Almost any material can be welded using common welding processes: metal inert gas or metal active gas (MIG/MAG), tungsten inert gas (TIG) or electrode (manual metal arc) welding methods. Which process to use depends on the requirements of the component and the production process. Johann Dallmannsböck, trainer at Fronius International’s Welding Business Academy, explains which welding process to use and when.
Welding speed
MIG/MAG can reduce welding times. This welding process lends itself to automation, which makes joining particularly quick and speeds up the entire production process. Electrode welding and TIG welding in particular cannot keep up with such high welding speeds.
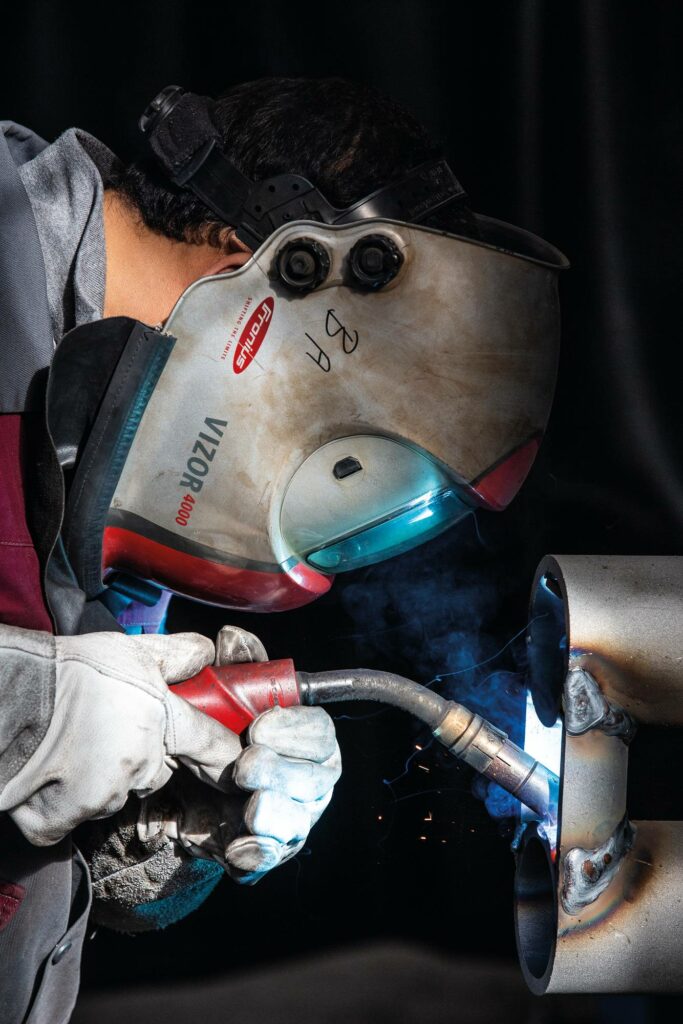
High speed can be important in terms of cost effectiveness where large quantities have to be produced in a short time. But high welding speeds also mean a smaller heat-affected zone on the component. This zone is created in the area of the weld seam, where the heat input into the workpiece can reduce the quality of the metal. Heat can harden the metal locally and make it brittle, leading to cracks or fractures and reduced tensile strength. It is therefore important to minimize the amount of heat introduced into the component. This is particularly important if it is later exposed to dynamic, i.e., alternating loads, such as bridge girders, train cars, or parts of a vibrating machine.
Welding environment
The choice of welding process depends on environmental influences. Is the component exposed to wind and weather or can it be welded while protected from these? TIG and MIG/MAG processes require a protective gas shield provided by a separately supplied gas. This can only be guaranteed in enclosed spaces or by sheltering the component so that the supplied gas cannot be blown away. When welding outdoors, it is better to use the manual metal arc welding method. The burning coating forms shielding gases and slag which protect the melt from chemical reactions with the ambient air.
