Co má jedno z nejlepších terénních vozidel pro každodenní použití na světě společného s dokumentací nastavení svařovacích parametrů? Enormní světlá výška a obrovská hloubka brodění Mercedesu G dávají na první pohled tušit, že vůz musí obstát i v těch nejnáročnějších terénních podmínkách – vždy přitom musí být zaručena tažná síla a dlouhá životnost. Pokud je vůz vystaven prudkým nárazům ve vysoké rychlosti na nesjízdném terénu, znamená to také neustálé vysoké namáhání všech svarů. Proto je zde tak důležité zajištění kvality a optimalizace výrobních procesů na základě sofistikovaného systému správy svařovacích dat.
Optimalizace výroby rámů Mercedesu G ve společnosti Magna Presstec
Nejvyšší nároky na kvalitu třídy G – vyžadované výrobci i koncovými zákazníky – se odrážejí i v poptávce: Zájem o luxusní terénní vozy neustále roste. Aby bylo možné splnit požadované počty kusů, je při výrobě rámu podvozku naprosto nezbytná vysoká míra automatizace a optimalizace výrobních procesů.
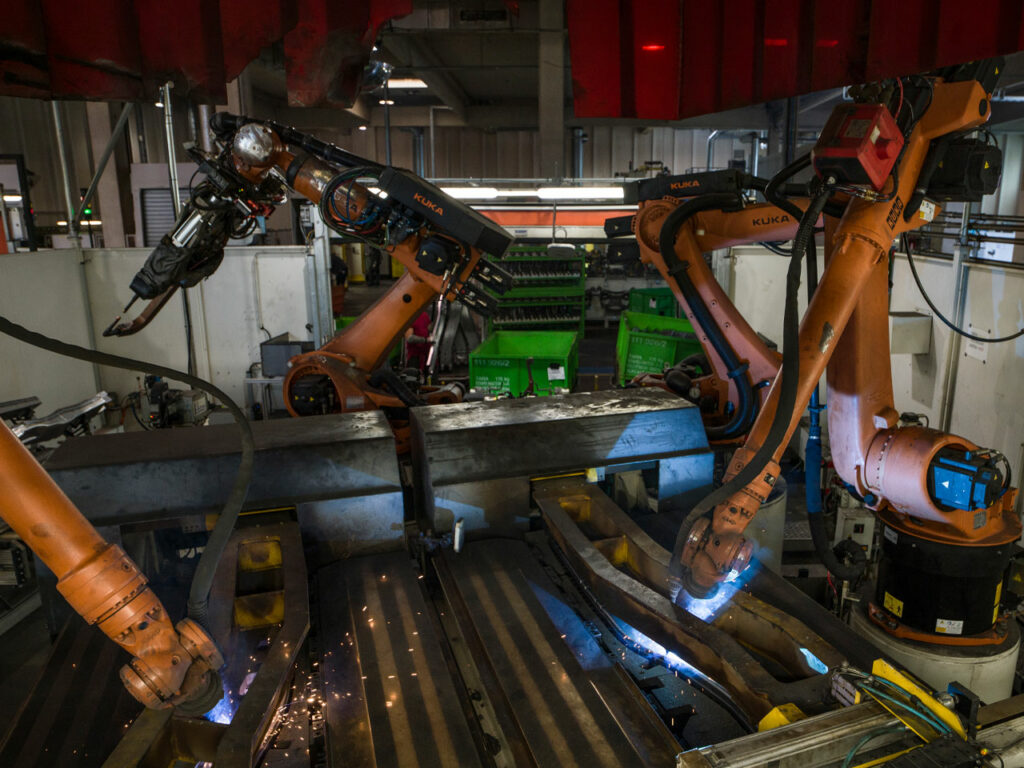
Technologicky vyspělá výrobní linka společnosti Magna Presstec, dodavatele Tier 1, v Lebringu na jihu Rakouska má vše: Na délce 100 metrů jsou systémy manipulačních a svařovacích robotů dokonale propojené. Extrémně rychlý, vysoce přesný a digitálně řízený pulzní svařovací proces (Pulse Multi Control od společnosti Fronius) přitom splňuje vysoké požadavky na zásadně nezbytnou technologii spojování.
