Souder avec succès dépend en grande partie de l’expérience. Néanmoins, la routine présente parfois des inconvénients au travail : par exemple, lorsque les erreurs de manipulation deviennent coutumières, ou lorsque des systèmes de soudage ultra-modernes sont utilisés exactement de la même manière que leurs prédécesseurs vieux de plusieurs dizaines d’années. Et soyons honnêtes : combien de soudeurs parcourent les centaines de pages des instructions de service avant d’essayer un nouveau système ? Dans cet article de blog, vous découvrirez 6 faits souvent méconnus à propos de votre système de soudage, auxquels vous devriez prêter attention pour améliorer votre soudage et son efficacité.
Les systèmes de soudage de qualité sont conçus pour que les erreurs de manipulation les affectent le moins possible. Et les soudeurs expérimentés obtiennent souvent des résultats remarquables lorsqu’ils ignorent complètement les avertissements ou recommandations centralisés du fabricant. Cependant, même le plus robuste des systèmes de soudage équipé de pièces d’usure de qualité optimale ne peut être manipulé éternellement de la mauvaise manière. Un jour ou l’autre, les coûts deviennent plus ou moins conséquents.
Utiliser un système de soudage le plus efficacement et le plus longtemps possible nécessite donc de connaître quelques points essentiels. Des points qui sont à vrai dire évidents, et également mentionnés dans les instructions de service, mais qui, d’après l’expérience des équipes de service dans les entreprises des techniques de soudage, sont étonnamment méconnus de bon nombre de soudeurs, ou tout simplement ignorés.
À quels points fondamentaux faut-il donc veiller pour utiliser de manière optimale un système de soudage moderne ?
1. Le fil d’apport et la gaine guide-fil, des âmes sœurs à harmoniser
Pour un fonctionnement optimal des systèmes de soudage ultra-modernes, le matériau d’apport et les pièces d’usure doivent être parfaitement adaptés les uns aux autres, ce qui s’applique entre autres aux gaines guide-fil des faisceaux de liaison des appareils MIG/MAG. Les soudeurs doivent veiller à toujours opter pour la gaine guide-fil correspondant au fil d’apport utilisé : une gaine guide-fil en acier pour un fil d’acier, une gaine guide-fil en graphite en cas de soudage de l’aluminium. Les indications du fabricant permettent de déterminer la gaine guide-fil adaptée au fil d’apport.
Souder de l’aluminium en utilisant une âme avec intérieur graphite dans la torche de soudage ne s’avère guère pertinent à long terme. La relative rugosité du fil d’aluminium est à l’origine de dépôts et de résidus sur cette dernière, ce qui entraîne des répercussions négatives sur l’arc électrique. Une fois la gaine guide-fil usée, c’est l’ensemble de la torche de soudage qui est compromis : le fil ne s’y insère plus correctement et finit par sortir de l’enrobage en caoutchouc. Les soudeurs doivent donc vérifier l’état de la gaine guide-fil à intervalles réguliers.
En cas de soudage de différents matériaux par le même système, à des intervalles qui varient rapidement, les soudeurs seront mieux servis par une âme universelle. Mais plus le fil d’apport et le matériau de la gaine guide-fil sont adaptés l’un à l’autre, moins il sera nécessaire de changer cette pièce d’usure. Si le même matériau est toujours soudé, il est alors systématiquement recommandé d’utiliser la gaine guide-fil spécifique prévue à cet effet.
