In the second part of our series on MIG/MAG welding torches, we take a closer look at special versions. The choice of MIG/MAG welding torches in particular is almost unlimited, with a version for every process variant, welding challenge, and personal welder preference.
High-tech welding torch
The more specialized and complex the application and welding process, the more high-tech the welding torch solution.
Key to high-quality push-pull systems in general is that the electric motors of the two wirefeeders are perfectly synchronized. The torch motor actual values must be supplied to the power source in real time. This is the only way for the drive to be precisely adjusted so that the wire ultimately stays rigid.
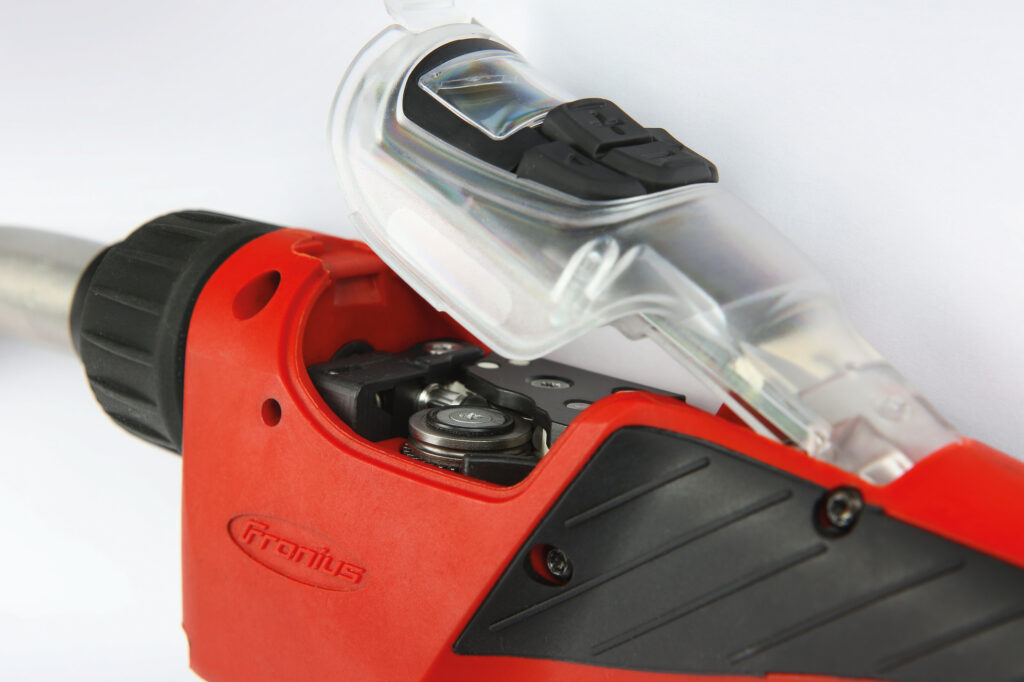
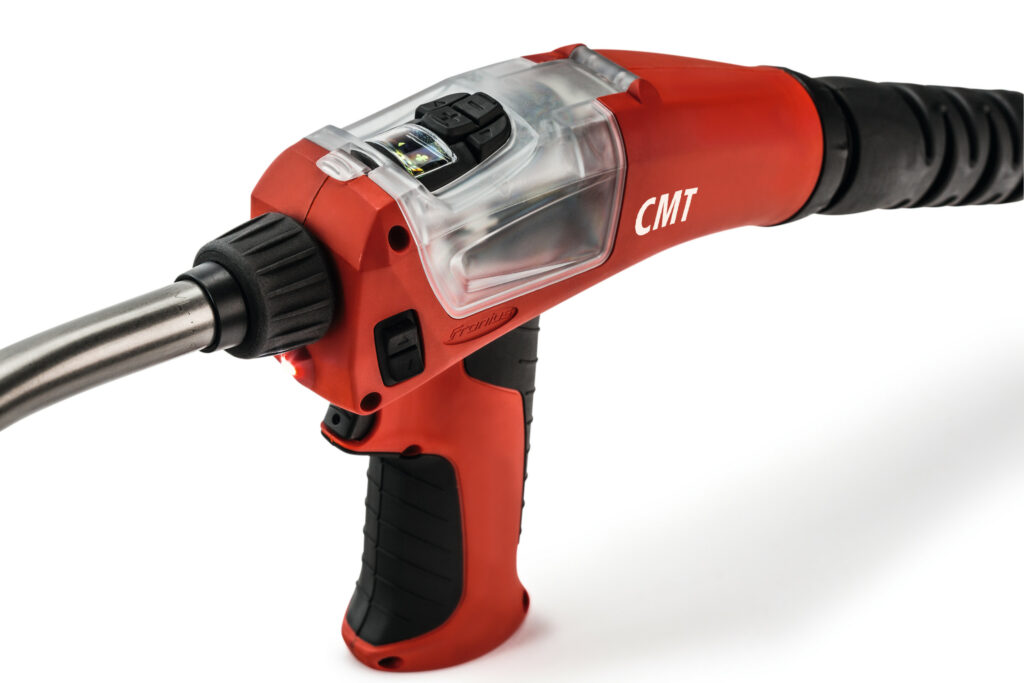
