It’s like playing with fire: arc plasma at up to 20,000 degrees, dramatic changes from one microsecond to the next, and a huge impact on materials. Natural lightning and arcs during welding work according to the same physical principles. But what’s the role of electric arc technicians? To transform something inherently unstable, volatile, and intangible into something steady and reliable. In other words, to develop a stable arc that makes welding fast, convenient, and reliable.
In order to understand what an arc technician actually does, you should know the basic principles by which arcs work. To put it simply, in order for an arc to occur, there must be an electrical potential difference – i.e., an electrical imbalance – between two points. At one point there is a surplus of electrons (i.e., negatively charged particles), and at the other, there is a shortage of electrons.
Electrons in the plasma channel
To compensate for this imbalance, a voltage breakdown occurs under certain conditions. In this case, the air (or the shielding gas) between the two points is ionized by heat or high electrical voltage. Electrically conductive plasma is created. Current then flows between the two points through a plasma channel. As long as the current flows, the arc also exists.
If the imbalance (the potential difference) between the two points is eliminated, the current flow stops, and with it the arc. Whereas in lightning the potential equalization takes place in a few tenths of a second, in welding the electrons must flow continuously through the plasma channel.
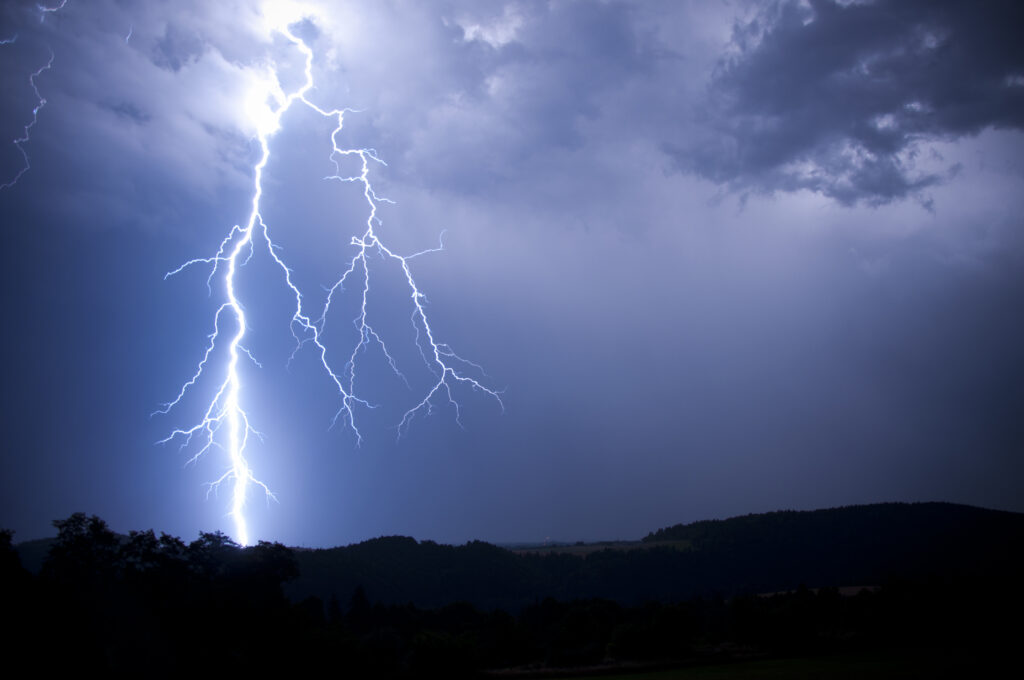
The processes involving the arc are described in detail in the blog post “What is an arc and how does arc welding work?”.
Arc design: what does the perfect arc look like?
The fundamental question that electric arc technicians face in practically every situation is “What does the perfect arc look like?”. That’s why a key task for arc technicians is to design the arc in welding processes in such a way that it remains as stable as possible even under the most adverse circumstances – and even when it’s being used not as expertly as it should be.