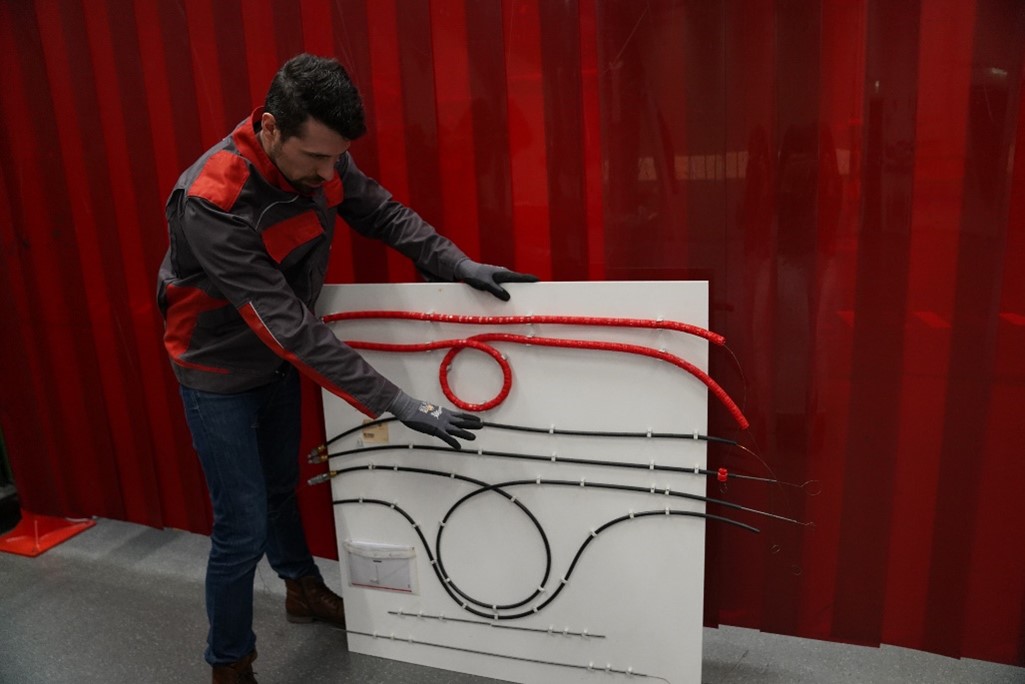
2. Des galets d’entraînement adaptés à l’épaisseur du fil
Mieux vaut harmoniser les pièces d’usure et le matériau d’apport pour un fonctionnement optimal des systèmes de soudage ; il en va de même pour les galets d’entraînement et le fil d’apport. En d’autres termes : le système de soudage doit être exclusivement équipé des galets d’entraînement recommandés par le fabricant pour l’épaisseur du fil concernée.
Agir ainsi contribue à assurer le fonctionnement optimal du dévidoir, qui influe à son tour positivement sur la stabilité de l’arc électrique. En cas d’écartement des bords des galets d’entraînement trop élevé ou trop faible pour le fil d’apport concerné, ce dernier est généralement tout de même amené. Cependant, en pareilles circonstances, le dévidoir ne fonctionne pas de manière optimale. Pour les procédés de soudage complexes d’un point de vue technique, tels que le soudage pulsé, les résultats laissent alors souvent à désirer.
Cela découle notamment du fait que la manipulation du bain de fusion est grandement tributaire du fonctionnement correct du dévidoir. En cas de fonctionnement insuffisant, de nombreux process de soudages ne sont plus commandés de manière optimale.
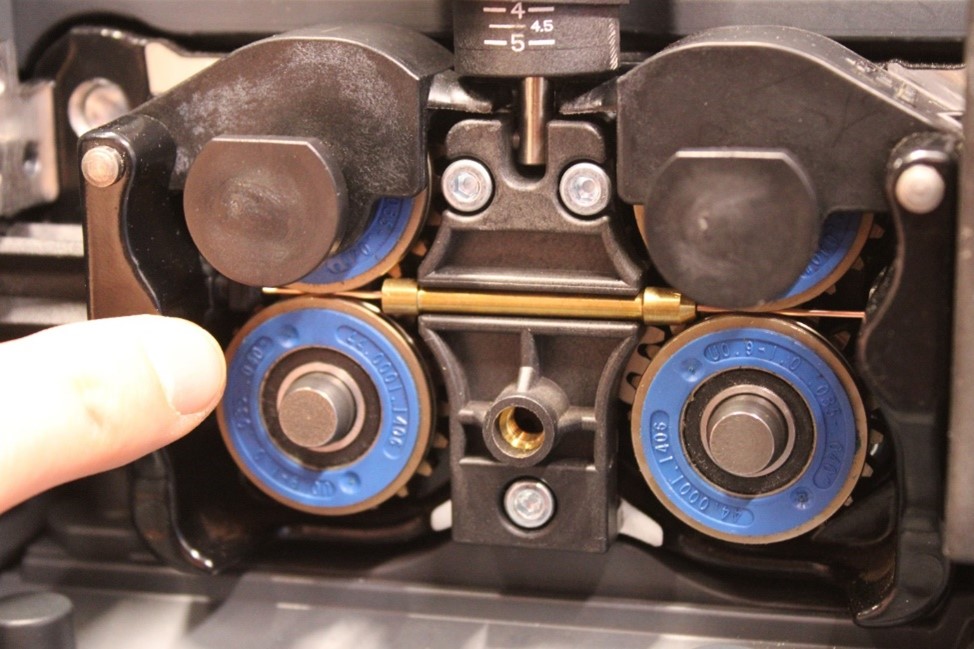
3. La pression d’appui, une histoire de réglage