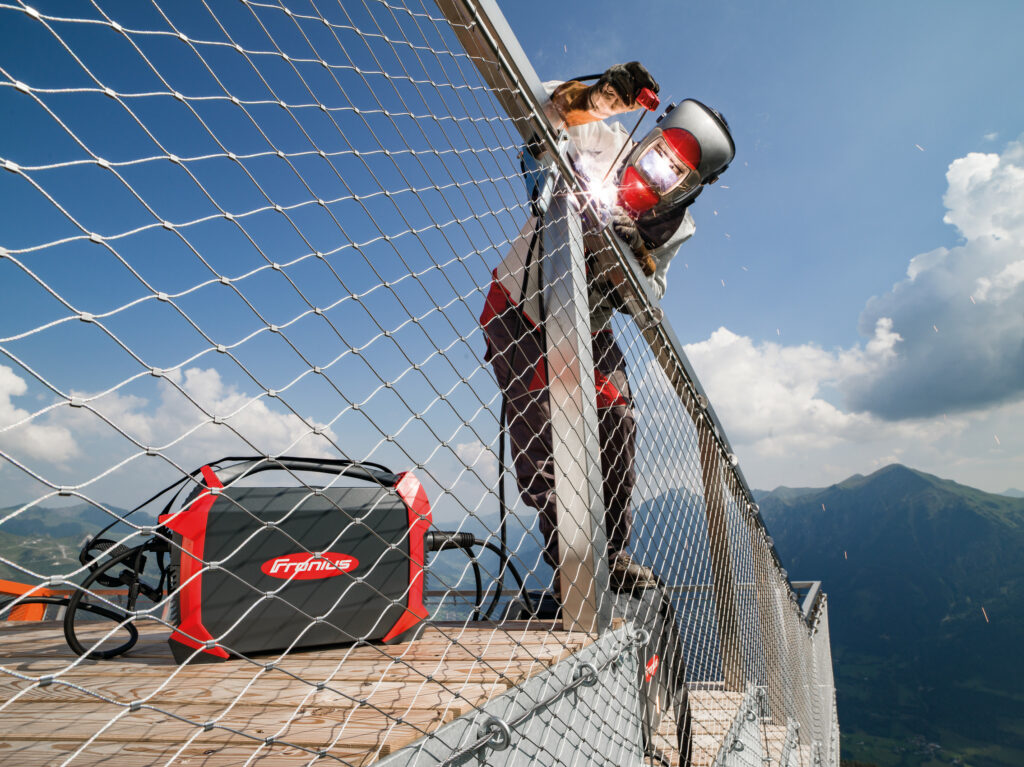
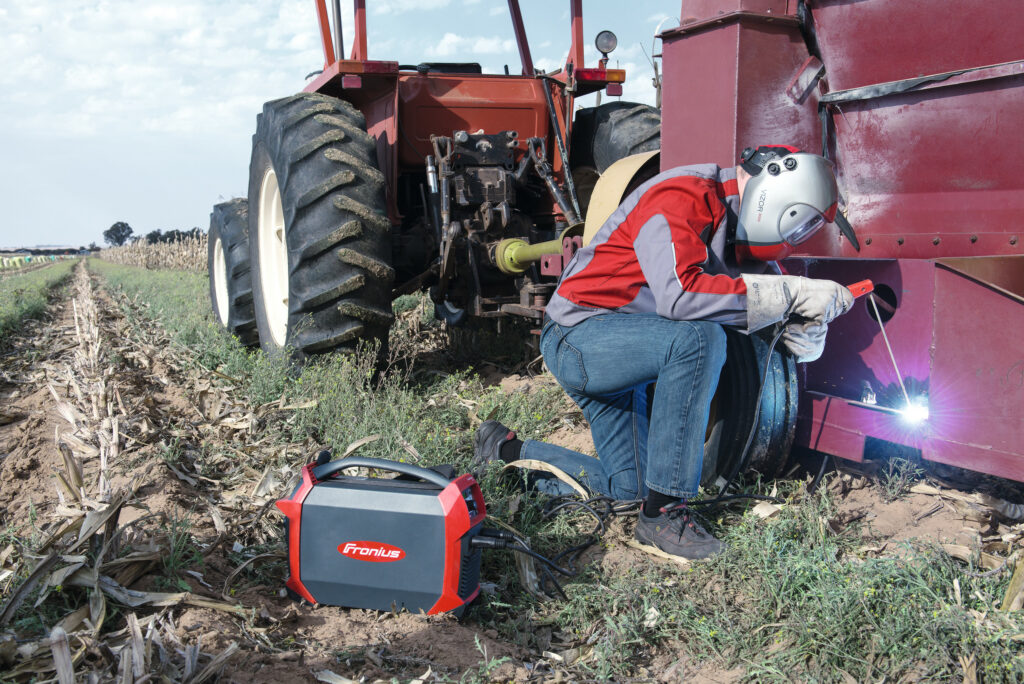
Seam optics
With visible seams, a flawless appearance is vital. A smoothly rippled seam appearance with an extremely fine texture is often required. This can only be achieved with the TIG process or by using special functions