It is clear to see why the number of metal construction companies adopting 3D printing, known as simply WAAM (Wire Arc Additive Manufacturing) in the industry, is on the rise. The growing demand for modern, individualized production facilities is closely followed by the desire for customized single solutions. Time and again, we need non-standard spare parts within the shortest possible time. And in prototype construction, we aim not only to save on tool costs but also to shorten development times. When it comes to meeting all these demands, additive manufacturing demonstrates significant strengths. Component geometries that seemed impossible yesterday are becoming a reality today, layer by layer, with metal 3D printing, precisely when we need them.
WAAM – Less material, less weight, less cost
When comparing metal 3D printing with subtractive processes such as milling, it becomes apparent that Wire Arc Additive Manufacturing consumes significantly less material. The higher the raw material prices, the quicker this type of additive manufacturing pays off.
Elaborate molds, like those required for casting, are also not needed. Instead, we can use modern welding technology to manufacture complex, topology-optimized metal components layer by layer, according to a specific recipe. In technical terms, this recipe is known as an Additive Manufacturing Procedure Specification (AMPS). An AMPS contains everything needed for the perfect “print process”: individual welding instructions (Deposition Procedure Specifications, or DPS), operator and material certificates, as well as the kinematic strategy required for the path planning and motion control of the welding robot.
Material certificates guarantee the production quality of welding wires. Operator certificates ensure that the DED arc robotic welding cells, commonly used in additive manufacturing, are only operated by skilled specialists. DED arc stands for Directed Energy Deposition Arc, which is an arc used for the layer-by-layer melting of welding wire.
“In topology optimization, we aim to ensure the ideal material distribution of components. Specifically, the goal is to reduce weight while maintaining rigidity,” explains metal 3D printing expert Philipp Roithinger, adding: “Typical applications include bionic, nature-inspired structures, like those found in the aerospace sector, for example. Another advantage of metal 3D printing is the ability to produce in a decentralized way. Unlike series production, no production lines are needed regardless of location. Additive manufacturing with welding wire relies on specially equipped robotic welding cells that can be used flexibly worldwide. Today, the use of metal 3D printing is increasing in any application where our aim is to reduce weight, material, costs, and environmental impact in metal construction.”
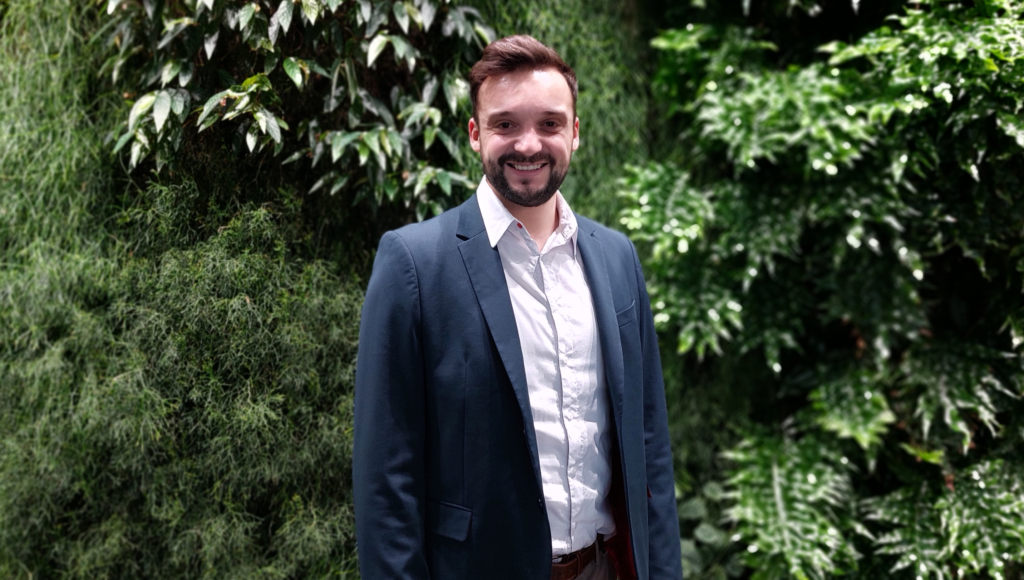
CMT ensures the stable arc essential to metal 3D printing
To achieve the desired quality in additive welding, we need an extremely stable welding process, such as CMT (Cold Metal Transfer). CMT is a “cool” dip transfer arc process that, despite its high deposition rate, keeps the heat input low. This is possible because the droplet detachment is triggered by a reversing wire electrode transition.
In conventional dip transfer arc processes, which are less suitable for WAAM and generate a higher heat input, the wire moves continuously toward the workpiece, unlike in CMT. As soon as the softened wire end touches the weld pool, a short circuit occurs. A large portion of the molten welding wire flows into the weld pool, causing the process known as droplet detachment. During the short circuit phase, the welding voltage drops close to zero, while the current spikes, breaking the short circuit and reigniting the arc.
Droplet detachment and arc reignition are more controlled and require less energy in the CMT process compared to the dip transfer arc process. This is achieved through a backward transition of the wire electrode during the short circuit phase. Depending on the filler metal, shielding gas, and electrode diameter characteristics, the reversing wire transition occurs at a frequency of 50 to 170 Hz.
