When is the user actually ready for welding? When they’ve prepared the workpiece, put on their gloves and helmet, the system is switched on, and the gas hose is already connected? What’s next? Our blog article provides answers using the example of MIG/MAG manual welding.
1) The parent material
Long before it becomes a question of how the welder settings need to be applied, it is necessary to identify the metal the workpiece is made of – the basis for all further steps. In most cases, the welder is of course aware of the material in question. If not, some test methods will help:
Long before it becomes a question of how the welder settings need to be applied, it is necessary to identify the metal the workpiece is made of – the basis for all further steps. In most cases, the welder is of course aware of the material in question. If not, some test methods will help:
/ Visual impression: The trained eye can see at first glance whether the material is steel, stainless steel, aluminum, or another metal. The color is a particular giveaway. Dull, dark gray indicates a high iron content. Bright and sparkling suggests chrome-nickel alloys.
/ Magnet test: In case of doubt, a magnet can help to identify the material. Only steel, nickel, and cobalt are magnetic at room temperature. If the material is strongly attracted to the magnet, it is usually iron or low-alloy steel. If there is a weak attraction between the material and the magnet, it is probably alloyed stainless steel. Aluminum is not magnetic.
/ Oxidation: If the workpiece has formed rust spots, it is steel. Stainless steels, also known as chrome steel and aluminum, do not rust.
/ Weight: This criterion is particularly relevant with regard to aluminum. Steel has a much higher density than aluminum, and the same size of material is therefore about three times as heavy.
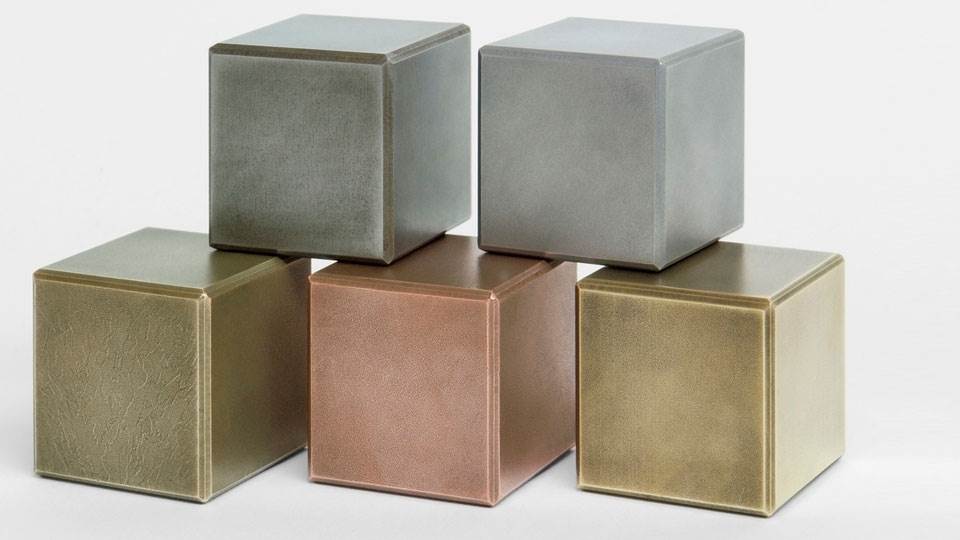
2) The filler metal
Before the user can get started, they need to select the correct wire electrode. The electrode must match the parent material and be of higher quality in comparison. This is because during welding, alloying elements in the parent material and in the wire electrode evaporate due to the heat. If an equivalent filler metal were to be used, the weld seam would ultimately be inferior and this must be prevented.
