eine höhere Abschmelzleistung möglich. Da gleich zwei Drahtelektroden gleichzeitig abgeschmolzen werden, eignet sich dieser Schweißprozess besonders zur Überbrückung der größeren Spaltbreiten von Yellow Goods.
Die Drahtelektroden verlaufen in zwei voneinander elektrisch isolierten Kontaktrohren, wodurch ein getrenntes elektrisches Potenzial entsteht. Vorteil dieser Trennung ist, dass sich dadurch die Lichtbögen individuell regeln und trotz unterschiedlicher Leistung exakt aufeinander abstimmen lassen.
Doppelte Geschwindigkeit bei gleichbleibender Qualität
Trotzdem arbeiten beide Drähte in derselben Gasatmosphäre und bilden ein gemeinsames Schmelzbad. Dabei erfüllen sie unterschiedliche Aufgaben: Der vordere Draht wird als Lead-Draht bezeichnet und ist für den Einbrand verantwortlich. Der zweite Draht (auch Trail-Draht genannt) dient hauptsächlich dem Auffüllen des Nahtvolumens.
Die entstehende höhere Abschmelzleistung führt zu höheren Schweißgeschwindigkeiten und kürzeren Produktionszeiten im Vergleich zum Eindrahtschweißen. Außerdem müsse nur gelegentlich manuell nachjustiert werden, was ebenfalls viel Zeit spart. „Für diesen Prozess sprechen aber vor allem die hervorragende Nahtqualität und Nahtoptik“, so Bernd Rutzinger.
Wechsel von Zwei- auf Eindraht
Tandemschweißen ist somit nicht nur zeitsparender, sondern liefert auch ein qualitativ hochwertiges Schweißergebnis. Dabei bietet der Prozess ein hohes Maß an Flexibilität. Die Lichtbögen können unabhängig voneinander gesteuert und präzise geregelt werden. Zwangslagen beim Schweißen lassen sich durch den möglichen Richtungswechsel des Brenners deutlich leichter vermeiden.
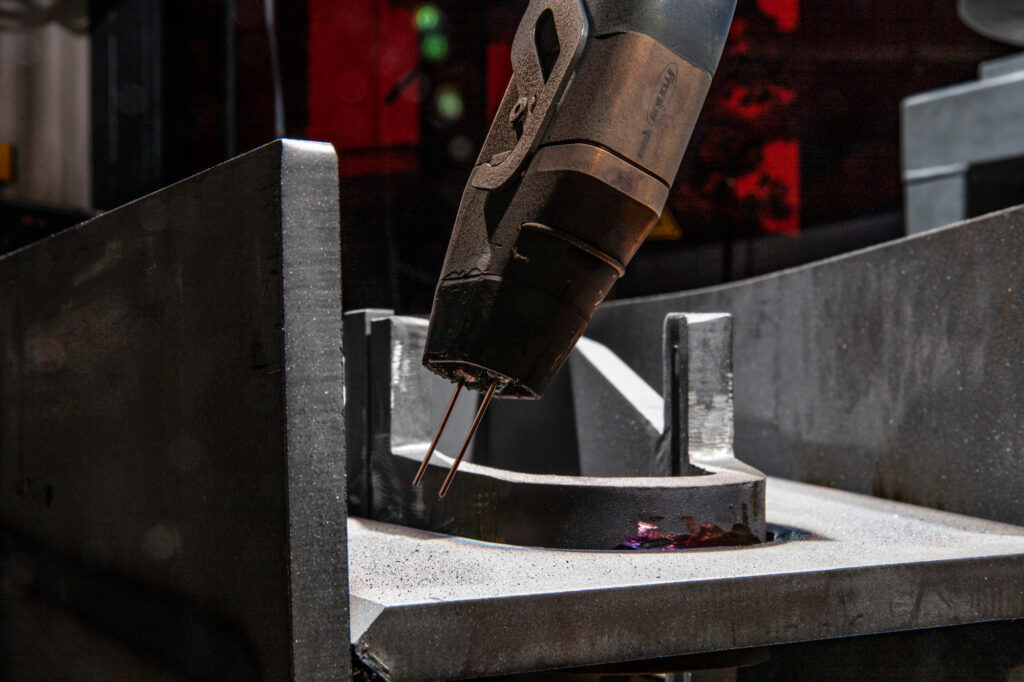
So kann bei schwer zugänglichen Schweißnähten der Rohrbogen von Tandem auf Eindraht getauscht werden. Es ergibt sich ein größeres Applikationsfenster, wodurch auch der Einsatzbereich der Anlage erweitert wird. Dafür muss der Schweißprozess nicht unterbrochen werden: Die Umschaltung von zwei Drähten auf einen erfolgt über den TWIN-Controller, der mit der Robotersteuerung verbunden ist. Außerdem besteht die Möglichkeit, die beiden Drähte mit unterschiedlichen Lichtbogen-Arten wie Sprühlichtbogen und PMC (Pulse Multi Control) zu verschweißen.
