When amperages of up to 700 A regularly rush through the arc, one thing quickly becomes clear—welding is an energy-intensive process. This brings with it the question: “Is it possible to save energy here?” The answer is a resounding yes! Energy-efficient welding machines and processes are essential in doing so. We show you five features that you should look for in an energy-efficient welding machine.
Like many other technical processes, welding also has an impact on the environment; resources such as energy, shielding gas, welding wire, and various wear parts are consumed, while welding fume is released into the atmosphere.
There are many different ways to save resources in welding, including the resource-conserving production of welding machines, the use of long-lasting, repairable, and recyclable equipment, opting for multiprocess machines and equipment, and the optimized application of wear parts. But is there much scope for reducing electricity consumption?
When it comes to energy efficiency, the technical properties of the welding machine used are key. So the question is, what technical features must a welding machine have in order to weld as energy-efficiently as possible?
Inverter technology in place of old analog welding machines
The Transarc 500 with inverter technology, first launched on the market in 1981, represents a quantum leap in the development of welding machines and welding processes. Compared to the relatively simple analog welding machines that had been widely used until then, inverter welding machines require up to a third less power.
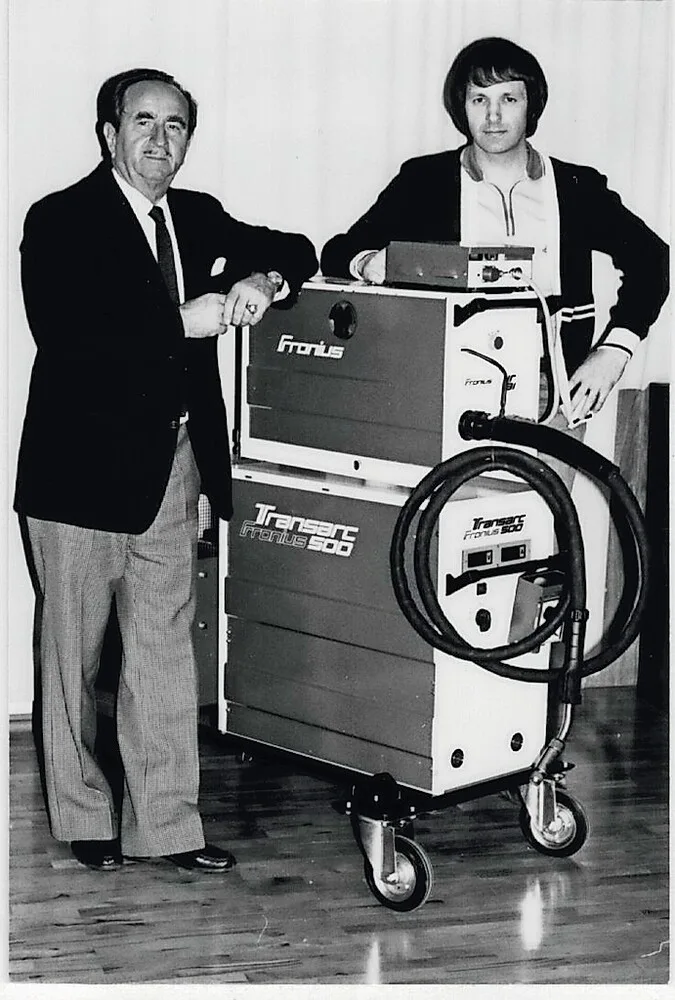
In practice, it’s obvious that inverter machines are significantly more energy-efficient because they hardly heat up at all compared to their analog counterparts. The current drawn by inverter machines is therefore predominantly used for the welding work itself, whereas with analog machines a significant amount of energy is wasted in the form of heat. A further important distinguishing feature is the lighter and more compact nature of inverter welding machines, due to the significantly smaller welding transformer. This makes them more mobile than analog welding machines.