Welding torch with pistol grip: The pistol grip is available for conventional push welding torches, as well as push-pull torches. The choice of version depends entirely on the welder’s preference. The pistol grip can aid handling, especially in the case of heavier welding torches, such as CMT torches.
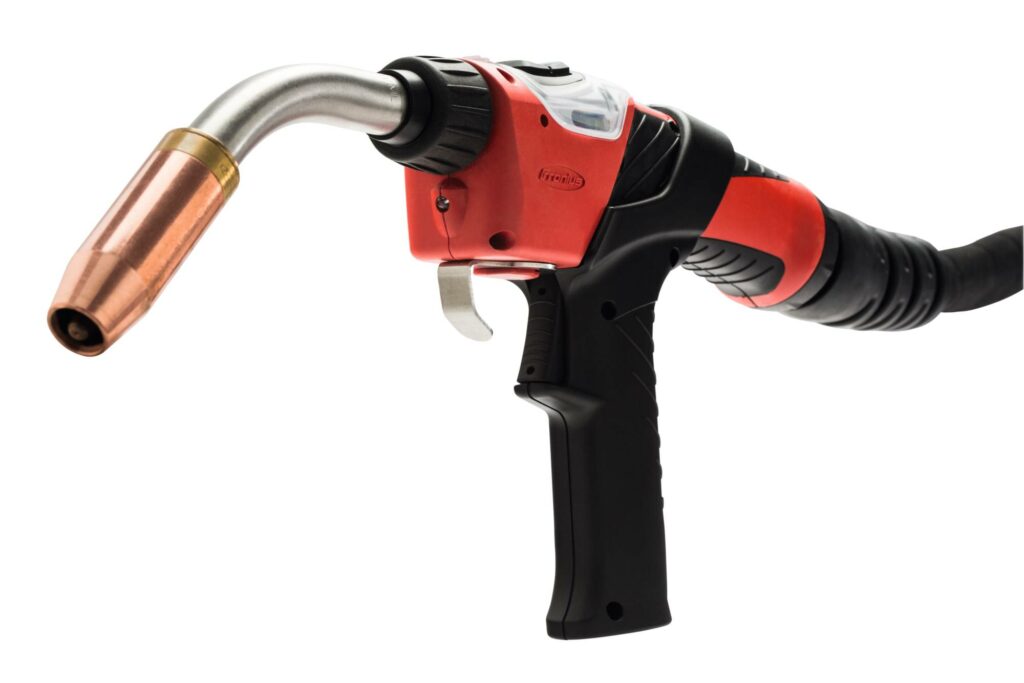
The fume extraction torch: There is a greater awareness these days of health and safety at work, and in welding technology concerns focus primarily around the avoidance of welding fumes. After all, who wants to spend every day working in a fog of foul-smelling fumes? A well-designed fume extraction torch acts like a vacuum cleaner: opening slots immediately behind the gas nozzle extract the air around the weld seam – without affecting the gas shroud around the weld pool. Clean air and a better workplace environment make the job of the welder much more pleasant.
