We are all living in volatile times. The energy revolution, geopolitical tensions, and uncertain supply chains are putting us all to the test almost every day. Discussions are often controversial and heated. But one thing is sure: production is more challenging than ever—because in the future it will have to be more resource-efficient, faster, more flexible, more cost-effective, more environmentally friendly, and in small batch sizes. This is where metal 3D printing comes in.
Metal 3D printing: what is it exactly?
Metal 3D printing, like all other 3D printing processes, is a manufacturing process that has revolutionized the production of many products both technically and economically. Building a product layer-by-layer, which seemed like science fiction yesterday, is a reality today. Three-dimensional objects are produced by the layered, additive build-up of a base material. 3D printing is now gaining traction in more and more industries, as it increases the flexibility and therefore the competitiveness of companies across a number of sectors. Potential applications can be found in the automotive, electronics and consumer goods, oil and gas, aerospace, power plant construction, toolmaking, medical technology, and construction industries.
Metal 3D printing offers huge potential and numerous advantages
Classic production techniques often require complex molds and tools to be constructed, and are associated with long lead times and high set-up costs. Additive manufacturing helps to drastically shorten development cycles. Printing components on demand accelerates prototype construction (rapid prototyping), enables just-in-time production—doing away with spare parts stockholding and its associated costs—and significantly simplifies repair work.
If spare parts are required, the correct “recipes” are selected in the software and printed or copied as required. There are hardly any limits for component geometries. Even complex honeycomb and cavity constructions can be made. Metal 3D printing offers a special advantage in prototype construction, as design problems can be detected at an early stage and remedied without complex and expensive mold and fixture construction. At the same time, the process accelerates innovation and increases a company’s productivity. Printed components optimized in terms of shape and load (topology-optimized) are often lighter than conventional ones and can reduce the fuel consumption of aircraft or vehicles, while also increasing the payload of transport vehicles.
Metal 3D printing with high-end welding technology
Various generative methods are available for 3D printing processes. Objects are built up and shaped layer-by-layer by joining individual layers of material. The processes involved in metal 3D printing are divided into two fundamental types: powder-based and wire-based. In powder-based processes, the layers are built up using molten metal powder. The most common method, the powder bed process, boasts a high degree of precision, but is relatively slow. The wire-based process builds up the workpiece by melting the wire using either an electron beam, a laser, or an arc. These processes have a high deposition rate and therefore help to cut production times.
Wire arc direct energy deposition, or DED-Arc for short, is arc-based and uses the gas metal arc welding process (GMAW). This metal 3D printing variant currently has a deposition rate of up to 4 kg/h, but this figure is expected to increase in the future as special processes are introduced and multi-wire solutions come on stream. Equipment and material costs are important factors in the choice of printing process. At the heart of the DED-Arc method is a stable welding system. There is no need for costly vacuum chambers, such as those used in the electron beam process. “The right welding path with the right welding parameters and processes is crucial for a good printed result,” explains Philipp Roithinger, an expert in additive manufacturing. “In addition, you need an automated welding system that ensures the welding torch accurately follows the path. High-quality welding robots today offer a path and repetition accuracy as high as +/- 0.02 mm.”
Component production using large-volume metal 3D printing
Stability and temperature management of the welding process used are essential for DED-Arc. The process needs to be low energy, i.e., as “cold” as possible, to prevent it introducing too much energy into the component. The welded layers should also be consistent, spatter-free, and even. If any flaws were to occur, these would be replicated in each subsequent layer.
With its intelligent process control variants, the unique Cold Metal Transfer (CMT) metal arc welding process already meets the high demands that we place on welding technology for additive manufacturing. “CMT is characterized by an extremely stable arc and allows flexible heat input,” explains Roithinger, adding: “The process enables an almost spatter-free material transfer, which helps to prevent flaws and reduce rework. In addition, CMT allows us to achieve excellent deposition rates and control the detachment of each droplet, so we can work even more precisely. What’s more, with CMT Additive Pro, we have further optimized the process for additive manufacturing in order to ensure a more constant layer structure and better thermal management.”