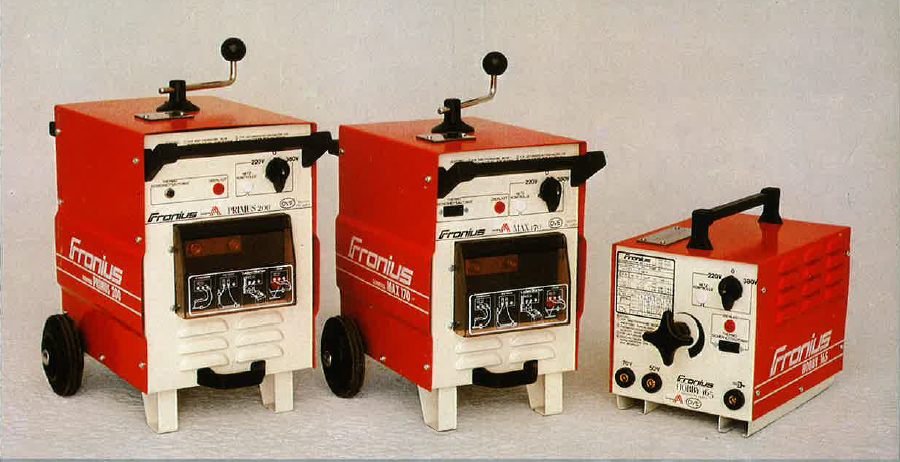
So if you still own an analog welding machine, you have already contributed towards energy efficiency simply by switching to inverter technology.
Not all inverter machines are the same
However, there are also measurable variations between different inverter machines in terms of energy consumption, especially as leading manufacturers of welding machines are constantly striving to optimize the energy efficiency of their products.
For example, the power factor correction in modern inverter welding machines helps to increase efficiency. In models with a power factor of over Cos φ 0.95, almost all of the energy drawn from the grid for welding is used for this very purpose.
State-of-the-art inverter machines consume less power than machines that are already somewhat outdated. A series of tests carried out by Fronius at the beginning of 2024 can confirm this—a modern inverter model was directly compared with an inverter machine with slightly older technology in industrial operation. The results were clear: the older inverter welding machine consumes 255 kWh more electricity per year.
In terms of the electricity costs of the individual machine, this may seem rather negligible. But with countless welding machines in use around the world, the higher consumption of 255 kWh per year does make a difference in terms of overall energy consumption, the required power plant capacities, and the energy costs.
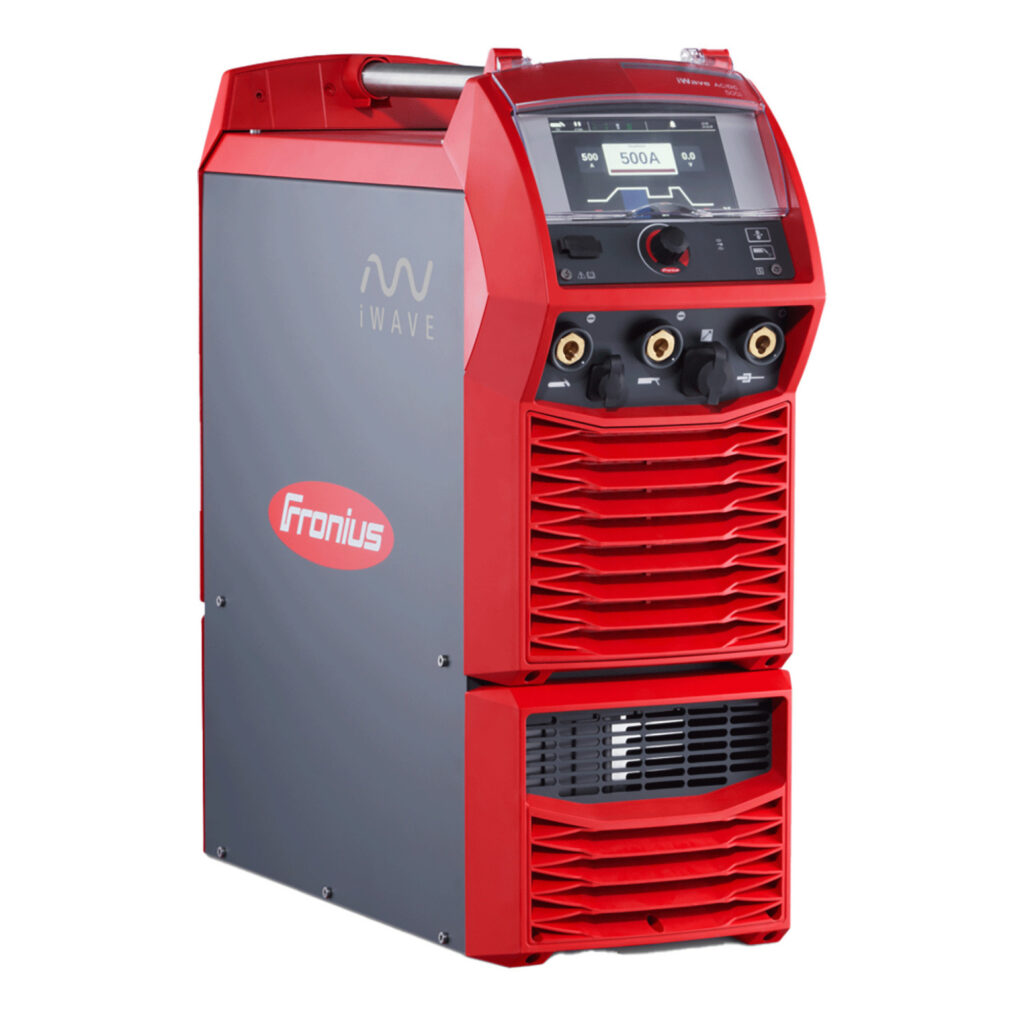
Digitalization enhances energy efficiency