Trouver l’alliance parfaite du fil et des galets d’entraînement ne dépend pas uniquement du choix des composants adéquats. Après avoir installé les galets d’entraînement recommandés par le fabricant pour le fil d’apport du système de soudage utilisé, il faut procéder au réglage de la pression d’appui optimale. De nombreux systèmes de soudage de qualité indiquent à combien doit en principe s’élever la pression d’appui à l’aide d’étiquettes signalétiques situées près des galets d’entraînement.
En s’appuyant sur les recommandations du fabricant, il est ensuite possible d’effectuer des réglages fins, d’autant plus que les torches de soudage ne sont pas identiques et qu’il peut également exister des différences d’un fabricant à un autre. Un peu de doigté et d’expérience représentent des atouts lors de ces réglage fins. En règle générale, le fonctionnement du dévidoir est optimal lorsque les galets d’entraînement entourent fermement le fil d’apport. La commande du système de soudage a alors pleinement le contrôle sur la vitesse d’avance du fil.
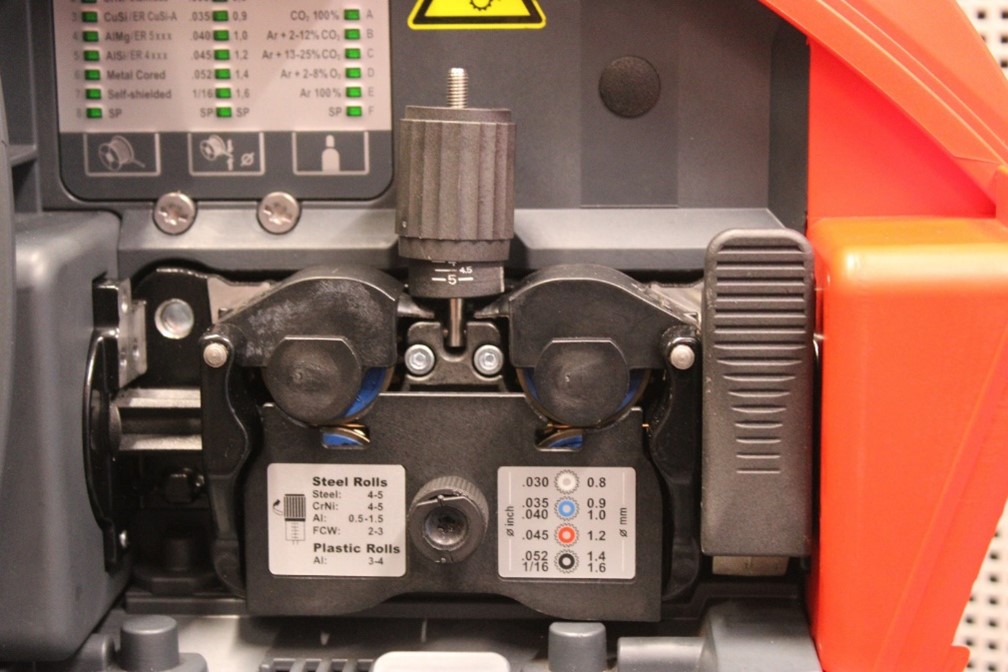
4. Une quantité optimale de gaz de protection
La quantité optimale de gaz de protection est l’une des conditions essentielles pour un arc électrique aux projections les plus faibles possibles et des soudures de qualité irréprochable. En matière de réglage de la quantité de gaz de protection pour le soudage MIG/MAG, la règle d’or est la suivante : multiplier par 10 le diamètre de fil. Par exemple, pour un fil de 0,8 mm de diamètre, la quantité recommandée de gaz de protection est de 8 litres/minute.
