Tried and tested countless times, with proven handling and outstanding weld seam quality: So why even bother making further improvements to the TIG welding system? Our iWave series proves that it was absolutely worth the effort: Its multiprocess welding systems are suitable for both TIG and MIG/MAG welding, 100% prepared for Industry 4.0, and offer significantly optimized welding processes. But how did the initial concepts for a new TIG welding system become a market-ready multiprocess system?
What does a new generation TIG welding system need to do to rank among the top devices in the market of the future? The people who know best are those who use it every day—our customers. Their preferences, opinions, and experiences shaped the development of the new iWave right from the very start. A total of 120 team members were involved in this project: they came from a range of R&D departments, such as arc technology and simulation, to software development, right through to product management, service, and production.
Optimizing TIG Welding
“Our overriding aim, from the moment we first started developing these products, was to make significant improvements to all the welding processes—no easy task given the high technical standard of existing TIG welding systems,” stresses Paul Hofer who, in his role as Technical Product Manager, was heavily involved in the development of the new iWave. “Right from the early stages, we focused on new ignition properties for these devices, as well as on developing an exceptionally strong AC performance and new TIG processes—all designed to open up a wide range of new possibilities for welders,” adds Hofer.
It soon became apparent that “multiprocess capability” was a key issue. “As the technical basis of the new iWave, our TPS/i platform lent itself to MIG/MAG welding systems. So, we soon realized that we needed a welding system which—as well as an all-round optimized TIG process—could also master other welding processes like MIG/MAG welding to an equally high standard without compromising on quality,” explains Stefan Aichinger, Project Manager for the iWave development. “Ultimately, we set out to be the first quality provider to create the proverbial ‘jack-of-all-trades device’—i.e., the first complete combination welding system,” Aichinger continues.
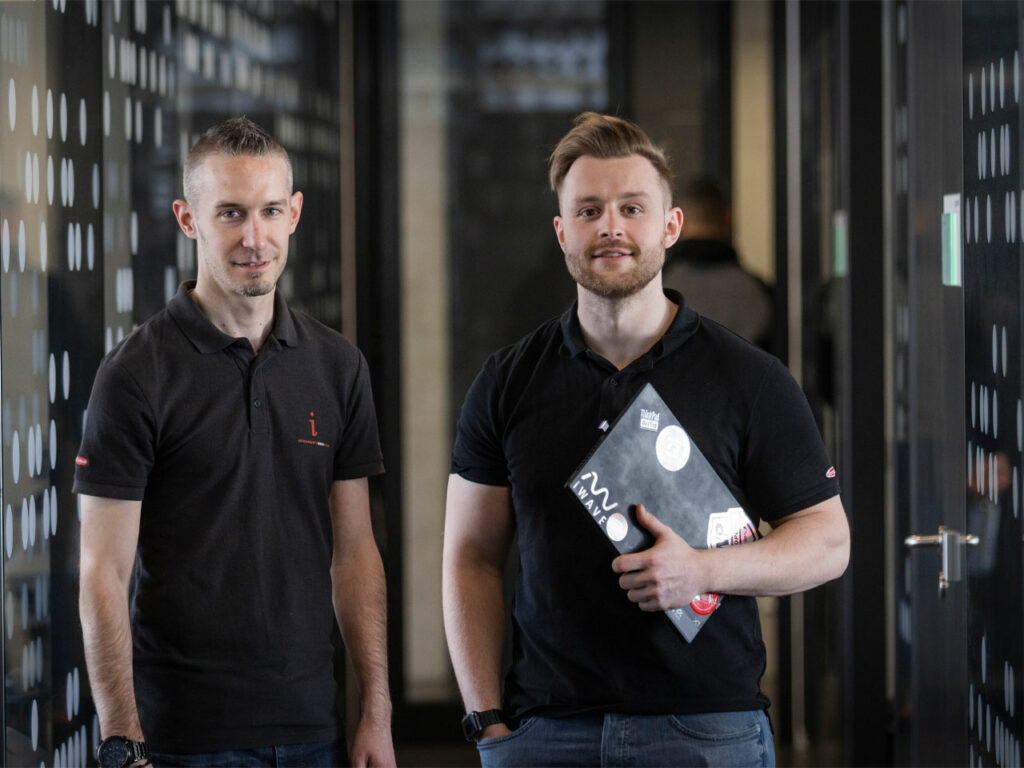
So, how can we visualize the iWave development process? It can basically be broken down into 10 main steps:
Step 1: Requirements specification. Which features would inspire our customers?
The 180-page requirements specification gives answers to the questions that we asked ourselves after numerous discussions with customers and a great deal of market research:
- How can we make the quality of all the welding processes that the iWave is intended to perform even better?