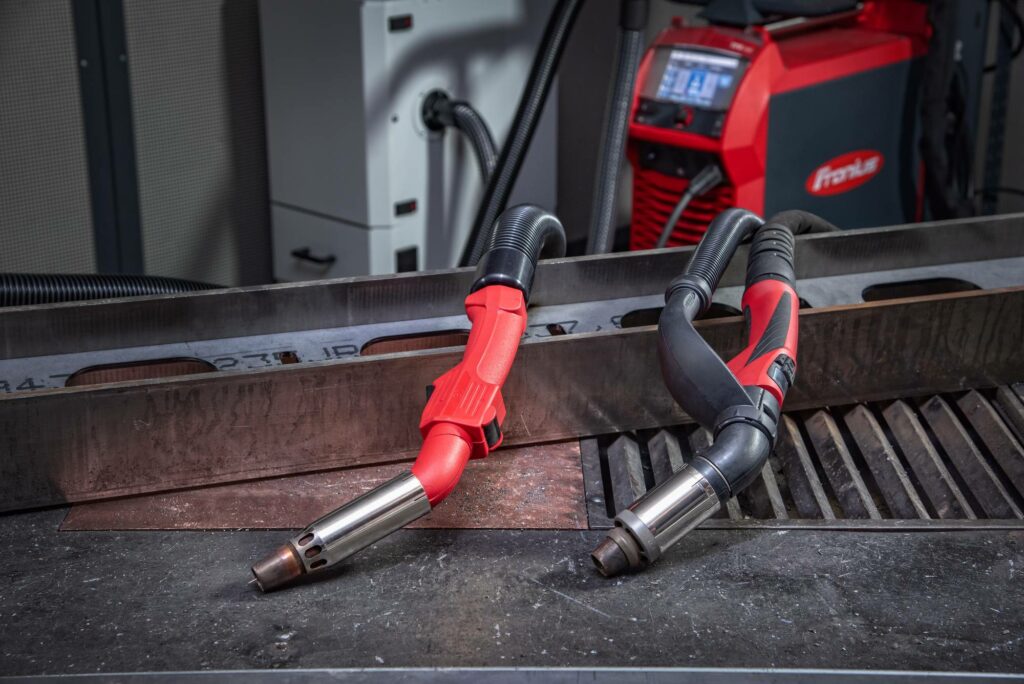
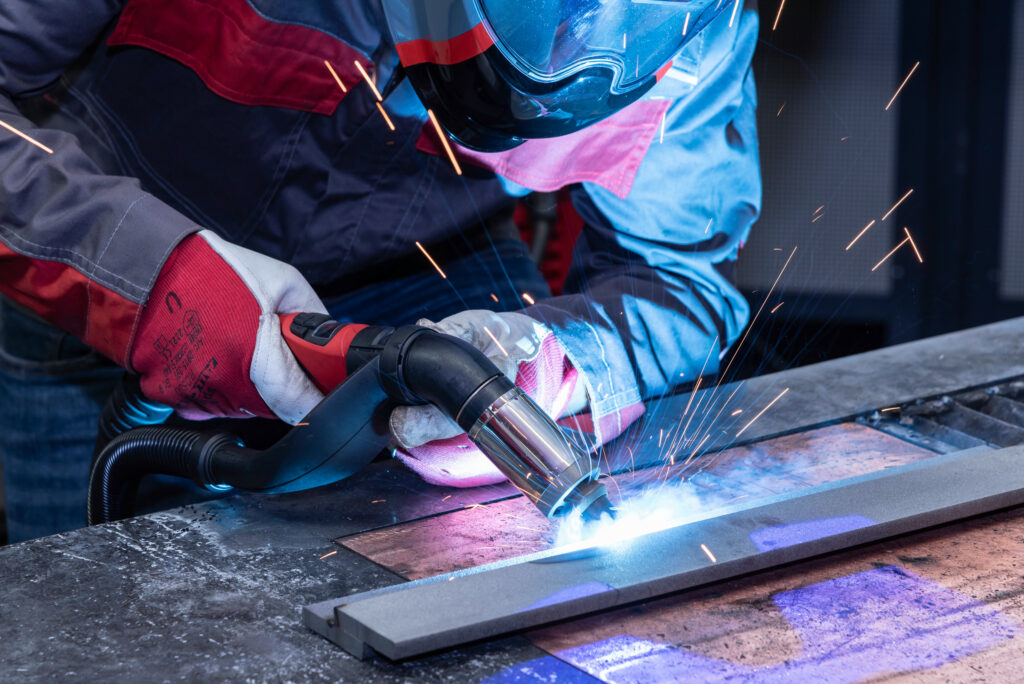
Flexible torch body: Examples of use include where component accessibility is very restricted or the welding position is particularly awkward. It can be connected to the MIG/MAG hosepack using the Mulitlock System. This system utilizes twisted copper pipes in the main that allow the torch body to be bent into more or less any shape within reason, so that the weld seam can be accessed from the best angle. As a result, very special applications can be effected that would be completely impossible for conventional welding torches. However, it is essential to ensure that the torch is bent as few times as possible since the material will be weakened each time the shape is changed. High-quality flex torches can be bent up to 1000 times before they too will need replacing.
