Welding systems and robots may create the optimal basic conditions for MIG/MAG welding, but the real action happens front and center on the torch body. Temperatures of up to 15,500 degrees, spatter from liquid metal, and continuous abrasion by the welding wire: the thermal and mechanical forces imposed on wearing parts such as contact tips and gas nozzles are enormous. So, what can be done to delay the inevitable demise of these parts for as long as possible?
The less frequently that wearing parts such as contact tips, gas nozzles, and inner liners in the hosepacks need to be replaced, the better – this is good for the environment and customers benefit from lower production costs.
Essentially, wearing parts that are optimally tailored to the welding systems and material being welded last considerably longer. That is why different wearing parts have to be used for steel and CrNi alloys to those used for aluminum welding and CuSi applications.
Before we come to the four measures, there is one question that needs answering: why is it that wearing parts lose their function over time?
The contact tip: continuous contact – continuous wear
There is no MIG/MAG welding without a contact tip: the contact tip – often also referred to as a contact tube or contact nozzle – is where current flows to the welding wire by means of a “sliding contact”: this means that wire and nozzle are in permanent contact and grind against one another.
As such, “grinding out” is a major culprit when it comes to why contact tips become unusable over time. Continuous grinding of the wire alters the interior of the contact tip until welding wire and contact tip are no longer in permanent contact with one another. The flow of current becomes unstable, as does the arc, and the nozzle has to be replaced.
However, the opposite may also occur: wear to the wire and the extreme heat in the contact tip can result in an alloy layer. In this case, the interior of the contact tip increases slowly in size until the wirefeeder is blocked.
Gas nozzles – the fight against spatter
The second central wearing part on the torch body of a MIG/MAG welding torch is the gas nozzle. It is responsible for developing the gas shroud above the arc. The temperature has a decisive impact on the service life of gas nozzles: if the gas nozzle is too hot, more spatter will stick – this can fuse together with the gas nozzle and prove impossible to remove as a result. When a cold nozzle is used, spatter simply bounces off it.
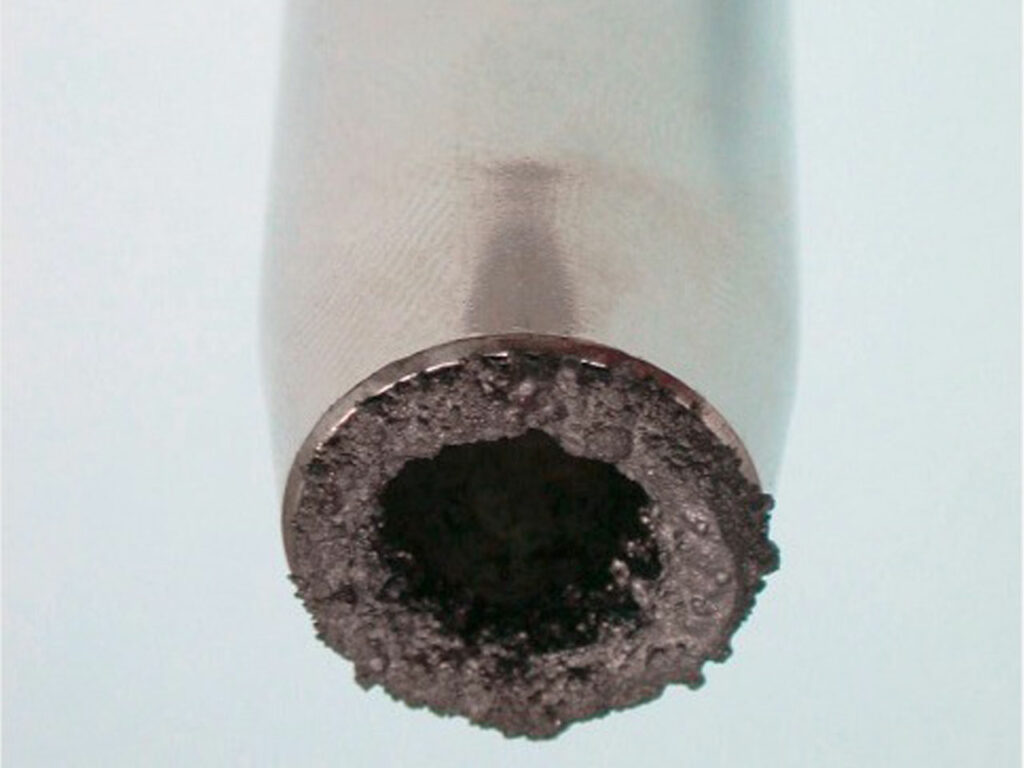
It is crucial that different types of nozzles be used for steel and aluminum respectively: gas nozzles for aluminum are typically coated, which makes the relatively soft aluminum spatter easier to remove.
Inner liners – the inner parts of hosepacks
The inner liner guides the welding wire through the hosepack and becomes worn over time as a consequence of the resulting friction; in the case of the FCS connection, inner liners start at the power source and end in the torch body at the contact tip.