Although the further development of hardware continues to play an important role in welding technology, significant software innovations are now also being introduced. Digital innovations form the basis for new welding methods and processes that make welding more efficient and also have a positive impact on energy consumption.
One example of this is the CMT process developed by Fronius. CMT stands for Cold Metal Transfer, a process that is characterized by a precisely controlled current feed, an extremely stable arc, and a very low heat input. This reduces the distortion of the base workpiece and the volume of waste. All these factors help to save energy.
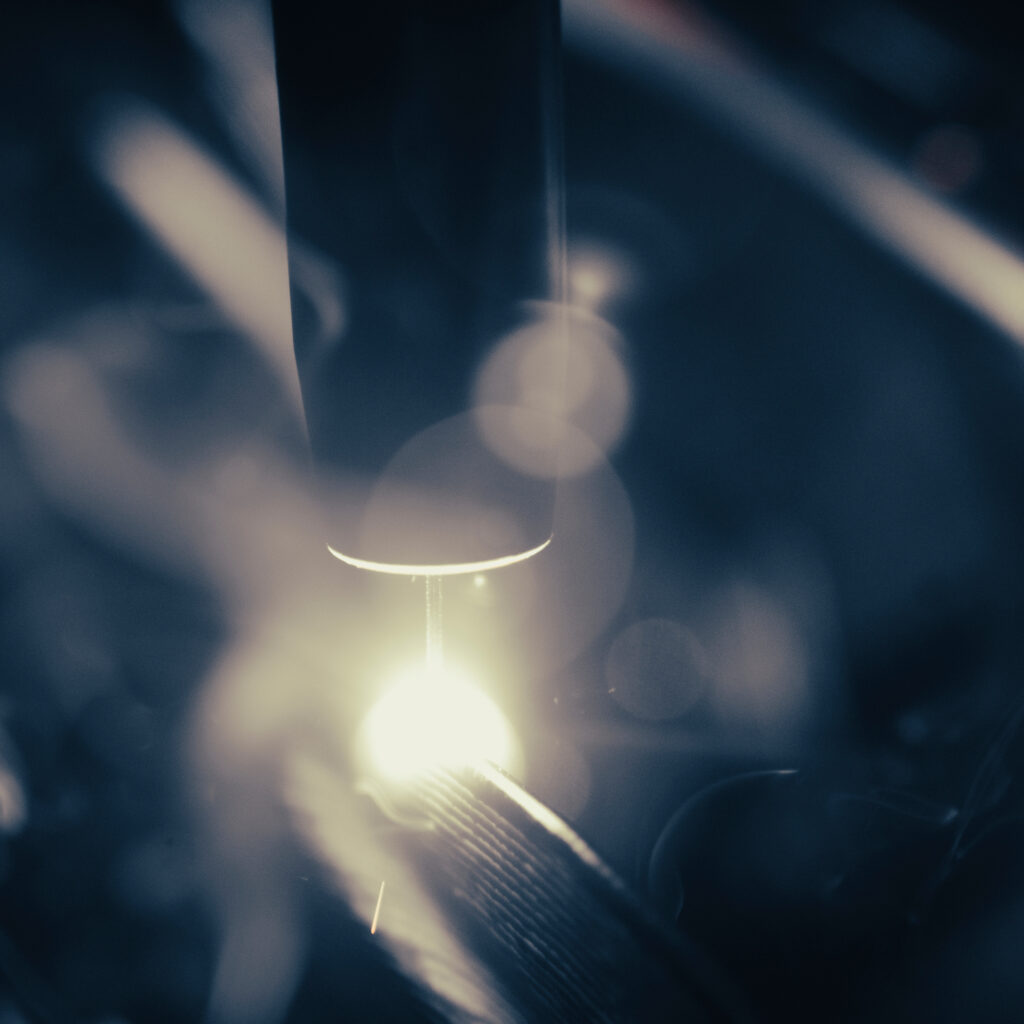
Modern welding processes = faster welding = lower energy consumption
Welding processes that ensure higher welding speeds with the same or improved arc stability also have a positive effect on energy consumption. A good example of this is the Pulse Multi Control (PMC) welding process.
The optimized pulsed arc results in a very stable arc with consistent or even higher seam quality, welding speeds that are 15 to 20% faster, and a correspondingly lower energy input into the base material compared to the conventional pulsed arc. Digital penetration and arc stabilizers form the technical basis for welding processes such as PMC.
Performance-adapted cooling
The welding torch of most high-performance MIG/MAG welding machines is cooled with coolant. Unfortunately, this is not always particularly energy-efficient—in many older welding machines, the coolant constantly circulates at the same speed, regardless of how much energy is introduced into the arc and therefore how much heat is generated at the tip of the welding torch.
