Every day we cross bridges, hold on to stair railings, lean over balustrades, and rely on the same thing when doing so: support and safety. These properties can only be achieved through flawless, high-quality weld seams produced by qualified manual welders. We are talking about a professional field in which there is a huge shortage of skilled workers—a problem that is causing concern in the entire industry. But what is actually important when it comes to manual welding? What can happen in the event of weld defects? And why will this profession always exist despite advancing automation?
“Welder urgently needed” ads are proliferating more than ever before. The shortage of skilled workers has the welding industry firmly in its grip. As ever more members of the older generation retire and take their considerable amount of valuable experience with them, there is a lack of younger welders coming through the ranks to replace them. Manual welding, which requires skill, expertise, and the highest sense of responsibility on the part of every welder, is particularly affected. If bottlenecks occur here, companies are no longer able to fulfill their orders—especially where automation as a solution is not an option. Firstly, let’s take a look at what the field entails and in which industries manual welding has become particularly established.
What is manual welding and what does it involve?
Manual welding is a manual joining process that permanently bonds metals together. It includes processes such as MIG/MAG, TIG, and electrode welding, and is indispensable in many sectors. Manual welding is versatile, usually requires little equipment, and impresses with a high degree of mobility. As a result, it has become firmly established in steel construction in particular, but manual welders are also used on a daily basis for repair welding, pipeline construction, assembly work, or on construction sites.
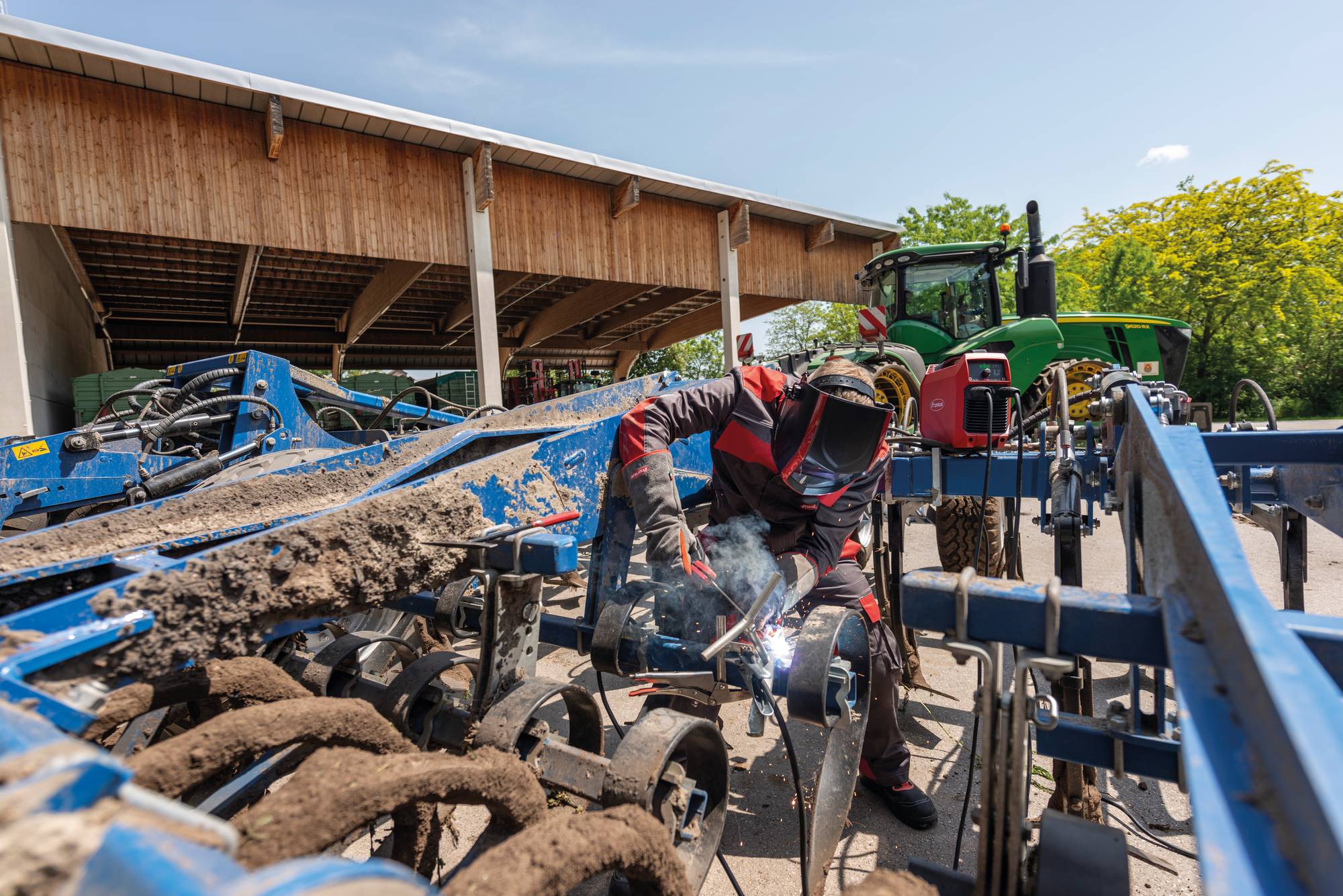
Automation as a solution for everything (or not)?
