Why should you clean stainless steel welds thoroughly after TIG welding? There are two compelling reasons for this. Firstly, it just looks better. And secondly – and this is the real clincher – properly cleaning welds prevents corrosion, i.e., the long-term degradation of the stainless steel. So, the only question that remains is how best to remove annealing colors from TIG welds.
In principle, there are three tried-and-tested methods for removing annealing colors from a stainless steel TIG weld:
- The chemical method, which uses an aggressive pickling fluid consisting of hydrofluoric, nitric, and sulfuric acid
- The mechanical method, which involves manual brushing, e.g., with a stainless-steel wire brush, or rotating plastic brushes or non-woven cloths
- The electrochemical method, which uses electricity and an electrolyte fluid
All three methods are useful in different situations, but they all function more or less according to the same principle: The passive layer destroyed by the heat of the arc during welding is restored. To understand what exactly is going on here, we need to take a quick look below the surface of stainless steel.
Stainless steel TIG weld before and after cleaning:
Long live the passive layer!
Stainless steel—also called rustless steel or chromium-nickel steel—generally has a chromium content of over 12.5% and a carbon content of less than 1.2%. If the chromium contained in the stainless steel comes into contact with oxygen, a thin layer of chromium oxide is formed, which is referred to as the passive layer. This passivation process prevents oxidation and corrosion. Therefore, it is the passive layer that gives stainless steel its most important property.
The passive layer of stainless steel is very difficult to destroy. But the arc of a TIG welding system—which can be as hot as 10,000°C—makes light work of it and immediately exposes the passive layer to atmospheric oxygen. This then produces the typical annealing colors, which indicate that the passive layer has been stripped away at the corresponding location.
Point of entry for rust
The surface structure of the stainless steel at the annealing colors is rougher and thus more susceptible to corrosion. In other words, the stainless steel—which is meant to be resistant to rust—can start to rust at the points where the passive layer has been destroyed. On top of that, these roughened surfaces of the annealing colors provide an ideal home for bacteria, which is above all problematic for applications in which the highest standards of hygiene are essential, for example in the field of healthcare or food processing.
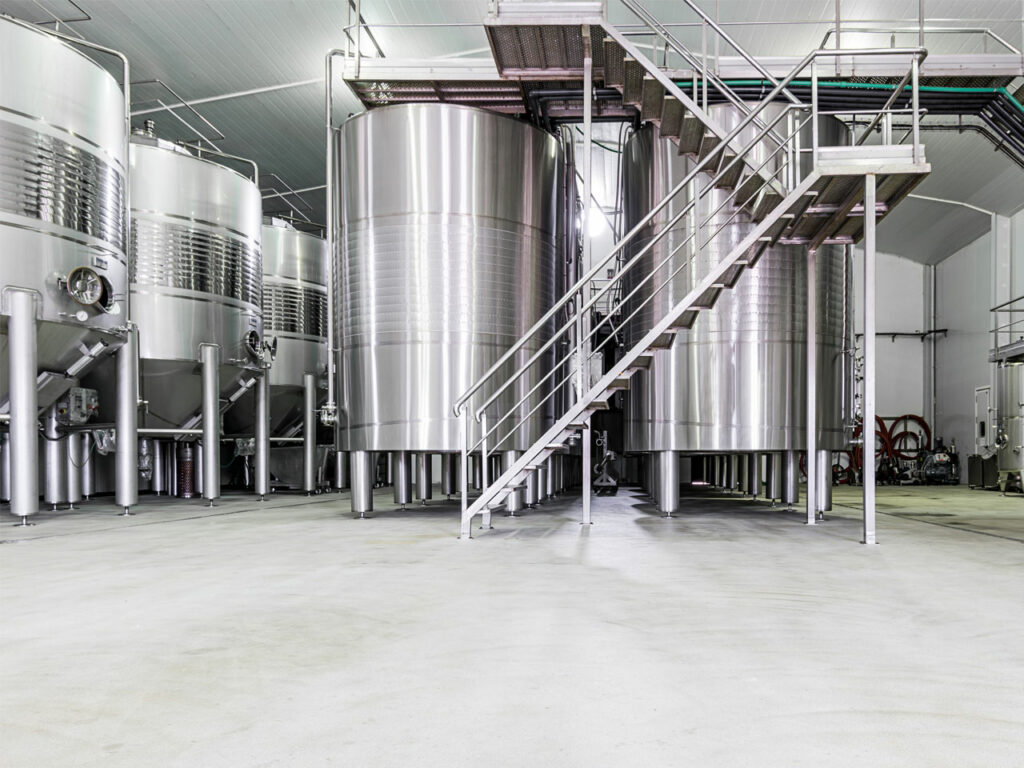
© Adobe Stock / charlymorlock
But which of the three methods is the best for cleaning stainless steel welds? To answer this question, we must first look at how the individual methods differ from one another.