The heat input generated during CMT welding is up to 33% lower than in conventional dip transfer arc processes. This makes CMT highly suitable for additive welding, where the cyclical deposition of beads causes high heat input. If the component temperature becomes too high, it can degrade material properties and lead to downtime. In such cases, the welding process would need to be interrupted until the weld layers cool down. In CMT, fluctuations in the contact tube distance are less critical, the arc remains stable, and the single-wire system provides an additional degree of freedom in robot programming.
CMT additive pro: targeted heat input for consistent layer build-up
The CMT process supports functions specifically suited for metal 3D printing, such as “power correction.” This function ensures that the electrical power is precisely adjusted to the respective process phase—layer build-up and heat input—while maintaining a consistent deposition rate.
“With our CMT Additive Pro functions, specially developed for additive manufacturing, such as power correction or the Deposition Stabilizer, we can precisely control the power input and thus the height and width of the weld seam,” explains Roithinger.
If a new weld start is required during layer build-up due to the replacement of empty wire drums, this can be a significant source of error. Resulting binding errors or weld seam excesses in the weld start area would massively impair the quality of additively manufactured components. Here, the Pulsed HotStart function provides a solution. When active, it achieves the necessary penetration at the restart in the pulsed arc, maintaining a consistent layer height.
360° service at the Fronius prototyping center
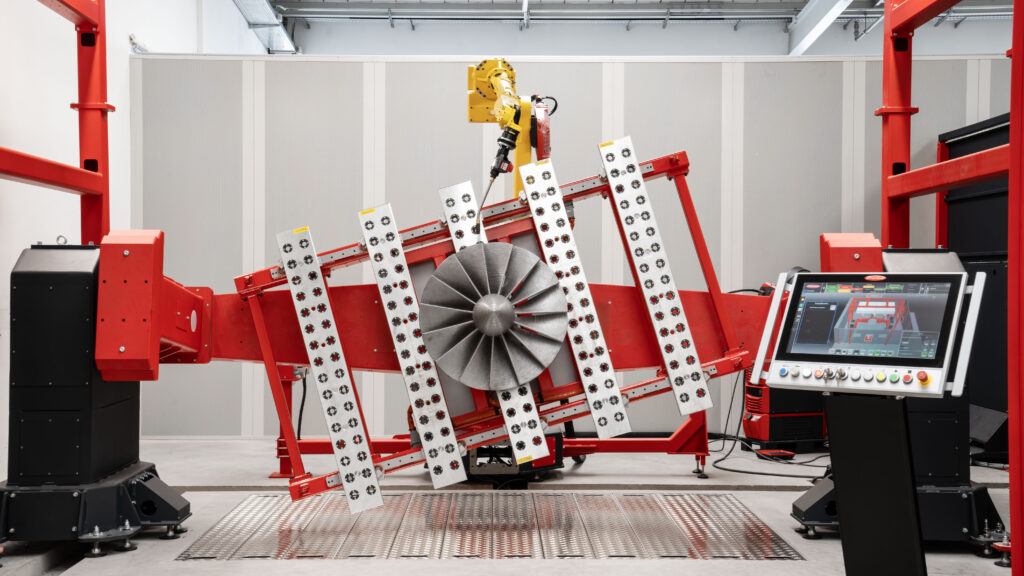
At our prototyping center in Wels, Austria, we offer a comprehensive service package. It includes feasibility studies, tailored solutions for individual customer requirements, process optimization, and prototype production, all in close collaboration with our clients and under strict confidentiality. In prototype construction, we aim to keep the time from development to product maturity as short as possible. To achieve this, we fully leverage the potential of our welding technology.
If necessary, our experts not only support prototype construction but also pre-series production. They assist with a smooth transition into robotic metal 3D printing and provide reliable recommendations on the welding process, cost-effectiveness, quality, and production. The approximately 900 m² prototyping center houses robotic systems with advanced welding, sensor, and measurement technology. There is also a welding lab where non-destructive and destructive testing of components can be performed. Our full-service package includes offline programming, simulations, metallurgical analysis, 3D component measurement, welding data documentation, and much more.
New standards for metal 3D printing
In various industries, the first standards for arc-based additive manufacturing are now emerging. Together with Linde Engineering, which provided the application case, wire manufacturer Migal.co, and TÜV Süd Germany, Fronius participated in the model qualification of an additively manufactured pressure container in the form of a pipe branch. The applicability of the draft standard preEN 13445-14 for the use of additively manufactured pressure containers was assessed.