To achieve the best-possible service lives and safe implementation of the desired welding processes, inner liners should be used that are optimally matched in terms of their design and inner diameter to the welding system in use.
So, what can be done to minimize wear to gas nozzles and contact tips?
While for the inner liners it is essentially just a matter of choosing the right product, the issue becomes a little more complex when it comes to contact tips and gas nozzles. These four measures can significantly increase the service lives of these parts:
Measure 1: optimally coordinate contact tip and welding wire
The right relationship between the welding wire and the contact tip – specifically between the wire diameter and the bore diameter of the contact tip – has a decisive impact on the service life of the contact tip.
The complex interplay of different factors such as amperage, stick out, and wire quality render expert advice essential. Without it, it would be impossible to specifically meet the various requirements. Say, for instance, a contact tip with a slightly smaller bore diameter needs to be used: it can be ground down for longer – and will also last longer as a result.
The wire corkscrewing – in other words, the extent to which the wire is bent in the contact tip – can also have an influence on the service life of a contact tip. If the wire corkscrewing is insufficient, the contact tip will grind out too quickly. If the wire corkscrewing is too great, the sliding contact – and therefore the welding process – won’t function very well. The solution? With new types of contact tips – such as those of the Contec split tip system – there are now innovative contact tips on the market that wear very evenly and thereby ensure very stable welding processes. We recommend Contec for aluminum and applications that really require an optimal current transfer.
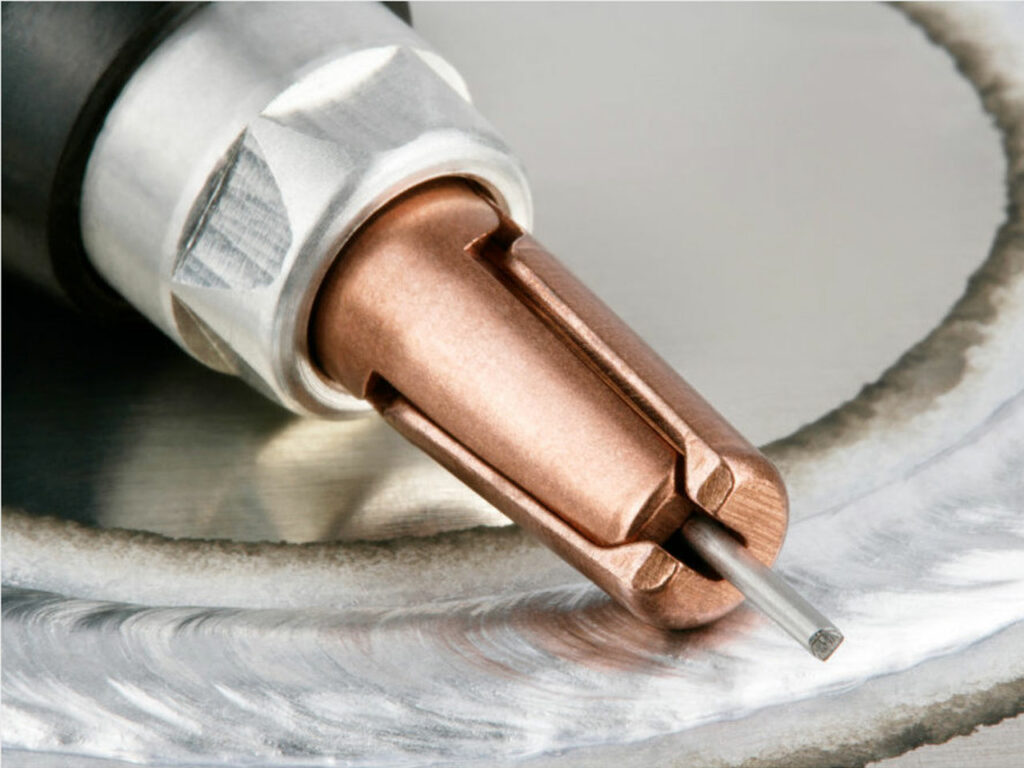
Measure 2: use contact tips made from high-quality material
How long a contact tip lasts depends, among other things, on the material it is made from. Three different types of contact tips are currently used:
Electrolytic copper – E-Cu: low-performer. The high level of purity of the copper does ensure an excellent flow of current but electrolytic copper contact tips are very soft, not very heat-resistant, and therefore not particularly durable – as a result, they are not recommended for robot applications.
Copper-chrome-zirconium – CuCrZr: the industry standard. These days, CuCrZr contact tips are most commonly used. The alloy elements chrome and zirconium render the nozzles hard and thermally resistant.
Tungsten copper – WQ quality: top performer in terms of a long service life. WQ contact tips are anything but cheap as far as procurement is concerned – however, money is saved in the long term because they have five to fifteen-times longer service lives than CuCrZr contact tips. The result? Production does not need to be interrupted as often. This makes them very cost-effective to use, particularly for hard steel wires. Their “secret”? The front section is made from an extremely resistant tungsten-copper alloy.