Chemically cleaning stainless steel welds: pickling
Anyone who wants to go down the chemical route for cleaning stainless steel welds needs one thing: a lot of chemicals. The pickling fluids or pastes contain a mixture of hydrofluoric, nitric, and sulfuric acid. They are generally brought into contact with the TIG weld by means of a pickling bath, spraying, or a brush. After the pickle has removed the annealing colors, it takes a while for the passive layer to grow back in the next step. Once it has, the corresponding points are once again protected against corrosion.
The main advantage of pickling is its thoroughness. Another major benefit is that larger stainless metal surfaces and several welds can be cleaned at the same time in industrial pickling baths.
The main disadvantage of chemical weld cleaning is the danger posed to human bodies and the environment: pickle attacks human skin, eyes, and respiratory tracts, and can permanently damage the internal organs. This incurs high lifecycle costs associated with occupational safety and the proper disposal of the pickle.
Mechanically cleaning stainless steel welds
Stainless steel welds can also be cleaned by mechanical means, for example using stainless steel wire brushes, rotating plastic brushes mounted on drill drivers or cordless drills or using a non-woven cloth. This almost always requires physical exertion. But the main advantage of mechanical cleaning is the relatively low procurement costs for the devices and auxiliary materials used.
However, the removal of annealing colors with brushes or cloths is very time-consuming. In addition, unsightly scratches may be created on the TIG welds and base material, especially if the person brushing the welds is not very practiced at it. The main argument against mechanical weld cleaning is that not all points can be reached, which means that corrosion can still occur.
As with pickling, the passive layer takes a while to recover after the annealing colors have been mechanically removed from the weld. This method is mainly used in the hobby sector or by small companies who only occasionally have to clean stainless steel welds.
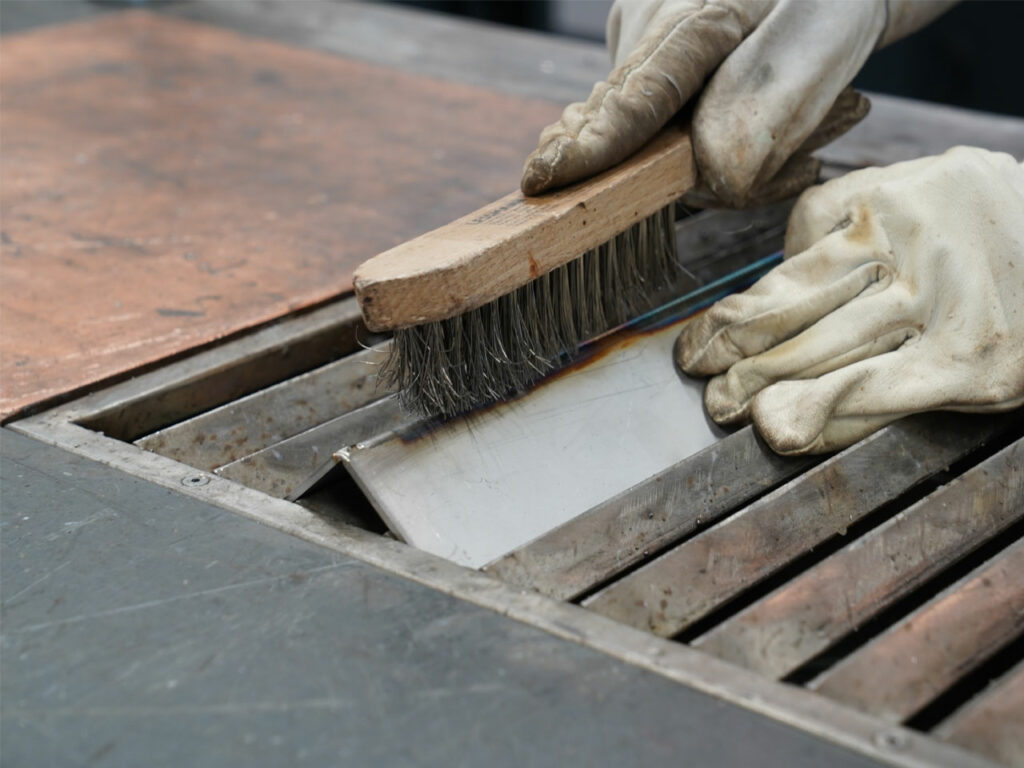
Electrochemically cleaning stainless steel welds: professional weld cleaning devices
Weld cleaners are devices that clean stainless steel welds quickly, thoroughly, and safely. For electrochemical cleaning, you will need an electrolyte fluid and a standard alternating current in addition to the weld cleaning device. The electrolyte fluid is simply applied to the TIG welds or stainless-steel surfaces to be cleaned.
