Gas metal arc welding falls broadly into two categories: Metal Inert Gas (MIG) welding and Metal Active Gas (MAG) welding. Within these two groups, the market offers endless choice, with a host of solutions for different processes and control options. Yet the design of the welding torches is almost identical, with only a few small internal differences depending on the process in question.
So what exactly is a “welding torch” and a “MIG/MAG welding torch” in particular? Read on to find out more.
Standard MIG/MAG Welding Torch Design
Put simply, the welding torch is everything from the start of the hosepack up to the gas nozzle. A MIG/MAG welding torch therefore includes the connection between the torch and the union nut plus the shielding gas hosepack, as well as the various conduits, such as the protective hose, water inlet and outlet for water-cooled torches, power cable, gas hose, and inner liner.
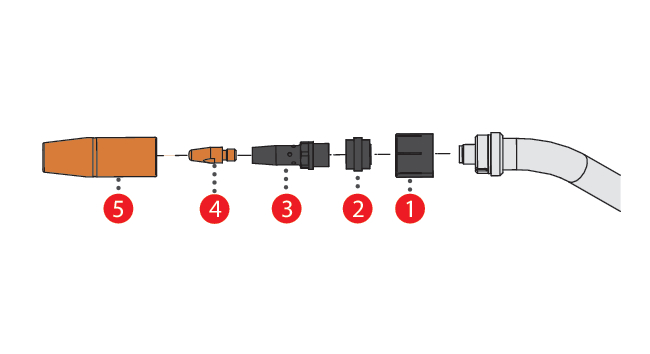
The welding torch package also includes the handle with torch trigger and the torch neck with wearing parts such as the gas nozzle, contact tip, nozzle fitting and spatter guard. All together, a standard model measures up to six meters in length.
When purchasing a welding torch, it is important to look at the amperage. It makes no sense to use a 600 A welding torch with a power source that can only put out up to 220 A, nor to fit a high performance welding system with the smallest available torch. Your MIG/MAG welding torch should always be suitable for the maximum power range of your power source.
Gas-cooled or Water-cooled?
Another key question is whether to opt for gas or water-cooled. It’s a bit like buying a motorbike—should you go for the air-cooled single cylinder engine or the water-cooled four-cylinder one? The fact is water-cooled designs are often more durable and certainly boast better handling.
And welding systems are no different: Anyone who has used a welding system with water cooling right up to the tip of the gas nozzle will tell you how smooth the torch control felt and how easy it was to handle. Plus, water-cooled systems last longer and provide more power. Air-cooled welding torches are not suitable for higher amperages, whereas water-cooled torches continue to perform well at amperages up to 200 A higher.
Naturally, the advantages of water-cooled over gas-cooled come at a cost, with purchase prices for water-cooled torches coming in 20–30% higher on average. There is also the additional cost of installing the water cooling system itself. As wearing parts, welding torches will form part of your ongoing operating costs and therefore price is an important consideration when deciding between gas or water-cooled options.
Control Functions for your MIG/MAG Welding Torch
Once you’ve decided on your preferred cooling option, the next question to ask is what operating controls you want. Do you need something simple or more multifunctional? What controls does your welding torch need to meet your welding requirements? The most basic option is a simple on-off switch, or torch trigger. But even then there are choices to be made: Do you want the trigger at the top or bottom? Ultimately, this comes down to welder preference—trigger at the top if you prefer to use your thumb or at the bottom if you prefer to use your index finger.
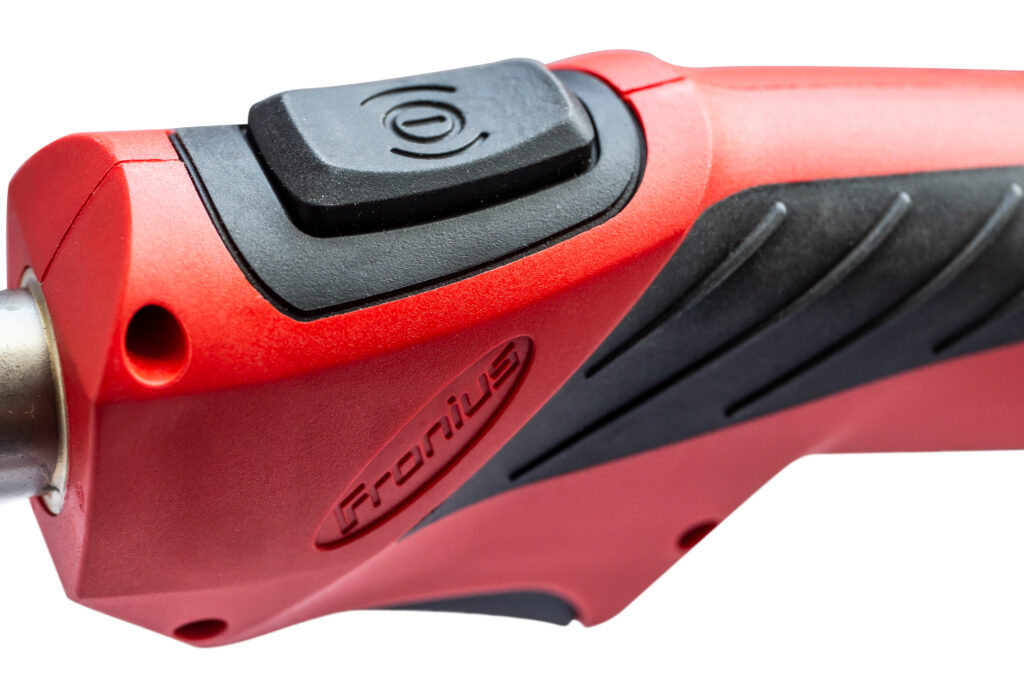
Perhaps you want to be able to increase or decrease the amperage whilst welding? A simple rocker switch on the top of the torch enables the welder to adjust the power up and down without stopping welding or changing their grip.
