Clad welding or cladding, also known as weld overlay, is a special welding process that is used to extend the service life of components and equipment. In particular when components are exposed to extreme conditions such as high temperatures, pressure, or aggressive chemicals, an additional protective layer is needed to prevent disastrous consequences.
Why clad welding is so important
Clad welding plays a crucial role in the oil and gas industry in particular. Leaking pipelines have been and continue to be the cause of pollution incidents in which large quantities of heavy oil are released into our oceans. These leaks also pose dangers in gas pipelines, as highly flammable gases can cause fires or even explosions when they come into contact with an ignition source such as oxygen. An unfortunate example of this was the “Eye of Fire” in the Gulf of Mexico in 2021, where a gas leak in a pipeline 150 meters from the drilling rig of the Ku-Maloob-Zaap oil platform caused a devastating underwater fire.
One thing is certain: when it comes to protecting pipelines and other critical assets, no measure should be spared that offers additional protection. Cladding minimizes potentially dangerous weak points. The additional protective layer has been proven to reduce the risk of leaks, which can prevent not only economic damage but also damage to the environment.
Cladding is an all-rounder in surface engineering
Applications for clad welding are not confined to the oil and gas industry; it is also used in power plant construction to protect membrane walls and heating surfaces from aggressive pollutants. This is the case, for example, in waste incinerators and biomass power plants, where high levels of sulfur and halogen place metal components under extreme stress.
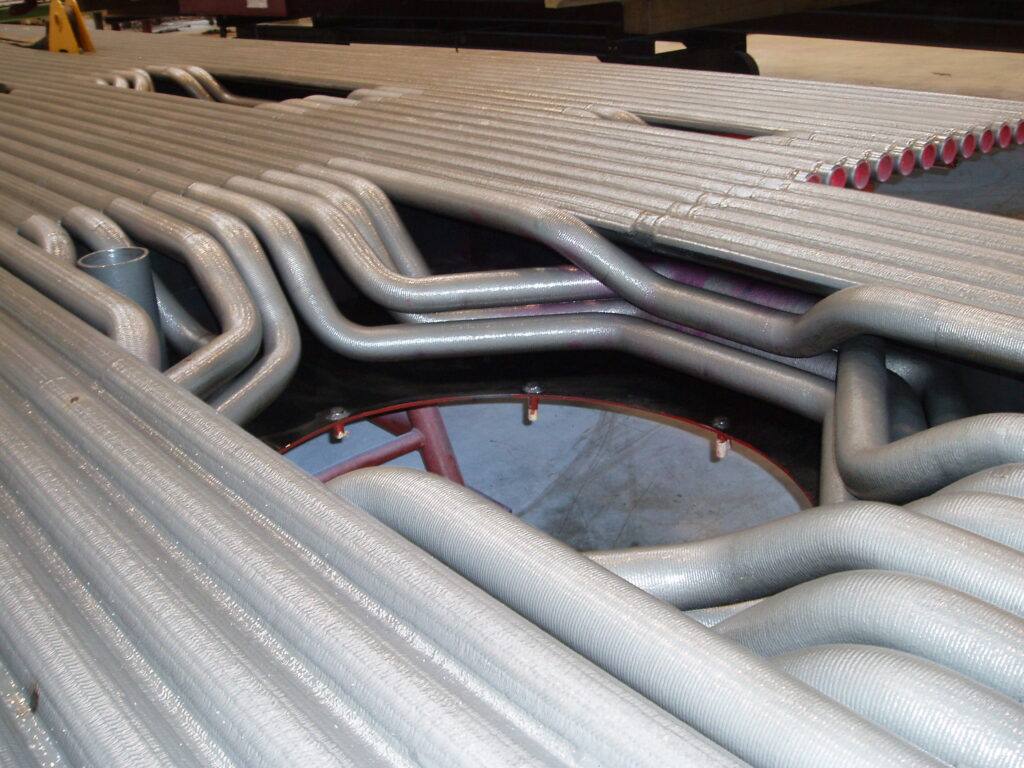
Accordingly, cladding is always a go-to when surface properties need to be improved in a specific way. This could be to increase resistance to wear and corrosion or as an economical way to repair components without having to replace the entire component.
More than just “welding on”
A simple “Just weld it on and it’ll hold” is not enough when it comes to cladding. To withstand the extreme stresses exerted, the metallic layers must be reliably bonded to the base material. This process is highly complex and requires precise adjustment of the welding parameters to avoid putting costly components at risk.
