Nina is getting a taste of her father’s metal construction company for the first time today. The demand for welding specialists is high. Many experienced professionals are gradually retiring, but welding is considered unattractive, hazardous to health, and dirty. Fewer and fewer young people want to learn this important trade. Nina also has her doubts. Work in the welding workshop is quite different to what she imagined. But she is amazed by what she sees next: innovative cobot welding systems wherever she looks.
In her imagination, she pictured people shrouded in smoke. They were dressed like astronauts. They stared at flashing arcs from morning till night. In one hand they held the welding torch, in the other they held a dark hand shield covered with silvery welding spatter. Instead, she steps into a bright, sunlit hall. Various kinds of welding cobots are everywhere.
When she opens the door to the workshop, she is greeted by Patrick Jungblut, a young operations manager. Patrick is a prime example of how much you can achieve at a young age with first-class welder training. “Are people actually welding here?” she asks, her gaze fixed on the strange red boxes. “Those are welding cobots,” Patrick explains with a smile. “These futuristic assistants are revolutionizing welding and making the job not only safer, but also more exciting. The cobots do welding work that demands consistent quality and must be reproducible at all times. This allows welders to focus on the more creative and challenging aspects.”
Modern, flexible equipment to combat the skills shortage
Mobile systems as well as one and two-station solutions are used, depending on the task. Nina is surrounded by high-tech equipment and she’s greatly impressed. She never imagined it like this! The workshop is far friendlier than she feared. She is greeted with smiles from all sides by employees wearing smart, practical work clothes. An extraction system hums quietly in the background, so the atmosphere is not at all stuffy. “Right now I’m fitting a hydraulic cylinder to one of our cobots,” explains Melanie, who recently completed her apprenticeship as a welding specialist. “At first I was very apprehensive about the machines and the materials, but I soon got over that. What I enjoy most is individually programming the machines, because it means that every workpiece is joined perfectly,” says Melanie proudly. In fact, it looks more like a robot center here—no sign of the dark space she always imagined.
Mobile cobot welding cells for large and small components
“Come with me!” calls Patrick and leads her to a nearby welding station. “This is our mobile cobot solution. The great thing is that it’s really flexible. Do you know why?” Nina steps up to the machine and takes a closer look. She sees a table with lots of small holes from which a long, multi-articulated arm rises up. Underneath is a red box. Next to it is a mighty excavator shovel which the cobot arm is lined up with. “I guess you can weld both large and small parts with it,” Nina replies somewhat uncertainly. “Maybe the plate with holes in it could be used to hold smaller parts.”
“Exactly right,” answers Patrick. “You hit the nail on the head. It can be used to weld components ranging from small oil containers to large transport units.” Nina frowns. “But isn’t it dangerous?”
Patrick smiles reassuringly. “When you weld with it, virtually nothing bad can happen if you use it properly. The welding system comes as a complete solution with extraction, a screen, and personal protective equipment consisting of a welding helmet, a welding jacket, and puncture-proof welding gloves. Cobot systems of this type comply with the safety requirements of the European Machinery Directive and are CE-marked.” He doesn’t want to overwhelm Nina with too many facts, but safety is important to him.
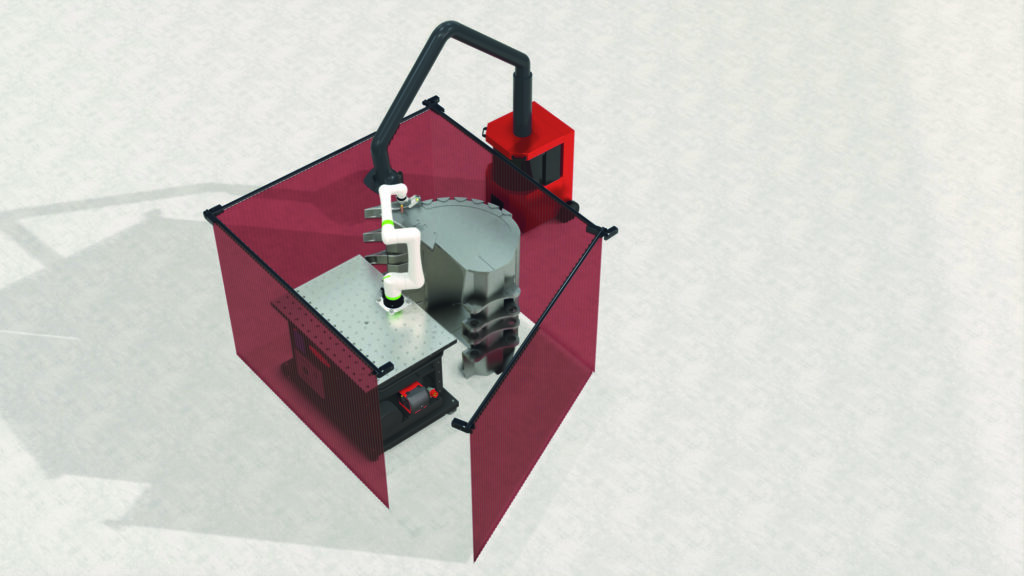
The Machinery Directive 2006/42/EC, published in the Official Journal of the European Union, lays down uniform health and safety requirements within the EU. It paves the way for friction-free trade in machinery within the European Economic Area and applies to manufacturers, operators, and those who place machinery on the market. Countries such as Switzerland, Liechtenstein, Norway, Iceland, and Türkiye have also implemented the Directive in national law. The CE label, which is standard in Europe, guarantees that the equipment produced complies with the Machinery Directive.
