Das Hochleistungs-Schweißverfahren wird vor allem beim Schweißen von massiven Bauteilen, wie zum Beispiel Mähdrescher-Felgen, Baggern, Teleskopladern oder LKW‑Sattelaufliegern, verwendet. Die bei diesem Prozess typischen hohen Schweißgeschwindigkeiten ermöglichen nicht nur lange Schweißnähte, sondern auch ein spritzerarmes Fügen. Was genau Hochleistungsschweißen ist, wie der Prozess entstanden ist und für welche Anwendungsfelder und Materialien sich das Verfahren eignet, lesen Sie in unserem Blogartikel.
Was ist Hochleistungsschweißen?
Beim Metall-Schutzgas (MSG) Hochleistungsschweißen kommen ein oder mehrere Massivdrähte mit 1,0 mm oder 1,2 mm Durchmesser zum Einsatz. Heute spricht man von Hochleistungsschweißen, wenn pro Minute mehr als 15 m Drahtvorschub gefördert wird. Prozesse mit größerem Drahtdurchmesser, wie 1,6 mm oder 2,0 mm, zählen ebenso zum Hochleistungs‑Schweißverfahren, sofern die Abschmelzleistung, also das abgeschmolzene Schweißgut, mehr als 8 kg pro Stunde beträgt. Um bei einer Drahtvorschubgeschwindigkeit von 15 m pro Minute 8kg pro Stunde abzuschmelzen, ist ein Drahtdurchmesser von mindestens 1,2 mm notwendig.
Beim Hochleistungsschweißen mit einer Drahtelektrode ist allerdings nicht nur wichtig, mehr Draht abzuspulen, es sind auch zwei weitere Komponenten entscheidend: die Gasmischung sowie ein speziell wasser-gekühlter Brenner mit einem längeren Stick-out. Der Stick-out bezeichnet den Abstand zwischen dem Ende des Kontaktrohrs und der Werkstückoberfläche (siehe Grafik), der im Gegensatz zum herkömmlichen MSG-Verfahren höher ist. Dadurch kann bei gleicher Ampere-Anzahl mehr Drahtvorschub eingestellt werden, was wiederum eine höhere Abschmelzleistung zulässt. Das Kühlsystem, das die Gasdüse direkt kühlt, garantiert zudem eine hohe Einschaltdauer bei voller Leistung.
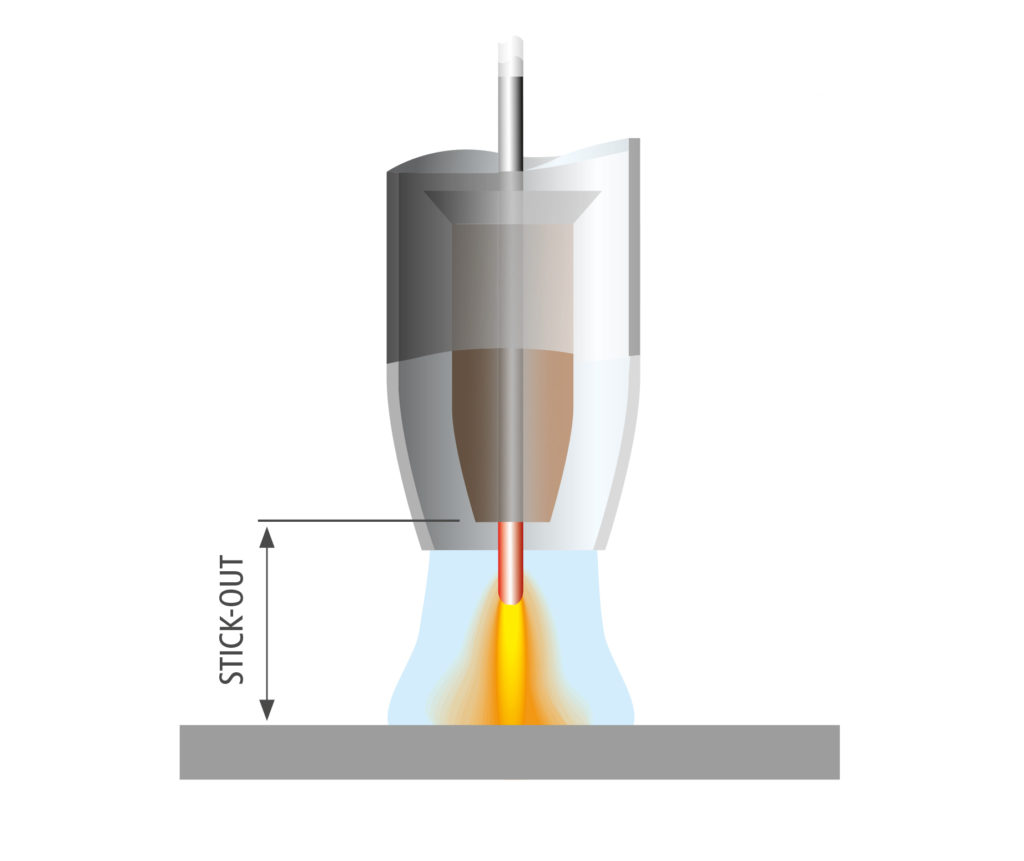
Die Geschichte zum Verfahren
Ein Blick in die Geschichte des Hochleistungsschweißens macht deutlich, dass bis in den 1980er Jahren mit Standardschutzgasen und einer Drahtelektrode MSG geschweißt wurde. John Church, einem kanadischen Entwickler und seiner Erfindung des TIME-Prozesses ist es schließlich zu verdanken, dass mit dem Hochleistungsschweißprozess noch schneller gefügt werden kann. TIME steht für Transferred Ionized Molten Energy, und bedeutet die Übertragung von hoher Energie auf den geschmolzenen Zusatzwerkstoff in einem ionisierten Plasma. Dafür entwickelte Church ein 4‑Komponentenschutzgas aus Argon (Ar), Kohlenstoffdioxid (CO2), Sauerstoff (O2) und Helium (He). Ausschlaggebend für die hohe Schweißgeschwindigkeit: beim TIME‑Verfahren lassen sich bei längerem Stick-Out sehr hohe Drahtvorschubgeschwindigkeiten bis zu 30 m pro Minute erreichen. TIME steht also nicht umsonst auch für die (Schweiß-) Zeit, die auf die Wirtschaftlichkeit des Fügeverfahrens anspielen soll.