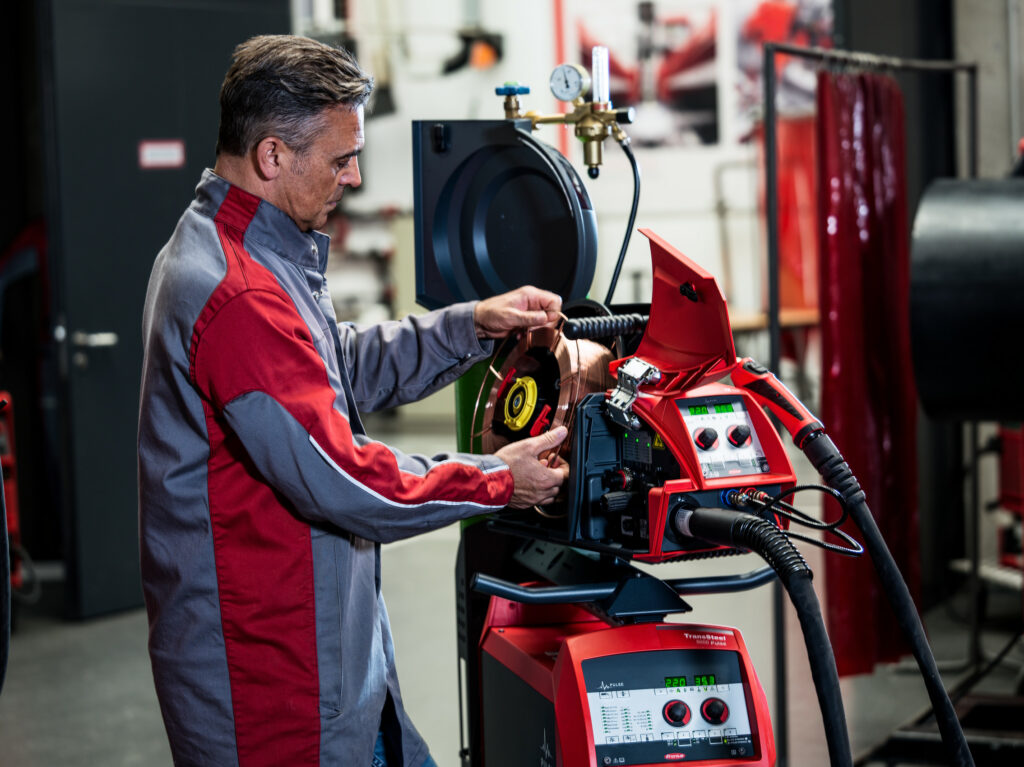
3) The shielding gas
MIG/MAG stands for metal active gas or metal inert gas welding. Both are known as gas metal arc welding [LINK: BLOG: WHAT IS MIG/MAG?]. Which process is ultimately used and the choice of shielding gas is also dependent on the parent material. Steels – from unalloyed to high-alloy – are MAG welded with a mixture of argon and CO2. MIG welding is used for non-ferrous metals such as aluminum or magnesium. Inert gases, i.e., argon and helium and mixtures made from these, are used for this purpose.
4) The gas quantity
Next, the gas valve is opened and the gas quantity is adjusted. There is a practical rule of thumb for this: Gas quantity (liters/minute) = wire diameter (millimeters) x 10 For example, if a wire electrode with a diameter of one millimeter is used, ten liters per minute are sufficient in a closed workshop. If there is a draft, a little more gas is needed.
5) The grounding cable
Before the welding system is adjusted, the grounding cable must be connected. The clamp should be attached as close as possible to the weld seam. If a welding table is used, the clamp can be mounted on the table, otherwise it must be attached directly to the workpiece.