Koordinationsgeschick gefragt
Trotz der vielen Vorteile müssen beim Tandemschweißen einige Faktoren beachtet werden. Die größte Schwierigkeit besteht darin, beide Lichtbögen erfolgreich zu steuern. Abhilfe schafft hier unser TPS/i TWIN-Schweißsystem, das intelligente Schweißparameter zur Verfügung stellt. Die Lichtbogen-Längenkorrektur und der Einbrandstabilisator sind zwei Funktionen, die in Kombination verwendet werden, um geringfügige Abweichungen wie Schwankungen im Abstand zwischen Kontaktrohr und Werkstück oder unsachgemäße Anarbeitung zu kompensieren.
Synchronisierte Lichtbögen durch intelligente Unterstützung
Das TPS/i TWIN-Schweißsystem basiert auf zwei unabhängigen Schweißgeräten, zwei Drahtantrieben und zwei Stromdüsen. Die elektrisch isolierten Stromdüsen befinden sich dabei in einem Brennerkörper. Nach ein paar wenigen Voreinstellungen wie der Drahtvorschub-Geschwindigkeit oder der Schweißspannung ist das TWIN-System schon bereit zum Einsatz.
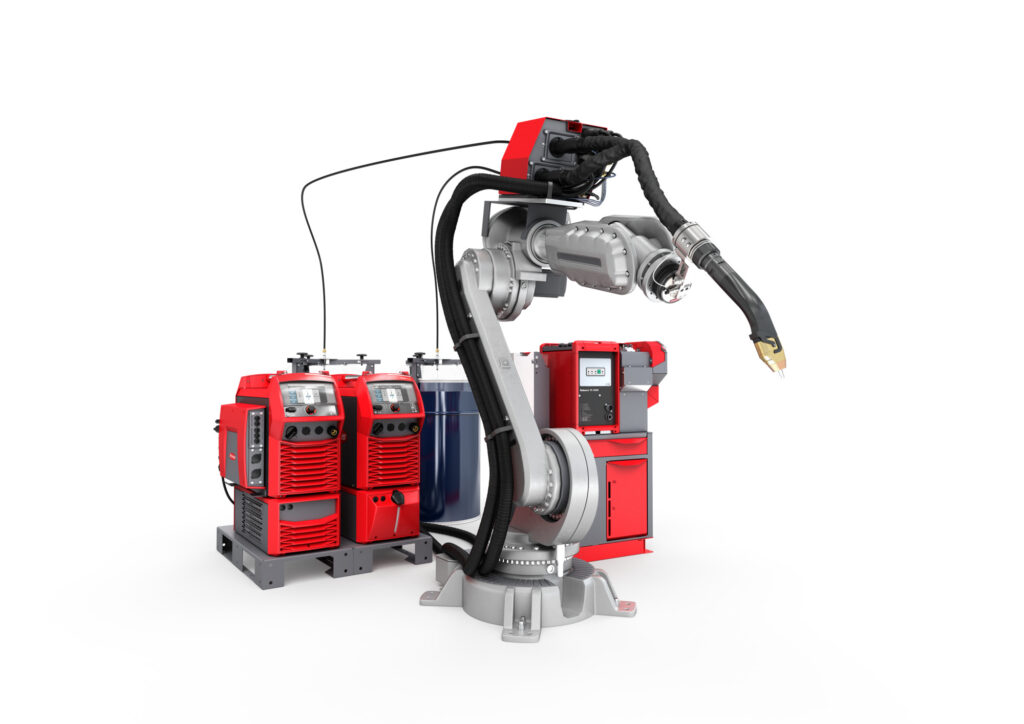
Die beiden Schweißgeräte sind über den TWIN-Controller optimal aufeinander abgestimmt. Dieser fungiert als Schnittstelle für eine intuitive Bedienung des Roboters. Das Schweißsystem ist außerdem auch für hochfeste und niedrig legierte Stähle bestens geeignet und daher auch eine effiziente Lösung für die Nahtanforderungen von Yellow Goods. „Das neue TPS/i TWIN-System ist durch die Synchronisierung und Volltextanzeige einfach zu bedienen, dadurch ergibt sich für Anwender ein effizienter Produktionsprozess, der Nacharbeiten reduziert und die Produktivität steigert“, fasst Rutzinger zusammen.
Der Alleskönner für Yellow Goods
Egal ob mit oder ohne intelligente Unterstützung – Tandemschweißen hat sich bei der Verbindung von hohen Materialstärken als bewährtes Verfahren etabliert. Als echter Superheld unter den Schweißprozessen werden selbst die anspruchsvollsten Nahtanforderungen von Baustellenfahrzeugen und landwirtschaftlichen Maschinen mit Leichtigkeit gemeistert.
Keine Kommentare