Pouze na začátku se výrobní linka zásobí jednotlivými díly. Každých 10 minut pak vyjede z dílny hotový rám podvozku Mercedesu G, který je jako mávnutím kouzelného proutku zavěšený na mostovém jeřábu.
Extrémně složité: podrobný popis autonomní špičkové výroby
„Naším požadavkem je, aby všechny rámy byly naprosto stejné. Odchylky musí být vyloučeny“, energicky vysvětluje Kurt Hartmann, vedoucí výroby a svářečský dozor ve společnosti Magna Presstec.
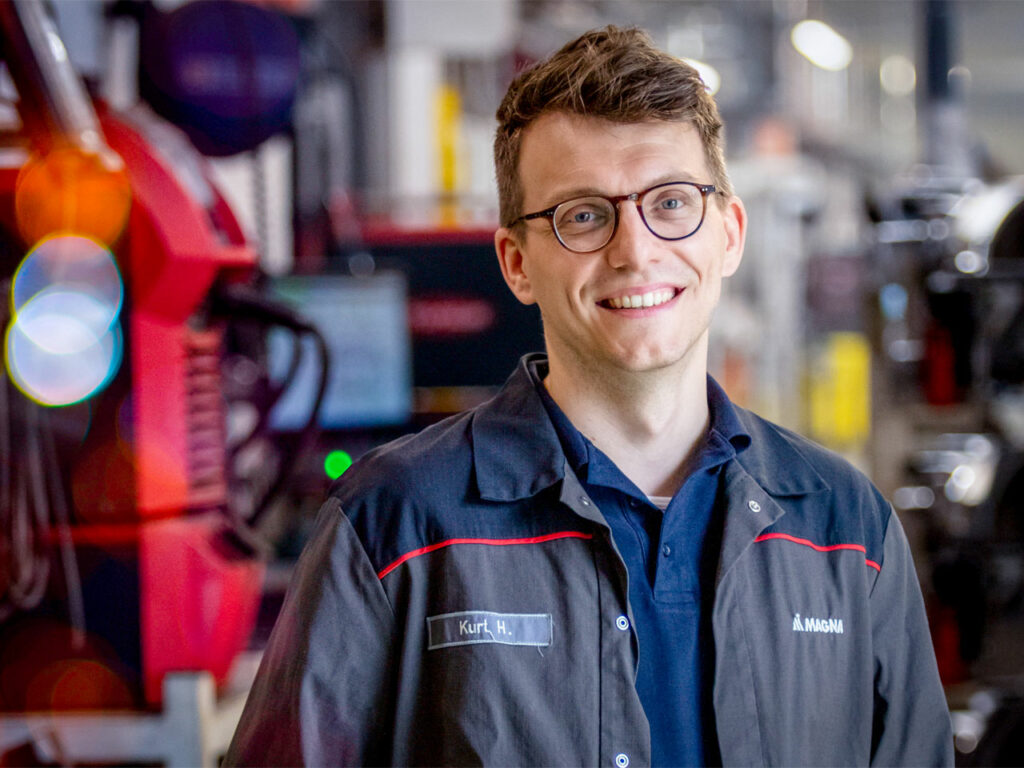
Přední a zadní část: „Vyrábíme zde ve třech sekcích,“ podrobně vysvětluje K. Hartmann. „Přední a zadní část (rámu) – tedy první dvě sekce výrobní linky – se vyrábějí současně. Tady nejprve několik zaměstnanců vybavuje svařovací přístroje.