For this reason, in practice, clad welding is usually carried out automatically using TIG hot-wire (TIG-HW) or the Cold Metal Transfer (CMT) process. A crucial quality factor is the dilution, which describes how much of the workpiece base material mixes with the applied material. A small amount of dilution is necessary for the applied material to retain its special properties, such as the desired high level of corrosion resistance.
Clad welding techniques in detail
Cladding essentially involves building up volume in the form of a top layer using welding filler metals such as wire or powder. Suitable special alloys such as Alloy 50 and 625, CrMo 910, or Inconel 625 are used for this purpose, which results in a significant advantage when it comes to surface coating: conventional steel can be combined with high-quality alloys, making cladding particularly economical.
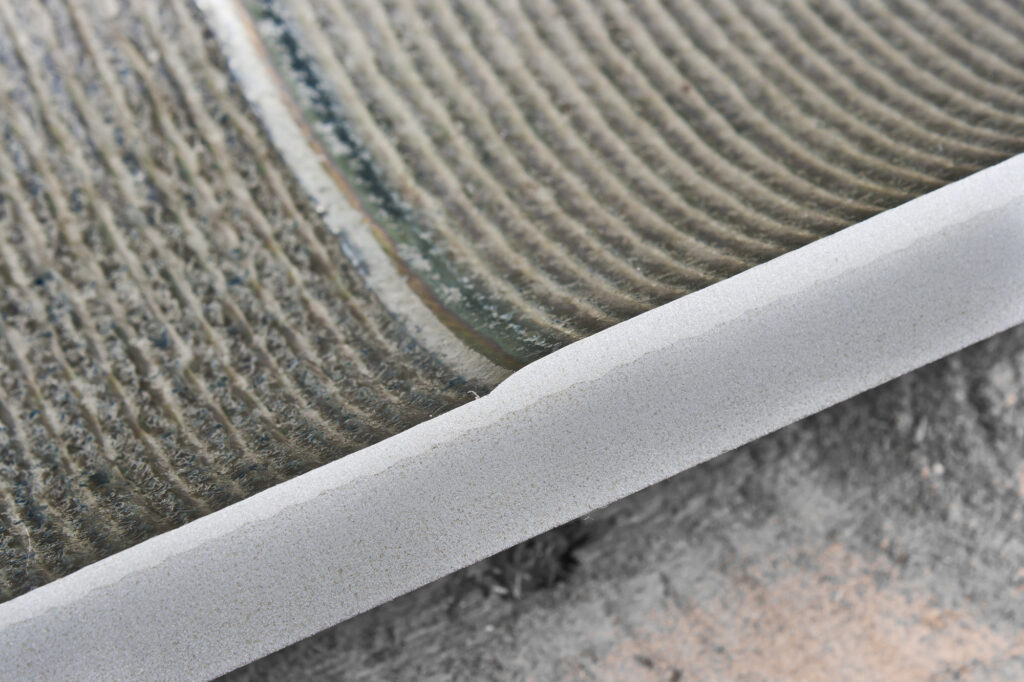
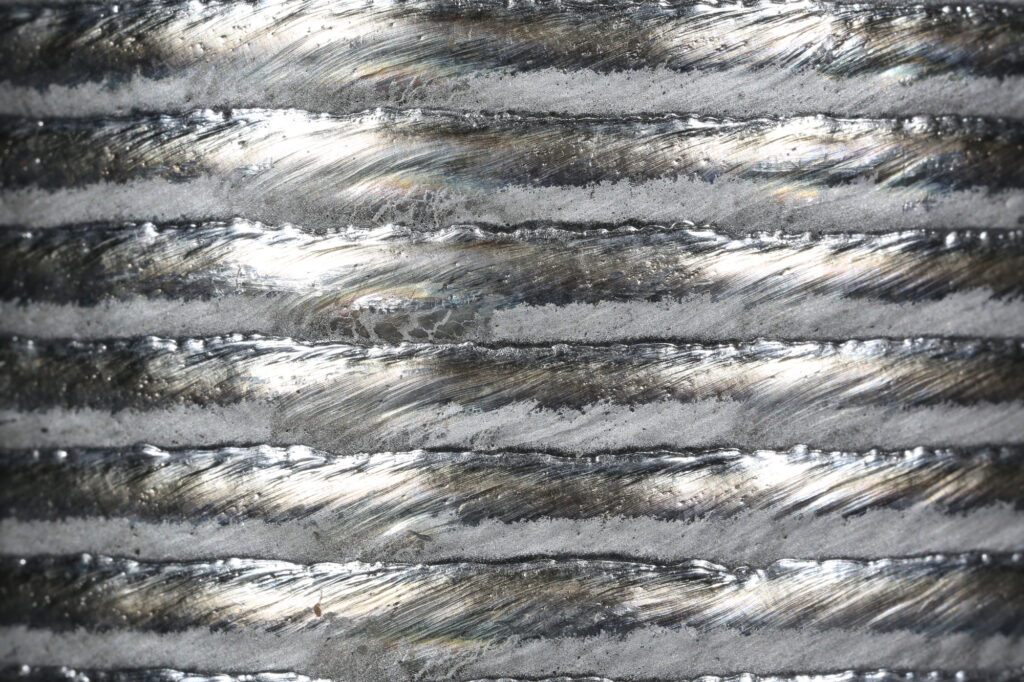
Due to the extremely high safety requirements in the oil and gas industry, TIG hot-wire welding is primarily used. However, laser cladding and plasma powder cladding are also common methods. It is impossible to say with certainty which method is best, as each approach offers specific advantages that need to be considered depending on the material, component size, and requirements.