“The shorter, the better” is a frequently applied basic principle in arc technology: the shorter an arc is designed, the faster and more convenient welding usually is. Short arcs are characterized primarily by high arc pressure and high energy density. With long arcs, there is an increased risk of undercuts, emissions, and lack of fusion.
Product development: defining requirements for arc welding systems
The arc is at the heart of most welding processes such as TIG, MIG/MAG, and MMA. This is why arc technicians are always involved in the development of new arc welding systems. They are the ones who define what the electrical requirements for a particular welding process should be, and what is needed for this in terms of hardware and software. In the end, it’s the performance of the arc that essentially determines the success of an arc welding system on the market.
Electricity as a working tool
Ever since 1782 when Georg Christoph Lichtenberg succeeded in connecting a watch spring and a knife blade with the aid of “artificial electricity”, arc welding has been all about electricity, and in particular the core parameters of amperage, resistance, and voltage. In MIG/MAG welding, the wire feeder (or the speed of the wire feeder) is also a decisive factor.
However, these main parameters are far from enough in modern arc welding systems: arc technicians have now identified hundreds of different secondary parameters, all of which can have an influence on the arc.
Developing algorithms to make arc welding smart
As in almost all demanding technical professions, a significant part of the work of an electric arc technician takes place these days in front of a computer. In order to correlate the essential parameters and factors that have an influence on the arc, arc technicians develop the corresponding algorithms and work constantly on optimizing them.
Control and regulation of the welding processes are represented in the algorithms. In other words, it is the algorithms that make welding processes and welding systems smart. The algorithms are embedded in the general welding system software, which in turn is further developed in close cooperation with arc welding technicians.
Arc welding programs for maximum user-friendliness
The arc welding algorithms form the basis for the development of welding characteristics and welding programs. It is the welding programs developed by the arc technicians that make a decisive contribution to the user-friendliness of modern welding systems for welders’ everyday work. These programs enable a wide variety of materials and filler metals to be welded together in a user-friendly manner, which means welders don’t need to know the detail behind the special relationships between the individual parameters and welding variables. All arc welders need to do is make a few selections and set the correct welding program on the system before they can get started.
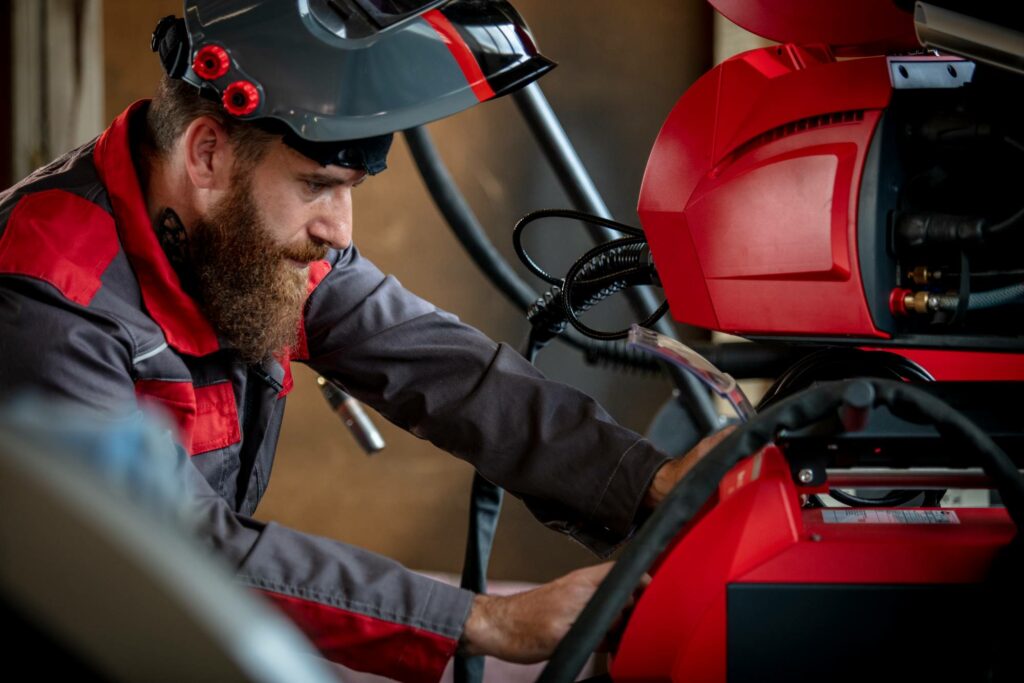
The limits of PC work for arc welding
Welding systems from the big manufacturers now feature hundreds of welding programs like these, particularly for standard materials. Nowadays, an essential part of the daily work of arc technicians, therefore, consists of developing welding characteristics or programs for more unusual material and shielding gas combinations.
