No other process offers more stable weld seams than TIG welding, as well as better quality in terms of the look and feel of the product. In addition, TIG has a wide range of applications: The process is suitable for all metals and thin sheets as well as out-of-position welding and root pass welding. What’s more, welding does not produce slag, the material hardly deforms at all, and the process is virtually spatter-free. The advantages and broad range of applications are clear. But what is important when purchasing a mobile TIG device? What are the most significant functions? Here are five key points to consider:
…
…
1. High frequency ignition
High frequency ignition (HF) is generally used for TIG welding. This produces an arc between the workpiece and the electrode without touching the workpiece with the electrode. For this purpose, the welding torch is positioned about two millimeters above the workpiece. If the welding torch trigger is then pressed, the arc ignites. As an alternative, touchdown ignition is recommended: The arc is ignited when the electrode touches the workpiece. However, there is a risk that the weld pool will be contaminated by the inclusions of the tungsten electrode. This is a serious shortcoming, particularly in sensitive welding tasks such as in medical technology.
Touch HF is the best way to easily and accurately position the ignition. The procedure for the welder is basically the same as for touchdown ignition: The workpiece is touched with the electrode. After lifting it off, the pre-set lead time starts. The arc then ignites exactly at the point where the electrode touched the workpiece. No other process offers better control during ignition.
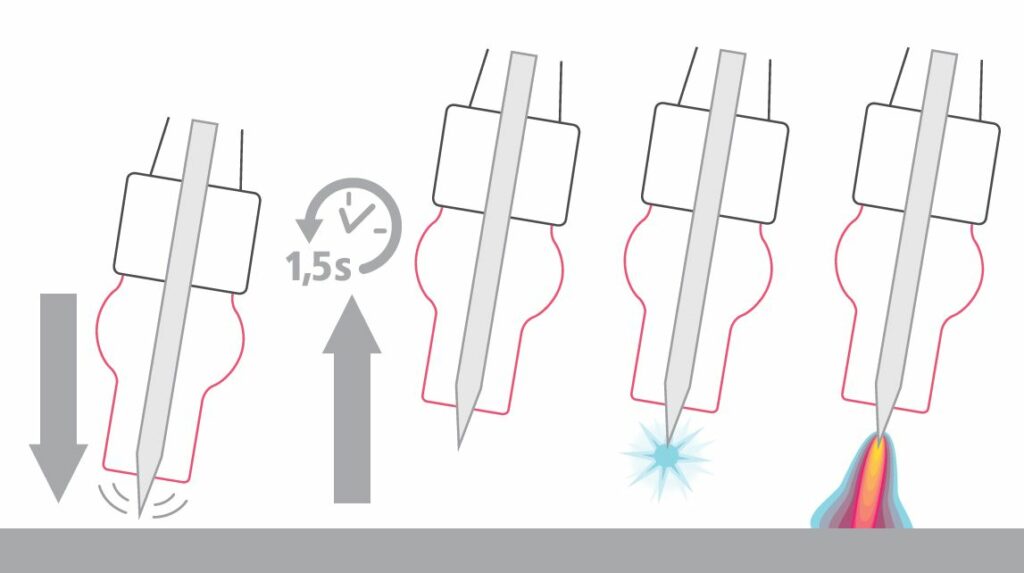
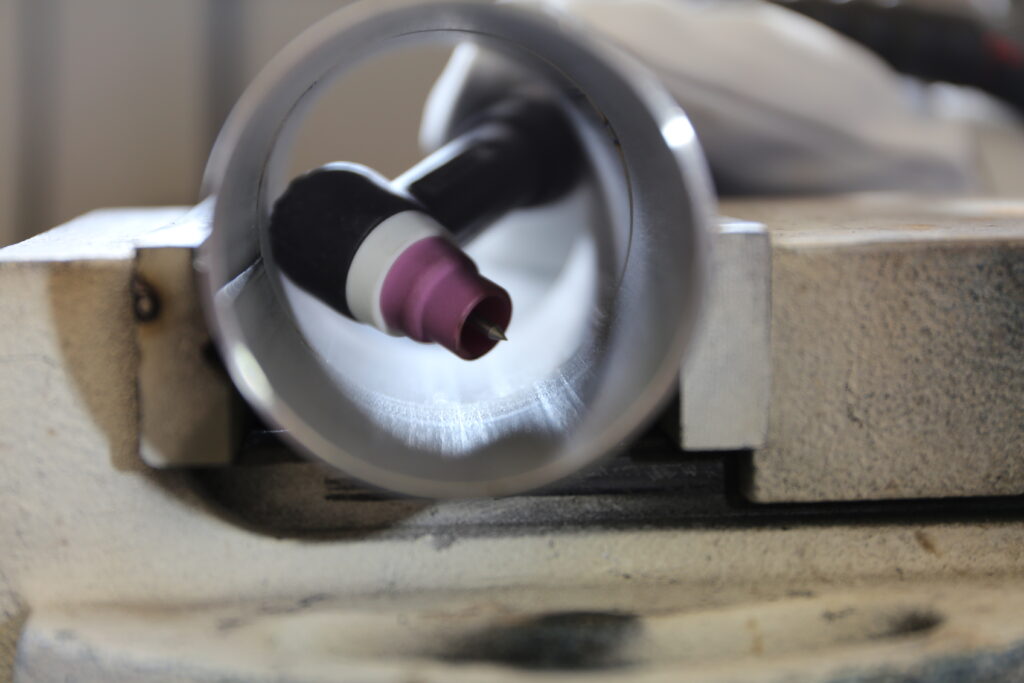
There are welding systems that can switch between HF and Touch HF ignition as standard. The optimum ignition can therefore be selected depending on the application.
2. Tacking function (TAC)
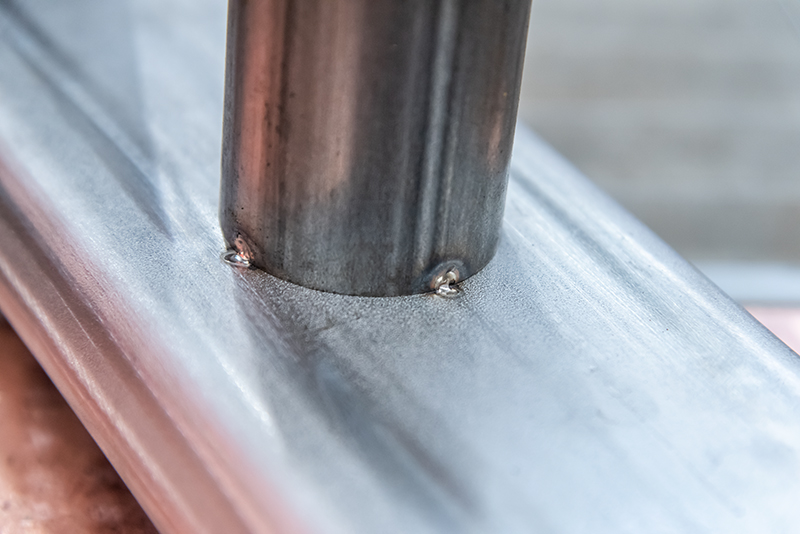
TAC stands for “tacking,” meaning to attach. If two different components are to be joined to a workpiece, they must first be fixed in preparation. The weld pool is oscillated by means of a pulse current. This makes it easier to tack components together without burning the edges. If TAC is used in spot welding mode, it is always possible to achieve the same size tacking points. The uniformity of the welding spots makes welding over in particular much easier. Another advantage of TAC is that the tacking function allows for low, or in the best case scenario no temper coloration, and also achieves time savings of up to 50% compared to conventional tacking.