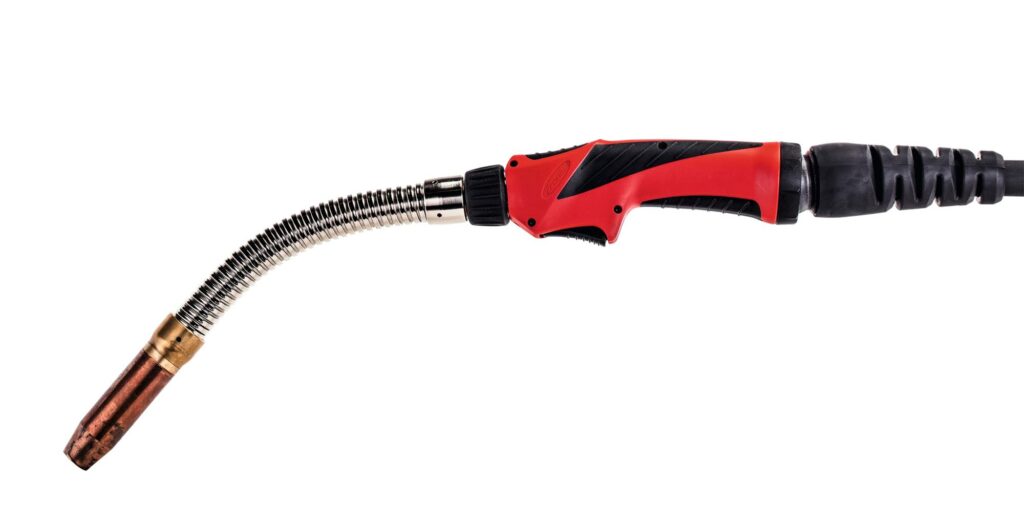
Wearing parts on MIG/MAG welding torches
No matter how high the quality to which standard and special welding torches are manufactured – they will all be subject to diverse material wear over time. These individual components need to be cleaned and replaced regularly to ensure the best possible process stability.
Inner liners: The liner is the sheath inside the torch that guides the welding wire. It gives the wire rigidity, from the point where it emerges from the power source to threading into the contact tip. This prevents any slippage and associated process inaccuracies.
The relevant steel inner liners, CrNi liners, or – for aluminum – combination liners are used to suit the different wires. To protect the fragile aluminum wire, combination liners are made predominantly of lead, ensuring minimal friction.