6) Welder settings
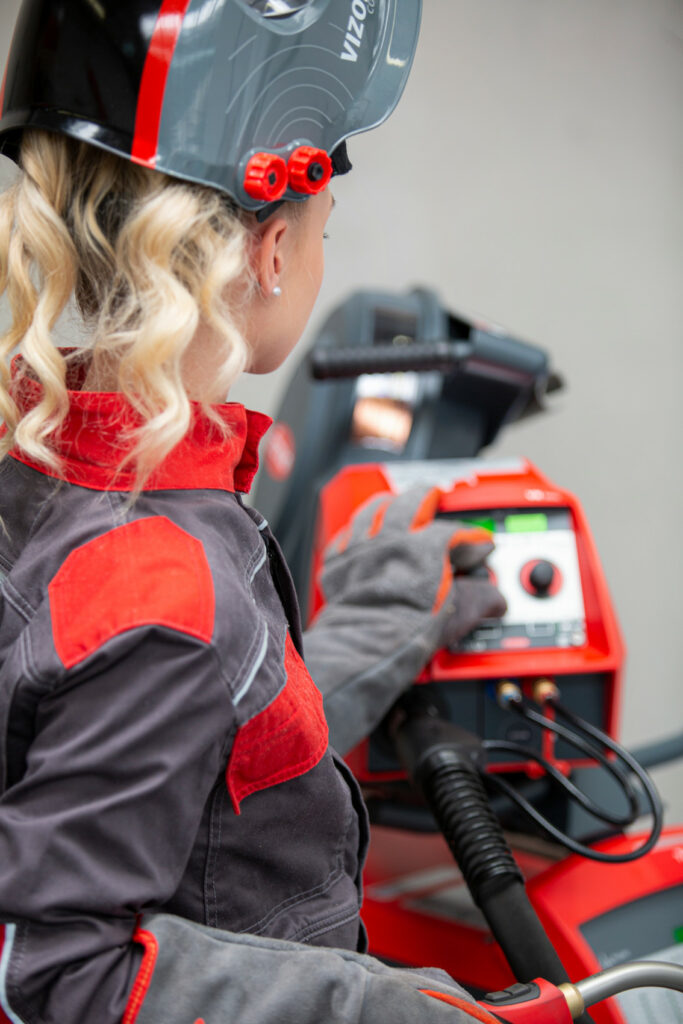
The most important measured variables in MIG/MAG welding are wire speed (in meters per minute), amperage (in amperes), and voltage (in volts). They are always dependent on the thickness of the material and the welding position. These parameters influence each other and must be in perfect harmony. Modern welding power sources have synergetic characteristics (also called “synergic lines”). These are welding programs that adjust the other relevant parameters in the background when the welder sets one of the variables on the control panel. Most often the welder sets the amperage. This is generally around 50 amperes per millimeter of sheet thickness. However, if you move within the range of increasingly thicker sheet metal, this factor is reduced to 40 or even 30 amperes, because the already high heat input must be reduced. The welding position also influences this rule of thumb. If, for example, welding is carried out in an upward position, less current is used so that the liquid weld pool does not fall victim to gravity. In addition, the characteristics used must be observed. For example, if you weld with a pulsed arc, there is considerably more heat involved. The amperage can be reduced significantly as a result. Once the welder has applied the welder settings, they should first test them on a test sheet.
Or: App for applying welder settings
Does all that sound too complicated? There is also a digital solution! Welding apps guide you intuitively through the basic information. Parent material, additive, shielding gas, desired welding speed, weld seam profile, and number of beads simply need to be entered and the welder receives the basic parameter sets in no time: current, voltage, wire speed, deposition rate, and heat input. Using the Wizard function of the Fronius WeldConnect app, these parameters can also be transferred directly to the welding system wirelessly via Bluetooth. The app therefore not only helps to find the right parameters, but also saves time when applying welder settings. The app is available to download free of charge for iOS from the App Store and for Android from the Google Play Store.
8 Comments
Frank Welder
27. August 2020 at 16:48That was good. Really nice information about setting the welder up correctly. Helps a newbie like me a lot.
redakteur
23. September 2021 at 15:11Thank you very much!
Bozeman Welding Company
22. September 2021 at 3:59Thanks for a good read. You did a great job illustrating how to properly apply the welder settings. I really enjoyed this article and think it will help my business when communicating with clients. Thanks for the article.
redakteur
23. September 2021 at 15:11Thank you very much for your feedback!
satnilesatnews
7. November 2021 at 17:00Thank you very much!
good. Really nice information
thanks
redakteur
8. November 2021 at 13:17Thank you for your feedback!
Dirman
22. June 2022 at 6:28Joe is the Master.
alhayat
7. November 2022 at 10:26Thank you for this valuable information, it has helped me a lot. Thank you
And also for you I found a lot of useful and valuable information like it on this site