TIG hot-wire welding for absolute precision
TIG-HW is a further development of conventional TIG (Tungsten Inert Gas) welding. In this process, an additional wire is electrically preheated before it is introduced into the melting area. This leads to a significant improvement in the deposition rate and efficiency of the welding process, minimizing defects such as cracks or deformation.
As a result, TIG-HW is extremely versatile and produces a high-quality surface with even, spatter-free welds that meet even the most stringent safety standards. The only disadvantage is that TIG hot-wire welding is very time-consuming, especially when it comes to large components or series production.
The SpeedClad 2.0 effectively answers this challenge. This high-tech clad welding process developed by Fronius makes significantly higher welding speeds of up to 110 cm/min (43 in/min) possible with just one specially shaped electrode and an additional wire. The slim welding torch also enables surfacing of small internal diameters from 100 millimeters (4 inches).
Reduced heat input thanks to CMT
While TIG hot wire is mainly used in the oil and gas industry, many companies in power plant construction rely on MIG/MAG or CMT to surface finned walls or other similar components. The advantage is that the digital process control detects short circuits automatically and promotes droplet detachment by retracting the wire.
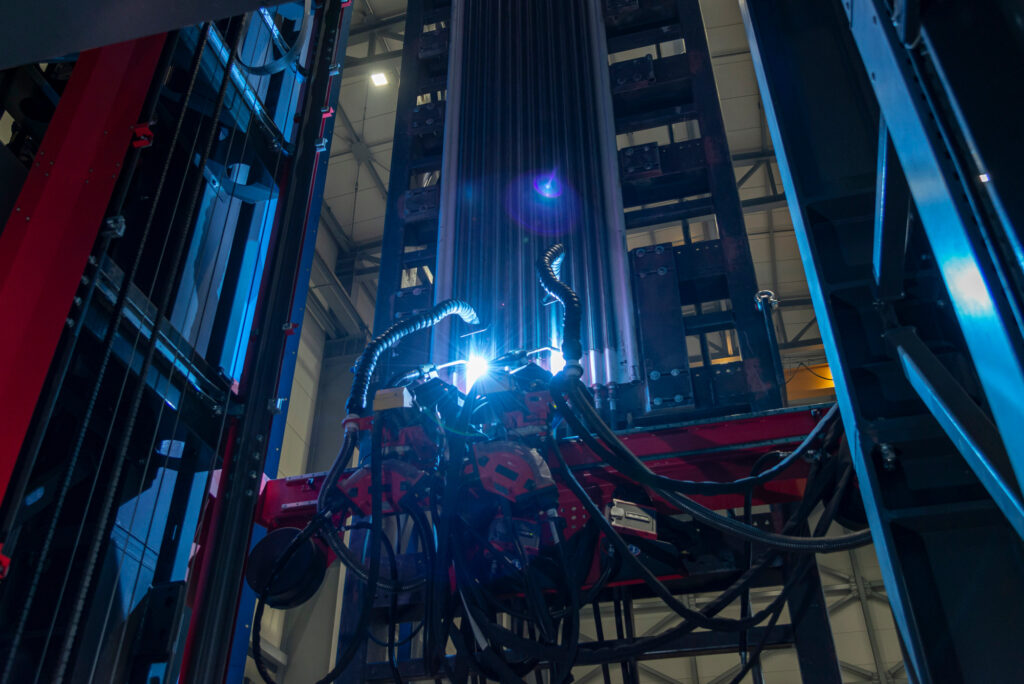
This forward and backward motion ensures a short arc burning phase, which significantly reduces the heat input. The result is a virtually spatter-free coating with an exceptionally smooth surface, soft seam overlaps, and consistent layer thickness.