- What are the requirements of a multiprocess welding system to make it suitable for both TIG and MIG/MAG welding without compromising on quality?
- How intuitive does the user interface of the future need to be in terms of design?
- How can we meet the demands of Industry 4.0?
- What challenges will we face with regard to the system’s modularity and how can we conceptualize the device in a way that protects the planet?
Step 2: Performance specification. How do we make it?
In the performance specification, we set out the ways in which preferences and requirements could be implemented. Technical solutions and concepts were developed in greater detail. The control system proved particularly challenging: We needed to ensure perfect synchronization in the control software between the different components and three welding types—each with their own individual variants—as well as all the associated welding programs.
At the same time, we wanted the iWave to have an intuitive, self-explanatory user interface. “For the iWave, we developed a “graphic dynamic” operating concept with a touchscreen. These graphics give welders an at-a-glance view of the processes and parameters they have set. It also offers direct feedback on how a weld changes according to adjustments made to the settings,” explains Paul Hofer.
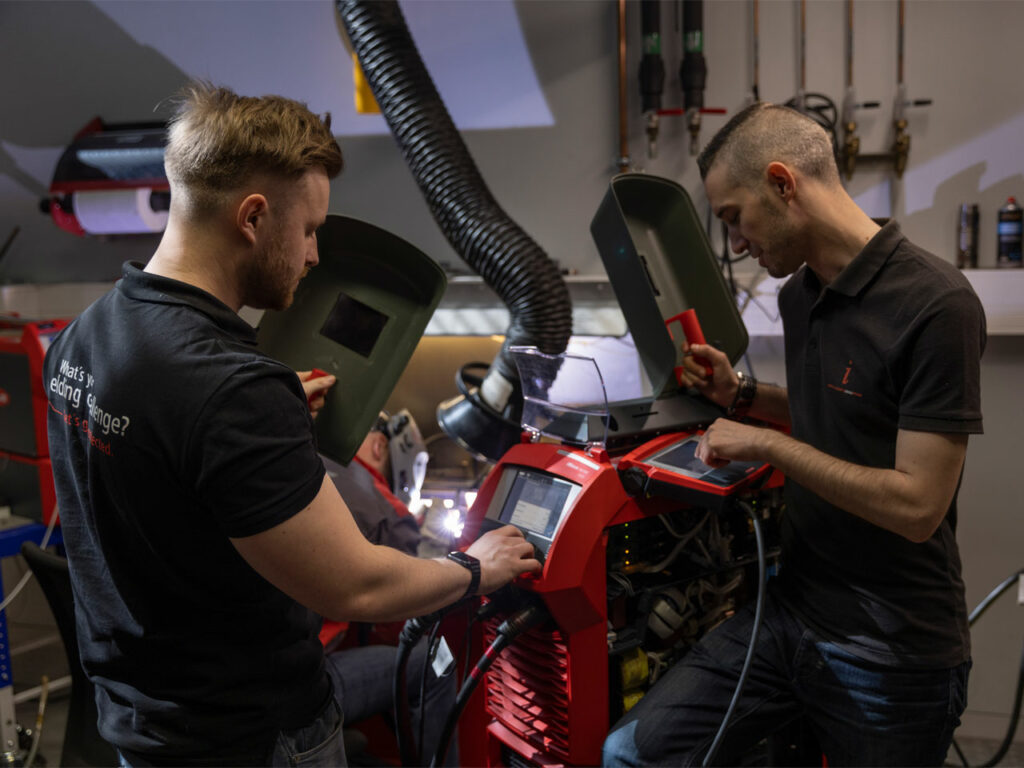
Step 3: Building prototypes—ideas and concepts turn into something concrete
In this next step, the iWave finally becomes actually “tangible.” Using the technologies detailed in the performance specification as a basis, the project team builds the first prototypes or an iWave pre-production series.
Step 4: Field tests with customers—with zero training for welding experts!
If pre-production series were 100% perfect, they wouldn’t exist. That’s why we put the iWave prototypes through their paces with comprehensive testing. Naturally, this is done internally—but also in practical applications, with our various foreign branches, representatives, and long-standing customers around the world. In order to put our self-explanatory operating concept to the test, we deliberately don’t give our welders any training on how to use these new devices. We wonder how that went down …
Step 5: We listen to our user feedback in order to improve our prototypes
This step involves analyzing the various feedback from the prototypes, categorizing it correctly, and integrating it into the further product development process. The development teams received particularly positive customer feedback on the weld performance, and many users reported that the device was very easy to operate.
Step 6: Product tests—hard impact tests, dust, and more
Now it’s time to take off those velvet gloves: new devices must, among other things, successfully pass an impact test with hammer blows, a drop withstands from a specified height, and a metal dust test. The iWave also successfully passed a low temperature performance test up to -40 degrees. Why did Fronius’ employees put their iWave through so much suffering? The reason is twofold: firstly, in order to meet the company’s strict internal quality guidelines, and secondly, in order to obtain certification and approvals for certain markets.