La distance entre la torche de soudage et la pièce à souder est un autre facteur déterminant pour la quantité de gaz de protection. Plus elles sont éloignées, plus une grande quantité de gaz de protection sera nécessaire pour que l’arc électrique soit stable. En partant du principe « diamètre du fil x 10 », des réglages individuels fins doivent ici aussi être effectués. Avoir de l’expérience dans le domaine du soudage s’avère alors utile dans tous les cas. Quelques essais sont parfois requis avant de réussir à régler correctement la quantité de gaz de protection.
5. Une orientation la plus parallèle possible de la torche de soudage vis-à-vis de la masse
En principe, en matière de soudage, un fil en métal est poussé à une vitesse relativement rapide à travers une torche de soudage, dont la durée de vie est élevée s’il est orienté de la manière la plus droite possible.
Les torches des systèmes de soudage de qualité sont certes conçus spécifiquement pour fonctionner sans heurts, même en cas d’enroulements et de boucles extrêmes, mais le soudage le plus économe en énergie et le plus respectueux des ressources est uniquement possible si le faisceau de liaison est installé parallèlement au câble de mise à la masse.
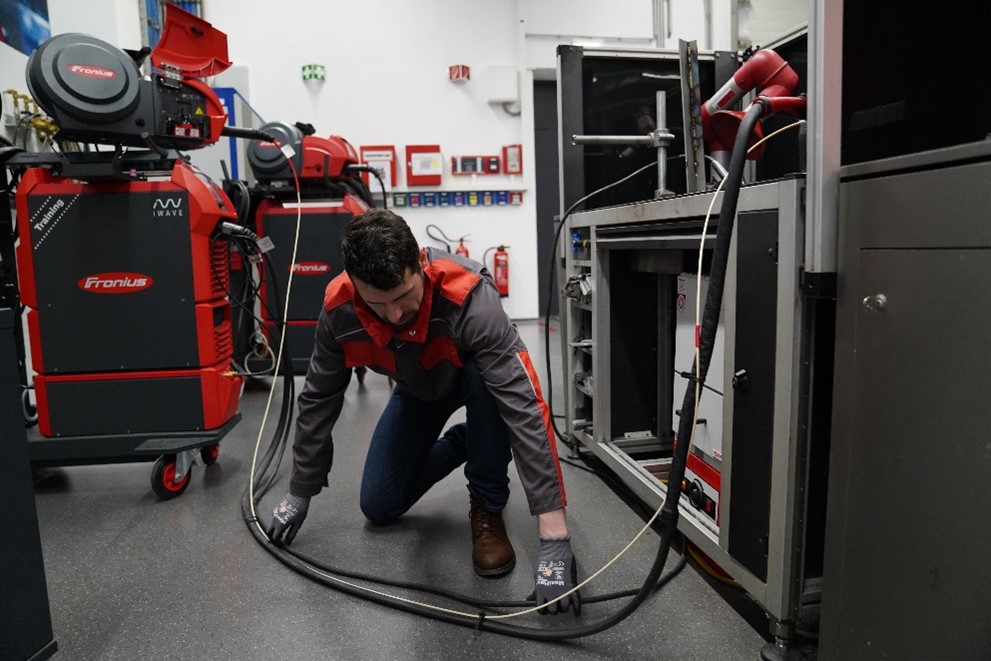
6. Le calibrage du câble de mise à la masse : procéder à l’ajustement R/L
Dernier point, mais non des moindres : le soudage nécessite que le flux des électrons du pôle négatif au pôle positif, c’est-à-dire le courant, soit adéquat. Selon le process de soudage, il n’est pas toujours identique, puisqu’il dépend de plusieurs facteurs, entre autres du type de métal à souder et des diverses résistances qui y sont liées. L’ajustement R/L antérieur au soudage permet de régler de manière optimale le système de soudage sur le circuit électrique concret sur place, afin de compenser les erreurs dues aux éventuels enroulements et boucles. La lettre « R » désigne ainsi la « résistance », et la lettre « L », l’« inductance ».