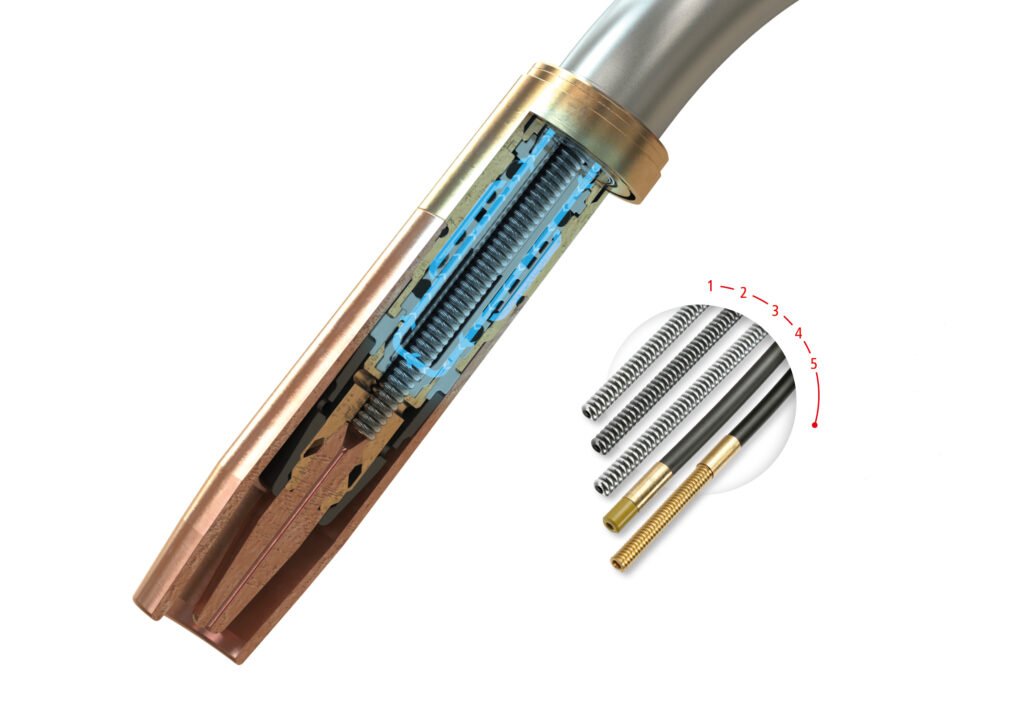
The contact tip sits under the gas nozzle and is responsible for the power transfer to the wire electrode. Since this continually grinds against the copper to make the contact, it will become worn over time. The less effective the contact, the more uneven the arc. For this reason, contact tips should be replaced once they exhibit a certain level of wear. A conventional contact tip can be used for around 120 minutes of on-the-job welding time, which is roughly what a professional welder would aim for in a day.
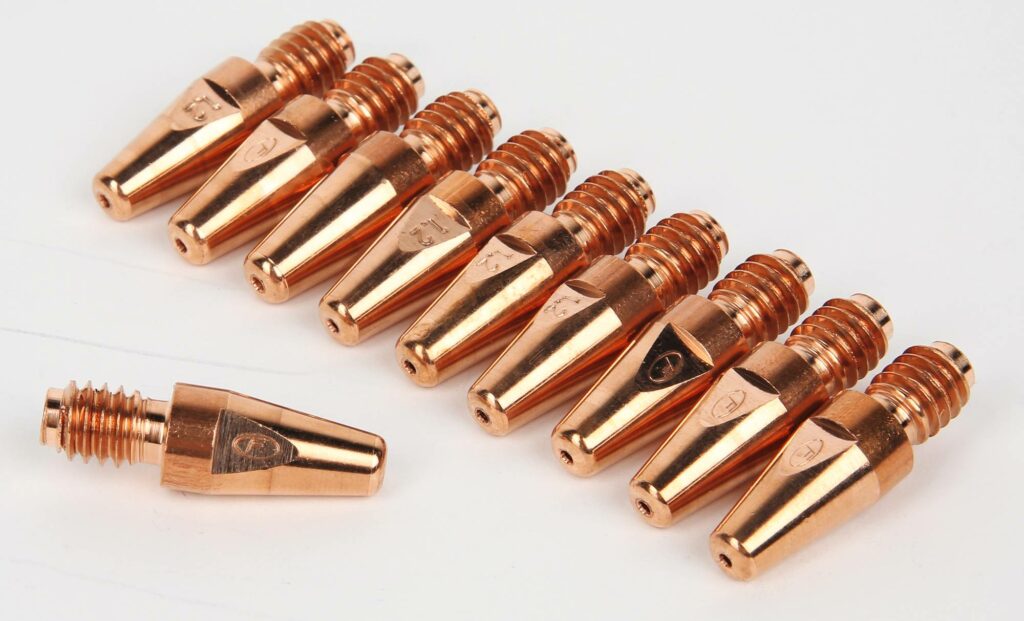
Contact tips are available in all sizes to suit the specific welding torch, power range, and wire diameter. The greater the power input, the bigger the contact tip since the extra material – mostly copper – helps to absorb heat that is generated.