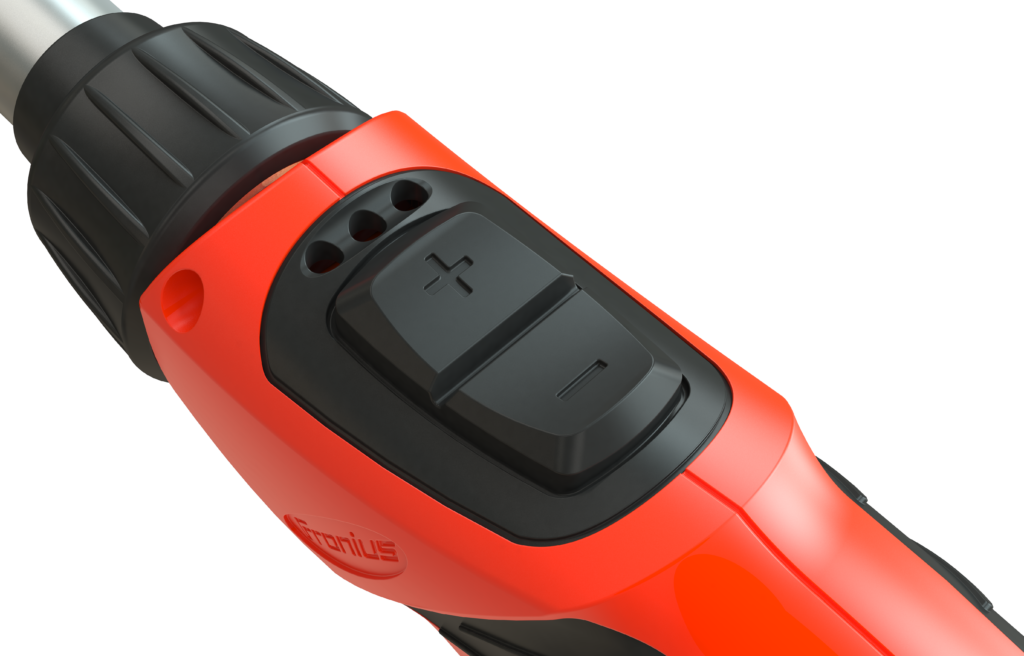
If you’re using a digital power source, there are many more sophisticated control functions available for your welding torch. Looking for something more advanced than simple power controls? Then you should opt for a torch with additional controls that link to all the different settings shown on the power source display. Each individual parameter can be viewed on the torch’s small display and selected or adjusted as necessary. There is also an option set specific parameters on the power source for a particular welding task or “job”. These presets can then be activated on the torch itself.