Les systèmes de soudage de pointe révèlent tout particulièrement leur plein potentiel lorsqu’un ajustement R/L a été effectué avant le soudage. Il suffit généralement d’une pression rapide sur une touche pour y procéder ; peu d’efforts sont donc requis pour profiter des meilleures performances du système de soudage, et atteindre des résultats de soudage parfaits.
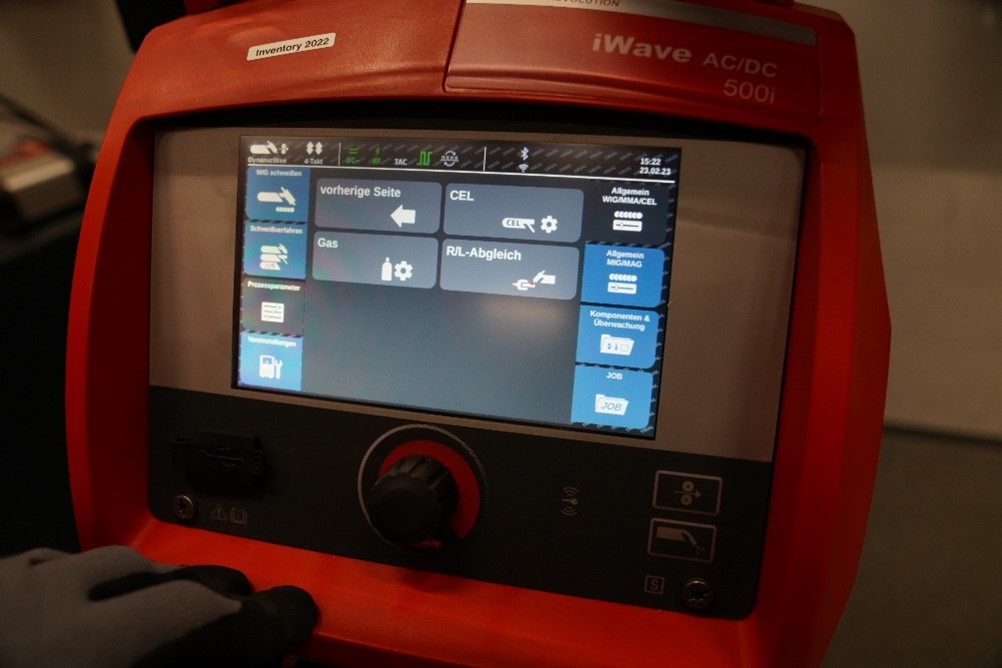
L’expérience des équipes de service
Si quelque chose tourne véritablement mal lors de l’utilisation de systèmes de soudage modernes, on finit presque toujours par consulter les équipes de service du fabricant :
« Notre expérience quotidienne démontre que la plupart des erreurs qui surviennent avec les systèmes de soudage sont dues à une utilisation non conforme. Même si nos systèmes sont des plus robustes et sont équipés de pièces d’usure de grande qualité, les résultats de soudage et la durée de vie du système de soudage et des pièces d’usure seront à leur paroxysme si l’on suit fidèlement les instructions du fabricant et si l’on connaît bien le système ».
Patrick Bezrucka, Strategic Product Manager – Product Lines Services chez Fronius
À propos de la durée de vie des pièces d’usure : cet article vous prodiguera 4 conseils pour augmenter la solidité des tubes contact et des buses de gaz. Jetez-y un œil !
Si vous avez des questions à propos de cet article de blog ou si vous avez besoin d’aide pour calibrer parfaitement votre système de soudage Fronius, vous pouvez contacter nos équipes de service via ce lien. Nous nous tenons à votre disposition pour vous conseiller et vous assister !
Aucun commentaire