3. Lowering current
The lowering current is only used for TIG 4-step welding. 4-step means:
- st step: Pressing the torch trigger causes the arc to ignite with starting current
- nd step: When the trigger is released, the welding process starts with full welding current
- rd step: Pressing the trigger again starts lowering of the arc
- th step: Releasing it again ends the welding process
Welding in 4-step mode is more ergonomic for the welder – they do not have to permanently hold the torch trigger down manually. The lowering current allows the welder to reduce or increase the main current as required during the welding process. In particular when changing the filler metal during the welding process, it is useful to reduce or increase the current slowly. The two additional delay times “Slope 1” and “Slope 2” help here. However, if a tacking point is to be welded over, a higher current than the set main current is required. This requires higher heat input, because the material is stronger at this point.
4. Mains voltage tolerance
Power Factor Correction (PFC) enables high mains voltage tolerance to be compensated for. This allows for optimum control of voltage fluctuations or too low input voltage, such as those caused by multi-port distributors, long mains cables, or the use of generators at construction sites. Depending on the welding system, even at 30 percent less input voltage, the devices can still deliver their full output. If, for example, only 160 volts are available, the machine uses PFC technology to maintain a constant voltage so that the welder can still weld with 170 or 210 amperes. This means that there is always enough energy available for a stable arc.
5. TIG Multi Connector (TMC)
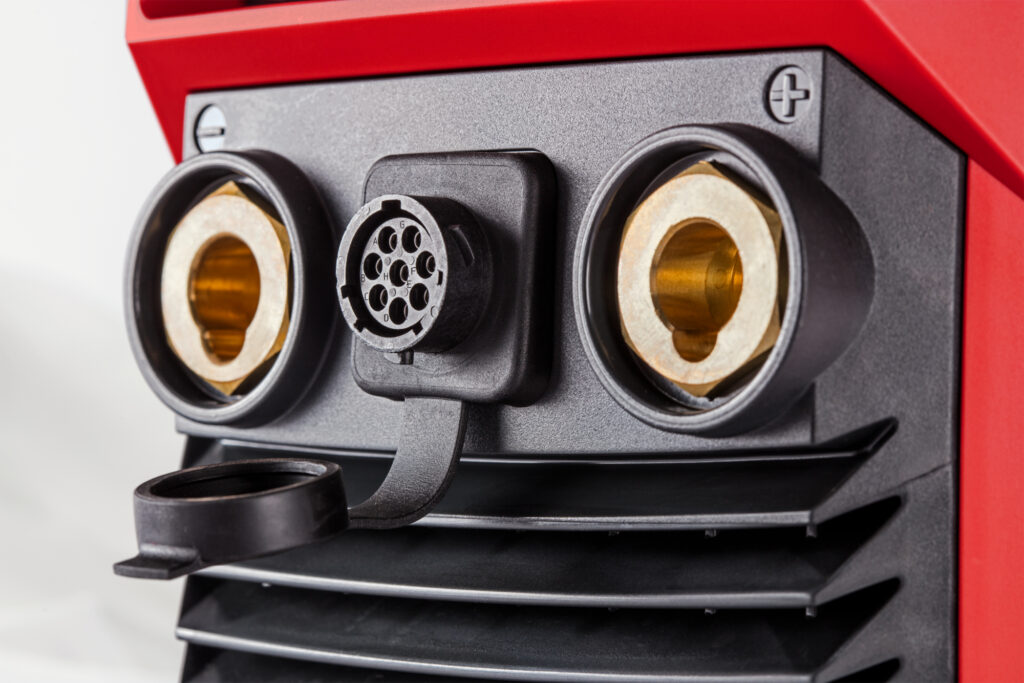
Of course, the various TIG devices offer many other functions, ranging from automatic switch-off to a gas test function. One feature that all TIG machines have in common is electrode welding. Because the devices are based on a digital resonance inverter, the ideal output characteristic is available for both processes. With all the possibilities, what functions should your welding system have?
Looking for a TIG device? Then take a look at the new TransTig 170/210 from Fronius – a machine with all the must-haves and more, including 40% duty cycle and 96 V to 265 V mains voltage supply.
No Comments