Where there is a lack of people, robots will step into the breach—or so you might think. This is indeed the case in many fields, including the welding industry to some extent. Solutions such as cobots mitigate the shortage of skilled workers, allow companies to breathe a sigh of relief, and reduce the strain on workers, especially when it comes to repetitive and tiring work. However, automated processes are reaching their limits when it comes to manual welding, because not every welding task is suitable for robots. Manual welding is advantageous or, in many cases, indispensable, especially with small production runs and for highly specific or complex components.
Manual welding is also the benchmark where highly individual and flexible welding is required, for example for vehicle repairs or when welding at great heights:
“In certain situations and at certain locations, you can only weld by hand. A good example is the construction of highway bridges. Finished sections of roadway are produced elsewhere and delivered to the site, but when the bridge is finally erected, the individual sections are joined together by manual welders. There is also no automated process here, so the responsibility ultimately lies with the individual welding specialists. That is why it is so important not only to continue to have enough manual welders, but above all to have highly qualified ones,” says welding technology expert and application engineer Tobias Rieder.
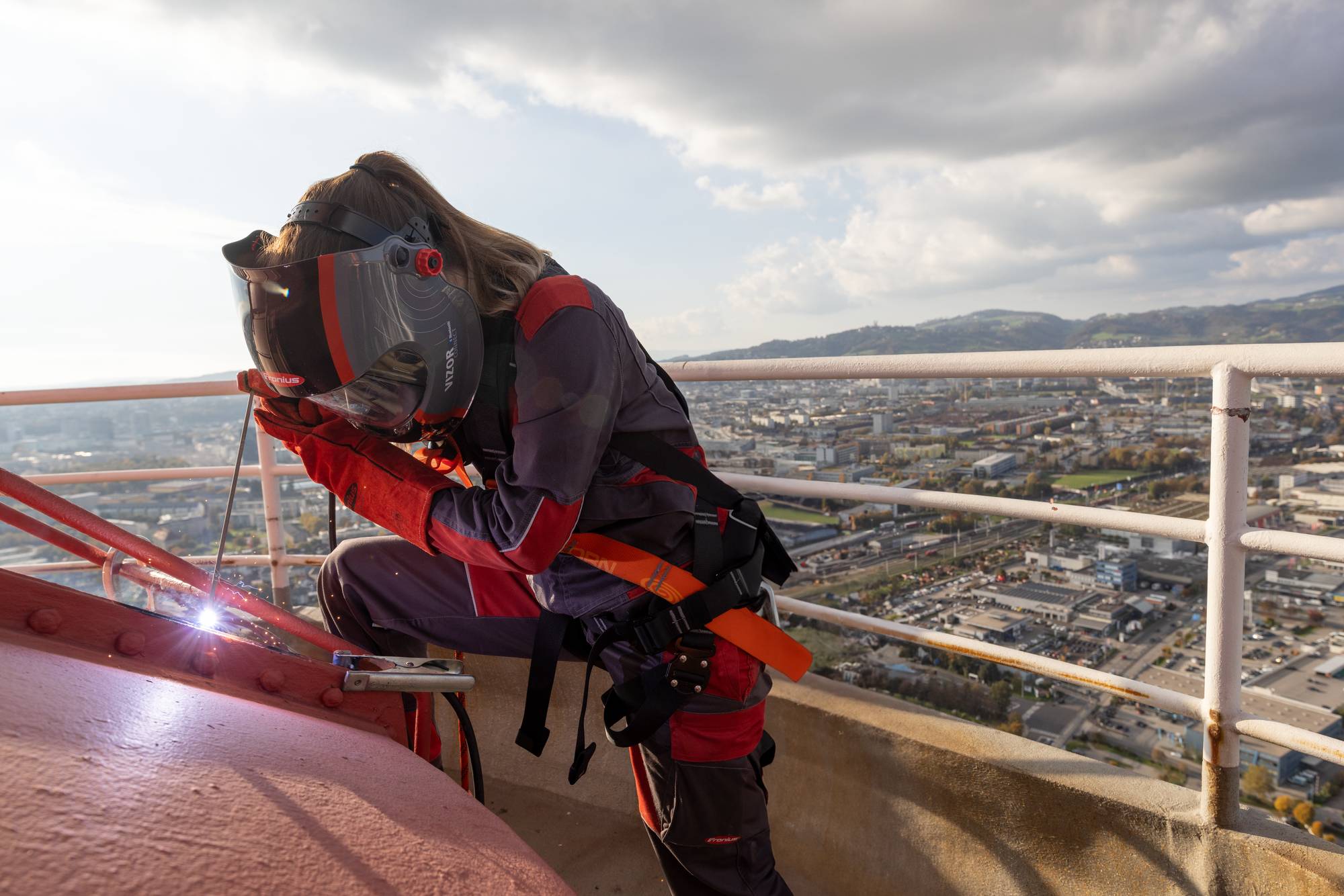
Requirements of manual welding
But what makes a good welding specialist? What I need to bring to the table if I want to work in this profession? The fundamentals are the trio of manual dexterity, understanding materials, and resilience. Be it lying under a pipe or kneeling in a narrow container, the working environment is often harsh and hours of welding under difficult conditions can be very physically demanding. For Rieder, awareness of how you can protect your own health is a fundamental prerequisite for every manual welder: “As a manual welder, you have to pay special attention to your own safety. You are often working for a long time in the most adverse conditions or in the narrowest of spaces, for example in a tank. It is important to ensure proper ventilation and always have a responsible supervisor at your side who checks the safety measures during the welding process.”
Excellent knowledge of materials also plays a key role. “I need to know how heat input and distortion behave during welding, for example, and the joint preparation work must also be carried out properly. What you weld has to last—you have to be able to rely on it”, says Rieder. But how can you be certain about the quality or qualifications of the specialists employed? According to Rieder, welding tests are essential to ensure that the welders are highly trained specialists and that their work is performed properly and professionally. “With their knowledge and experience, manual welders bear an enormous responsibility that cannot be emphasized enough,” emphasizes the welding technology expert.
The highest sense of responsibility for every seam