of the MIG/MAG process, such as MIG/MAG stitch welding or CMT. In manual metal arc welding, seam appearance depends on the type of electrode used.
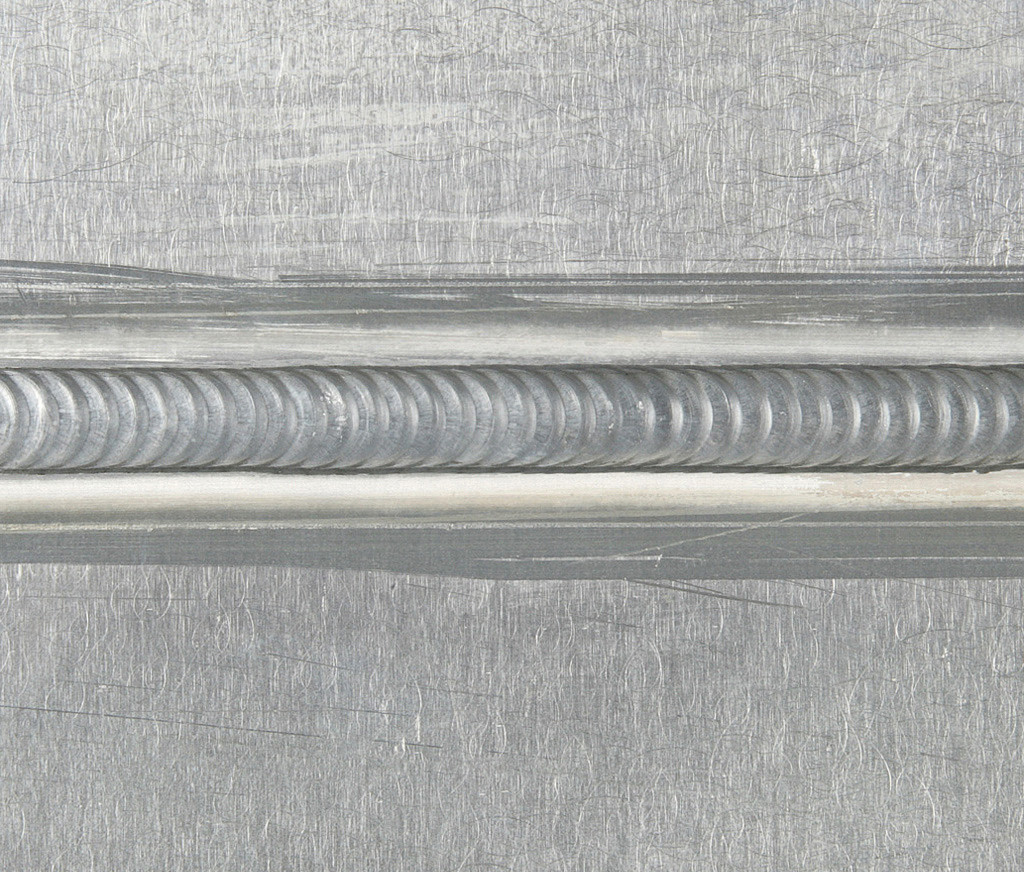
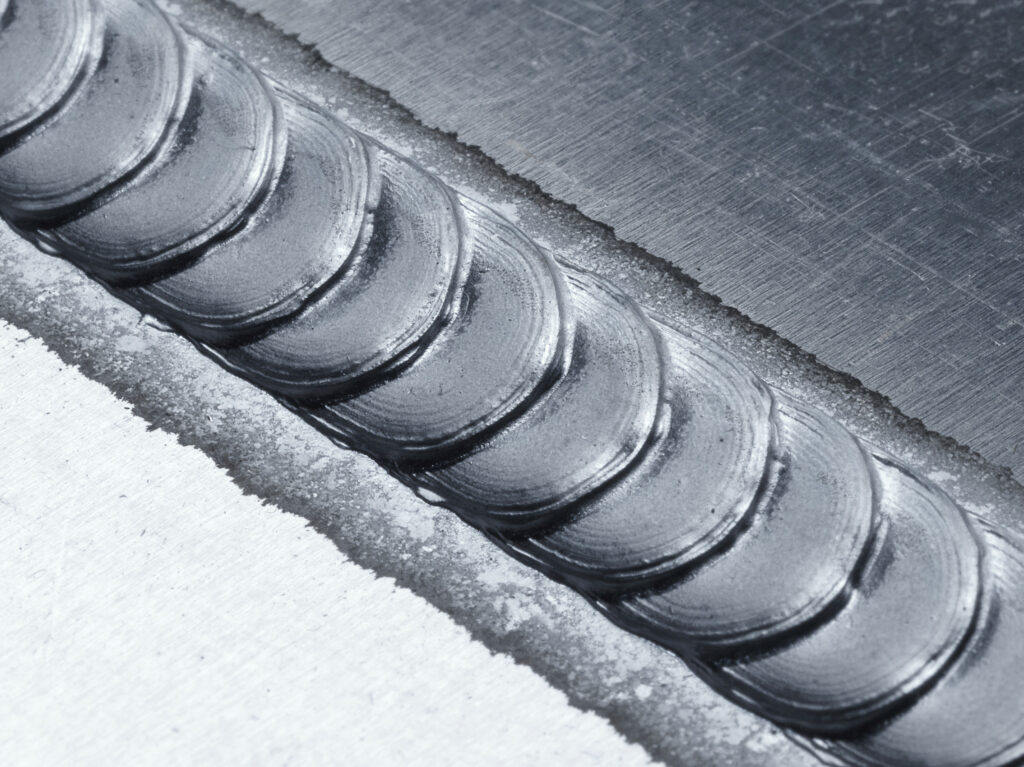
Seam quality
Where seam purity is paramount, TIG is the first choice. TIG weld seams have the best mechanical properties. MIG/MAG seams can also achieve very high quality.
However, high-quality TIG seams demand high purity of the joint edges prior to welding. They must be perfectly clean, i.e., free of rust, oil, grease, and any other impurities, in order to use the TIG process.