The subsequent electrochemical cleaning process is similar to that of welding: The component with the weld to be cleaned is connected to the cleaning device via a grounding cable. The cleaning pad or the carbon fiber brush connected to the positive terminal of the weld cleaner is then simply moved over the weld wetted with the electrolyte fluid. Most of the work is done by the alternating current with alternating cathodic and anodic polarization. This removes the annealing colors without altering or damaging the surface of the stainless steel.
On top of that, oxygen splits off from the electrolyte fluid during evaporation and immediately binds to the chromium contained in the stainless steel so as to produce the protective passive layer. The cleaning and the restoration of the passive layer – the passivation – therefore take place in the same work step. Unlike in pickling or mechanical weld cleaning, you do not have to wait for the passive layer to grow slowly back by itself.
You can see how weld cleaners are used for electrochemically cleaning TIG welds in the following video about the new weld cleaning device—the MagicCleaner 150 or 300:
Cleaning welds: Which method is best?
Essentially, all three methods mentioned have their virtues:
Chemical weld cleaning / pickling makes sense for some systematized production processes. The disadvantage of this method is that the pickle is not compatible with humans and the environment and incurs associated costs.
The advantage of mechanical weld cleaning is the low procurement costs for stainless steel brushes or cloths. The disadvantages are that it is very time-consuming and is not always one hundred percent reliable.
Electrochemical cleaning of stainless-steel welds is quick, easy, and, above all, thorough—even outside buildings. The removal of the annealing colors and the passivation occur in a single work step. But it is crucial that you have the right weld cleaning device on hand.
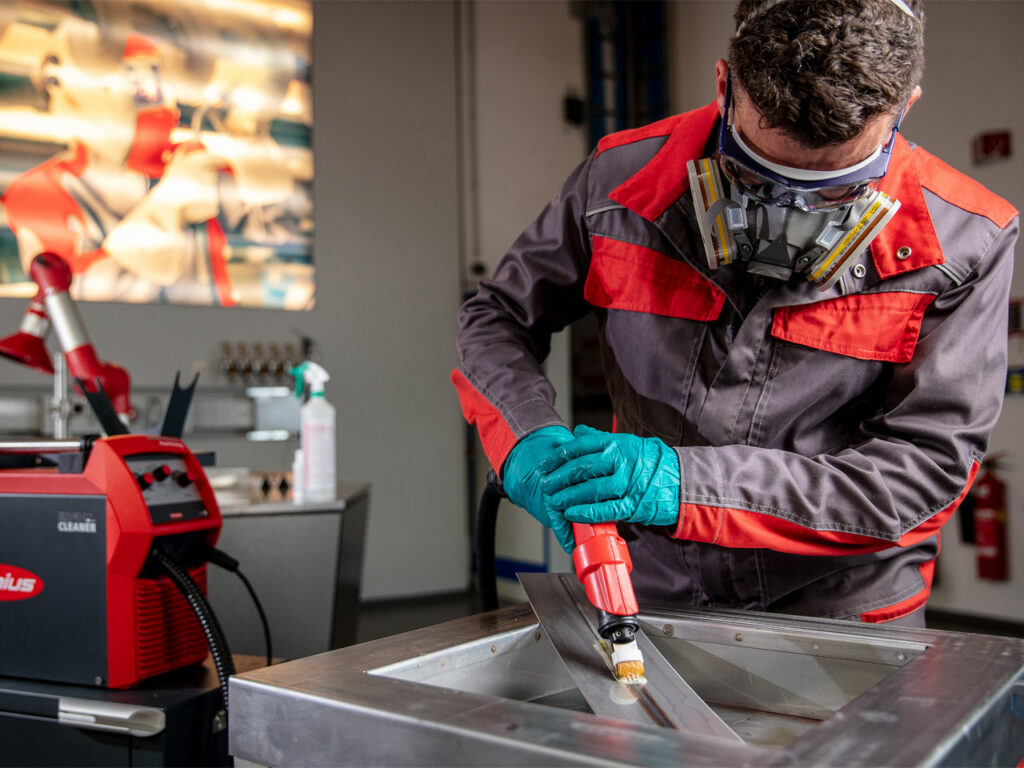
What makes a good weld cleaning device?