Where there is a high level of responsibility, mistakes are usually fatal. This also applies to manual welding, because weld defects can have serious consequences. A weld that is not executed properly could crack at some point and lead to material breakage—or, in the worst case, also endanger the safety of people.
“I know of a case that happened on a construction site in France a few years ago. A formwork panel fell from a higher floor, directly onto the head of a welder working there. The panel punctured his protective helmet and practically drilled into his head. He was in the intensive care unit for months, fighting for his life. He won the battle, but still lives with a piece of plastic in his head that replaces the part of the skull that was damaged. The cause of this accident was a defective weld,” Rieder explains, drawing attention to the high level of responsibility as a welding specialist has to bear.
Fronius Artis and Ignis: Effortless manual welding
In addition to skill, sophisticated knowledge of materials, and the highest sense of responsibility, the optimum welding machine is also an important ingredient for successful manual welding. The question here is, what does a good manual welding machine need to be able to do? First and foremost, it must be perfectly matched to the welding task at hand. For example, if welds have to meet the highest standards in terms of both quality and appearance, the Fronius Artis is an ideal choice. Visible seams on stainless steel handrails or high-quality pipe connections for swimming pools, as well as precise applications in tank and industrial plant construction, are produced by the Fronius Artis with ease.
The Fronius Ignis is a reliable companion when welding has to be carried out under the most adverse conditions. On the outside, the durable machine keeps environmental factors like dust and moisture at bay, while the pioneering technology offers a range of convenient functions to facilitate the welding process. At just 9.8 kg, the Ignis is lightweight, but still very robust. Welders can therefore count on the powerful manual welding machine both indoors and outdoors, in rain or sunshine, at great heights, or in the tightest of spaces.
Be it Ignis, Artis, or another high-quality welding machine, the key is to choose a machine that is perfectly designed to meet the needs of both welders and the task at hand—and on which the specialists can rely on day in, day out. But no matter the manual welding task, the responsibility does not lie with the machine, but rather in the hands of each and every individual welding specialist. After all, despite all the technical progress and automation we have seen, it is people who remain indispensable in many places.
Have we sparked your interest in manual welding? Read on to find out where to use which welding process—whether MIG/MAG, TIG, or electrode welding—and take a closer look at our Ignis and Artis machines. Find out what both powerhouses can do in detail on our website!
1 Comment
claire spillane
7. March 2024 at 11:55Insightful and so true. If only those who have influence over salaries could see that manual welders are key to the world’s infrastructure and transportation.
Great to see Fronius develop more equipment to help manufacturers with both staff issues and extensive projects.