Step 7: Design freeze—finally done with the iWave?
Many of the development team members were at least able to say, “finally done with the iWave!” at this point. “Design freeze” means that the product development process is over for the time being, and that no further changes will be made to the new multiprocess welding systems in the immediate future. So, what comes next?
Step 8: Pilot series—general test for production
Now it’s time to hand over the reins to the Fronius production technicians: Their role is to prepare the production lines for the iWave series production. The individual production steps are optimized under real-life conditions and designed with maximum efficiency in mind. In under three months we produced almost 60 pre-production devices of the different types of iWave to make sure that everything runs smoothly in the next stage.
Step 9: Start-up—series production begins
Almost there: Series production of the iWave begins, with production ramped up incrementally.
Step 10: Start of sales—and we’re off!
It’s January 19, 2022, and the new iWave is officially introduced to the market. This is when the Fronius sales and marketing team take over the main responsibilities. Their role is to help turn the years of dedication from the development teams and the hard work of the production staff into market success.
The start of sales marks the end of the development process, into which a lot of time, money, and energy has been poured. But, ultimately, it’s results that count—and the many tangible benefits and highlights that the new iWave brings to the world of welding.
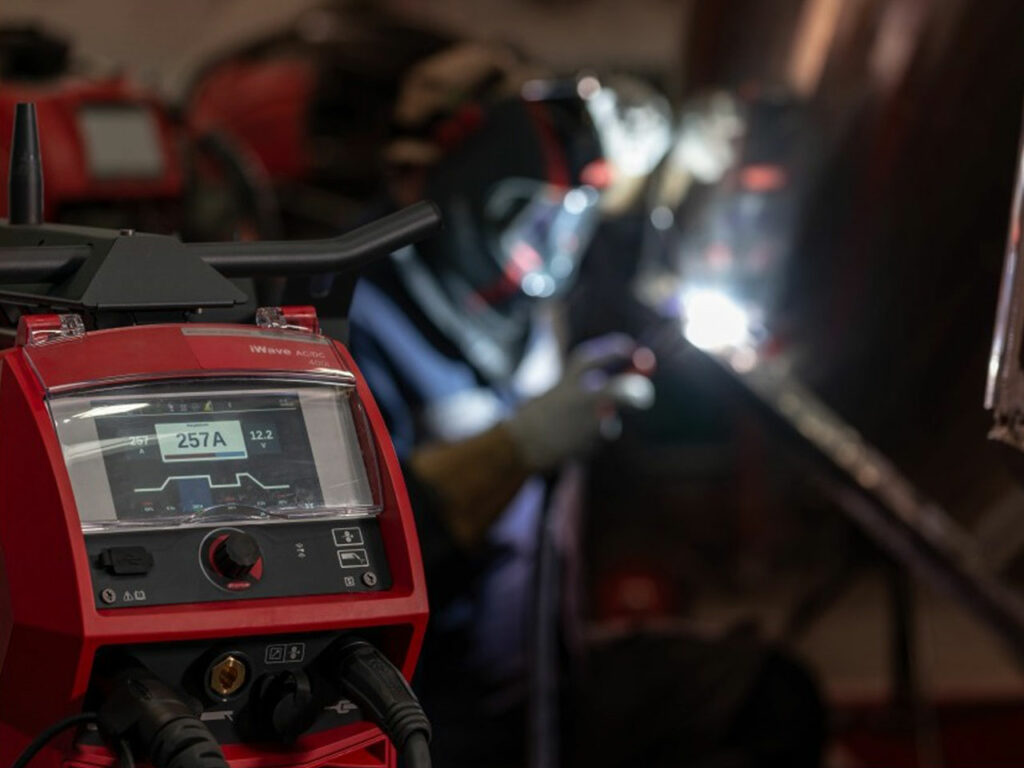
Development Never Ends
“We’re so happy that we were able to turn the prerequisites set out in the requirements specification into a reality—and this has obviously vindicated our years of hard work,” says iWave Project Manager Stefan Aichinger. Development processes for technical products like welding systems are never truly complete in the traditional sense, though: After successfully entering the market, the Fronius Life Cycle Team will oversee all the technical aspects related to the iWave. Over the course of the product life cycle, the iWave will undergo regular minor adjustments as well as occasional major ones.
And what are the numerous technicians involved in creating the new iWave doing now? The fact is that they won’t be running out of work any time soon: We’re looking to redesign our premium portfolio in the area of TIG welding systems—and we’ve already reached the first milestone with the iWave.
1 Comment
Msehli Saber
29. March 2022 at 12:27Je veux savoir plus d’informations