Gas nozzles are available in different versions – usually as copper gas nozzles since copper does the best job of dissipating heat from the arc and the weld pool. Coated nozzles are also used in aluminum welding, because they reduce the amount of spatter adhesion. It is easy to remove any spatter that is still left on the surface using special cleaning brushes.
High-quality gas nozzles are always designed to be screwed rather than clipped on. This ensures shielding gas cannot escape at the connection point and the gas flow is guided perfectly through the nozzle towards the weld pool. Heat dissipation can also be positively influenced by the thread.
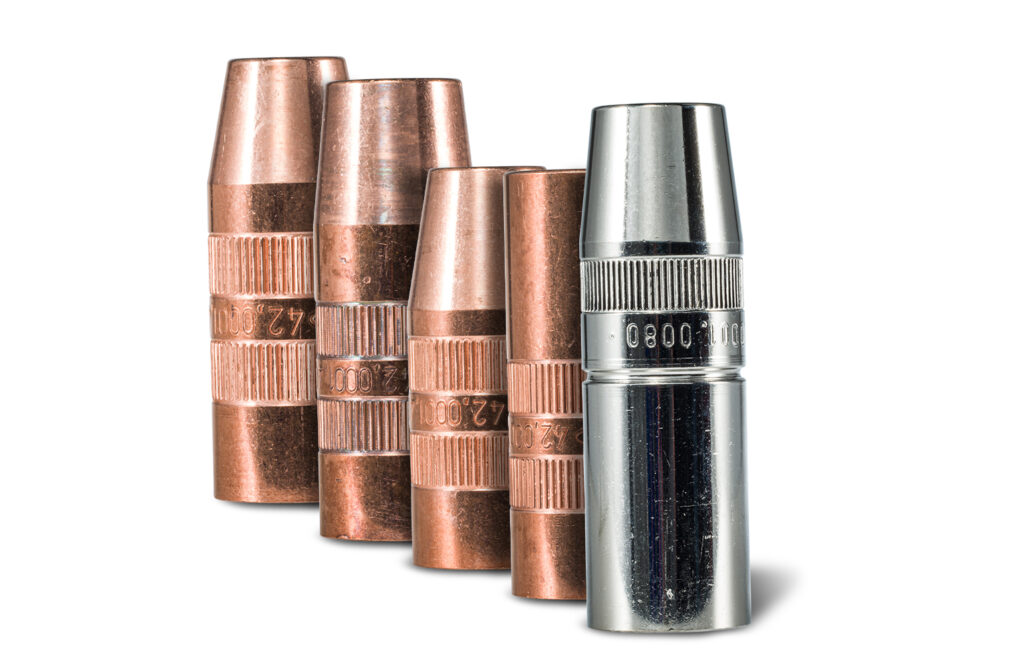
The spatter guard is screwed onto the nozzle fitting, which has holes to allow the shielding gas to flow out. This plastic guard acts in part to insulate the nozzle fitting so preventing any short circuit to the gas nozzle. Its other role is to prevent the gas outlet holes getting choked up with welding spatter. If these holes were to become blocked, the gas flow would be greatly impaired and the gas shroud would be disrupted. This is another reason the spatter guard needs to be cleaned and replaced regularly.