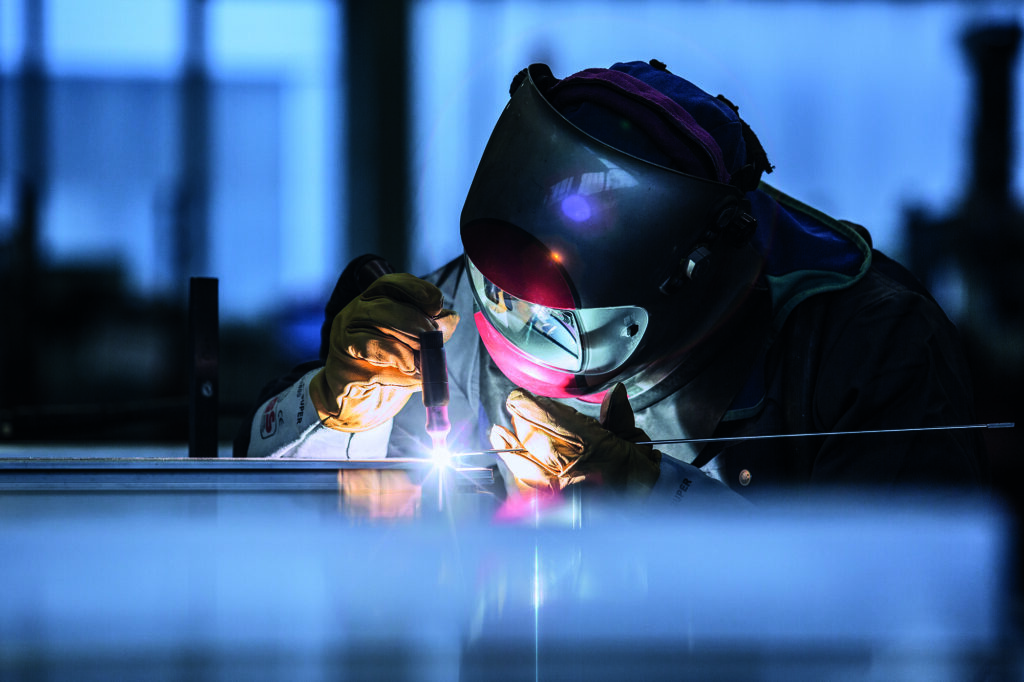
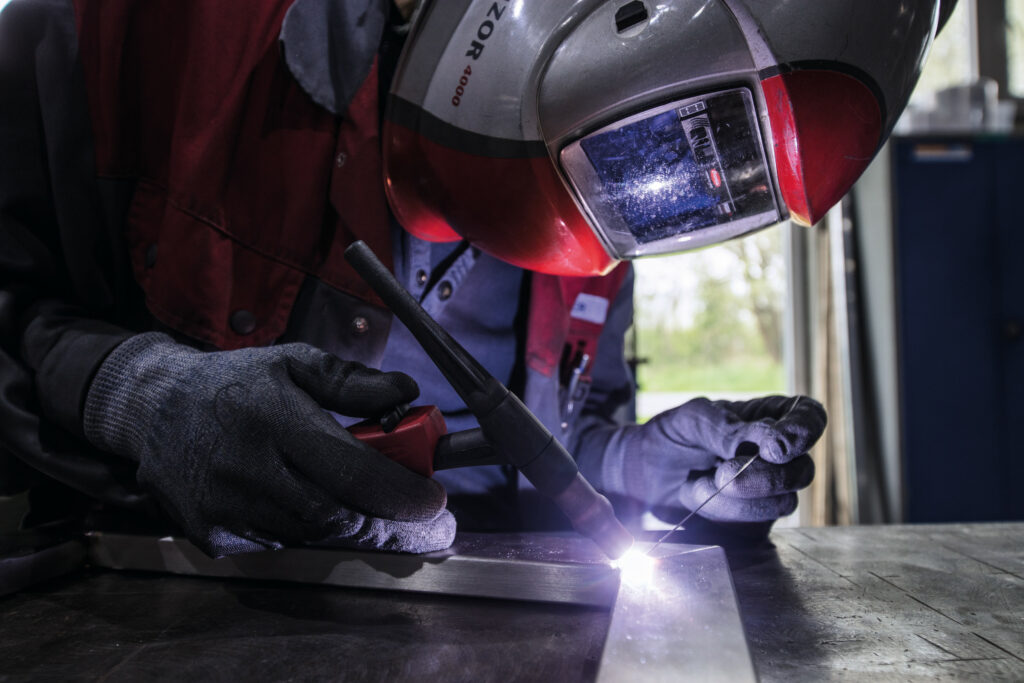
Component thickness
In addition to the above requirements for the seam, component thickness also plays a role when selecting the welding process. Components less than one millimeter thick cannot be welded with an electrode, but if the component is thicker than four millimeters, TIG welding is considered uneconomical. The MIG/MAG process, on the other hand, can be used for anything from ultra-light gage sheets to solid steel plates.
