The heavy duty or high-performance welding process is mainly used for welding huge components, such as combine harvester wheel rims, excavators, telescopic handlers, or truck semi-trailers. The high welding speeds typically used for these processes enable both long weld seams and low-spatter joining. Read on to find out what exactly heavy duty welding is, how the process arose, and the applications and materials suitable for use with this welding process.
What is Heavy Duty Welding?
Gas metal arc (GMAW) heavy duty welding involves one or more solid wires with a diameter of 1.0 mm or 1.2 mm. Today, we class a process as heavy duty or high performance if more than 15 m of wire is fed per minute. Processes with larger wire diameters, of 1.6 mm or 2.0 mm for example, are also high-performance welding processes if the deposition rate – the weld metal that is melted-off – is more than 8 kg per hour. To melt off 8 kg per hour at a wire speed of 15 m per minute, you need a wire diameter of at least 1.2 mm.
However, heavy duty welding with a wire electrode is not just about unreeling more wire; two other aspects also play a decisive role: the gas mixture and a special water-cooled welding torch with a longer stick out. Stick out is the distance between the end of the contact tip and the workpiece surface (see diagram), which is greater than with the conventional gas metal arc welding process. This means that a higher wire speed can be set for any given amperage, which in turn enables higher deposition rates. The cooling system which directly cools the gas nozzle also guarantees a high duty cycle at full power.
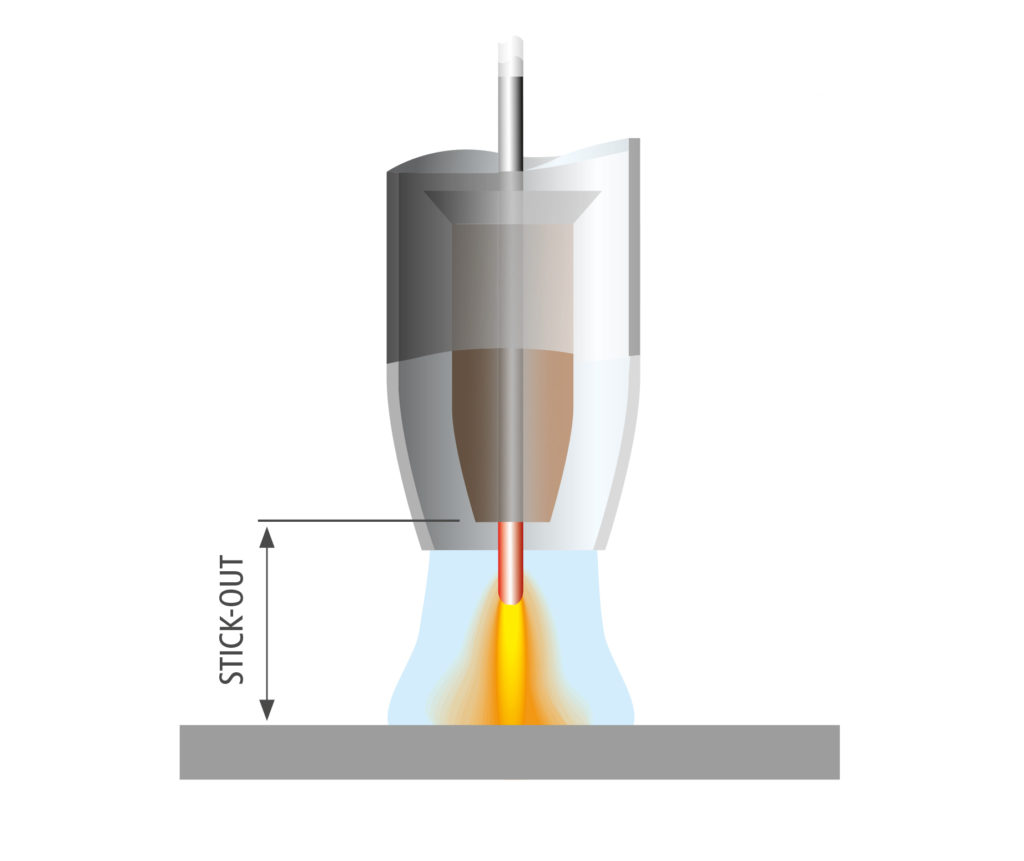
The History of the Welding Process
If you take a look at the history of heavy duty, you will see that welders used standard shielding gases and a GMAW wire electrode up until the 1980s. It is thanks to John Church, a Canadian engineer, and his invention of the TIME process, that we are able to weld joins even faster with the high-performance welding process. TIME stands for Transferred Ionized Molten Energy, which means the transfer of high amounts of energy to the molten filler metal in an ionized plasma. Church developed a four component shielding gas made of argon (Ar), carbon dioxide (CO2), oxygen (O2), and helium (He) for this process. The key to the high welding speed is that with the TIME welding process, very high wire speeds of up to 30 m per minute can be achieved with a longer stick out. It is thus not a matter of chance that TIME also stands for the (welding) time as a nod to the cost-effectiveness of the joining process.
However, the four-component gas that was used initially is hardly ever used today. The gas was very expensive because it is complex to produce. Not only that, but similar effects can be achieved with fewer gas components if you have the right equipment. As a result, a low-cost three-component gas mixture has prevailed.
From Double-Wire to Tandem Technology
Several solid wires can also be welded with the high-performance welding process. Double-wire welding emerged in the 1990s. This involves two welding systems connected to a welding torch with two holes in the contact tip. Simultaneous melting of two wire electrodes is also more cost-effective, as two weld pools cool quicker than one large pool. However, there are some drawbacks to conventional double-wire welding. The arcs cannot be controlled individually; if one wire short circuits, the energy is transferred to the second wire, resulting in an unstable process.
Several solid wires can also be welded with the high-performance welding process. Double-wire welding emerged in the 1990s. This involves two welding systems connected to a welding torch with two holes in the contact tip. Simultaneous melting of two wire electrodes is also more cost-effective, as two weld pools cool quicker than one large pool. However, there are some drawbacks to conventional double-wire welding. The arcs cannot be controlled individually; if one wire short circuits, the energy is transferred to the second wire, resulting in an unstable process.
Tandem welding enables arcs to be controlled individually thanks to two electrically isolated contact tips in the welding torch.
Where is Heavy Duty Welding Used?
The high-performance welding process is used in any application that calls for high welding speeds and deposition rates. Long weld seams, multiple runs, high volume components, and overlay welding of large areas are best tackled with the tandem process – whether it be in steel or container construction, shipbuilding, or mechanical engineering. The tandem process can be used manually or it can be automated and it is particularly suitable for steel, chrome-nickel, and aluminum applications – however, it is mainly used for steel.
The challenge with heavy duty welding lies in controlling both arcs. To do so, the right parameters must be set and it is important that the welding torch is cooled well to achieve high-quality seams at a high rate of output.
In addition to single-wire, double-wire, and tandem technology, there are other high-performance welding processes: LaserHybrid welding is a combination of a laser and the GMAW process. Find out more about LaserHybrid welding in our blog post of the same name.
Are you in the market for a powerful and reliable tandem welding system? Then take a look at our TPS 600i. It can handle continuous welding operations at 500 amperes.
And if you want to know if high-performance welding is the right choice for your application, simply contact our experts – let us help you with our application know-how. We can also carry out welding tests with you.
No Comments