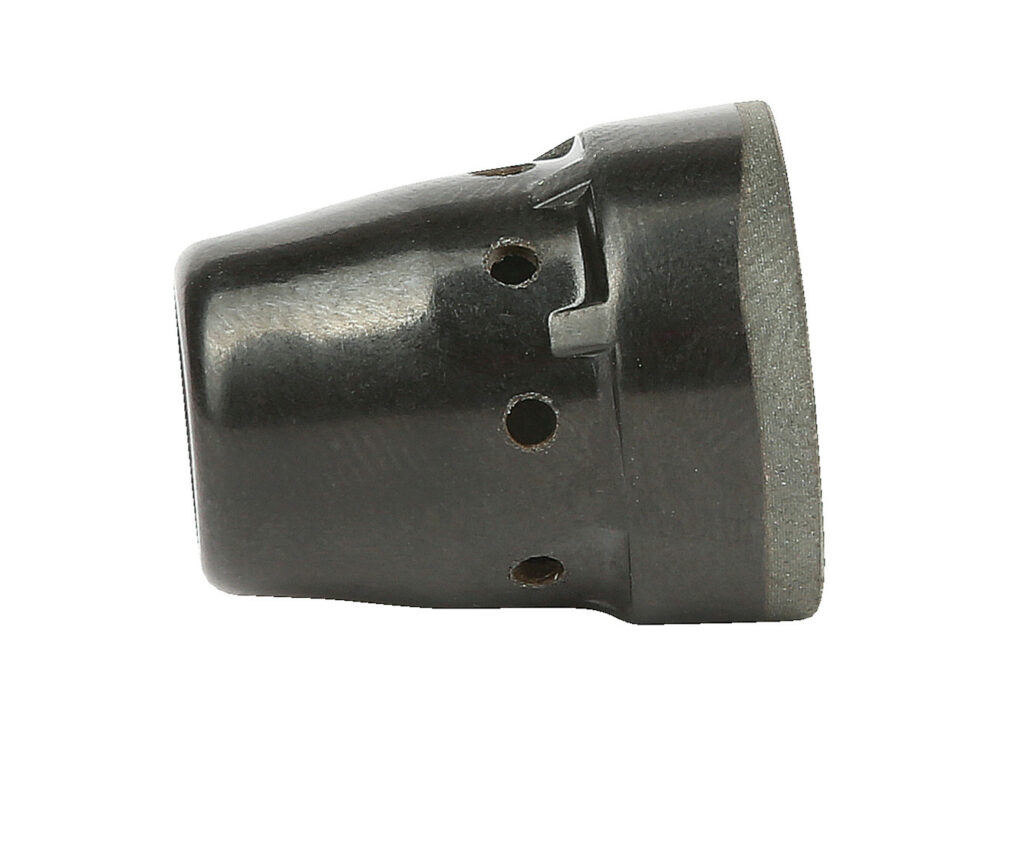
The right MIG/MAG welding torch for every application
As we have seen, many gas shielded arc welding jobs require a universal MIG/MAG welding torch, while some require a more specialist or a highly specific option. At Fronius, we offer a wide range of premium-quality welding torches, so you are sure to find the perfect choice for your power source and process. As you would expect, our service offering includes a comprehensive range of spare and wearing parts.
To find out more about our product portfolio, click here.
If you want to discover more about the fundamentals of MIG/MAG welding, then you can read our blog article here.
4 Comments
Carlos Farias
28. July 2020 at 13:15Trying to get a price on the 280i torch, can’t seem to find one anywhere on line. Will it fit my transsteel 2700?
redakteur
29. July 2020 at 6:37Hello Carlos! Please contact sales[at]fronius.com for more info. Thank you very much!
mag wheels christchurch
20. November 2020 at 10:28It is a great source of knowledge upon mig mag welding torches special version and the wearing parts. I am really happy to come across this exceptionally well written content. Thanks for sharing and look for more in future!! This is a brilliant post, thank you for sharing these great tips.
redakteur
23. November 2020 at 7:39Thank you for your kind comment – we are happy to hear that you like our blog! 🙂