Machinery Directive 2006/42/EC
“It may have been different in the past, but today, no welding specialist need have concerns about their health or safety,” says Patrick as they approach a fully enclosed cobot welding cell.
Ideal for small batch sizes
This is a compact single-station system with CE label for welding small components that vary constantly. An operator has just clamped a metal cylinder with longitudinal ribs on a special table that can be rotated and tilted—known as a rotilting positioner. He then programs welding sequences. The whole thing seems very simple. Patrick comes up and seems to guess what Nina is thinking. “As you can see, the welds for this component are very easy to program. And before you start welding, you can simulate the whole process. That way, you can see any collisions with the component right away—those are called interfering contours,” he explains, adding: “If you only encountered them during welding, you would end up with rejects and that would waste money. Look at this monitor here and I will give you a quick video demonstration.”
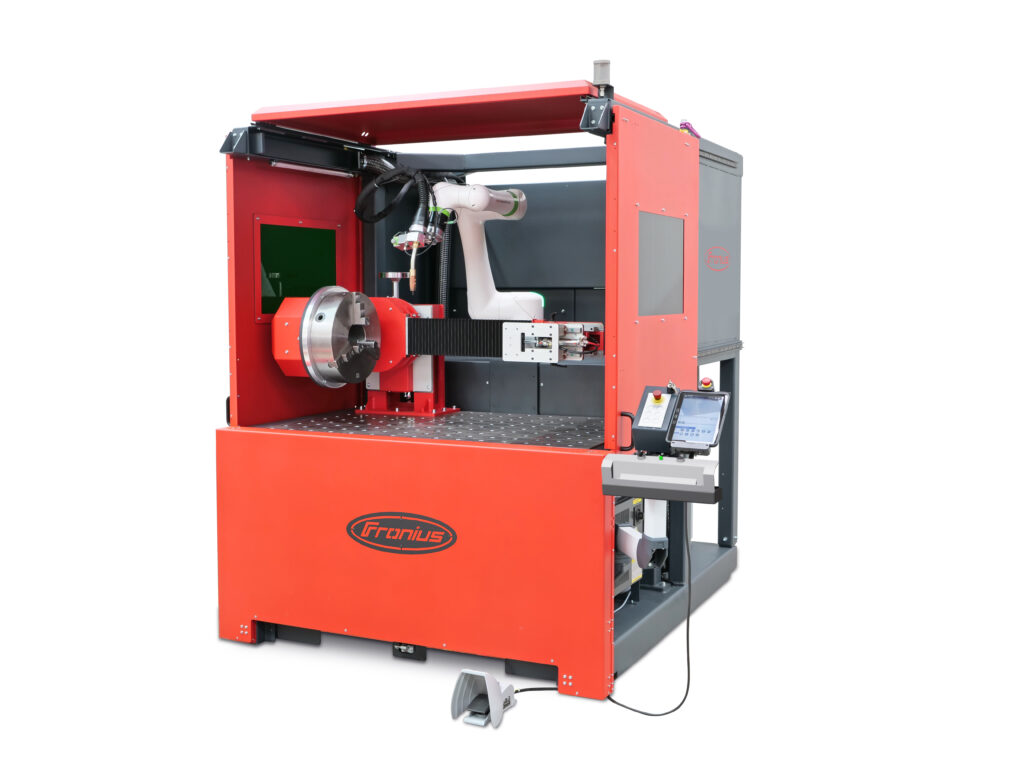
The video shows Nina how easy it is to operate a cobot. The welder drags and drops program icons into the programming field, enters the desired welding speed on the touchscreen, and teaches the cobot by moving the welding torch to the required start and end points. Nina is impressed. Just before the system starts welding, the front screen closes automatically, the integrated welding fume extraction system can be heard to switch on, and flashes start to appear behind the viewing window.
“Manual welding still accounts for maybe 10% of our work,” Patrick continues. “We only weld manually in places the cobot arm can’t reach. But you don’t have to worry—personal protective equipment and extraction systems provide sufficient protection against arc radiation and welding fume.”
By now they have arrived at a large cobot welding cell with two-station operation. Patrick goes to the control center and presses a button, whereupon the two safety doors at the front open automatically.
Set up on one side, weld on the other
As they continue to walk through the workshop, Nina notices many things. She sees different components stored on high shelves—hardly any two seem the same. Forklift trucks move around, transporting metal objects along marked routes. Two men are using a crane to position a component precisely on the left-hand side of a welding system that appears to have two working areas. They wear white hard hats while they do this. Everything looks well organized and safety seems to play a major role.