Das anfangs verwendete 4-Komponentengas wird heute allerdings nur noch selten verwendet. Die aufwändige Herstellung machte das Gas sehr teuer. Zudem lassen sich mit der richtigen Geräteausrüstung bereits mit weniger Gaskomponenten ähnliche Effekte erzielen. Damit hat sich das preiswerte 3-Komponentengasgemisch auf dem Markt durchgesetzt.
Von Doppeldraht- zu Tandemtechnologie
Beim Hochleistungs-Schweißverfahren können auch mehrere Massivdrähte verschweißt werden. Das sogenannte Doppeldraht-Schweißen entwickelte sich in den 1990er Jahren. Zwei Schweißsysteme angeschlossen an einen Brenner mit zwei Bohrungen im Kontaktrohr machen es möglich. Das gleichzeitige Verschmelzen von zwei Drahtelektroden ist außerdem wirtschaftlicher, denn zwei Schmelzbäder kühlen schneller ab als ein großes. Das Prinzip des konventionellen Doppeldrahtschweißens hat allerdings ein paar Mankos: Die Lichtbögen sind nicht einzeln regelbar; kommt es bei einem Draht zu einem Kurzschluss, geht die Energie auf den zweiten Draht über, was den Prozess instabil werden lässt.
Das erst später entwickelte Verfahren des Tandemschweißens ermöglicht hingegen die Lichtbögen individuell zu kontrollieren. Zwei elektrisch voneinander isolierte Kontaktrohre im Brenner, auch zwei unabhängige Potentiale genannt, machen es möglich. Der Anwender kann beispielsweise die Lichtbögen jeweils mit einer anderen Leistung versehen. Das Prinzip des Doppeldrahtschweißens wird heute oft mit dem Tandemprozess gleichgesetzt – obwohl sie sich verfahrenstechnisch deutlich unterscheiden.
Wo wird Hochleistungsschweißen eingesetzt?
Das Hochleistungs-Schweißverfahren kommt überall dort zum Einsatz, wo hohe Schweißgeschwindigkeiten und hohe Abschmelzleistungen gefragt sind. Auch lange Schweißnähte, Mehrlagen, großvolumige Bauteile und das Auftragsschweißen großer Flächen sind bestens mit dem Tandemverfahren zu bewältigen – sei es im Stahl-, Schiffs-, Maschinen- oder Behälterbau. Der Tandemprozess ist sowohl mechanisiert als auch automatisiert realisierbar und eignet sich speziell für Stahl-, Chrom-Nickel- und Aluminium‑Anwendungen; primär wird jedoch Stahl bearbeitet.
Die Herausforderung beim Hochleistungsschweißen liegt vor allem darin, beide Lichtbögen zu beherrschen. Dafür müssen die richtigen Parameter eingestellt und nicht zuletzt der Brenner gut gekühlt sein, um qualitative Nähte bei hoher Leistung zu erzielen.
Neben der Eindraht-, Doppeldraht- sowie Tandemtechnologie gibt es weitere Hochleistungs‑Schweißverfahren: Das Laser-Hybrid-Schweißen ist eine Kombination aus einem Laser und dem MSG-Prozess. Mehr zum Thema Laser-Hybrid lesen Sie im gleichnamigen Blogartikel.
Sie suchen ein leistungsstarkes und zuverlässiges Tandem-Schweißsystem? Dann werfen Sie doch mal einen Blick auf unsere TPS 600i. Sie schafft einen durchgängigen Schweißbetrieb bei 500 Ampere.
Und falls Sie sich fragen, ob das Hochleistungsverfahren überhaupt das Richtige für Ihre Anwendung ist, kontaktieren Sie einfach unsere Experten. – Wir unterstützen Sie mit unserem Anwendungs-Know-How und führen mit Ihnen Schweißversuche durch.
Keine Kommentare