It is a bright flame that can resemble a welding arc, but has nothing to do with joining itself – at most it is involved in the preparation. The arc moves over metal and plastic surfaces with millimeter precision, controlled with the highest level of accuracy by a robot. Afterwards the workpieces look the same as before, but on closer inspection significant differences are apparent.
Here we’re talking about atmospheric pressure plasma technology, a special case in plasma technology. But what exactly is plasma cleaning? What advantages does plasma cleaning offer and where is it used? How does plasma cleaning differ from conventional cleaning processes?
Activation and cleaning – application areas of plasma cleaning
Be it metallic or non-metallic, atmospheric pressure plasma is used to clean organic residues off surfaces without the use of liquid chemicals. Another application area for this process is in the activation of surfaces. The perfect surface pre-treatment of a wide range of different materials prior to bonding or welding is therefore the focus here.
What’s more, this is a relatively new, environmentally friendly, and comparatively inexpensive technology. The demand for such processes is continually increasing. Plus, as plasma cleaning is also very easy to integrate into production and many different materials can be processed, the procedure is used in several industries: automotive, commercial transportation, general industry, and many more.
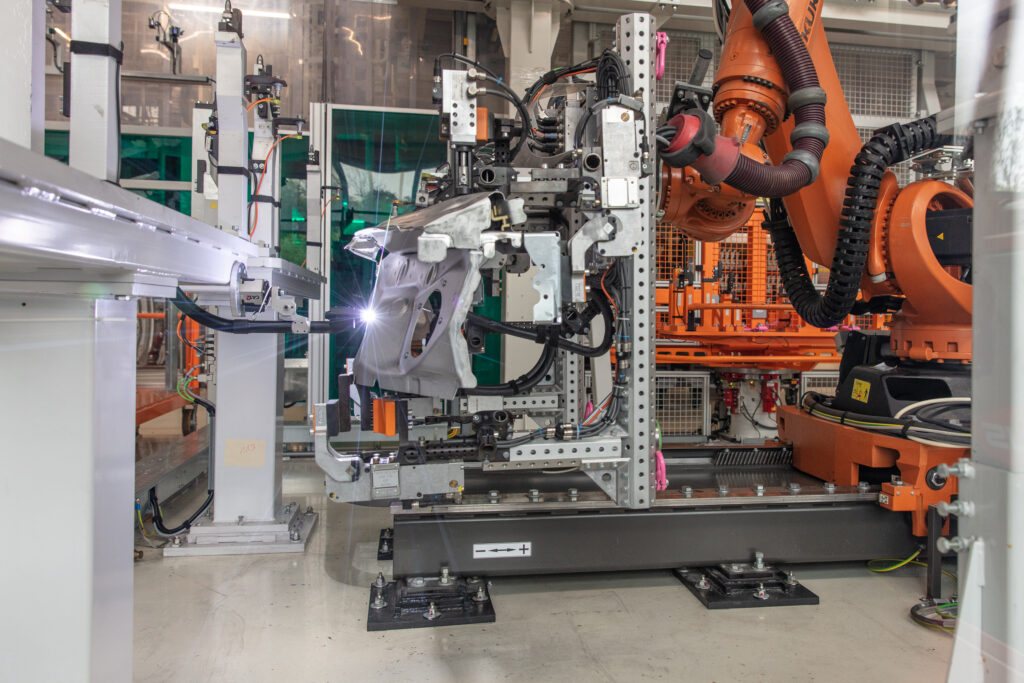
The cleanliness of part surfaces is an essential quality criterion for modern production and lightweight construction technologies, impurities or residues must be sufficiently removed in pre-cleaning or intermediate cleaning steps, so that subsequent production steps can be performed with sufficient quality.
How hot active plasma works
The precise way in which this process works is derived from arc welding technology: the un-transferred arc is ignited in the welding torch between the electrode and plasma nozzle. This means that a ground earth connection to the part is not necessary. The arc is then purged out of the nozzle with process gas. Finally, the resulting plasma flame cleans or activates the part surface with pinpoint accuracy, with mechanical, thermal, and chemical processes being responsible for this.
The plasma flame can also be precisely adjusted to the respective material surface using various process settings. For plastic surfaces, for example, the heat must be reduced significantly. This is achieved predominantly using process parameters such as treatment speed, distance to the surface, amperage, and gas regulation.
Extremely precise plasma cleaning is possible on different material combinations
Plasma technology is ideally suited to pre-treatment in joining processes, be it as a manual or fully automated solution. A wide variety of material combinations – for example a mixture of parts made from plastic and metal – can also be treated using extremely precise output control. The user can easily, individually, and precisely adjust the process parameters to the respective cleaning areas. The part surfaces are neither melted nor changed.
With atmospheric pressure plasma, efficient part cleaning and the required cleanliness are guaranteed. Thanks to the ability to program cleaning processes with hot active plasma with pinpoint accuracy, it is not necessary to clean the entire part before the next production step. Only those areas that require particular cleanliness are treated.
Atmospheric pressure plasma for part cleaning is sustainable and safe
Plasma pre-treatment is the ideal alternative to conventional pre-treatment methods such as grinding or chemical washing treatment. Adverse effects such as grinding dust pollution or chemical hazards are therefore eliminated. And the technology not only improves working conditions; the absence of solvents and chemicals also means that plasma cleaning is ecologically beneficial.
The advantages of plasma cleaning at a glance
- Economical and environmentally friendly
- Sustainable
- Fast and reliable
- High compatibility
- Universal application
- Can be used on thin and thick materials
- Can be used on metallic and non-metallic surfaces (mixture of materials)
- Easy integration into existing production lines
- Partial component cleaning
Differences compared to conventional cleaning processes
- Compared to previous cleaning processes, HAP (hot active plasma) technology is used exclusively where cleaning or activation of the surface is actually necessary. This means no superfluous cleaning on unnecessary areas of the part. In addition, no chemicals or other hazardous substances are used, and HAP technology is extremely sustainable overall.
- Argon is used as the process gas in the HAP technology described above. This gas is already standard in many production lines, so the compact plasma process is relatively easy to integrate into existing production lines.
- Compared to chemical washing or laser cleaning processes, plasma cleaning is an extremely cost-effective alternative.
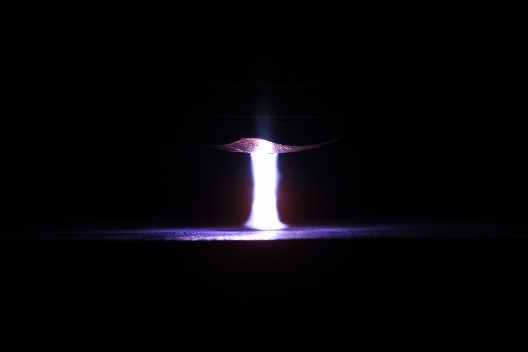
Hot active plasma technology at Fronius
Have these versatile and fascinating process characteristics sparked your interest? With ACERIOS, we at Fronius have succeeded in developing a robot-controlled solution for plasma cleaning based on arc technology. The system can be perfectly integrated into a wide range of production processes. Intrigued? You can find out more about HAP technology from Fronius here.
No Comments