V buňkách se pak komponenty spojují pomocí svařovacích robotů. Manipulační robot odebírá hotové komponenty, přepravuje je do další buňky a tam je polohuje. Na konci každé sekce se nachází buňka, která je pro personál nepřístupná. Ta slouží ke svařování dlouhých svarů. Buňky se však používají také jako chladicí stanice nebo jako komplexní stanice, např. pro lisování: Zde se spodní skořepiny vkládají do horních skořepin podélných nosníků, polohují se a pod tlakem svařují.“
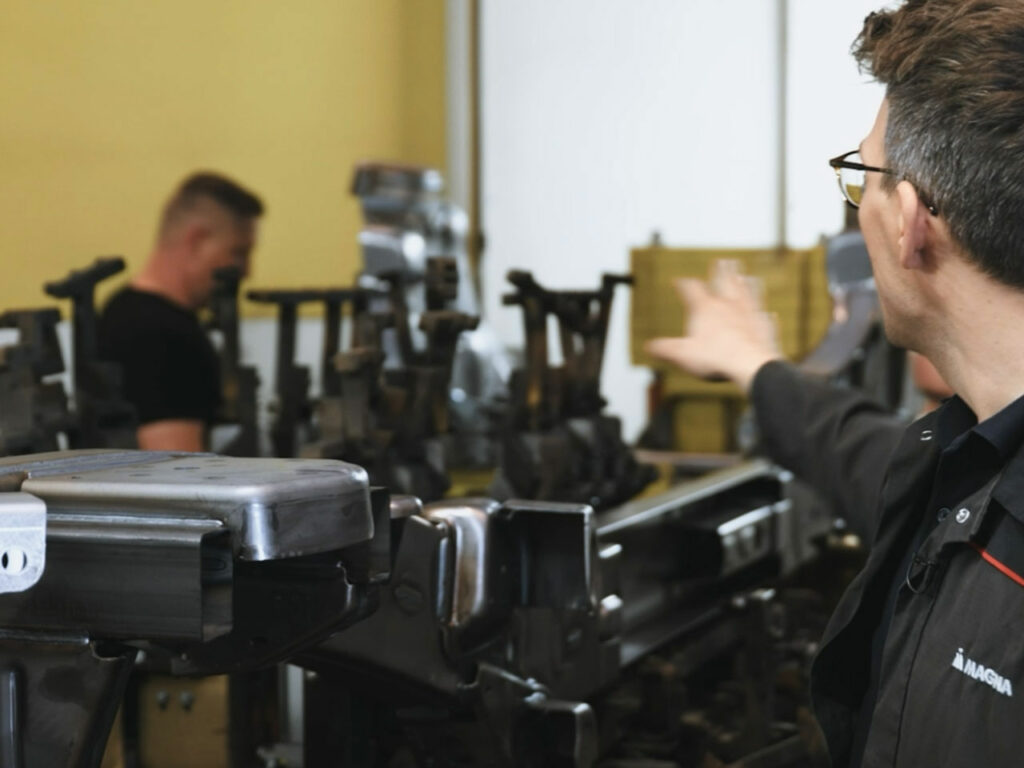
Konstrukce podvozku: „V poslední fázi výroby, v konstrukci podvozku, se přední a zadní část spojí dohromady. Rám dostane svůj charakteristický tvar,“ dále rozvádí K. Hartmann. Závěrečné pracovní kroky pak zahrnují vyražení odpojených spojovacích bodů podvozku. Kromě toho zdvihové zapalování nastřílí na rám 192 čepů. Vyškolený svářeč pak zkontroluje kvalitu svarů, odstraní poslední svařovací rozstřiky a v případě potřeby svary přepracuje.
Pro kompletní zajištění kvality se provádí stoprocentní proměření rámu robotickou laserovou měřicí technikou. Po poslední kontrole rám opustí karosárnu prostřednictvím systému Power&Free (dopravník). Následuje předání k dalším procesním krokům.
Pro zajištění kvality: Monitorování nastavení svařovacích parametrů pomocí aplikace WeldCube Premium
Samotný vynikající svařovací proces však nestačí k tomu, aby společnost Magna Presstec splnila obrovské nároky na kvalitu modelu G. Je třeba systém, který nahradí chybějící „oči“ na 100 metrů dlouhé výrobní lince – tedy možnost 100% monitorování a kompletní dokumentace svařovacího procesu.