This is also where working on a PC has its limits for electric arc technicians: new welding programs are developed and tested in an arc laboratory under practical conditions. Manual welding and the use of welding robots, therefore, form part of the everyday work of most arc technicians.
Testing to achieve the optimum result
Customers usually name the specific materials and shielding gases for which a new welding program is to be developed. Arc technicians use their experience with existing welding characteristics in their daily work. It is sometimes necessary to carry out several welding tests under real-life conditions until a new welding program is found. The algorithm, the welding program based on it, and the arc may be perfect, but ultimately it is always the result of the welded material that counts.
Workplace: dedicated arc laboratory
Arc technicians largely work independently. Most of them have a dedicated laboratory at their disposal where they carry out tests undisturbed with newly developed welding programs and don’t endanger anyone else during welding. In addition to equipment for manual welding and welding robots, the basic equipment of an arc laboratory primarily includes measuring instruments. One key instrument every arc technician has in their armory is an oscilloscope. This tool makes it possible to measure various voltages and currents as well as wire speeds.
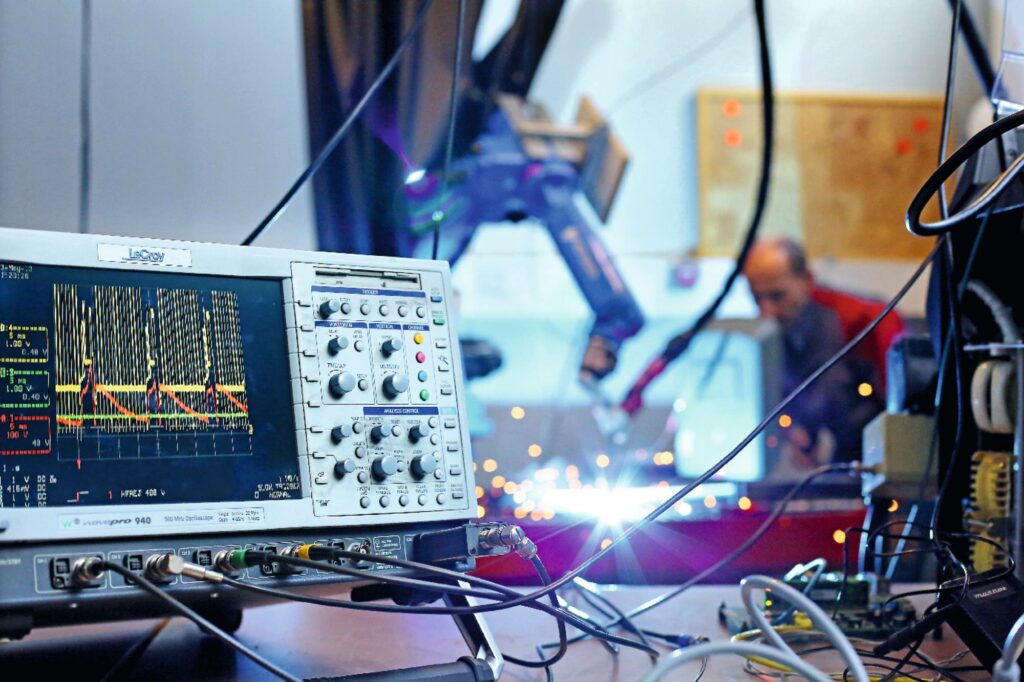
Key question: what does really happen inside an arc?