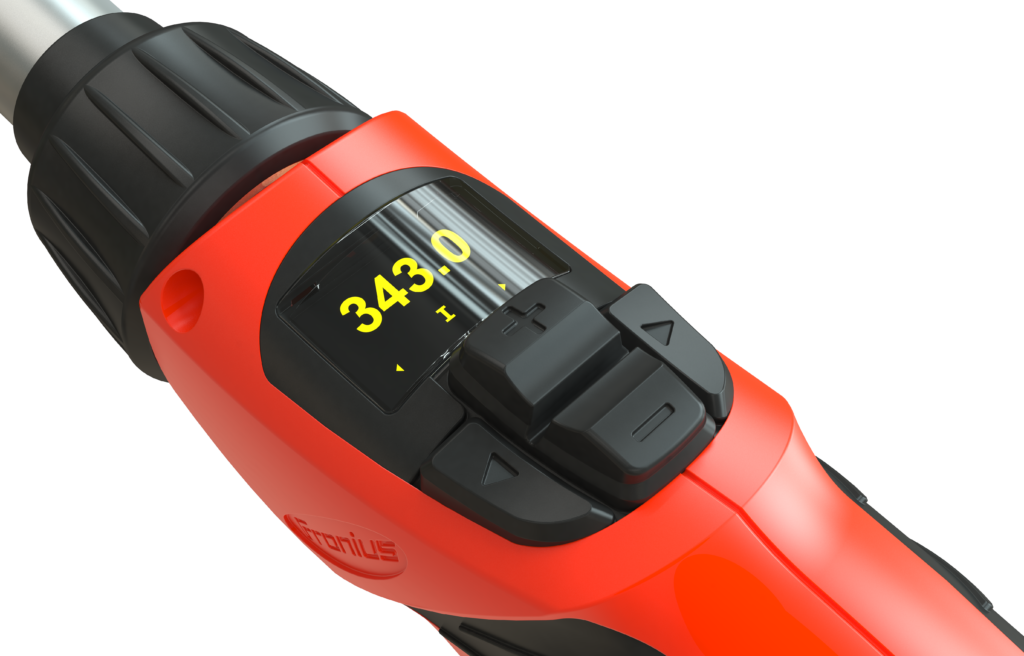
All the settings you need in your everyday work can be controlled directly on the MIG/MAG welding torch without any need to use the controls on the welding system itself. These multifunctional torches are especially advantageous when welding in positions where the power source cannot be positioned right next to the weld site or where longer hosepacks are needed to access hard-to-reach components.
Multilock: Single Welding Torch—Multiple Variants
Multifunctional means more than just a range of process controls. Our Multilock system has been designed with ultimate flexibility in mind, enabling welders to change the torch body, depending on the shape of the component to be welded and how accessible it is. By interchanging torch bodies with different lengths and angles, you can achieve exceptional welding results no matter how challenging the task.
Multilock is also really handy for replacing defective parts. For instance, if the torch body is damaged but the hosepack is absolutely fine, the torch body alone can be changed quickly and easily thanks to the Multilock connection.
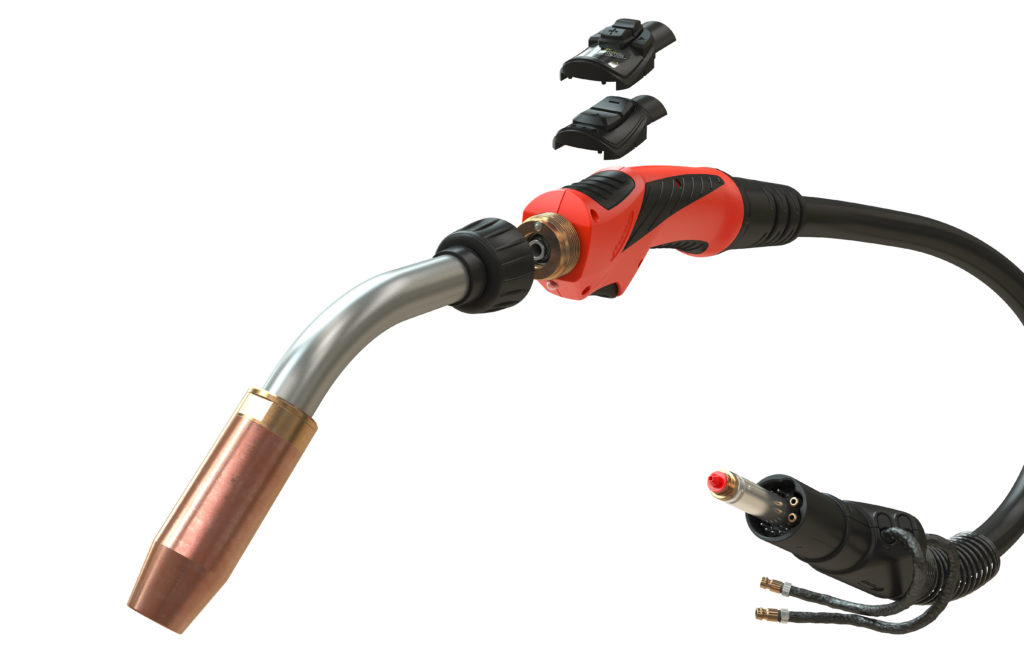
The torch neck can also be rotated through 360° thanks to this specially designed connection. For instance, turning it 180° to point upwards makes it easy, not to mention ergonomic, to complete welding tasks in an overhead position. The operation of the torch trigger remains the same. Note that when installing a Multilock system, you will also need to use a Multilock shielding gas hosepack.
The Right Welding Torch for every Application
As we have seen, most gas shielded arc welding jobs require a universal MIG/MAG welding torch, while some require a more specialist option. At Fronius, we offer a wide range of premium quality torches, so you are sure to find the perfect choice for your power source and process. To find out more about our product portfolio, click here.
If you want to discover more about the fundamentals of MIG/MAG welding, then you can read our blog article here.
No Comments