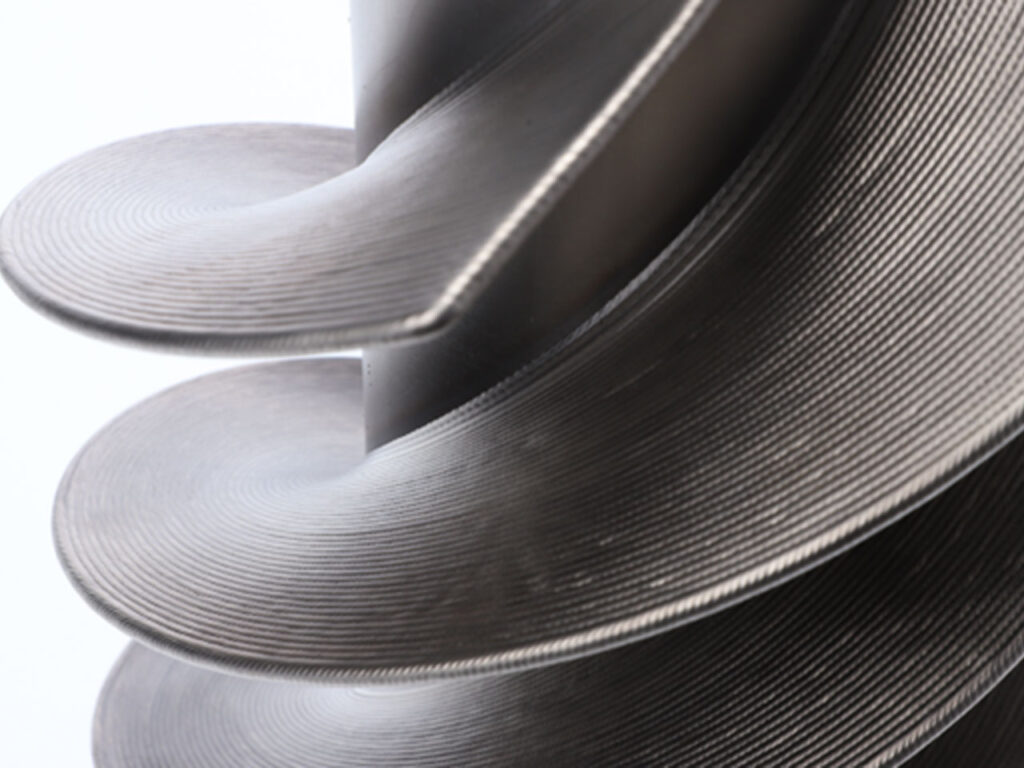
Keeping the arc under constant observation with metal 3D printing
Despite the high-tech equipment, it is recommended that welding experts keep an eye on the arc and the droplet detachment. Special camera systems can be used to monitor welding work and detect potential flaws, so the welder can take prompt action if needed. For example, ArcView 2 is a process-triggered camera that allows you to monitor the process directly from your workspace. The camera delivers crisp images in the millisecond range. The individual photos are taken during the short-circuit phase, i.e., at the precise moment when there is no arc. Many such images provide welding specialists with a perfect real-time video for process control. This can be viewed on a screen outside the robot welding cell, offering welders the highest level of protection from arc radiation.
Economically and environmentally sound
Alternatives to additive manufacturing would be milling or machining, but these generate a lot of waste, as the required parts are cut out of metal blocks—often huge ones. When working with a hollow body, the amount of waste is enormous. In the case of additive manufacturing, we produce the component layer by layer, so afterwards, only rework is required. Plus, this is not always necessary. Material usage is therefore much lower compared to the usual production methods. In situations where 80% of the material is lost on certain bodies during milling, the equivalent during additive manufacturing—for example with DED-Arc—is often as little as 20%, with the loss occurring during reworking.
“Let’s look at a striking example: the metal propeller shown below was made with metal 3D printing. If it had been milled from a block, the block would have been 60 x 90 x 90 cm in size and weigh around 4 tons, while the finished component weighs just under 100 kg,” says Roithinger.