The question “What really happens inside an arc?” is crucial to the development of arc technology. High-speed cameras use slow-motion images to provide comprehensive insights into the processes that often take only milliseconds inside an arc during welding.
The introduction of high-speed cameras – and the knowledge gained from them – has contributed to significant advancements in welding technology in recent years. These include the reversing wire feeder for the “CMT” welding process, innovations in the droplet transfer of the pulsed arc, as well as in laser processes or innovations in connection with plasma or TIG arcs.
Today, arc technicians use high-speed cameras for a wide variety of tasks related to product development and arc design.
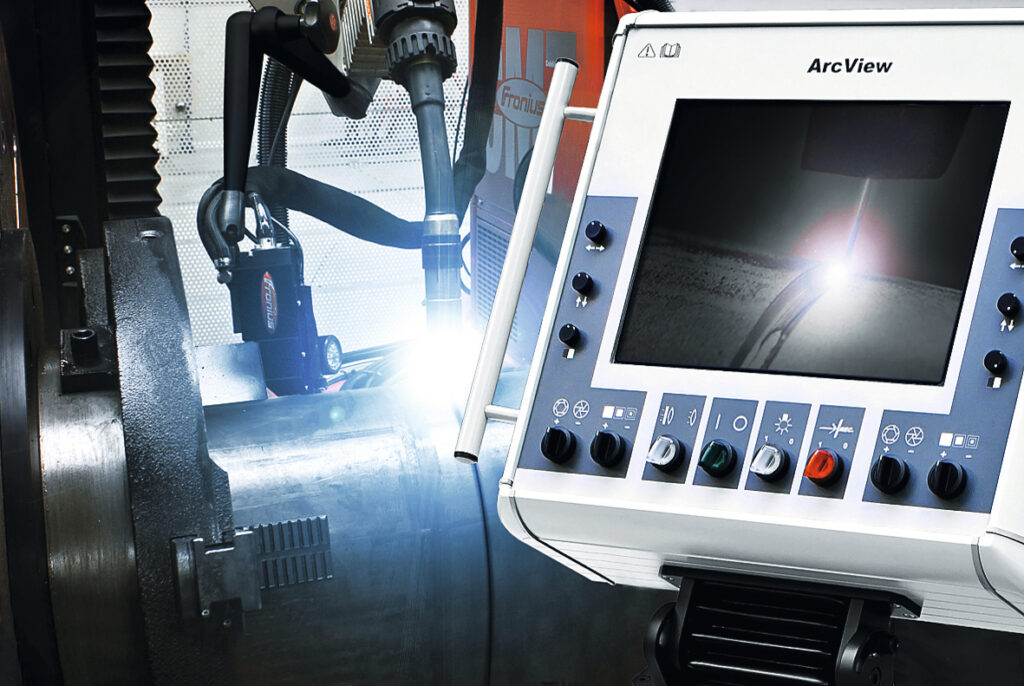
Arc technician profile: a thirst for research and the will to optimize
One question that has not yet been covered is “What makes a good arc technician?”. You should have a basic understanding of electrical engineering, knowledge of physics, a good technical-mathematical understanding, and some connection to welding.
“In addition to being fascinated by technology, arc technicians definitely need a certain zeal for research so they can perfect welding processes and make them as simple as possible to apply,” emphasizes Josef Artelsmair, who has been head of arc technology at Fronius for many years and played a key role in developments such as CMT technology.
“Welding is something you need to have a feeling for, and the human factor still plays a major role. This is precisely what makes working as an arc technician so interesting and exciting for me,” concludes Dominik Söllinger, now head of the arc team at Fronius.
2 Comments
Umesh Jagtap
28. April 2022 at 8:33I love the Arc Technology. Weldign is my passion. Doing something different to make any application successful by manipulating parameters/syneegic points/aec physics are always motivating me to work for the Arc Technolgy. This blog was really inspiring for me !
redakteur
28. April 2022 at 10:58Thank you very much for your feedback! Happy to hear that you do what you love!