With performance-adapted cooling, the cooling is permanently linked to the respective power consumption and as such to the heat that develops at the welding torch. This system cools using only the amount of energy actually needed to deliver optimum welding results, avoiding unnecessary, energy-consuming cooling.
But what more can welders do to conserve energy?
The points set out above all relate to the technical features that an energy-saving welding machine should have, and if welders select a modern and energy-efficient inverter machine then they’ve already made a significant contribution to saving energy.
Beyond this, it’s advisable to set modern welding processes on the machine. These can make welding simpler, higher quality, and usually more energy-efficient too: the cleaner the work of the welding specialists, the less rework required, and the lower the overall energy consumption.
Conclusion
High weld seam quality and saving energy during welding are anything but a contradiction in terms—they go hand in hand. Welders who produce high-quality weld seams efficiently, virtually spatter-free, and in a time-saving manner using modern welding machines not only do an excellent job, they also act sustainably both in ecological and economical terms. And they do so simply by using energy and our natural resources as efficiently and sparingly as possible.
Want to know more about resource-conserving welding? The articles “Welding and sustainability: how do we combine the two?” and “Sustainability at Fronius: what are we doing?” will give you further insights into this area. And if you want to find out how to ensure your welding machine ages more slowly, we recommend the article “8 Anti-aging Tips for Your Welding System”. Enjoy!
No Comments