TIG cladding made easier
In the supply industry, manufacturing companies like to use cladding cells to create a stable welding environment. The Fronius Compact Cladding Cell, or CCC for short, has proven to be a powerful and cost-effective solution in this regard. With a footprint of just six square meters (64.5 square feet), it provides sufficient capacity for simple component geometries with a diameter of up to one meter (39 inches), a height of up to 1.9 meters (75 inches), and a maximum weight of 2500 kilograms (2.5 tons), making it ideal for the internal surfacing of valves.
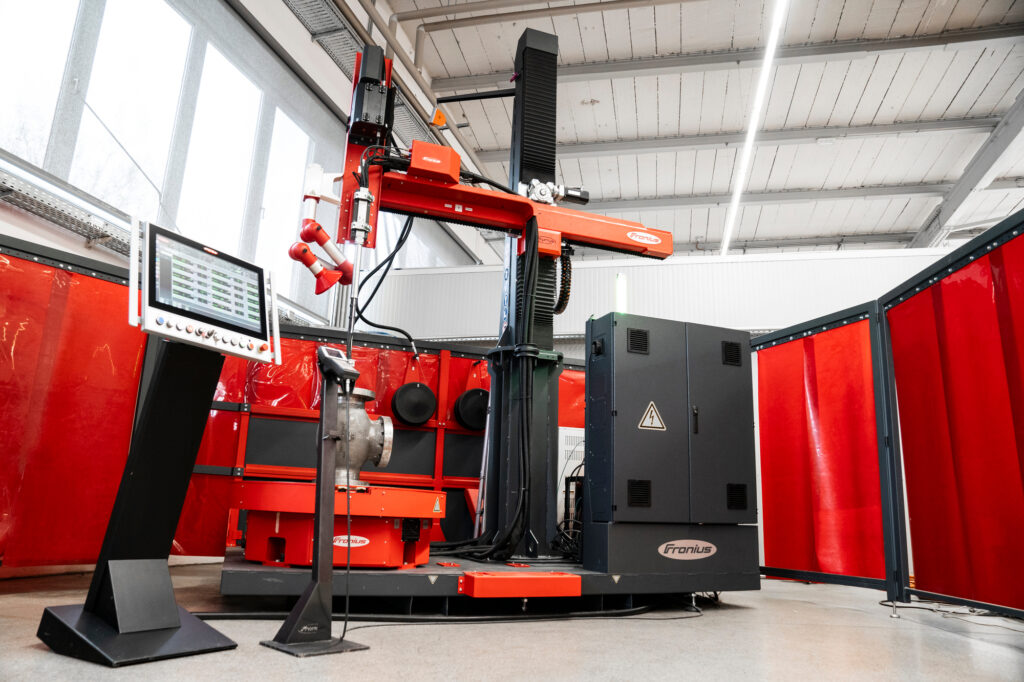
The Compact Cladding Cell only uses TIG hot wire or SpeedClad 2.0 for the welding process to produce the highest quality welds. With features such as the ergonomic wirespool holder, 21-inch touch display, and real-time process visualization, the cladding process is not only user-friendly, but it can also be easily monitored to avoid errors. The CCC’s compact design means that it can be easily transported from one location to another with a forklift truck—a space-saving option that allows smaller suppliers to take on surfacing jobs in the oil and gas industry.
Precise cladding for complex component geometries
For larger and more complex components, endless torch rotation (ETR) systems impress with an endlessly rotating welding head that allows the torch position to be determined automatically in 3D space, allowing for short set-up times. The synchronized movement axes that cause the welding torch and positioner on which the component is located to move in sync represent a further advantage.
The welding torch can always be held in the optimal position for the cladding process and the weld seam is prevented from flowing out, meaning that even complex geometries can be surfaced automatically. Equipped with a 21-inch touch display, the ETR systems are compatible with SpeedClad 2.0 and offer user-friendly control and real-time visualization, and, as a result, high productivity.
Conclusion: weld cladding as an indispensable solution
Be it with modern cladding cells or systems such as ETR, cladding is and remains a key process that protects us from dangerous material failure caused by corrosion and abrasion. The wide variety of modern clad welding processes means that the best solution can be found for every application.
If you would like to learn more about the individual processes and cladding solutions, you can find more information on our website.
No Comments