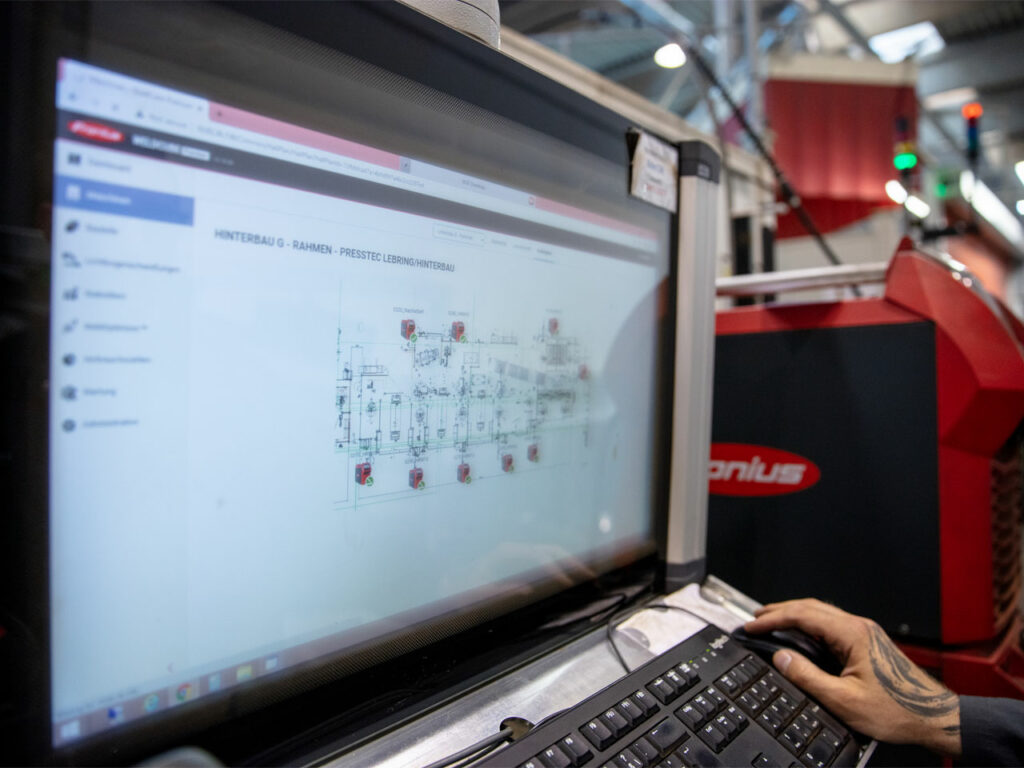
„Ve výrobní hale je software WeldCube Premium základním pilířem řízení kvality,“ je přesvědčen K. Hartmann. „Absolutní vysledovatelnost každého jednotlivého svaru pro nás má zásadní důležitost. Na stanicích kontroly kvality dostávají vyškolení pracovníci přesné informace prostřednictvím terminálu: Jsou nějaké nápadné nebo skutečně vadné švy?
Prostřednictvím WeldCube – tedy na základě nastavení svařovacích parametrů – jsou odhalena případná chybná místa, která se podrobí důkladné vizuální kontrole a případně dopracují. Teprve poté je G-rám uvolněn pro další procesní kroky.“ Shromážděná data se pak zase využijí při optimalizaci výrobních procesů a automatizovaných svařovacích procesů.
Od monitorování k prediktivní údržbě
„Jelikož WeldCube Premium zaznamenává každý milimetr svaru bez výjimky, můžeme pomocí analytických nástrojů hravě vypočítat náklady na spotřební materiál, jako je plyn a svařovací drát. Vidíme zde však mnohem větší potenciál: Jedním z bodů by jistě byla Predictive Maintenance (prediktivní údržba), tedy možnost včas a v dostatečném množství objednat spotřební díly a materiály,“ nastiňuje K. Hartmann vyhlídky do budoucna.
„Predictive Maintenance prostřednictvím WeldCube Premium by nám navíc mohla nabídnout obrovské možnosti úspor, například pokud nám správa svařovacích dat poskytne přesné intervaly údržby. Vždy bychom tak přesně znali stav kontaktních špiček, těl svařovacích hořáků, svařovacích hořáků a podavačů drátu. To by nám umožnilo provést servis přístrojů ve správný čas, takže bychom se vyhnuli vadným svarům, předělávkám nebo dokonce zmetkovitosti dílů.“
Pro speciální úkoly: jen odborníky!