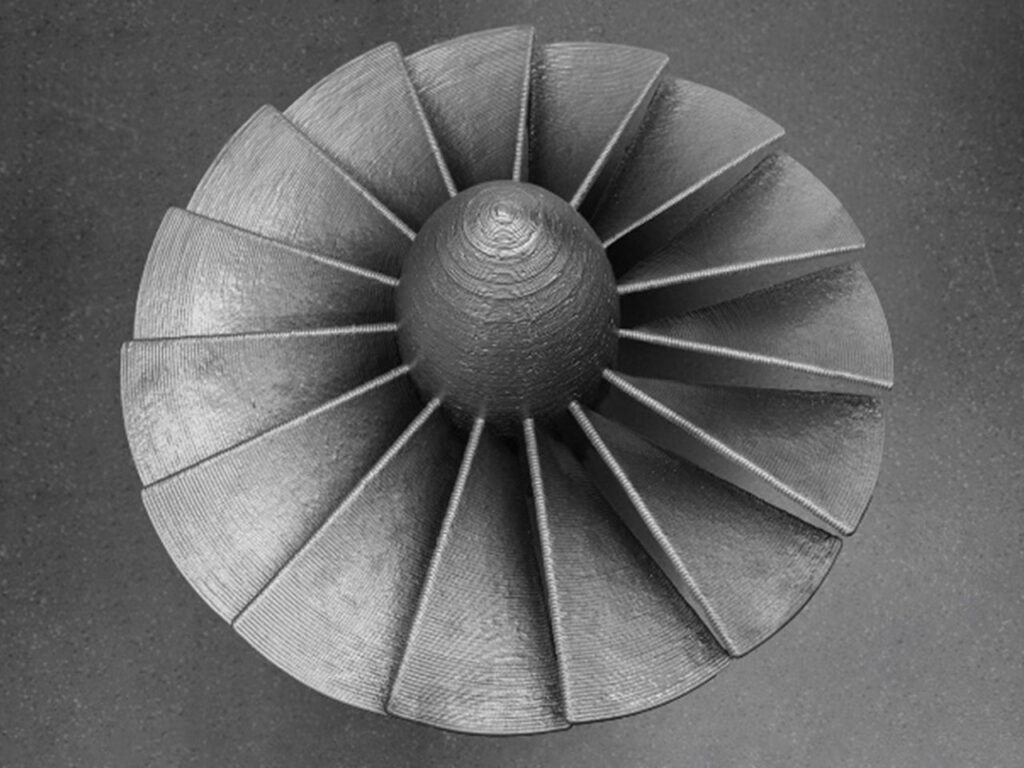
The future of metal 3D printing at Fronius—an outlook
“The additive welding process has enormous potential. As ever when new technologies come onto the market, there is always some initial resistance before the appropriate applications are found and the technology starts to flourish. DED-Arc is still young compared to other 3D methods,” Roithinger explains. “However, there is already a huge demand for the reconstruction and repair of damaged parts. Metal 3D printing allows us to extend the service life of components such as propellers or screw conveyors by years. But not only that: all the spare parts that might possibly be required can be printed on demand. Many commercial and industrial companies become independent of location and delivery time, which makes them more competitive—and crucially so. They also save on unnecessary storage costs.”
Fronius engineers are taking the additive process to a new level in order to increase the range of possible applications of metal 3D printing and achieve even more process stability. “Our vision is that sooner or later we will start printing immediately after the design phase and the 3D printer will spit out the perfect result. Once this technology has been established, it would be possible to simply distribute digital recipes instead of components. These would then contain the required printing instructions with welding path, welding parameters, waiting times, and everything else the user will need. All customers will have to do is upload the recipe to the on-board computer of the automated system—the control system—and press ’Print’,” adds Roithinger, giving a final insight into the thoughts of the Fronius innovation team.
2 Comments
Larry
8. February 2024 at 16:07Nice, clear explanation of an exciting new technology. It will be interesting to see it develop in the coming years. If the surface finish of the additive welding process can be flattened to a sub-mil range, it will open up much more markets for this type of welding. Good luck.
Niharika
5. November 2024 at 10:35Great article