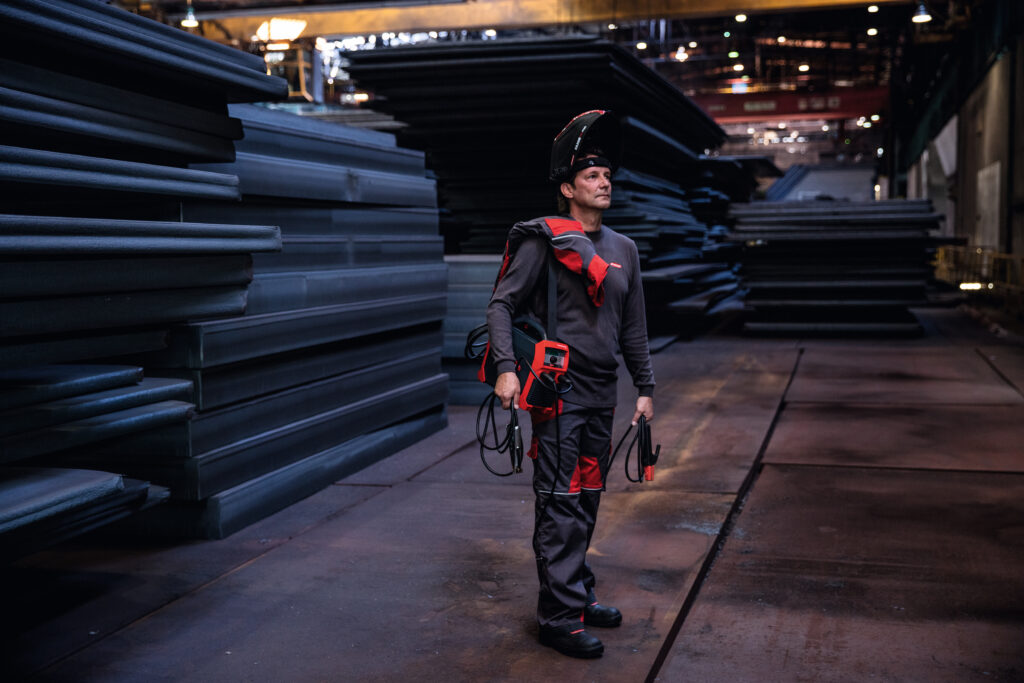
The expert:
Johann Dallmannsböck is a professional welder with decades of welding experience behind him. For many years he was also employed as an expert in the commissioning of robotic welding systems worldwide. Today he is a trainer at the Welding Business Academy of Fronius International in Austria, where he trains users in the operation of state-of-the-art welding equipment.
Welding technology reference: Explanations of all technical terms can be found in the Fronius Welding Wiki.
3 Comments
Sandeep Kumar
9. August 2022 at 10:59Excellent explanation. As always Fronius is providing quality information related to welding.
May I have permission to use some of this post material on http://www.materialwelding.com by mentioning this page reference. Thanks.
Aaina
26. May 2025 at 13:21This is an excellent, concise guide that effectively explains the key differences and ideal applications for TIG, MIG/MAG, and electrode welding processes. It’s a valuable resource for anyone looking to understand when to use each method.
redakteur
27. May 2025 at 7:19Thank you very much for your feedback!