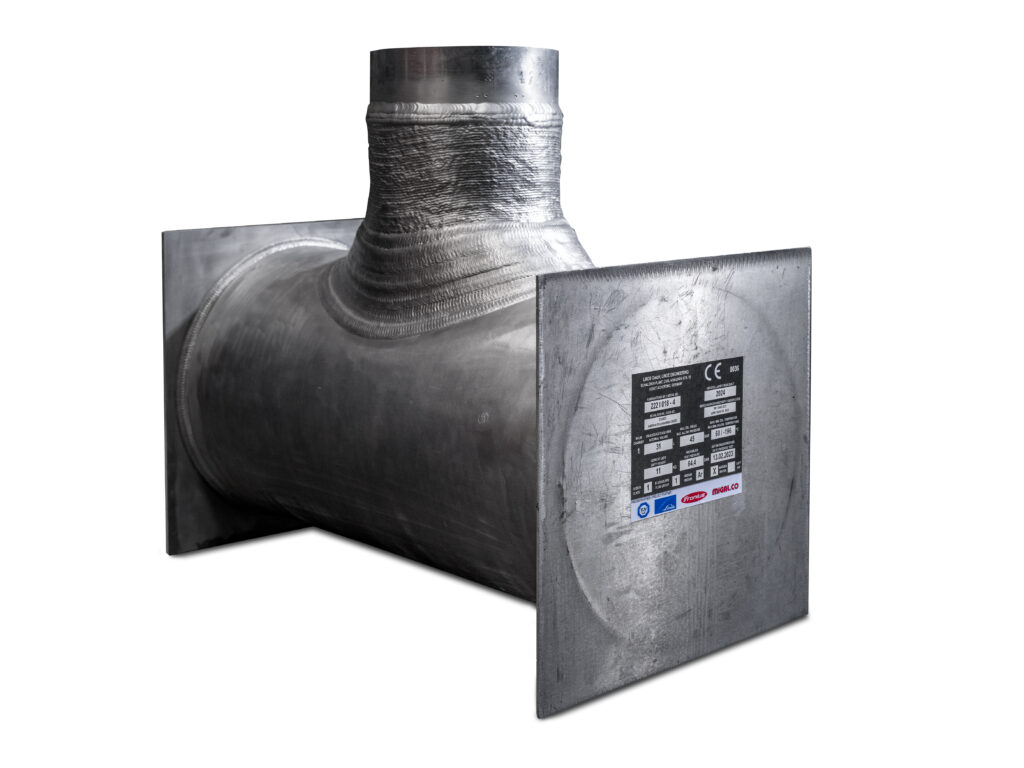
In metal 3D printing, the quality of the materials used is crucial. In this specific case, a naturally hardened aluminum wrought alloy was chosen. Due to its excellent low-temperature toughness down to -273°C, this material, also used in lightweight construction, is particularly well-suited for building pipeline systems.
The aforementioned European draft standard considers the entire value chain for additive manufacturing, including all necessary monitoring details. The aim is to ensure that the fundamental safety requirements defined in the Pressure Equipment Directive are fully met.
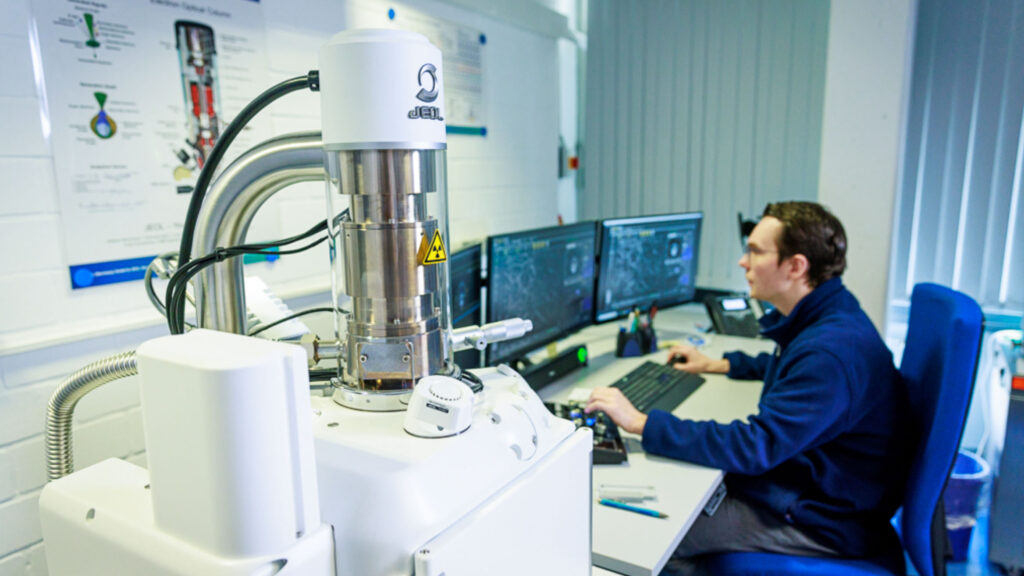
During the model qualification, we reviewed and documented the entire process chain from design, construction, manufacturing, and path planning to process monitoring and final pressure testing.
Detailed information on the model qualification of the pressure container with final CE certification by TÜV Süd is provided in this video: YouTube
1 Comment
Kashish Sambhwani
10. April 2025 at 13:10Incredible insight into how WAAM and CMT are shaping the future of metal 3D printing! The integration of AMPS, CMT Additive Pro, and real-world applications like pressure containers shows the maturity this tech is reaching. At Paanduv, we echo this vision through our DED simulations with AM PravaH. Exciting times ahead for additive manufacturing! 🔧🚀