First off: If you work with a high-quality welding system which has components that are easy to maintain and repair, it will last you a lot longer. However, even with highly sophisticated state-of-the-art technology like this, it is possible to extend the service life in just a few simple steps. We will show you eight simple and practical measures you can take to extend the operating life of your welding system.
Nothing lasts forever, and at some point even the most robust industrial welding system will come to the end of its life. Welding systems are, after all, just machines, and the more carefully you handle them, the longer they will continue to work for. All pretty straightforward so far. But what specific steps can you take to ensure that you get the most out of your welding system for as long as possible?
1) Check Wear Parts Regularly
The essential wear parts in a MIG/MAG WELDING system are the contact tube (or contact tip), the hose core, and the gas nozzle. Quality welding systems for industrial applications are usually designed so that they cannot be harmed by damaged wear parts. The device or the corresponding function switches off automatically before any damage can occur and an error message is displayed.
However, those wanting to keep equipment costs down should not rely on this entirely as, for example, damage can occur if the wirefeeder no longer works properly due to a clogged contact tip and a weak motor heats up and wears out more quickly. Damage can also occur if the welding wire passes through a broken inner liner and damages the pipes with the cooling water or even the power cables that run through them.
As a general rule, the more regularly you check the condition of the wear parts, the less unplanned downtime there will be, and the longer your welding system will last. Find out what steps you can take to extend the service life of wear parts in this article: Wear parts in MIG/MAG welding: Four effective measures to make savings with contact tips and gas nozzles.
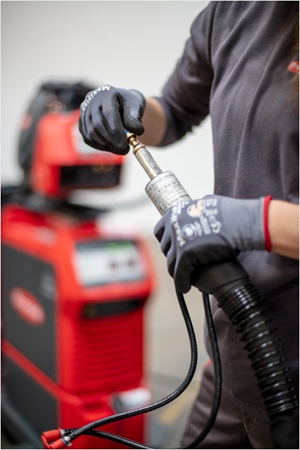
2) Check the Coolant Level
High-performance MIG/MAG and TIG welders are usually liquid-cooled. Welders should get into the habit of regularly checking the level of coolant in their devices and refilling the coolant before the minimum limit is reached. This is important for two reasons:
On one hand, this prevents downtimes, because it avoids the need to top up the coolant at inconvenient times, such as during the night shift. On the other hand, if you are prepared, you will always have the right coolant to hand.
3) No Water, No Cola: Use the Correct Coolant
Using the right coolant is crucial for the service life of a welding system’s cooling system. In principle, only coolants recommended by the manufacturer should be used. It is better to avoid improvising with dubious alternatives, which can range from demineralized water to cola.
But why does using the wrong coolant shorten the service life of the welding system, and why might something seemingly innocuous like pure water cause damage?
Cooling water in general: Essentially, you should avoid using any type of water as a coolant, because the particles, salts, and mineral molecules contained in the water cause pipes and seals to corrode in the long term.
Hard tap water—condensed water: The use of water above a certain degree of hardness causes the pipes the heated cooling water flows through to slowly clog up due to lime or calcium carbonate deposits. In welding systems, increasing calcification of the pipes has a negative effect on the circulation of cooling water and thus on the cooling process.
Algae formation: When tap water is used, algae can also eventually form in the tank. Algae formation is usually noticeable due to a greasy film that forms over time on the bottom and on the walls of the tank. In the cooling circuit, these deposits can damage the cooling system pump, as well as other components.
Good coolants for welding systems have the following characteristics:
- Protection against corrosion
- Incombustible
- Frost-proof (in Central Europe up to min. –10 degrees)
- Environmentally friendly disposal
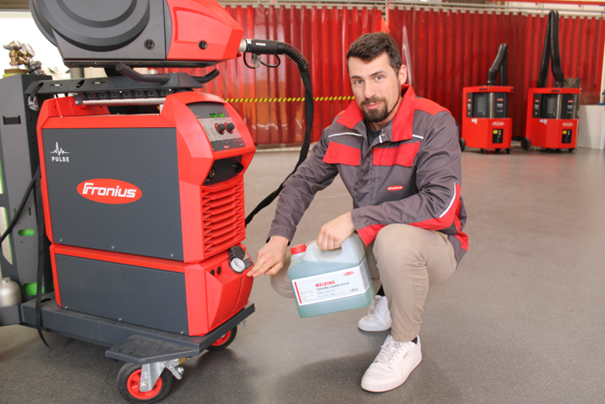
4) Check Pump Function
The coolant pump is the central element of any cooling system that works with liquid. It therefore makes sense to regularly check that this key part is working properly. A faulty cooling circuit or a malfunctioning pump can significantly affect the service life of welding systems, especially since heat that is not dissipated attacks the entire system.
It is easy to check whether the cooling circuit of the welding system is working by checking whether the pump is functional and generating enough return flow. To do this, unplug the return line and run water into a bucket for one minute. If there are at least 1.5 liters in the bucket, the system is functional. At the same time, you should determine whether there is sufficient coolant, especially as running a pump dry can often irreparably damage it.
5) Quick Check on the Fan
Just like almost all devices in which electronic components are installed, welding systems also require a well-functioning ventilation system. If this goes unnoticed, electronic components such as printed circuit boards or control elements may overheat and thus become unusable. Minor malfunctions of the fan that go unnoticed for a long time can be particularly insidious.