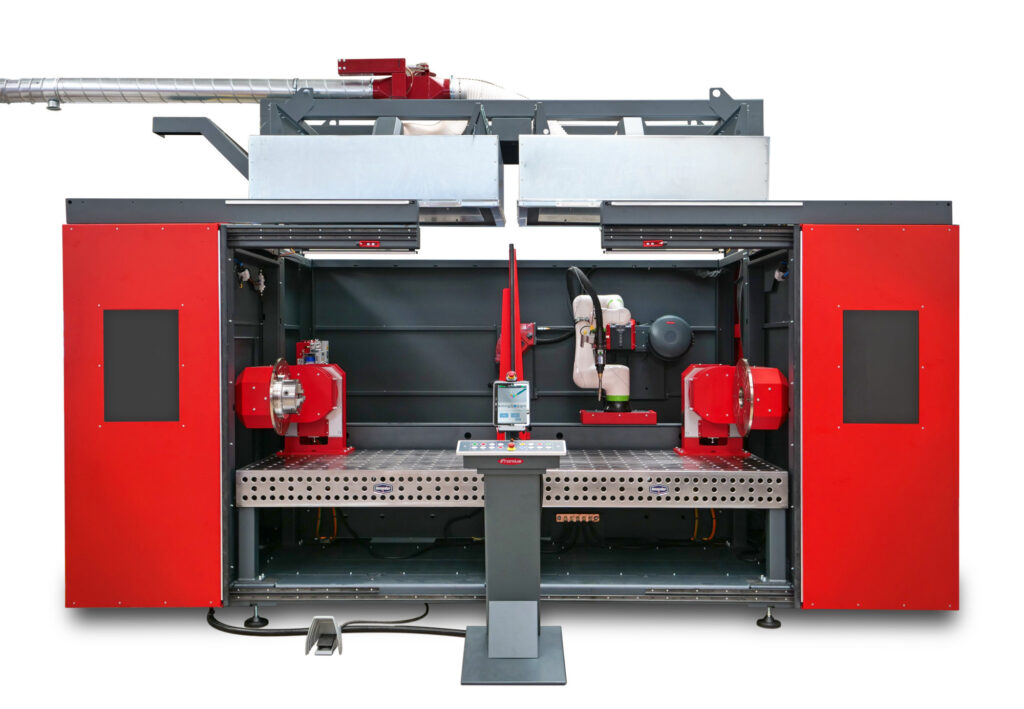
“This cobot welding cell here allows two-station operation,” says Patrick, pointing to the system. “We can weld a component on the right-hand side while we clamp a new one on the left and vice versa. If we remove the central partition wall, we can join large components up to a length of 3 meters and a maximum weight of 2 tons. The cobot uses its longitudinal axis for this and moves along it from A to B.” Patrick points to what looks like a longitudinal rail while the robot is actually moving.
The young operations manager explains to Nina that creating welding programs is not rocket science for experienced welders. You set the start, end, and positioning points, define the necessary parameters, simulate the welding sequence, and start the welding process.
Nina discovers a control unit with lots of buttons. It looks like her little brother’s games console—he loves programming toy robots. Patrick explains that it really is a robot controller. “We use it to program complex sequences involving clamping devices, for example,” he explains.
Nina also learns that the two enclosed cobot welding cells CWC-S and CWC-D can be switched from cobot to robot mode. This allows far higher speeds: instead of 250 mm/s in cobot mode, up to 2 m/s are possible in robot mode. There are no safety issues, as both systems are fully enclosed.
Welding technology at its best
Nearing the end of the tour, Nina learns more about the cobots’ welding equipment. All of them can be equipped with advanced Welding Packages such as Low Spatter Control (LSC), Pulse Multi Control (PMC), or the world-famous Cold Metal Transfer process (CMT). It almost goes without saying that all systems are equipped with innovative welding machines such as TPS 400i Push, CMT, or iWave CMT.
Patrick continues the conversation: “I hope today was an exciting first taster day for you. Welding is nowhere near as unattractive as some people think—quite the opposite, in fact. Of course, you start your training with manual welding, but once you have mastered this, you have the opportunity to gradually expand your skills, moving on to cobot and robot welding. Offline programming of welding sequences using a laptop or PC is especially attractive. You can also do this in the office or working from home.”
Nina asks: “Do all the cobots come from the same company? They look so similar.” Patrick replies: “Yes, absolutely. We’ve been using Fronius welding systems for a long time. They offer us advanced technology and they’re also reliable and safe.”
At the end of an exciting day, Nina even gets to make her first weld. She puts on 3D glasses and uses a futuristic device called the Welducation Simulator. It immediately reminds her of gaming with her friends. She thinks it’s great. Patrick looks over her shoulder and says: “Wow, Nina, you have genuine talent—that looks really good!”
Nina is thrilled and thinks: “Perhaps this could really be my new job!”
No Comments