Anyone interested in professional electrochemical weld cleaners should look out for a few important factors and features when choosing the right device:
- In-depth expertise of the provider in the field of welding technology
- Simple, self-explanatory operation
- Ready to use in just a few steps
- Sparing use of the electrolyte fluid / simple and precise dosing
- Low energy consumption
- Robust product housing while being as light as possible
- High-quality accessories for different uses
- Easily accessible and/or regional distributor and service network
With the models MagicCleaner 150 and MagicCleaner 300, Fronius launched a new generation of multifunctional weld cleaners for electrochemically cleaning stainless steel welds onto the market in February 2022.
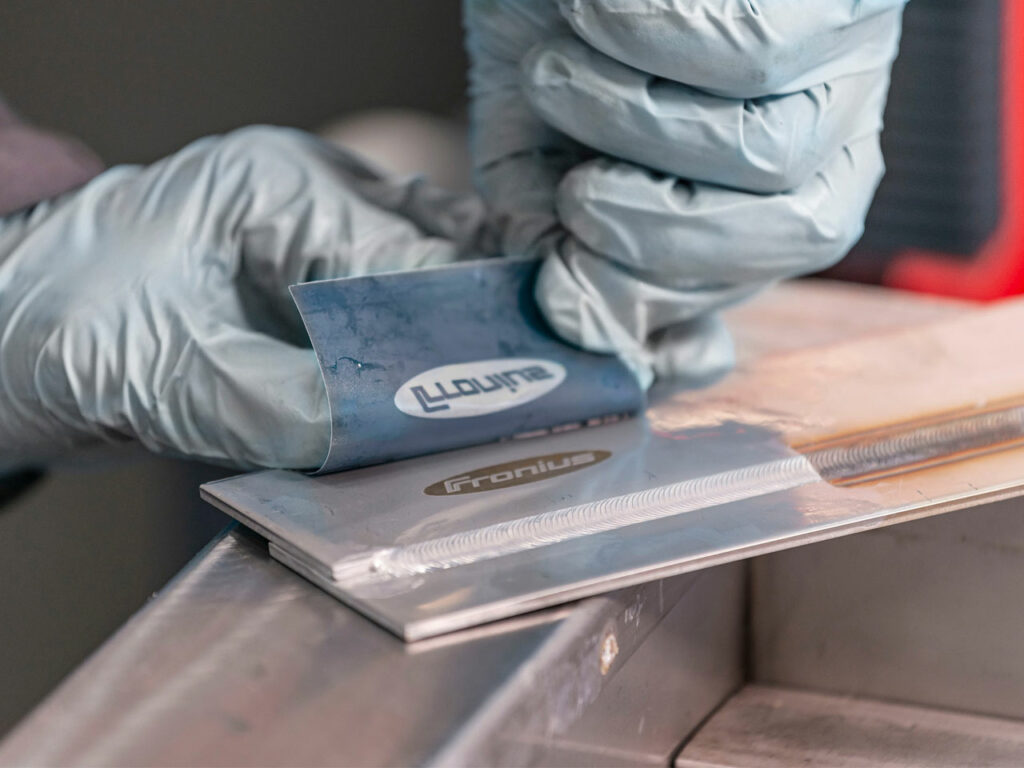
In addition to stainless steel weld cleaning and passivation of stainless-steel welds, the new MagicCleaner devices can also be used to polish and print. The polishing process ensures uniformly shiny stainless-steel surfaces after cleaning. And the print function makes it possible to permanently label stainless steel surfaces as a simple alternative to stickers or laser engraving.
You can find more information on the new MagicCleaner devices at: https://www.fronius.com/magiccleaner
2 Comments
S R UNNI
13. May 2022 at 15:58very interesting information, useful applications with latest technology.
redakteur
16. May 2022 at 7:46Thank you very much!