Dokumentace a analýza nastavení svařovacích parametrů však společnosti Magna Presstec nestačí: „Kromě toho již používáme softwarové řešení Central User Management (CENTRUM) – které nás také podporuje v řízení kvality. Díky tomu přiřazujeme centrálně řízená uživatelská a svařovací oprávnění. Svářeč se u svařovacího zdroje prokáže čipovou kartou. Tak dokážeme zajistit, že s určenými parametry a na správném místě pracují pouze pracovníci vyškolení pro specifické úlohy. Tímto způsobem nejlépe vyloučíme další zdroje chyb,“ je přesvědčen K. Hartmann.
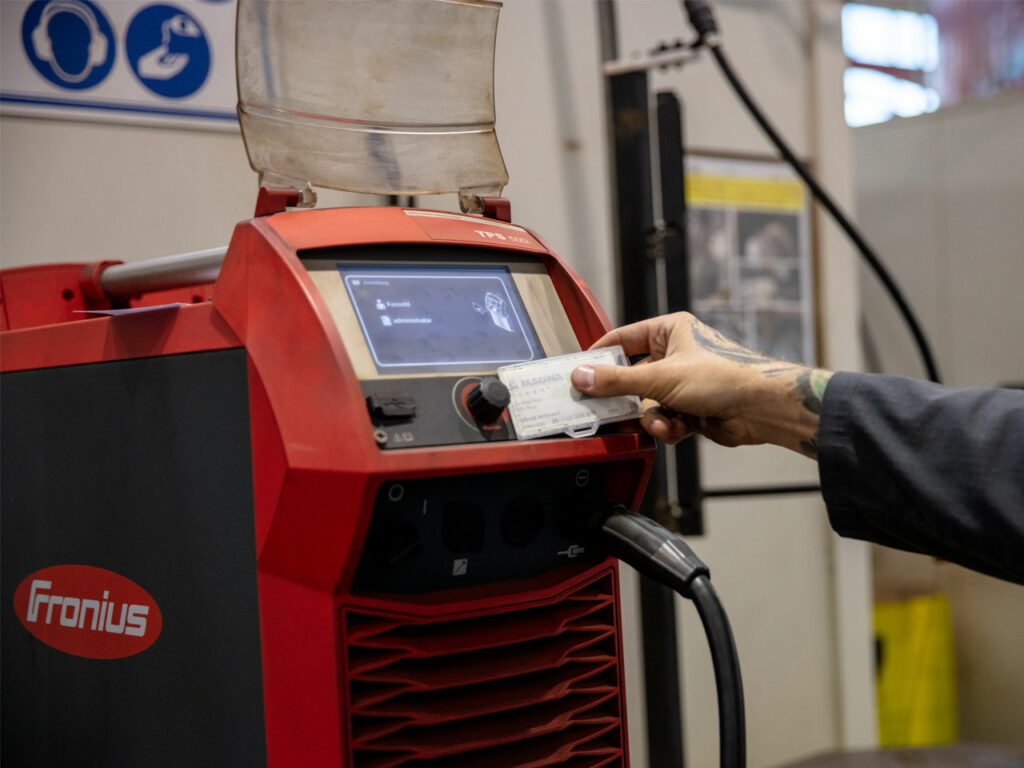
Řešení týkající se dokumentace nastavení svařovacích parametrů od společnosti Fronius
Všechna softwarová řešení používaná společností Magna Presstec byla vyvinuta společností Fronius. Počínaje aplikací WeldCube Premium až po Central User Management jsou však všechny produkty výsledkem intenzivní výměny zkušeností se společností Magna Presstec: Teprve dlouhodobé testování prototypů ve výrobě společnosti Magna umožnilo získat potřebné informace a dosáhnout zralosti pro uvedení na trh.
Podívejte se na náš krátký dokument o výrobě rámu Mercedesu G v společnosti Magna Presstec, dodavatele Tier 1:
Pokud vás zajímají také naše perspektivní řešení podporující autonomní výrobu, nabízíme vám zde další informace o produktech.
Žádné komentáře