For many devices, the fan still runs for a time after switching off in order to remove the remaining heat, and occasionally also the remaining electricity, from the device. After switching off, a simple quick check can be carried out to quickly determine whether the fan is performing its task: This involves either listening for the sound of the fan or checking whether its components are moving.
6) Blow Out: Remove Dust from the Welding System
Excess dust can negatively affect the functionality of mechanical and electronic components in the welding system in the long term, thus affecting the service life of the entire system.
Compressed air is the weapon of choice in the fight against dust. In most cases, it is sufficient to remove dust from the cooling fins of the welding system at regular intervals using air from the compressor to ensure continuous ventilation.
At least once a year, though, appropriately trained and qualified personnel, such as company electricians, should open the welding system and also blow out the interiors. It is particularly advisable to proceed with caution when it comes to delicate components, such as printed circuit boards. The compressed air jet should never be directed at sensitive parts at close range.
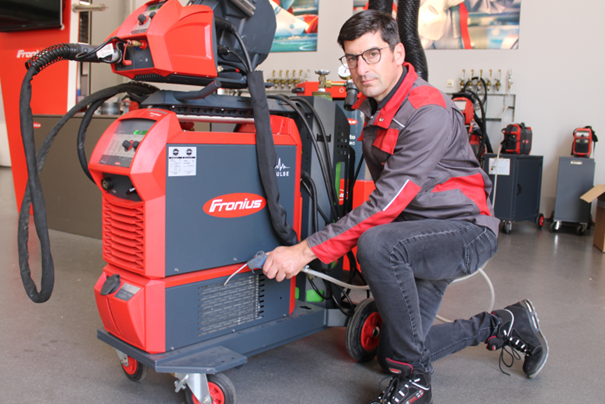
7) Be Good to Your Welding System—Even If You Don’t Need It Right Now
Quality industrial welding systems are actually extremely robust, but even with these, you should pay attention to a few basic points if they remain unused for an extended period:
Avoid overly dusty environments: As mentioned above, excessive dust is not good for your welding system, even if it is out of service for a long time.
Avoid moisture: Do not store your welding system in wet areas or in a humid environment. This can cause corrosion, which damages certain components such as trolleys or housing parts and causes the devices to age faster.
Unplug: Disconnect your welding system from the grid when not in use. In standby mode, a welding system still consumes power. Most importantly, you should pull out the plug to prevent damage to the electronics as a result of overvoltage from possible lightning strikes.
8) Take Advantage of Manufacturer’s Maintenance Packages
The more you know about your welding system, the better: Read the operating instructions and follow the manufacturer’s recommendations. You often learn things here that you didn’t previously know about your welding system.
Good brand manufacturers who focus on quality often have an interest in ensuring that their devices remain usable for as long as possible. The most convenient way to extend the service life of your welding system is to book a maintenance package from your manufacturer. The service teams of the welding technology companies can then also answer very specific questions about care and maintenance on site.
Fronius offers modular maintenance packages with ready-to-use services. The development of durable welding equipment that is easy to repair is part of the Fronius sustainability strategy.
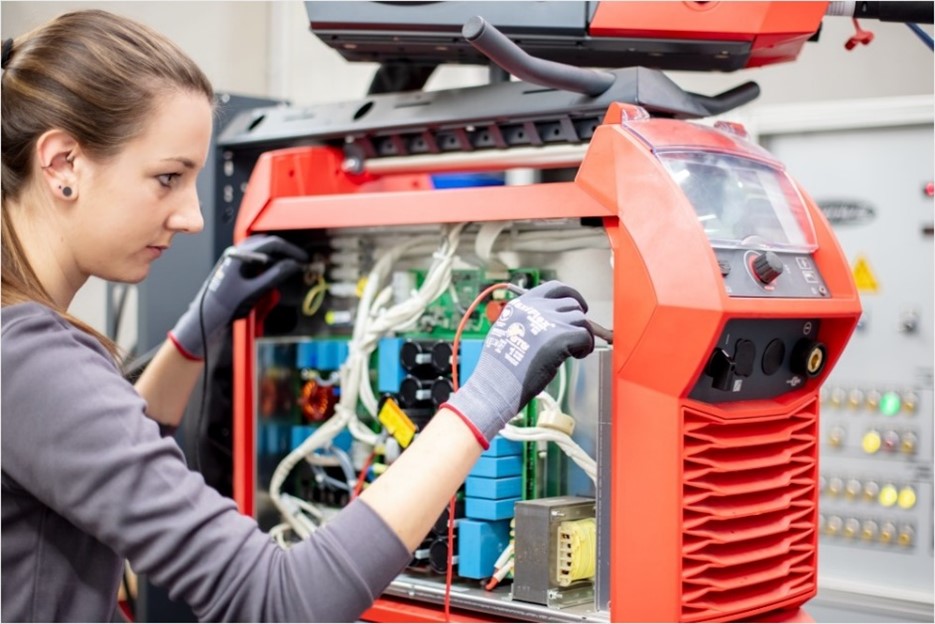
Conclusion: If you choose high-quality equipment from the outset, take note of the measures suggested here and regularly maintain and service your device, there is a good chance that your welding system will continue working for decades.
1 Comment
ArcOne
15. January 2024 at 16:27Thanks for these anti-aging tips!
Also, for heavy dust accumulation, using a vacuum cleaner with a suitable filter before compressed air might be more efficient.