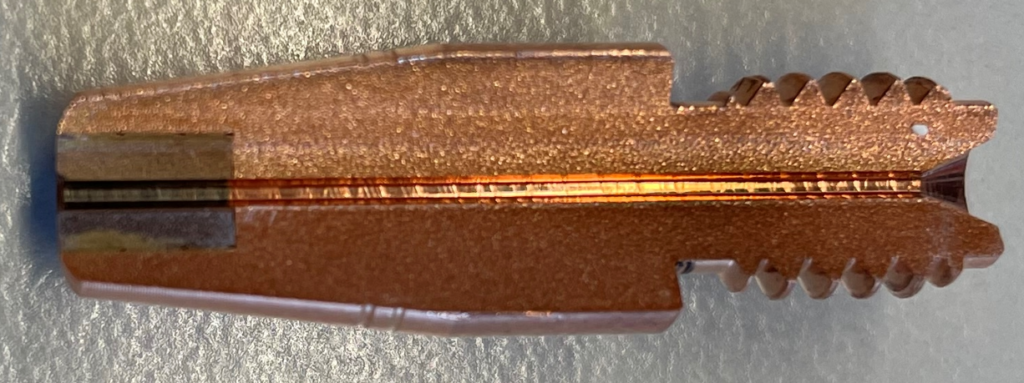
Measure 3: reduce the effects of heat on contact tips and gas nozzles
Located right at the front of the torch body, both the gas nozzle and the contact tip are exposed to extreme thermal loads. There are two options for reducing this:
1) Maintain distance: the bigger the stick out – in other words, the distance between the working part and the torch body – the lower the heat radiation affecting the contact tip and gas nozzle. As a general rule, the temperature in the front section of the torch body drops by 50 degrees for every millimeter from the working part. If the stick out is extended by just four millimeters, the heat to which the gas nozzle is exposed will fall by 200 degrees, making a significant difference.
2) Choose the right nozzle shape: the influence of the nozzle shape on the temperatures in the gas nozzle and contact tip is not to be underestimated. If welding is carried out with a short stick out, “pointed” contact tips and gas nozzles are recommended. They have front openings that are relatively small in diameter, which allows less heat radiation into the nozzle.
Measure 4: clean the torch body – extend service lives
The systematic removal of spatter extends the service lives of contact tips and gas nozzles considerably. The method used to clean a torch body depends mainly on whether it is steel or aluminum that is being welded:
Cleaning methods for steel and CrNi steel
Mechanical: milling is the most reliable method for removing spatter from wearing parts in the torch body. Various milling machines penetrate the inside of the wearing part from below by as much as 5 cm – and remove spatter using the tried-and-tested mechanical method. A good milling machine will also clean the front face of the gas nozzles.
Magnetic: the benefit of the magnetic cleaning method is this: there is no mechanical contact with the wearing parts. In magnetic cleaning devices, there are coils and a strong magnetic field is generated via a current pulse. The force exerted by the magnetic field removes all steel spatter from the wearing parts. There is no question that this method is on a par with milling but it does not work on aluminum.
Cleaning of aluminum and CuSi – brushing
Aluminum spatter is too soft to be milled away – milling would just smear it. That is why aluminum welding and CuSi applications are cleaned using brushes. The basic principle is the same as for milling.
Conclusion
The service life of wearing parts in a MIG/MAG process essentially depends on the following:
• Correct selection of wearing parts – optimal coordination to the respective area of application
• Product quality of the wearing parts used, particularly with respect to thermal and mechanical loads
• Interplay of the wearing parts with the other components of a welding system
• Efficient cleaning systems
All contact tips and gas nozzles from Fronius are developed in Austria and – like all Fronius wearing parts – they are tailored to the respective area of application. As a result, Fronius has, for example, more than 300 gas nozzles for welding steel in its portfolio.
If you want to find out more about which contact tips, gas nozzles, or inner liners would be best for a specific situation, please get in touch. You won’t be far from one of our 27 branches around the world – and our experts will be on hand to support you with advice and assistance!
2 Comments
Dwayne Boehm
10. January 2025 at 16:31We are interested in trying your tungsten copper tips and your Contec tips in our automated mig welding setups. We currently use Tweco compatible torches. Would you have an adaptor that would allow us to adapt your tips to Tweco torches? This would allow us to try your products and if we like them, maybe even switch to them when the time comes.
Can you tell us where in the US we can order the products from?
redakteur
8. May 2025 at 9:38Hello and thank you very much for your interest!
Here are the contact details for our headquater in the US:
Fronius USA LLC
6797 Fronius Drive
46368 Portage, Indiana
sales.usa@fronius.com
T: +1 (877) 376-6487
F: +1 (219) 734-5502
Have a nice day!